The most recent news off the press is that huge robots powered by artificial intelligence (AI) are currently using additive manufacturing to print whole rockets by employing the largest metal printers in the world.
In 2018, the finalized version of a 3D metal printed bridge was displayed to the world and is just waiting to be installed in Amsterdam, its final location.
3D metal printing is being heralded as the modern method for fabrication, set to replace the traditional techniques. It is a highly exciting development. Hitachi has worked with the metals industry for several years and is inspired by developments in technology and this is a great example.
The Rise of Additive Manufacturing
While traditional methods are already established as being safe, affordable, and fast, additive manufacturing is a technique that is proven to be even more efficient, affordable, and safer than what has been seen before.
At a tenth of the cost of traditional technology, 3D metal printing provides products that are materially similar to, and in several respects higher performing than, products created by traditional methods.
3D metal printing is a manufacturing tsunami that will soon sweep throughout traditional metal fabrication sectors.
When metal is additively manufactured, raw materials are introduced and formed in thin layers instead of being cut or subtracted from a solid body of metal.
The amount of raw material employed is highly resource-efficient, creating essentially no waste and decreasing both tooling and material costs extensively.
Additive Manufacturing is as Good as the Raw Material that Goes in
There is a cost related to the introduction of additive manufacturing but for smaller manufacturers, constant developments mean that quality machinery is becoming much more cost-effective.
It is important to note that what is produced by the 3D printer is of equal quality to the raw material that goes in, as with any conventional metal manufacturing process.
The materials employed are tungsten, titanium, stainless steel, copper, chrome, cobalt, and aluminum. They must first exist as alloy powder or pure elements before any of these are used as raw materials.
This ‘powder’ could be tested with an XRF (X-ray Fluorescence) metals analyzer to verify it is of the desired quality before its transformation into a critical component.
An intricate image of the item to be printed using a 3D metal printer is first produced on a computer. This image is utilized to manage the fusion methods and the deposition of metal powder.
This outline has several layers printed on top of it, normally only 0.1 mm in thickness, enabling the production of very detailed and complicated shapes.
This creates a range of design possibilities and gives manufacturers the chance to make parts that could otherwise be too expensive or impossible to create through the use of conventional techniques such as casting, machining, or forging.
The ability of the printer to work with very thin layers leads to easy accommodation of extremely hollow or thin designs, which decrease the weight of the item.
This is especially advantageous in industries such as aerospace, which actively look for products that are lightweight to enhance aerodynamics and decrease the consumption of fuel.
Ensuring Quality Control
Additively manufactured metal also has a significantly decreased impact on the environment because the material is being added, rather than subtracted, and any waste is easily recycled during the process.
When evaluating the retooling process necessary in conventional manufacturing, it is not difficult to observe where additive manufacturing deserves consideration as an option that offers more sustainability.
The final product is a dense and sintered metal. Metal-printed parts have greater hardness and strength. They are also likely to be more flexible compared to traditionally manufactured parts. Despite this, these parts can have a higher vulnerability to fatigue.
The most important issue is understanding and managing the precise composition of the fabricated components. The line of handheld XRF analyzers by Hitachi enables comprehensive and instant analysis of the powders and final components as they develop within the process.
The Hitachi devices additionally allow this wealth of data to be stored in the cloud for instant access and analysis.
As for the bridge, Hitachi cannot wait to observe the installation in Amsterdam, as this will be a first within the industry.
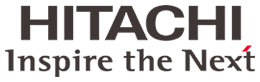
This information has been sourced, reviewed and adapted from materials provided by Hitachi High-Tech Analytical Science.
For more information on this source, please visit Hitachi High-Tech Analytical Science.