Including flow additives in a blend in order to tailor flowability, is common practice in many powder processing industries. Often powders developed to meet certain product performance targets are not conducive with consistent and predictable flow, creating a demand for additives that can enhance flow properties.
Within food processing for example, flow additives are routinely employed to reduce or eliminate powder caking, a phenomenon that compromises product value, while in pharmaceutical blends additives help to support the efficient die filling needed for successful tableting. Although typically incorporated to improve process efficiency, the use of additives can also have a substantial influence on final product quality. In the powder coatings industry, for example, additives are used to produce blends that flow and level easily, to create a high-quality surface finish.
When optimizing the use of flow additives it is important to recognize that their impact on behavior may extend beyond a simple improvement in flowability. Choosing the most appropriate grade of flow additive for a particular blend, and incorporating it at an optimal level for the application is also crucial. Many powders have poor basic flow properties: They block in hoppers and die feed frames, exhibit inconsistent or pulsatile discharge rates, adhere to surfaces of equipment or don’t mix readily with other materials.
In such cases, it is possible to reduce particle-particle friction and change the powder’s bulk resistance to movement by the addition of a lubricant powder. Magnesium Stearate (MgSt), highlighted in the study below, is used extensively as a lubricant in the manufacture of pharmaceutical oral solid dosage forms. It is commonly added to formulations in low concentrations (typically <1% w/w) immediately prior to tableting.
Over a range of processes, however, the relationship between flow additive and substrate is less well-understood. Due to the differing demands placed on powders by different processes, the relative influence of a given additive on a given substrate may not be consistent under all circumstances.
Preparation of Samples
Three different Magnesium Stearate (MgSt) formulations (Stear-O-Wet, Monohydrate & Dihydrate – Malinckrodt) were blended separately with five excipients (Avicel PH101 – FMC; Inhalac 230 & Granulac 70 – Meggle; C*Mannidex & C*Sorbidex – Cargill).
The blending was undertaken for a fixed period and rotational speed in a Turbula T2A mixer (Willy A Bachofen AG). The resultant blends were tested using an FT4 Powder Rheometer® to evaluate their Dynamic Flow, Bulk and Shear properties, and compared with the results generated for their respective substrates without lubricant.
The Relative Influence of Flow Additive Content on Flow Properties
Dynamic Testing: Basic Flowability Energy
All lubricants significantly reduce the BFE of the substrates, indicating increased flowability in dynamic, forced flow operations such as feeding and blending, with the Inhalac 230 showing the greatest sensitivity to lubrication overall and Mannitol the least. Considering Avicel PH101 as the substrate, even small quantities of lubricant (0.1%) significantly improve the dynamic flow properties, but increases in concentration do not result in further enhancement.
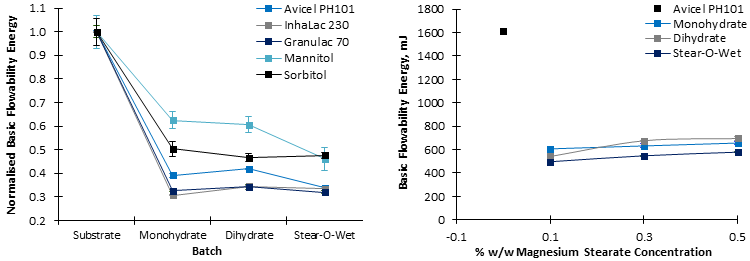
Image Credit: Freeman Technology
Bulk Testing: Compressibility
The addition of lubricant to Inhalac 230 caused significant changes in Compressibility. The Mono- and Dihydrates generated a reduction in Compressibility, but the addition of Stear-O-Wet caused an increase, indicating that the different lubricants interact with the substrate in different ways. Only moderate changes in Compressibility were observed for the other combinations of substrate and lubricant. Using Avicel PH101 as an example, the substrate showed a divergent response to the addition of different grades. Monohydrate and Stear-O-wet caused an increase in Compressibility at low concentration followed by a decrease as concentration increased. Dihydrate caused the opposite response. High Compressibility is often a sign of cohesivity within the bulk, and can prove detrimental to compaction operations such as tableting.
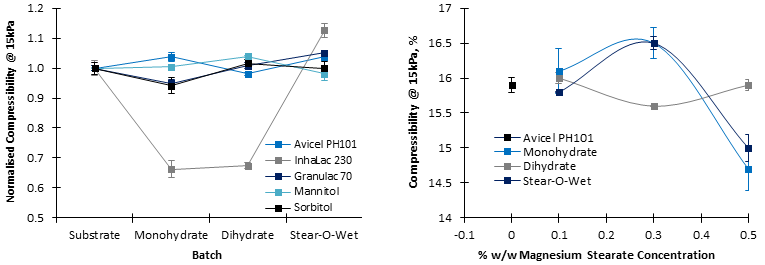
Image Credit: Freeman Technology
Shear Cell Testing
The Dihydrate and Stear-O-Wet typically increase the UYS of the substrates (drastically in the case of the Sorbitol/Dihydrate blend), indicating that these combinations would become more resistant to the onset of flow following storage (hence why lubricant is added towards the end of the process, and not in the hopper, where the effect may be detrimental). The influence of Monohydrate on UYS is dependent upon the substrate. Granulac 70 and Inhalac 230 both show a reduction in UYS, in contrast to the other three substrates. With Avicel PH101 as the substrate, the increase in UYS was shown to be not only dependant on the type of lubricant, but also on the concentration.
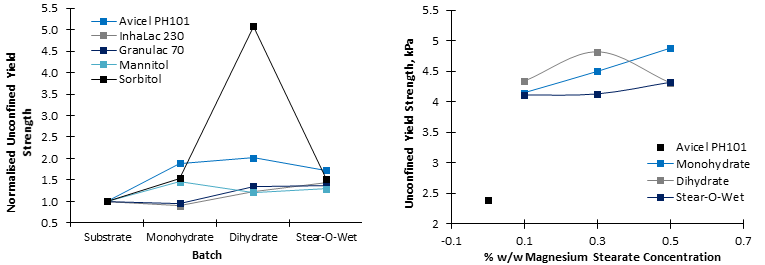
Image Credit: Freeman Technology
Conclusions
Choosing the most appropriate flow additive to resolve a processing issue, and incorporating it at an optimal level, requires a comprehensive approach to powder analysis. Testing must accurately reflect the impact of the additive on the specific substrate being used and represent conditions that are directly relevant to the manufacturing process or final application. This study quantifies how the addition of a lubricant can dramatically change the flow properties of a range of typical pharmaceutical excipients, and how the concentration level and type of lubricant is key to optimising processability and cost-efficiency. It also demonstrates that lubricant/substrate interactions are complex, even for a simple two component system, and the influence of lubricants must be quantified with respect to process conditions.

This information has been sourced, reviewed and adapted from materials provided by Freeman Technology.
For more information on this source, please visit Freeman Technology.