For millennia, humanity has embraced the use of ceramics primarily because of the abundance of raw materials and the simplicity of which basic pottery can be manufactured.
While industrial production is a more complex task than simple green kiln firing, even modern ceramics like aluminum oxide (Al2O3), boron nitride (BN) and zirconia (ZrO2) derive from source materials that are considered plentiful on earth. This is a common argument in favor of the eco-friendly characteristics of technical ceramic materials.
So, does this fundamentally natural composition of ceramics make them an eco-friendly engineering solution? This discussion explores the relationship between ceramic materials and pollution with an overview of the life cycles of state-of-the-art ceramic components.
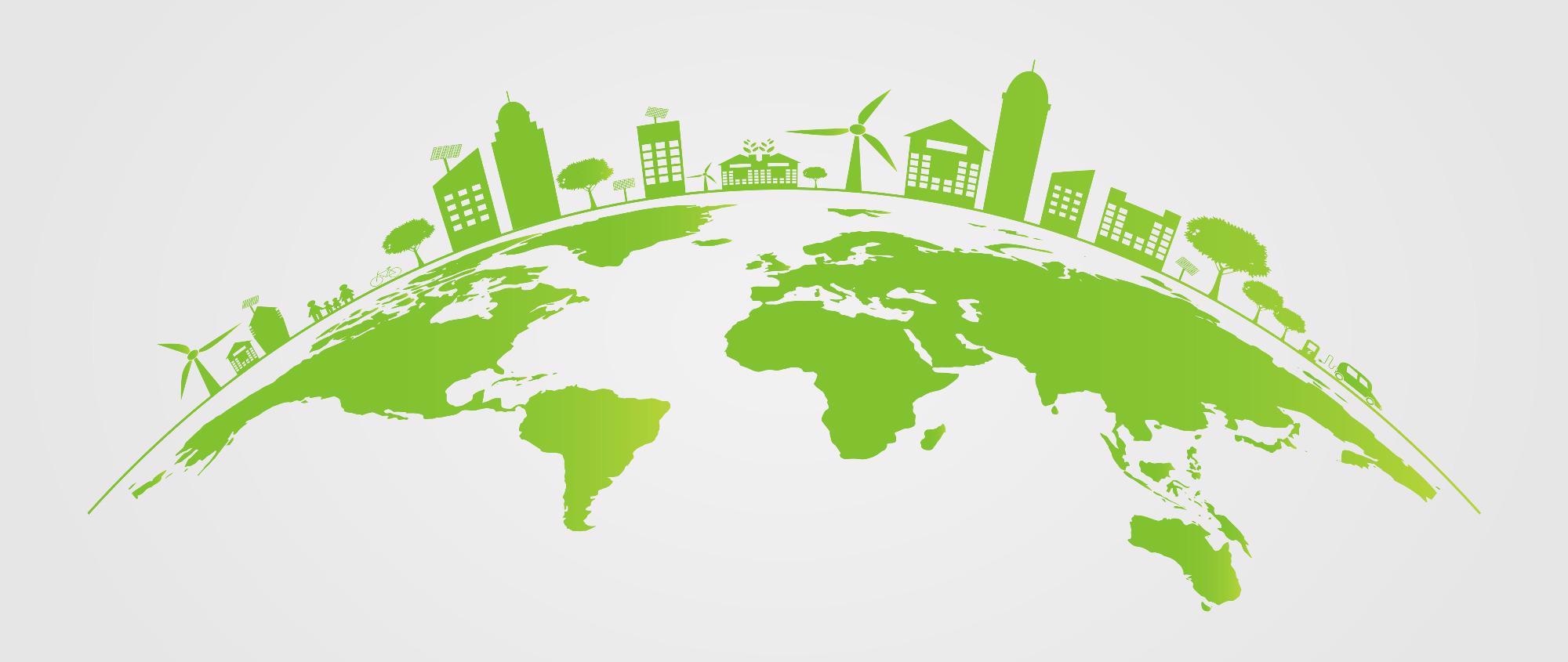
Image Credit: Shutterstock
What Makes a Sustainable Material?
International mass consumption has considerably influenced the earth’s ecology, simultaneously depleting non-renewable resources while polluting the environment.
There is profuse evidence of anthropogenic climate change, which has resulted in a gradual paradigm shift in favor of sustainable materials, which are classified as products that protect our environment during their entire life cycle. This means that in order for finished ceramic materials to be truly sustainable raw materials must be ethically sourced.
Whether classed as sustainable or not, ceramics are exceptional materials when their negligible pollutive behavior is considered across their entire length of service and beyond.
Ceramic Materials: Non-Polluting Engineering Solutions
Most technical ceramics are exclusively inert and non-toxic, which means they are largely non-polluting. For example, aluminum oxide (alumina) powder is categorized as safe for use in cosmetic products, including antiperspirant deodorant, indicating minimal-to-no-risk of bioaccumulation, cytotoxicity, immunotoxicity, or reproductive toxicity.
Meanwhile, zirconia is one of the most frequently used dental biomaterials around the world. The astounding biocompatibility of such materials is a symptom of their intrinsic inertness, which also accounts for their general lack of decomposition over time.
Recyclability is another key factor of sustainability; how effectively materials can be reused and recycled. As ceramic materials do not deteriorate naturally, they do not simply decompose into raw materials for reformation. However, once aggregated, there are novel applications on hand for so-called ceramic waste.
A number of engineers have transformed this shortcoming into a potential sustainable solution, utilizing recycled crushed ceramic rubble (RCCR) to stabilize expansive soil and advance progress in geotechnical engineering.
Studies have demonstrated the technical practicability of RCCR for stabilizing expansive, highly expansive soils (HES). Therefore, beyond its component life cycle, aggregated ceramic waste continues to contribute to a healthy environment.
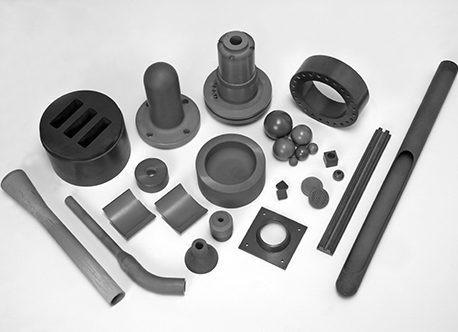
Image Credit: International Syalons (Newcastle) Ltd.
Are Technical Ceramics a Sustainable Solution? An Insight into Properties
Technical ceramics are replacing heavy duty metallic alloys and even refractories in several challenging applications and industries, establishing ceramics as a cornerstone in the production of advanced engineering materials.
This derives from their excellent all-round thermomechanical properties but can also be associated with gradual improvements in the design and development of ceramics and ceramic manufacturing.
So, what effect does this shift towards high performance, specialist material solutions have on the social responsibilities of corporations and sustainability initiatives?
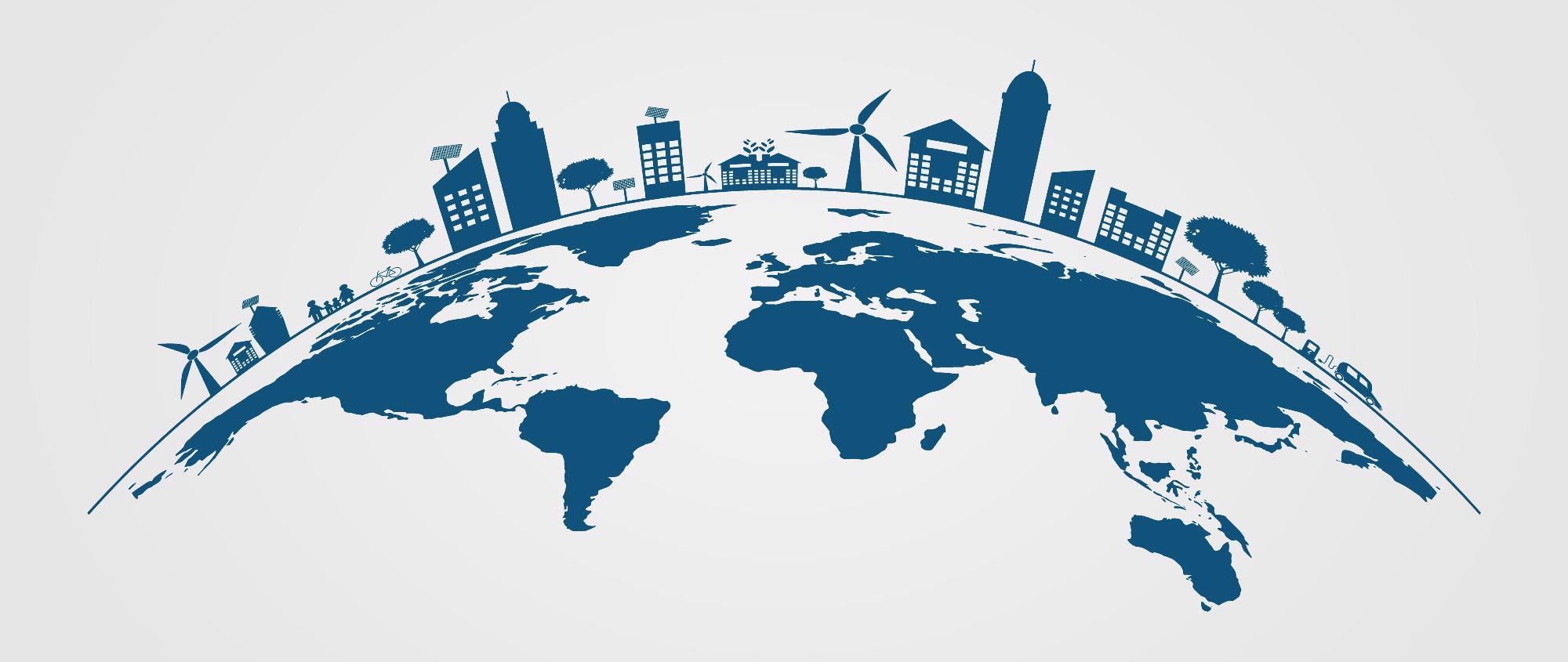
Image Credit: Shutterstock
Production & Performance: Key Drivers of Sustainability
Specialist technical ceramic solutions have attracted attention from a wide cross-section of industrial areas due to long-term performance. Technical ceramic components can tolerate higher temperatures and loading forces with a significant increase in the number of successful run cycles when compared to traditional materials.
Fundamentally, this means a considerable enhancement of efficiency, which is often a key factor in the indication of sustainability.
However, regardless of performance comparisons, without production methods that are cost-effective, it can be almost impossible for engineers to justify the expense of producing relatively new materials in industry versus conventional solutions (i.e., HSLA steel).
Yet, the incremental improvements in binding, forming and sintering processes have made the likes of alumina (Al2O3), silicon nitride (Si3N4) and zirconia (ZrO) more accessible from an economical perspective.
Cost vs. Performance vs. Sustainability
Project and supply chain managers must always consider the appropriate material for the contract, not just the job. That includes mapping out the initial to the long-term cost of materials, plus the accessibility of various solutions: all while balancing this against client-defined performance expectations.
Previously, cost versus performance was the primary driver in engineering applications, but project managers are progressively tasked with meeting the requirements of sustainability.
In short, a sustainable solution is typically defined as one with a negligible ecological footprint. Given the power-hungry processes that go into the production of advanced engineering materials, they are rarely considered to be truly sustainable.
However, technical ceramics are thought to be relatively more eco-friendly in applications where counterparts made from traditional materials are susceptible to wear or failure.
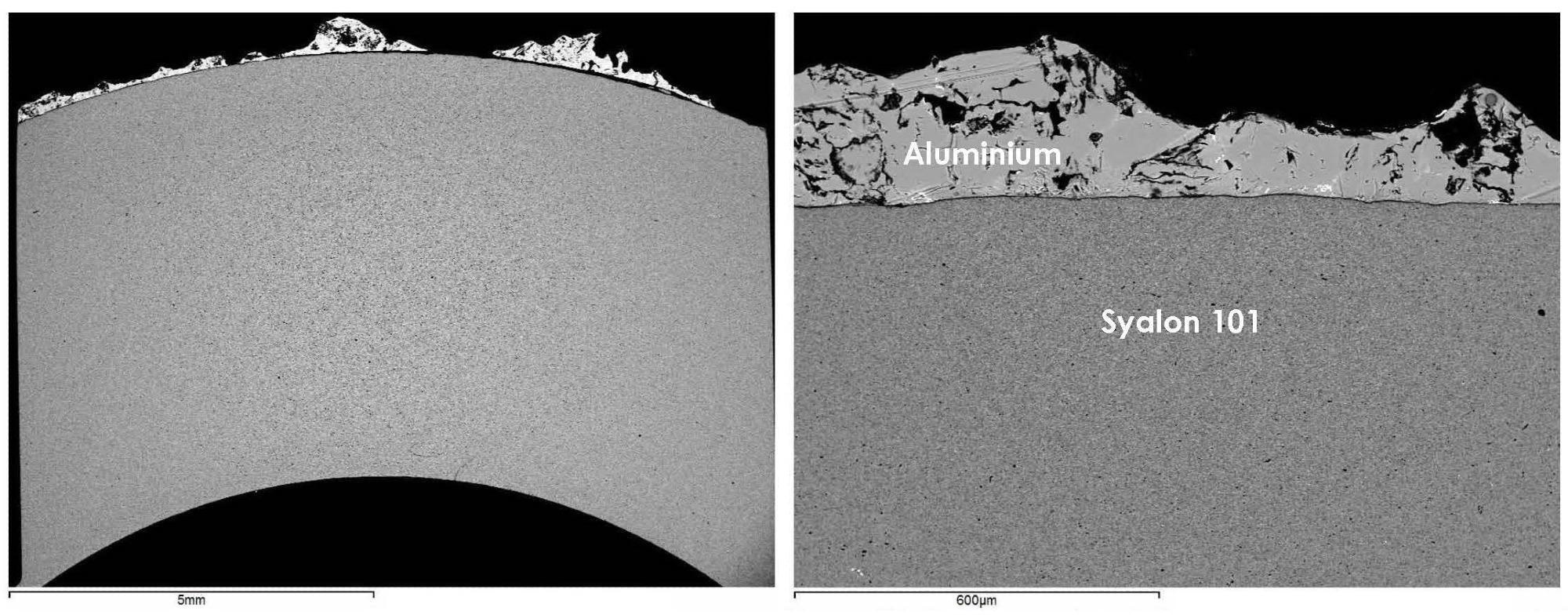
Image Credit: International Syalons (Newcastle) Ltd.
Sustainable High Duty Solutions
When considering the validity of sustainable materials in taxing and rugged environments, lifetime is a key factor. The frequency of part replacement and maintenance directly impacts the amount of waste produced, mandating both disposal and further production.
Traditional materials are becoming progressively recyclable, meaning reliance on landfills – which pollute sediments and water sources – is diminishing.
Yet, the necessity to still routinely produce replacement parts inevitably creates emissions that contribute to the greenhouse effect. Anything that can intervene in this cycle of consumable goods is a progressive change.
When using technical ceramics in any project, there are a number of design parameters that should be taken into consideration. This includes the various properties of oxide and non-oxide ceramics, plus the specific differences across ceramic grades determined by their composition, purity and henceforth.
However, with mechanical properties that are generally favorable (hardness, strength, toughness, elastic modulus, etc.) and excellent thermal characteristics (CTE, thermal conductivity, thermal shock resistance, etc.), technical ceramics offer unique heavy-duty solutions for certain demanding application areas.
Are Ceramic Manufacturing Processes Environmentally Friendly? An Insight into Production
Manufacturing advanced ceramics is an intricate multi-step process centered on the consolidation and sintering of raw mineralogical feedstocks.
Regardless of the type of ceramic (oxide or non-oxide) or the shape, size, structure, or complexity of the completed part, it is the densification stage of production that reveals the exceptional thermomechanical properties of technical ceramic materials.
However, it is also the most energy-intensive link in the manufacturing chain of advanced ceramics. Therefore, it is difficult to reconcile ceramic manufacturing from an environmental perspective due to the power-hungry nature of sintering processes.
So, it is worth considering key ceramic manufacturing processes to see whether they could be regarded as environmentally friendly.
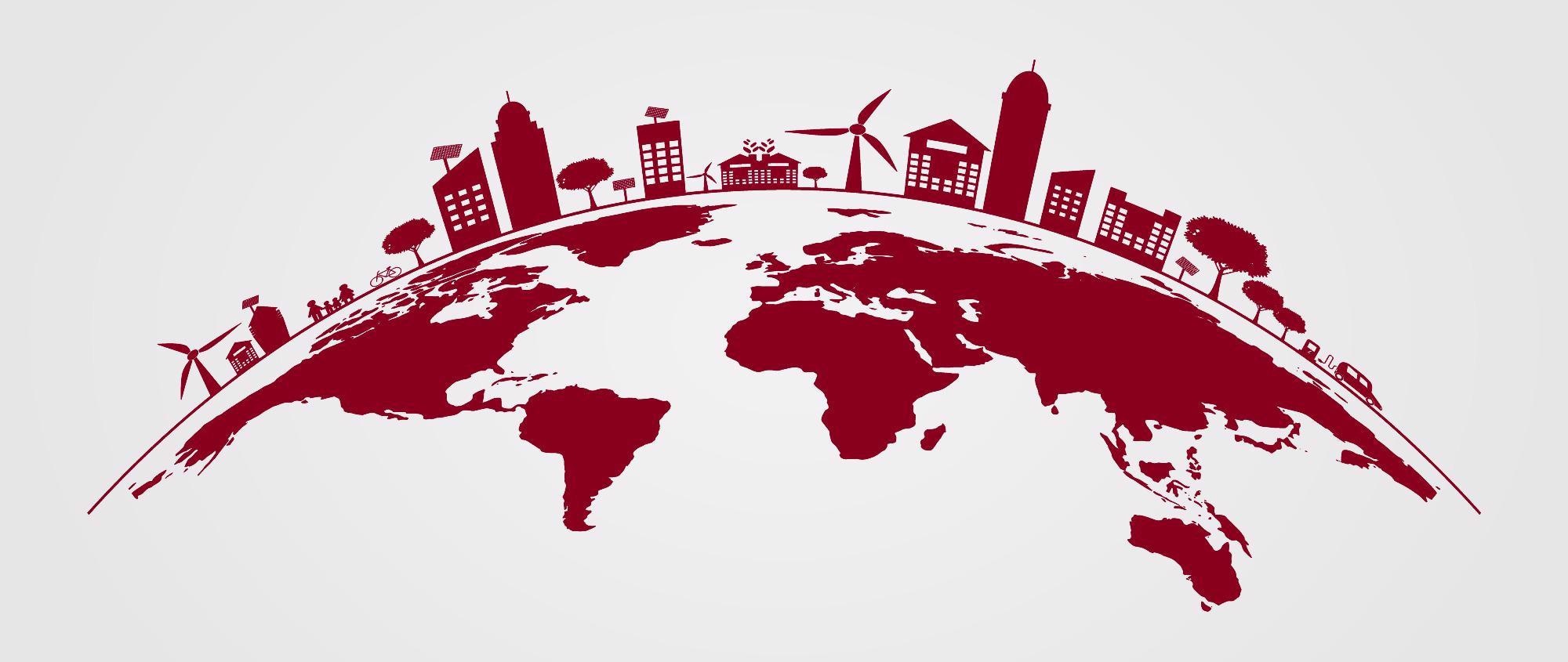
Image Credit: Shutterstock
Technical Ceramic Forming Processes
The green forming stage of ceramics manufacturing takes place when raw powders are amalgamated into a ‘green body’ using applied pressure.
Techniques that are common include uniaxial pressing, compacting feedstocks into a rigid shape using a tool steel die; isostatic pressing, where spray-dried powder in a polyurethane/rubber bag is exposed to isostatic pressure; extrusion, forcing a plasticized paste-like mixture through an orifice; and slip casting, which utilizes an aqueous slip and a porous mold.
It is hard to assess an overall ecological footprint due to the diversity of forming processes. For instance, applied pressures in uniaxial or isostatic pressing can range from 20—700 MPa, with high compaction pressures generally translating to higher green compact strength.
Mechanical green forming methods such as these typically depend on moderately energy-intensive processes such as electrically derived pneumatic or hydraulic pressures – yet, these processes are gradually improving in efficiency. High volume commercial potteries serve as an example where pressure is a chosen application.
To reduce casting time and improve throughput, slip is pushed into porous molds, speeding up the natural capillary action necessary for slip casting and reducing casting times by a factor of 10. In this case, traditional slip casting would be commercially impracticable.
However, the majority of ceramic forming processes are not thermal in nature —with the notable exception of hot isostatic pressing (HIP)— so the forming stage is relatively ecological.
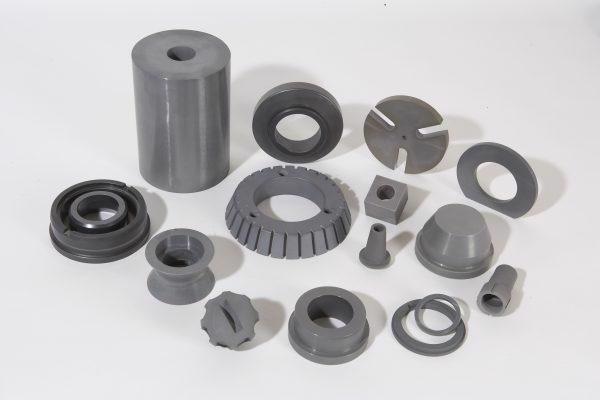
Image Credit: International Syalons (Newcastle) Ltd.
Ceramic Sintering Processes
After consolidation, the green body is fired at extreme temperatures via either solid-state or liquid-phase sintering.
While potteries and ceramic construction material manufacturers rely heavily on traditional gas-powered furnaces, technical ceramic sintering very rarely takes place in open flames because of the ceramic’s sensitivity to atmospheric conditions and the necessity for precision temperature control.
Instead, extremely high temperatures requisite to densification are produced utilizing electrical resistance of metallic or composite heating elements.
Utilizing renewable energy sources such as hydroelectricity, solar and wind means the sintering processes could have a low environmental impact in contrast to other manufacturing processes.
Here, an opportunity is presented for technical ceramics manufacturing to embrace the green technology revolution, and by doing so, significantly reduce the environmental costs affiliated with continuous material production.
Environmental Engineering
Environmental engineering is a comparatively new term that is distinct from clean energy and/or sustainable innovations, as it calls attention to systems that actively protect the environment.
One of environmental engineering's great successes is the lambda sensor, an exhaust gas oxygen (O2) sensor for the monitoring of air/fuel ratios in vehicles by providing feedback to catalytic converters for better reductions in engine emissions.
Advanced ceramics, including alumina and zirconia, are commonly used to produce lambda sensor components because of their excellent thermomechanical properties, which allow them to tolerate the severe conditions of combustion engines for prolonged periods of service.
Clean Energy
Parallel to the expansion of the environmental engineering sector is the more familiar market of clean energy. Today, there is a broad consensus that a global movement towards clean energy is crucial to how we can preserve the natural systemic balance of the planet’s ecosystems.
This means significantly reducing greenhouse gas emissions by embracing hybrid and electric vehicles while obtaining energy from renewable sources like wind and solar.
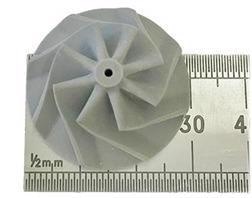
Image Credit: International Syalons (Newcastle) Ltd.
Advanced ceramics continuously play a significant role in clean energy production, from specialized piezoelectric systems for solar exchangers to solid oxide fuel cells (SOFCs) and high temperature roller bearings in high efficiency wind turbines.
Innovative transformations in additive manufacturing of technical materials facilitate the manufacture of more complex, long-lasting systems for hyper-efficiency energy conversion systems. For instance, 3D printed microturbines and impellers made up of silicon nitride (Si3N4) may offer novel solutions for hybrid vehicle motor recuperation.
To discover how advanced ceramics could benefit your sustainability initiatives, contact a member of the International Syalons team today for more information.
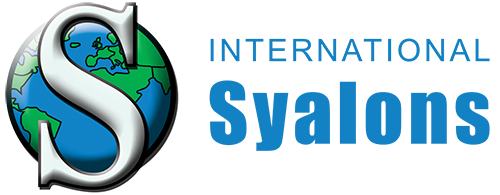
This information has been sourced, reviewed and adapted from materials provided by Internatrional Syalons.
For more information on this source, please visit International Syalons.