Efficiency can be defined as “the good use of time and energy in a way that does not waste any”1. Fig. 1 shows a simple process diagram showing basic input, process, output, and loss.
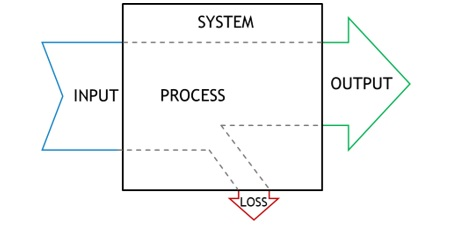
Fig. 1 - Process diagram showing basic input, process, output, and loss.
This diagram represents many industrial processes where industrial inputs might include time, energy, material, knowledge, motivation or even health and safety, and where “loss” can be the undesirable waste of any input. Loss is expected to have a detrimental effect on a business’ productivity, overheads, profit, and environmental impact, and so should be reduced where possible.
Properties of Sialon
Sialon (Si-Al-O-N) is a silicon nitride-based (Si3N4) advanced ceramic which contains alumina (Al2O3) and rare earth oxides such as yttria (Y2O3), magnesia (MgO), or ytterbia (Yb2O3). Like many advanced ceramics, sialons offer an outstanding set of high temperature themo-mechanical properties compared to most metal, polymers and composites. As summarised in Fig. 2, advanced ceramics typically offer greater high temperature stability, hardness, wear and corrosion resistance, stiffness and compressive strength.
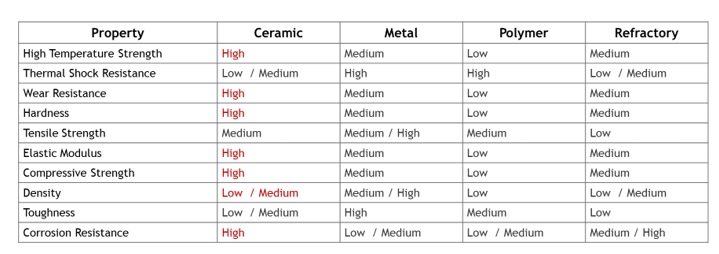
Fig. 2 – Table summarising general material properties
For specific applications it is important to consider each of a material’s properties carefully, and to avoid design features which may lead to premature component failure. For advice, read our useful guide on Designing with Ceramics.
Each of the material properties which sialon ceramics offer can be used to significantly improve the efficiency of a system, when applied correctly. Below are some examples where losses have been reduced due to the use of sialon in industry.
Industrial Wear – Nozzles
As automotive manufacturers strive to produce lighter more efficient vehicles many have moved to using aluminium gearbox casings. While this saves considerable weight, the aluminium must be coated with bronze (CuSn) to meet the required hardness. Prior to coating, the aluminium surface must be roughened by a grit or sand blasting process to provide a key for the coating to adhere to. The process of grit blasting is extremely abrasive and wear intensive on the nozzle from which the alumina grit is shot.
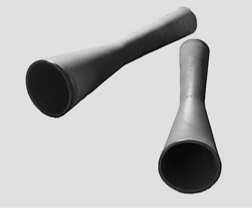
Fig. 3 – Syalon 050 shot blast nozzles.
A recent study by International Syalons found that Syalon 050 nozzles lasted over 814 hours of use, which is outstanding in comparison to tungsten carbide (WC), one of the hardest engineering materials available, which lasted only 20-25 hours of use. Based on these results, the prices of each consumable nozzle and the downtime per nozzle change, and it was estimated our customer would save approximately £6,500/year per machine, and up to £250,000/year across the customer’s Group. This is a great example of how one material property, in this case hardness, results in an improved operational efficiency (consumable wear and downtime) to significantly improve productivity and reduce costs.
Molten Metal Processing – Tubes
Aluminium is the most abundant metal on the planet. Its low density and corrosion resistance have seen it become one of the world’s most commonplace materials as a wide range of alloys for use in construction, automotive transport and aerospace, and food and packaging industries. During the manufacturing of aluminium products such as vehicle alloy wheels or rolled products such as drinks cans, a furnace such as the one shown in Fig. 4 is charged with aluminium and heated to its melting point (approx. 650-750 °C depending on the alloy composition). At this temperature molten aluminium is extremely corrosive, and any surface in contact with the melt must be very resistive to attack and thermally stable to survive.
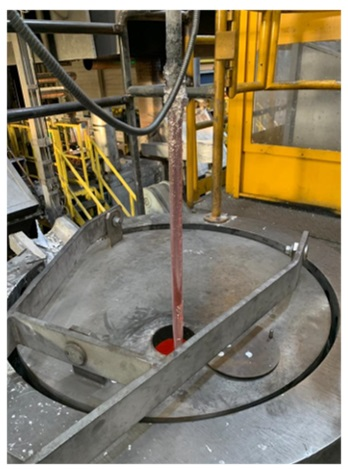
Fig. 4 – Syalon 101 thermocouple protection sheath in use at an aluminium foundry.
Syalon 101 is a β-sialon silicon nitride-based advanced ceramic with outstanding non-wetting behaviour and corrosion resistance to molten aluminium. Also, with a maximum operating temperature of 1200 °C in air and a thermal shock resistance of Δ900 °C it is stable in even the most demanding aluminium processing environments. In comparison to aluminium-titanate (Al2TiO2) or nitride bonded silicon carbide (NBSC) Syalon 101 offers a greatly improved service life, with many protection tubes lasting up 12 months use if handled and maintained correctly. This, in addition to a lower density and higher strength allows for thinner tube walls and a more efficient heating and temperature measurement system within the furnace. Overall, switching from cast iron or low-grade refractories to Syalon 101 can significantly reduce annual consumable and energy costs, as well as reducing the safety risks and downtime associated with frequently replacing tubes.
Automotive Manufacturing – Weld Pins
Captive nut welding is a process commonly used by automotive manufacturers prior to the chassis and body panel assembly stages. It often involves spot welding a nut to a pre-cut hole in a sheet of metal so that later a second section of the vehicle can be quickly fixed to it. A weld location pin is used ensure the nut and hole are correctly positioned. This process can be repeated several thousands of times per day on a single manufacturing line, so it is vital that each pin meets the necessary requirements of the demanding environment. During each weld cycle, firstly the hole of a sheet of metal is placed over the pin, then a nut is located on to the top of the pin and is held tightly to the metal sheet. Welding electrodes then apply a localised current through the nut and sheet to melt the metal and form a weld. The process is carefully controlled to melt just the right amount of material, and the weld time often takes only 10-100 milliseconds. During this time the weld region and pin are subjected to mechanical stress, high currents, extreme thermal shock, and corrosion from molten metal and weld splatter.
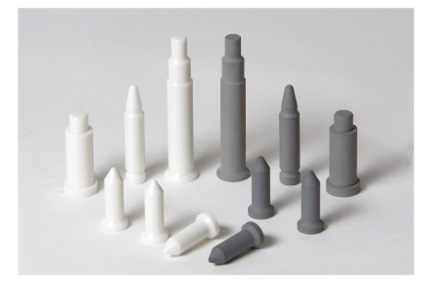
Fig. 5 – Zirconia and sialon weld location pins.
Zirconia and sialon ceramic weld location pins offer substantial benefits over low-cost steel or ceramic-coated metal pins. These advanced materials can withstand the extreme temperature fluctuations, whilst offering good non-wetting properties from molten metal weld splatter. As both ceramics are electrically insulating throughout the material there is no possibility for the current to pass through the pin causing arcing between the electrodes, unlike coated pins which become conductive once the ceramic coating has worn away from the metal substrate, resulting in poor quality welds. Aside from these, the two most attractive properties which zirconia and sialon ceramics offer are are fracture toughness and wear resistance. Because of the output demands on the automotive industry the whole process of spot welding a captive nut to a metal sheet usually takes less than 15 seconds, and is often robotic or semi-automated and operates 24/7; hence, the pins must be able to endure many thousands of cycles without wearing, and withstand impacts from misaligned holes or clumsy operators.
Considering that a five-minute production line stoppage, once per day, can result in a loss of 10 vehicles produced per week, equating to about €7 million in lost revenue per year2, it is vital that the efficiency of a production line is maintained through the use of high quality advanced ceramic pins. It has been shown that a sialon pin can last up to 100,000 weld cycles; more than double a typical metal pin. In practice, this significantly reduces production line stoppage and increases output.
Learn more in A Guide to Technical Ceramics.
Technical Ceramic Products from International Syalons
In summary, the material properties which sialon and zirconia advanced ceramics offer such as high temperature strength and thermal shock stability, hardness and wear resistance, low density, corrosion resistance, and electrical resistivity are enabling a wide range of industries to improve the efficiency of their processes by increasing operating temperatures or feed rates and speeds, by reducing consumable usage and equipment downtime, and improved sensitivity or precision. Each efficiency saving which is applied to a process can result in a reduction in wasted energy, time, and costs, or detrimental environmental impacts, which are vital for business sustainability.
International Syalons is one of the UK’s leading suppliers of advanced ceramics, offering a versatile line of sialon and zirconia ceramics.
If you would like more information about the full range of advanced ceramics, please do not hesitate to contact a member of the International Syalons team today.
References
- https://dictionary.cambridge.org/dictionary/english/efficiency
- https://cordis.europa.eu/article/id/36214-new-automatic-welding-system-makes-car-production-cheaper