Introduction Solid oxide fuel cell (SOFC) is a clean and highly efficient electric power generator. A typical SOFC with yttria-stabilized zirconia (YSZ) electrolyte is operated at about 1273 K. A decrease of the solid electrolyte thickness enhances the power density. Rare earth-doped ceria (RDC) electrolyte has a higher oxide ion conductivity than YSZ, which is effective to lower the operation temperature of SOFC [1]. On the other hand, the electric power density is also influenced by the electrochemical properties of electrodes. Sr-doped samarium cobaltite cathode with a composition Sm0.5Sr0.5CoO3 (SSC) for SOFC with RDC electrolyte has a high electronic conductivity of 103 S/cm at 769-1176 K [2]. In addition, SSC has a lower overpotential than LaxSr1-xCoO3 [3]. In this study, SSC and RuO2-doped SSC were characterized as a cathode of SOFC with Sm-doped ceria (SDC) electrolyte. Ni-SDC anode was also prepared to evaluate the cell. Experimental Procedure Electrolyte Material The oxalate solid solution (Ce0.8Sm0.2)2(C2O4)3 was produced by adding the mixed nitrate solution (0.2 M) of Ce and Sm into a 0.4 M oxalic acid solution [4]. The coprecipitated oxalate powder was decomposed to a polycrystalline oxide solid solution by heating up to 873 K. After milling of the as-calcined SDC with alumina ball at 80 rpm for 24 h, the specific surface area of the SDC was 41.7 m2 /g, which corresponded to 20 nm diameter of equivalent spherical particles. The electrolyte of 16 mm diameter and 1 mm thickness for cell test was formed by filtration of an aqueous suspension of 35 vol% SDC with polyacrylic ammonium of 0.25 mg/m2 –SDC powder at pH 8 through a gypsum mold. Then the disk was pressed isostatically under a pressure of 196 MPa. The green compact was sintered at 1773 K for 4 h in air. Electrode Materials A SDC powder calcined at 873 K was immersed in a 1.4 M Ni (NO3)2 solution at the volume ratio of Ni / SDC = 30 / 70 and freeze-dried. The mixed anode powder was heated at 623 K for 1 h in air. Two types of cathode materials were prepared. (A) A mixed solution of Sm (NO3)3, Co (NO3)2 and SrCl2 at the composition of Sm0.5Sr0.5CoO3 was coprecipitated at pH 10 and freeze-dried. This dried SSC powder was heated at 1473 K for 4 h in air. (B) A high purity Ru powder (purity > 99.99 mass%, 1.65 µm diameter) was oxidized at 1473 K for 3 h in air. This powder was mixed with SSC powder calcined at 1473 K at the volume ratio of RuO2 / SSC = 50 / 50. The phases produced in cathode were identified by X-ray diffraction (RAD-2B, Rigaku Co., Japan). The microstructures of the electrodes were observed using a scanning electron microscope (FE-SEM, JSM-6330F, Nihon Denshi Co., Japan). Cell Test The SSC, RuO2-doped SSC and Ni-SDC powders were dispersed at 15 vol% solid in the mixed solution of 90 vol% ethanol – 10 vol% ethyleneglycol. The prepared suspension was formed with screen (mesh: 250 µm) of 5 mm diameter thread on the surfaces of SDC electrolyte (> 98 % theoretical density) of 15 mm diameter and 600-700 µm thickness. The printed anode material was heated at 1573 K for 4 h in air. Similarly, the printed cathode material was heated at 1273 K for 1 h in air. The Pt wire reference electrodes were fixed on both the SDC surfaces with Pt paste at 1173-1273 K. A Pt mesh was attached to each electrode with Pt paste. The SDC electrolyte with the cathode and anode was set to an alumina holder using a glass O-ring. The glass O-ring was heated to 1173 K to seal the electrolyte and cooled to 1073 K to measure the cell performance (As-510, NF Kairosekkei Block Co., Japan). Air and a 3 vol% H2O-containing H2 fuel were fed at 100 ml/min to the cathode and anode, respectively. A direct current-voltage relation and AC impedance of the cell in the frequency range from 0.01 Hz to 100 kHz at the current of 10 mA were measured at 1073 K. Results and Discussion Phases of Cathode Sm2O3 reacted with CoO to form SmCoO3 at 1073 – 1273 K. SrCl2 was stable at 1073 K in air. Some CoO changed to Co3O4 at 1273 K. SmCoO3 reacted with Co3O4 and SrCl2 to form Sm0.5Sr 0.5CoO3 at 1473 K. Further heating to 1573 K split (111), (200), (211) and (220) diffraction lines of SSC into two or three, respectively. This result may be related to the phase separation of Sm0.5Sr 0.5CoO3 solid solution into some kinds of solid solutions with different compositions. On the other hand, no new phase was produced by heating the mixture of 50 vol% RuO2- 50 vol% SSC for 4 h at 1173 K in air. However, RuO2 reacted with SSC to form SrRuO3 and Co2RuO4 at 1273 K. Microstructure of SSC Cathode / SDC Electrolyte / Ni-SDC Anode Cell Figure 1 shows the cross section of SSC cathode / SDC electrolyte/ Ni-SDC anode cell after the operation at 1073 K using a 3 vol% H2O-H2 fuel. The cell consisted of dense SDC of 670 µm thickness, porous SSC cathode of 150-225 µm thickness and porous Ni-SDC anode of 100 µm thickness. The microstructure of another cell with RuO2-doped SSC cathode was also observed. This cell consisted of SDC of 617 µm thickness, porous RuO2-doped SSC cathode of 103-130 µm thickness and porous Ni-SDC anode of 83-88 µm thickness. 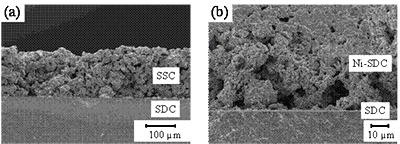 Figure 1. Microstructures of (a) cathode and (b) anode of the SSC / SDC / Ni-SDC cell. Terminal Voltage and Power Density Figure 2 shows the terminal voltage (a) of the cell with SDC electrolyte, Ni-SDC anode and SSC or RuO2-doped SSC cathode using a 3 vol% H2O-containing H2 fuel at 1073 K. The open circuit voltage (E0) was 0.82 and 0.55 V for the cells with SSC cathode and RuO2-doped SSC cathode, respectively. The maximum power density and the corresponding current density were 112 mW/cm2 and 255 mA/cm2 for SSC cathode and 170 mW/cm2 and 560 mA/cm2 for RuO2-doped SSC cathode, respectively. Addition of RuO2 to SSC cathode was effective to increase the power density. The open circuit voltage of the cell is given by Eq.(1) [5] (1) where R is the gas constant (8.314 J/mol.K), T the temperature (1073 K), F the Farady constant (9.649x104 C/mol), Po2(c) the oxygen partial pressure (2.10x104 Pa) at cathode and Po2(a) the oxygen partial pressure at anode, σi the oxide ion conductivity (0.118 S/cm) at 1073 K [1], σe the electronic conductivity at 1073 K and n (= 5.19) and C (= 1.51x10-4 S/cm) are experimental constants for σe (σe = CPo2-1/n) [6]. The Po2(a) value measured by yttria-stabilized zirconia oxygen gas sensor was 4.0x10-17 – 9.4x10-17 Pa and the E0 value was calculated to be 0.970 and 0.977 V for the cells with SSC cathode and RuO2-doped SSC cathode, respectively. The measured E0 values became lower than the calculated values. The remarkable decrease of OCV for the cell with RuO2-doped SSC cathode is explained as follows. As mentioned in Section 3.1, RuO2 reacted with SSC to form SrRuO3 and Co2RuO4 at 1273 K. This reaction releases Sm2O3 component. The formed Sm2O3 may dissolve in the electrolyte by substituting for CeO2 (Ce0.8-xSm0.2+xO1.9-x/2). The increased Sm content in the electrolyte decreases the oxide ion conductivity [7], leading to the decrease of OCV in Eq.(1). 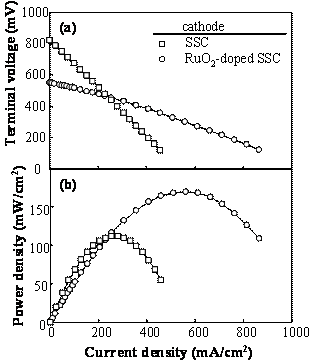 Figure 2. Terminal voltage (a) and electric power density (b) as a function of current density for the SSC or RuO2-doped SSC cathode / SDC electrolyte / Ni-SDC anode cell using a 3 vol% H2O-containing H2 fuel at 1073 K. Ohmic Resistance and Overpotential The ohmic resistance and overpotential at the cathode or anode were separated by analyzing the AC impedance spectroscopy during the measurement of power density. The voltage drop by ohmic resistance and overpotential between cathode (C) and reference electrode (RC) of the SSC/ SDC/ Ni-SDC cell at 1073 K increased with an increase of current density (Figure 3(a)). Figure 3(b) shows the voltage drop between C and RC when RuO2 was added to the cathode. The voltage drop at the cathode was greatly reduced by the addition of RuO2. No overpotential was measured and the ohmic resistance dominated the voltage drop. This result may be caused by (1) the increase of electronic conductivity at the cathode and (2) the acceleration of diffusion of oxide ion at the interface between RuO2 and SSC. As well known, the diffusion coefficient of ion is usually larger for grain boundary diffusion than for lattice diffusion. The RuO2 addition increases the length of triple phase boundary of the mixed conductor (SSC)- electronic conductor (RuO2)- O2 gas at the cathode. Oxygen molecules adsorbed on the triple phase boundaries easily react with the electrons supplied from RuO2 and the formed oxide ions diffuse along the grain boundaries between SSC and RuO2. Figure 4 shows the voltage drop of the RuO2-doped SSC/ SDC/ Ni-SDC cell at 1087 K. The voltage dropped in the following order of the factors : ohmic resistance of anode > ohmic resistance of SDC electrolyte > ohmic resistance of cathode > overpotential at anode > overpotential at cathode. 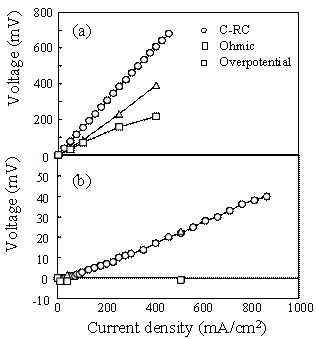 Figure 3. Terminal voltage drop between cathode(C) and reference electrode(RC) of (a) the SSC / SDC / Ni-SDC cell and (b) the RuO2-doped SSC / SDC / Ni-SDC cell at 1073 K. 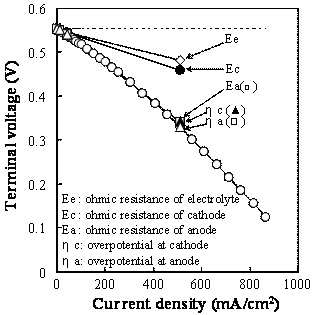 Figure 4. Factors of voltage drop for the RuO2-doped SSC / SDC / Ni-SDC cell at 1073 K. Conclusions A single phase of Sm0.5Sr0.5CoO3 (SSC) was formed by heating the freeze-dried mixture of Sm(NO3)3, Co(NO3)2 and SrCl2 at 1473 K. SSC reacted with RuO2 to form SrRuO3 and Co2RuO4 at 1273 K. Power densities of 112 and 170 mW/cm2 at 1073 K were measured for the SSC/ SDC/ Ni-SDC cell and RuO2-doped SSC/ SDC/ Ni-SDC cell using a 3 vol% H2O-containing H2 fuel, respectively. Addition of RuO2 to SSC cathode reduced the ohmic resistance and overpotential at the cathode, and increased the power density. The dominant factors to reduce the terminal voltage of the cell with RuO2-doped SSC were the ohmic resistance of Ni-SDC anode and SDC electrolyte. References 1. S. Sameshima, H. Ono, K. Higashi, K. Sonoda, Y. Hirata, and Y. Ikuma, “Electrical Conductivity and Diffusion of Oxygen Ions in Rare Earth-doped Ceria”, J. Ceram. Soc. Jpn., 108 (2000) 1060-1066. 2. T. Ishihara, M. Honda, T. Shibayama, H. Minami, H. Nishiguchi and Y. Takita, “Intermediate Temperature Solid Oxide Fuel Cells Using a New LaGaO3 Based Oxide Ion Conductor”, J. Electrochem. Soc., 145 (1998) 3177-3183. 3. M. Koyama, C. Wen, T. Masuyama, J. Otomo, H. Fukunaga, K. Yamada, K. Eguchi, and H. Takahashi, “The Mechanism of Porous Sm0.5Sr0.5CoO3 Cathodes Used in Solid Oxide Fuel Cells”, J. Electrochem. Soc., 148 (2001) A795-A801. 4. K. Higashi, K. Sonoda, H. Ono, S. Sameshima and Y. Hirata, “Synthesis and Sintering of Rare Earth-doped Ceria Powder by Oxalate Coprecipitation Method”, J. Mater. Res., 14 (1999) 957-967. 5. Y. Hirata, S. Yokomine, S. Sameshima, T. Shimonosono, S. Kishi and H. Fukudome, “Electrochemical Properties of Solid Oxide Fuel Cell with Sm-Doped Ceria Electrolyte and Cermet Electrodes”, J. Ceram. Soc. Jpn., 113 (2005) 597-604. 6. T. Shimonosono, Y. Hirata, Y. Ehira, S. Sameshima and T. Horita, “Electronic Conductivity Measurement of Gd- and Sm-Doped Ceria Ceramics by Hebb-Wagner Method”, J. Ceram. Soc. Jpn., Suppl., 112 (2004) S616-621. 7. H. Yahiro, Y. Eguchi, K. Eguchi and H. Arai, “Oxygen Ion Conductivity of the Ceria-Samarium Oxide System with Fluorite”, J. Appl. Electrochem., 18 (1988) 527-531. Contact Details |