Spray forming combines the metallurgical benefits of fast cooling during solidification to produce low segregation, refined microstructures with the cost advantages associated with near net shape processing. It can offer particular advantages in manufacturing certain components, such as rings and casings for aero-engines. As aero-engine diameters increase to deliver more power, manufacturing the large diameter rings and casings that are required becomes more difficult. Spray forming offers a route to manufacture these large components more easily, and it also allows the possibility of using alloys which cannot currently be used in other manufacturing methods. It provides a route for producing components with enhanced properties and ultimately could lead to larger, more powerful aeroplanes. History Spray forming was commercialised by Osprey Metals of Neath in the 1970s and consequently is commonly referred to as the Osprey process. Holders of Osprey licenses include major Al, Cu, Fe and Ni alloy manufacturers. Production facilities at PEAK, Germany produce high Si containing Al alloys (3,500 tonnes per year) to be used as cylinder liners for Mercedes, and Sprayform Technologies International (STI), USA manufactures large diameter Ni rings (500 tonnes per year per shift) for the aerospace industry. The Process The spray forming process is shown schematically in figure 1. The first step is Ar or N2 gas atomisation of a melt stream to produce a spray of 10-500μm droplets. These droplets are deposited at a growing sprayed preform surface translated under the spray cone, where any residual liquid in the sprayed preform cools relatively slowly and solidifies. 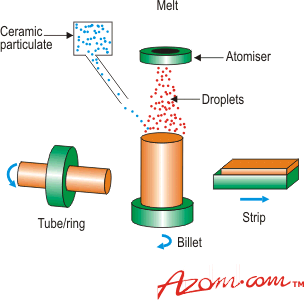 | Figure 1. Schematic of the spray forming process. | Characteristics of Spray Formed Materials Billet, ring and plate geometries can be manufactured, as well as particulate reinforced metal matrix composites (MMCs) by the co-deposition of a solid ceramic phase, typically 5-15μm SiC particulate. Sprayed preforms have characteristically equiaxed grains of 15-50μm diameter at all preform locations, and low- levels of micro-segregation and macro-segregation. The microstructure of the sprayed preform is crucially dependent upon the average spray solid fraction at deposition, which usually lies critically in the range 0.3 to 0.8. Sprayed preforms always contain a residual porosity of 1-3vol%, and require downstream processing by extrusion, hot isostatic pressing (HIPing), rolling etc to full density. Advantages of Spray Forming Consolidated spray formed materials have shown consistently equivalent or superior tensile, toughness, fatigue and creep behaviour in comparison with conventionally processed equivalents. The economic benefit of near net shape processing by spray forming is component sensitive but, for example, the removal of processing steps in the manufacture of large diameter Ni superalloy aero-engine rings is expected to realise savings of up to 30% compared with cast and wrought methods or powder processing. Commercial Evaluation Programmes The United Kingdom In the UK, the commercial viability of spray forming large diameter Ni superalloy preforms for aerospace has been explored by Allvac-SMP, Sheffield, in collaboration with Osprey and Danish Steel. One tonne preforms of up to 400 mm in diameter and 1200 mm in length have been produced. The feasibility of spray forming 600 mm diameter and 2700 mm long preforms as feed stock with improved forgeability in down-stream processes such as ring rolling and/or HIPing is now under investigation. The Unites States of America There are two major programmes in the US to develop spray formed Ni superalloys. The objective of a programme involving General Electric and Teledyne Allvac is to develop spray formed and forged compressor and turbine discs. Because these critical components are fatigue sensitive it is essential to eliminate all refractory based inclusions. A pilot plant has therefore been commissioned which combines electroslag remelting of vacuum induction melted (VIM) feedstock, cold crucible induction melting and a cold induction guide for bottom pouring of the melt. This arrangement removes the need for ceramic crucibles and nozzles, and is capable of producing 280 kg preforms at up to 20 kg per min. Sprayform Technologies International The Sprayform Technologies International programme (a joint venture between Pratt & Whitney and Howmet) aims to manufacture large diameter spray formed rings and casings. In this case, VIM and spraying onto a large diameter rotating steel mandrel have been combined, and 1400 mm diameter rings can be manufactured directly from 2700 kg melts. High pressure turbine casing rings for the PW4000 engine, produced in Ni superalloy IN718, have been spray formed and HIPed and/or ring rolled, and have been engine tested successfully. Spray Forming Nickel Superalloys Characteristics The spray formed Ni superalloy microstructure typically consists of fine equiaxed grains, low in chemical segregation, with refined carbides and reduced formation of embrittling topologically close packed (TCP) phases. The resulting improvements in processing, hot working and machining have the potential to reduce the time for component manufacture and reduce costs. For example, lower flow stresses and increased forgeability in comparison to conventional cast and wrought materials have allowed a greater than 50% reduction of spray formed Ni superalloy rings in only two roll passes. Machining of final detail is one of the most costly stages in the manufacture of aero-engine rings and casings. Spray formed Ni superalloys have shown a 25-35% increase in cutting speed combined with a more than four-fold increase in tool life for Ni superalloy U720. Properties Processing improvements are not achieved at the expense of mechanical properties. The ultimate tensile and proof strengths of spray formed and consolidated IN718 and U720 have been shown to be comparable with their cast and wrought counterparts. Furthermore, creep stress rupture and low cycle fatigue performance is comparable or slightly improved. Mechanical property improvements have also been realised in the steel Jetehete M152, which is used for the manufacture of aero-engine casings. Strength, ductility, creep strain and hardness have all been shown to lie within aerospace specifications, even in the as spray-formed state. Consequently, for some components there is potential to derive maximum benefit from near net shape spray forming without the need to develop properties with downstream thermomechanical processing. Ar vs N2 for the Atomising Gas A technological and scientific controversy surrounds the optimum spray forming of Ni superalloys and the use of either Ar or N2 atomising gas. If Ar is employed, porosity closed during HIP consolidation may reappear during welding operations or at elevated temperature in service - this is known as thermally induced porosity (TIP). A TIP response occurs because of the very low Ar solubility in Ni and may severely compromise mechanical performance. Ar is also more expensive than N2. If N2 is used as the atomising gas, then TIP response is reduced or eliminated because N2 reacts readily with the common alloying addition Ti to form TiN. However, TiN formation itself may be detrimental to mechanical properties, particularly fatigue life, and can introduce a cost penalty in the recycling of any overspray powder. Spray Forming Aluminium Alloys The exploitation of the homogeneous microstructure afforded by the rapid cooling during spray forming has been investigated for Al airframe applications by several Al alloy manufacturers. Cospray and Alcan International in the UK investigated spray formed Al alloys in the 1980s and early 1990s using a 300 kg billet pilot plant. More recently an Al-Si billet 300mm diameter and 2.5m long has been produced by PEAK. Aluminium-Lithium Alloys Developments at Cospray initially focused on conventional 8090 and 8091 Al-Li alloys. In comparison with direct chill (DC) cast alloys, the spray formed alloys had a substantially refined grain size of 20-50μm and more uniformly distributed second phase particles and grain boundary precipitation. Billets were either HIPed, forged or extruded to heal as-sprayed porosity. Similarly to Ni superalloys, the spray formed microstructure led to superior properties when compared with conventionally processed materials. Moreover, contaminant Na and H levels were reduced which further increased ductility and fracture toughness. Aluminium-Lithium-Zirconium Alloys New alloys containing Li and Zr additions beyond those that can be achieved in DC cast materials have been subsequently developed in collaboration with Lockheed and GKN-Westland Helicopters. High Li levels result in high strength, high modulus and low density, whereas higher Zr levels result in a high volume fractions of dispersoid particles which control the grain and sub-grain structures. Significant potential applications have been identified in both spacecraft and helicopters, where weight savings are of paramount importance. Two new alloys have been developed - UL30 [Al-3.0Li-1.0Cu-0.7Mg- 03U], and UL40 [Al-4.OLi-0.2Zr] the latter being the lowest density commercially available Al alloy. Properties of Spray Formed Aluminium Alloys Extruded and peak aged longitudinal properties of spray formed 8090, UL30 and UL40 are compared in Table 1. UL30 alloy is a higher strength alloy designed to achieve its high strength without the need for cold work to precipitate the S'-Al2CuMg phase, as is required for example, with 8090. Elimination of cold work is an advantage for the production of high strength forgings which can then be produced without the need for cold compression, thereby resulting in a cost saving. Table 1. Extruded peak aged longitudinal properties of spray formed 8090, UL30 and UL40. | 0.2% Proof Stress (MN.m-2) | 512 | 503 | 459 | Ultimate Tensile Strength (MN.m-2) | 550 | 515 | 528 | Elongation (%) | 5.1 | 4.9 | 4.7 | K1C (MN.m-3/2) | 46.4 | 34.6 | 20.1 | Youngs Modulus (GN.m-2) | 79.0 | 81.5 | 83.4 | Density (g.cm-3) | 2.54 | 2.51 | 2.41 | Other Aluminium Alloys Similar alloy development programmes have been carried out for high strength 7XXX and high temperature 2XXX series alloys. In 7XXX alloys, commercial DC cast alloys can contain up to 8 wt% Zn (eg 7449 and 7055). However, spray formed alloys can be produced with Zn contents up to 11-12%, and with higher than normal levels of Zr, such as Al-11.5Zn-2.5Mg-1.0Cu-0.2Zr. Forgings of these alloys have shown improved combinations of strength and toughness compared with conventional 7075 and 7050. 2XXX series alloys have also been developed with higher levels of Cu, Mn and other dispersoid forming elements such as Zr, V and Ti to obtain improved elevated properties compared with conventional high temperature alloy 2618. UL40 and a high Zn 7XXX series alloy, as well as other aerospace alloys are available from Osprey Metals. Whereas a number of new Al alloys have been developed specifically for spray forming, the different market and engineering requirements of Ni alloys for aero-engine applications have focused spray forming developments on reductions in manufacturing costs for existing alloys. However, as spray forming is established progressively in niche markets such as that being developed by STI, alloy developments will be pursued for Ni superalloys. Spray Form/HIPing Because the spray form/HIP route removes the conventional restriction that large diameter Ni superalloy casings must be in wrought alloy compositions suitable for substantial ring rolling reductions, spray formed rings that are closer in composition to casting alloys used in higher temperature applications may be possible. These alloys are now under investigation on a recently installed Osprey unit at The Oxford Centre for Advanced Materials and Composites (OCAMAC), figure 2. The objective of this research is to develop rings and casings with improved operating temperature and mechanical properties, at relatively low additional cost. 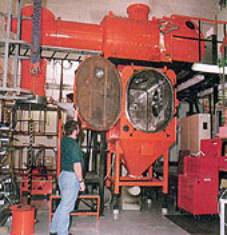 | Figure 2. The OCAMAC superalloy spray forming plant for alloy development during installation. | Economic Viability The improvement in mechanical properties conferred by the refined spray formed microstructure is now well established for a number of aerospace materials. A remaining challenge confronting spray forming technology is the realisation of the potential economic benefits in the production environment. Central to economic viability is maintaining an efficient conversion of liquid metal feedstock to spray formed product. Process yield is compromised by poorly controlled droplet trajectories (overspray), excessive droplet splashing, or bounce-off, on the preform top surface, non-reproducible sprayed shape and poor metallurgical quality such as excessive porosity. All these aspects and their manipulation are under investigation at several universities and corporate research laboratories. For example, Cospray in collaboration with OCAMAC implemented an on-line vision system for day-to-day shape control during the spray forming of Al alloys which reduced the variation in the diameter of a 300 mm diameter preform from ±10 mm to ±1 mm. Processing Conditions While shape control is now becoming standard in production systems, process conditions for good metallurgical quality are usually preset and not manipulated on-line. Some alloy compositions show a marked sensitivity to changes in spray forming conditions, whereas others are more tolerant and spray form always with a low porosity, fine scale microstructure. A quantified explanation of the relationship between optimum spray conditions and alloy composition has yet to be developed. Similarly, understanding and therefore control of porosity formation is another area that has received little attention. In contrast, recent important progress has been made in understanding some of the other critical processes occurring during spray forming. The importance of fine solid particles in the spray acting as nucleants for liquid in larger droplets has been demonstrated, and the thermal condition for the transition from a layered microstructure associated with sprayed coatings to an equiaxed structure has been quantified. The importance of droplet splashing and bounce-off in reducing process yield have also been revealed by the use of sophisticated laser and high speed imaging techniques. This last example highlights one of the barriers to generating improved basic understanding and thus control of spray forming - meaningful on-line measurements of the conditions during spray forming are often difficult because of the particularly hostile manufacturing conditions, and frequently require specialised techniques. Summary Spray forming has moved from the laboratory to the production environment for some Ni and Al aerospace alloys where both improved performance and reduced cost may be realised. This trend is likely to continue, but benefit will be best realised where cost reduction is combined with the development of alloys designed to exploit the unusual solidification conditions of spray forming. Central to the realisation of this promise is continued growth in basic understanding of the factors controlling microstructure and yield, and which is likely to be much aided by the use of numerical simulations and sophisticated diagnostic techniques. |