Acsion Industries, a company born out of the Canadian atomic energy organisation, is developing composite materials processing technologies for the next generation of high speed passenger aeroplanes, new fighter aircraft, and the replacement vehicle for the Space Shuttle. The area is rapidly advancing, since the idea took off in about 1985. The technology utilises high speed, high energy electron beams and involves electron beam curing for composites, a relatively new technique for processing components that could have a massive impact in the aerospace and defence industries and beyond. Research Collaborators Electron beam curing is being touted as a replacement for autoclave curing of composites. Acsion Industries, Oak Ridge National Laboratory's Centre for Materials Processing, Sandia National Laboratory, Lockheed Martin, Northrup Grumman and Boeing Commercial Airplane Group are among the key players pushing forward a technology that they claim could reduce costs significantly, speed up processing and offer better materials properties. The US Department of Energy is backing the work through a Co-operative Research and Development Agreement (CRADA) project. Achievements to Date This research has been bearing fruit since the mid-1990’s. A range of electron beam curable epoxy resins is now commercially available and the materials and technology have been tried out successfully in a large number of applications. Acsion recently signed an agreement with Air Canada, following lengthy in-situ trials, for the production and repair of some of the composite components in its A320 Airbus planes using electron beam processing. Lockheed is investigating the use of electron beam processing for curing whole wings and fuselage sections for its high speed civil transport aircraft and for the Venture Star, the Space Shuttle replacement vehicle, figure 1. NASA is also interested in taking the technology into space, where it could be used to cure composites for satellites and other orbiting structures such as the International Space Station. 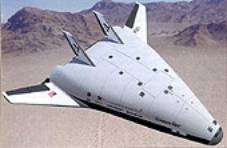 | Figure 1. The X-33 or Venture Star, proposed replacement for the space shuttle, which could use electron beam cured composite fuel tanks. | The Electron Beam Curing Mechanism Behind all of these possible applications is some relatively simple chemistry and physics. Radiation curing of polymers using cationic initiators is a common process - UV light has been used to cure a variety of materials for surface coatings for some time. Basically, the radiation creates positive ions from the initiator molecules, which then set off a polymerisation process. Free radical routes are also possible in some materials. Electron beams work by the incoming high speed electrons knocking off other electrons in the polymer-initiator mix, which is why curing is quicker and better as the beam energy is increased. The high energy of the electron beams, and also the x-rays that can be generated from these beams, means that the radiation penetrates into the composite, giving a uniform cure to materials several centimetres thick. Lower energy UV light cannot penetrate the material, making it poor for curing anything other than thin coatings. Accelerators Acsion’s pilot accelerator had a power of 1kW and produced high-energy 10MeV electrons. Such electrons can be used to process graphite composites up to 5cm thick by using two‑sided curing. Industrial accelerators are now available, rated at 50kW and producing the same energy electrons, that can process composites at a rate of 1000kg per hour in a continuous process. Thick composites with cross-sections of 16cm can be processed at 250kg per hour by converting electrons to x-rays for deeper penetration. Larger accelerators, up to 200kW, are also available, offering even faster processing. Because electron beam curing takes minutes as opposed to hours for thermal curing, the process offers a much faster throughput. Electron Beam Curing Materials New techniques such as electron beam curing are reliant on materials for their success. Key to the current increase in electron beam curing activity is the development of a range of epoxy resins that can be loaded with cationic initiator and produce composites with the required properties. Early research looked at using vinyl esters, and acrylate and methacrylate resins, but these had high shrinkage, poor thermal properties and poor mechanical properties. However, the new epoxy resins offer excellent properties that meet or exceed those of thermally cured resins. Resins Hundreds of different resin systems, including toughened formulations, are now available, some of which are tailored to customer specifications. The materials generally offer low shrinkage on curing (2-3%), a glass transition temperature of up to 400°C, very low water absorption (less than 2%) and an extended storage lifetime at ambient temperatures. They all cure in minutes to produce composites with high performance mechanical properties. Fibres The new resins can be reinforced with all existing fibres. Carbon and graphite fibres are highly stable to the treatment and, as good electrical conductors, ensure no charge buildup in thicker parts. Glass and aramid fibres are also very resistant to radiation, and other fibres such as polyethylene, can be used in the composites because there is little or no heating during curing. Advantages of Electron Beam Curing Processing Electron beam processing offers a number of other benefits over thermal curing. One of the most obvious is cost. Eight independent studies have shown potential manufacturing cost savings of 25-65%. For prototyping alone, this could rise to as much as 90-95%. This is because electron beam processing, as well as greatly speeding up curing time, cures the materials at ambient temperatures, allowing tools to be made from very low cost materials such as foam or wood. Savings are marked for complex shaped components such as engine inlets and cryogenic tanks. The stability of the resins also reduces costs because they have an almost indefinite shelf life. Another advantage of the electron beam process is its ability to combine several different resin systems in the same curing cycle. This may not be possible with thermal curing, because the different systems may need different temperatures or cure times. This is not a problem for electron beam curing because the beam of electrons is rastered across the part being cured, and the ‘dose’ given to each area of the component can be pre-programmed. Thus, different resins are easily processed on the same line, which enables the development of new products with tailor-made crosslinking profiles to give the necessary properties in particular areas of a component. Materials Properties Electron beam cured composites often have improved mechanical properties compared to thermally cured materials, and these are retained (and sometimes improved) following thermal or cryogenic cycling. In fact, one of the key advantages of electron beam curing is that it can reduce residual internal stresses in the microstructure of composite parts. The stresses are induced during cooling and can develop within layers, owing to the low linear expansion of the fibres compared to the resin, or between layers. Such stresses can limit composite part design. However, electron beam curing reduces such stresses because processing temperature can be ambient or even lower. This is very beneficial for producing cryogenic tanks, which must hold fluids at temperatures of -200 to -255°C. Conventional thermal curing is carried out at 150 to 200°C, and this large difference can causes large stresses, which are eliminated using the electron beam technique. Environmental and Health The electron beam technique also offers environmental and health benefits. The amount of volatiles produced using this technology are reduced significantly, with the resins typically producing 0.1% or less volatiles. Stack emissions of volatile chemicals from electron beam curing can be as low as 1% of the emissions from thermally cured resins. In addition, chemical crosslinking agents for thermosetting resins, which can be toxic and carcinogenic, can be eliminated. Research Programmes Air Canada The signs are that electron beam curing is beginning to emerge as a commercial process. On March 15, 1999, Acsion and Air Canada signed a technology transfer agreement to jointly develop the electron beam curing process for repairing and manufacturing certain components. This came about following successful trials on a wing-to-body fairing of an A320 passenger aircraft, figure 2. This part was chosen Current repair techniques are very time consuming and the curing properties are not optimal, with associated high maintenance costs. It is estimated that every 8 hours of downtime for a plane costs half a million dollars. 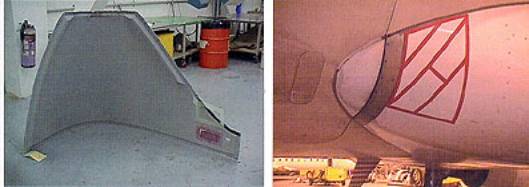 | Figure 2. The repaired panel (left) and re-installed for service (right) | Composite components make up 20-25% of the structural weight of an A320 aircraft, and so it is vital to use a rapid repair technique for any components that get damaged by lightning strikes, bird strikes, foreign objects etc. Acsion and Air Canada decided to try electron beam curing at Air Canada’s Maintenance Base in Winnipeg, beginning with the A320 fairing. The component was chosen because its function and location expose it to damage from baggage handling equipment and objects being thrown up by the aircraft's wheels - any repair would have to withstand a lot of abuse. A damaged panel on one of Air Canada’s planes was repaired by electron beam curing fresh material, and the panel was then monitored for 1800 hours of flying and 900 take-offs and landings. The test parts survived the test regiment and also had higher lap-shear strength, better hot-wet properties and higher crosslink density than using the standard repair process, and so was better able to withstand the rigours of flight. Air Canada will now routinely use electron beam curing for the wing-to-body fairings, a first for any aircraft, military or civilian. Meanwhile, two other panels have been repaired and monitored with similar results. Eventually electron beam curing could be used to repair all the composite components on the aircraft, minimising downtime and so saving money. It is possible that repairs could be carried out on the runway by a remotely controlled curing system, with new materials being rapidly laid up to repair the damage and the panel could be cured within minutes, ready for take-off again. US Air Force Military aircraft and other civilian aircraft are also benefiting from electron beam curing. The composite windshield frame for the T-38 jet trainer aircraft has been tackled by Oak Ridge Centre for Manufacturing Technology and the US Air Force. Steel-reinforced sections were x-ray cured and all-composite sections were electron cured in a simpler, cheaper manufacturing process than previously used. Lockheed Martin is assessing the technique, too, for the joint Strike Fighter aircraft. Advanced Short Take-Off Vertical Landing (ASTOVL) Craft Acsion are working with Lockheed Martin on a DARPA project called `Integrated airframe technologies for affordability’, looking at producing the ASTOVL - advanced short take-off vertical landing craft, figure 3. The plane would be 95% composites and be constructed from far fewer parts than normal - perhaps as few as 500 compared to 2500. Electron beam curing could play a major role in its construction. The proposed plane would have a one-piece 40 foot bulkhead, a one-piece top fuselage and a one-piece bottom fuselage. Such enormous parts could not be cured in an autoclave but would not present a problem for electron beam processing. 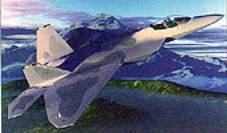 | Figure 3. The proposed F-22 ASTOVL aircraft, which could potentially be made from 95% composites. | NASA Acsion is also talking of producing big components with NASA’s Lewis Lab. In this case, the whole wing structure of the high speed civil transport aircraft. Potential savings per wing over conventional technologies are enormous. It is estimated that there would be a $6 million saving over autoclave for setup, plus an additional $2 million energy savings and $0.5 million savings on tooling. Theoretically, using electron beam processing could save more than $8 million per wing. These cost savings are also attracting space applications. Acsion and Lockheed Martin Skunk Works are working on the production of liquid hydrogen and oxygen tanks for the X-33 or Venture Star, the replacement for the Space Shuttle. These tanks would need to be 30m by 16m, and there is no autoclave big enough to process these parts. Electron beam curing would reduce the internal stress in the composite tanks, give lower microcracking, and offer much better hydrogen permeability than required. The total cost using electron beam curing would be about $65 million, compared to $100 million or more for conventional techniques. CASA Acsion has also produced a satellite reflector dish by electron beam curing for CASA, the Spanish space agency. The dish needed dimensional stability at an operating temperature of 100°C, which was easily achieved in an electron beam curing process that took less than 6 hours. Summary The future is bright for electron beam processing of composites. Apart from the projects described above there are many more potential and planned research programmes looking into resin development, adhesive development (to replace bolts and rivets) and interface chemistry, to improve the interlaminar shear properties of electron beam curable composites. There are also other programmes looking into composites repair applications for both military and civilian aircraft. Acsion itself is looking to expand as the number of applications for the technique grow, and may build a manufacturing and repair facility in the UK, possibly. At the moment, he thinks that the UK is at least five years behind North America in electron beam processing, but if current progress continues, then electron beam processing know-how could spread worldwide and become one of the key composite materials technologies. |