Mar 11 2013
Stainless Steel Fasteners Ltd (SSF), a leading UK manufacturer of high-integrity specialist fasteners, is the first fastener manufacturing company to be awarded NORSOK M-650 accreditation by Statoil ASA.
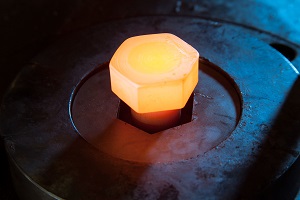
SSF has been qualified for the hot forging of its range of super duplex stainless steel fasteners. The Chesterfield- based company attributes the accreditation to a 30% increase in turnover over the last six months as oil and gas operating companies increasingly recognise that hot forged fasteners manufactured from super duplex to NORSOK standard can contribute significantly to the life and integrity of tools and assemblies.
The standard verifies SSF’s skill in developing a process that eliminates the risk of the problems associated with the hot forging of this high-grade material.
Heat treatment problems with duplex and super duplex, which are commonly used in process and seawater piping applications, have been rising over the last 25 years as the materials have become increasingly used in the offshore industry. The use of defective materials can cause potentially catastrophic failure; an issue which has been acknowledged by the HSE and many operators have written their own documents to control procurement of these stainless steels.
SSF has four specific procedures for hot forging, loading, heat treatment and testing which ensure product consistency and uniformity. NORSOK M-650 qualifies the company’s processes to ensure that all SSF die forged fasteners will perform to specification in the demanding offshore environment.
Statoil is recognised as an expert in super duplex material and the award gives SSF a coveted place on the Norwegian operator’s approved vendor list.
NORSOK M-650 is one of the oil and gas industry’s most demanding quality standards for suppliers of special materials.
Matthew Tongue, Operations Manager at SSF Ltd said: “We devoted two years to developing our processes to meet the demands of NORSOK and it is an outstanding achievement for a company of our size to achieve this accreditation.
“Our hot forging process for super duplex steel has overcome a major industry issue and enables us to supply fastening products that are guaranteed to perform to specification in critical applications.
“We have seen an increasing focus from operators and equipment manufacturers on the component industry in the last year. If low-quality components fail, then the likelihood is that the assembly or tool associated with it will also fail causing expensive downtime and replacement costs. It is vital that end users understand how components are produced and require evidence of quality throughout the whole supply chain,” he concluded.
Alan Harrison, Technical Advisor at British Stainless Steel Association underlined the achievement: “Approval of materials to the NORSOK standard is sought after by manufacturers of steel products in the oil and gas sector. It shows that the manufacturer has gone the extra mile in producing a consistently high quality product. Meeting these requirements is demanding and the manufacturer who achieves the NORSOK standard is therefore ensuring the optimum performance of the products in a very aggressive environment.”