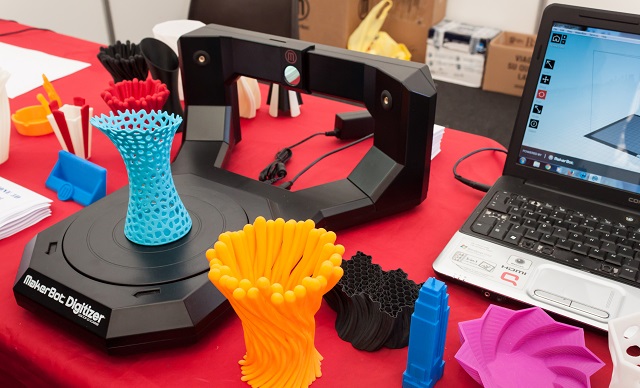
MakerBot® 3D Scanner on display at Robot and Makers show, Milan 2014.
Image credit: Stefano Tinti / Shutterstock.com
Using a MakerBot® Replicator® 2X Experimental 3D Printer, a research team from The Feinstein Institute for Medical Research has produced cartilage for tracheal repair or replacement.
This medical breakthrough has been showcased at the 51st Annual Meeting of The Society of Thoracic Surgeons, San Diego, in a presentation by one of the researchers, Todd Goldstein, a PhD candidate.
Daniel A. Grande and Todd Goldstein part of the North Shore-LIJ Health System, with MakerBot Replicator Desktop 3D Printer that was used to 3D print cartilage to repair tracheal damage. Image credit: Business Wire
Mr. Goldstein has been working with surgeons at the North Shore-LIJ Health System for about a year to analyze whether 3D printing and tissue engineering could be applied for tracheal repair and replacement.
Their achievement is remarkable in medical research as this is the first time standard MakerBot® PLA filament has been used to 3D-print a custom tracheal scaffolding, which was united with living cells to produce a tracheal segment.
Damage to the trachea occurs due to endotracheal intubation, blunt trauma, tumor, and other injuries. These can cause narrowing and weakening of the trachea, which becomes quite difficult to repair. The two conventional methods to reconstruct a damaged trachea have specific limitations.
David Zeltsman, MD, chief of thoracic surgery at Long Island Jewish Medical Center and Lee Smith, MD, chief of pediatric otolaryngology at Cohen Children's Medical Center (both from the North Shore-LIJ Health System), took the idea of using 3D printing and tissue engineering to create new cartilage for airway construction to Daniel A. Grande, PhD, director of the Orthopedic Research Laboratory at the Feinstein Institute, and Mr. Goldstein.
Zeltsman and Smith felt that using this technique for creating new cartilage may take at least 10 to 20 years. Dr. Grande and Mr. Goldstein were able to accomplish the task in a month.
The Feinstein Institute’s research team successfully integrated two emerging fields of 3D printing and tissue engineering. Tissue engineering uses living cells from skin, cartilage, or muscle as raw material instead of steel or computer code, which are used in other engineering fields. The researchers knew how to grow cartilage using a blend of cells known as chondrocytes, nutrients to nourish them, and collagen to bind all of it together.
MakerBot Stories: Feinstein Institute for Medical Research from MakerBot on Vimeo.
The role of 3D printing is essential in shaping the newly formed cartilage into a windpipe or a nose. Using a 3D printer, the researchers constructed a scaffolding, which could then be enclosed in a blend of chondrocytes and collagen.
Making a windpipe or trachea is uncharted territory. It has to be rigid enough to withstand coughs, sneezes and other shifts in pressure, yet flexible enough to allow the neck to move freely.
With 3D printing, we were able to construct 3D-printed scaffolding that the surgeons could immediately examine and then we could work together in real time to modify the designs. MakerBot was extremely helpful and consulted on optimizing our design files so they would print better and provided advice on how to modify the MakerBot Replicator 2X Experimental 3D Printer to print with PLA and the biomaterial.
We actually found designs to modify the printer on MakerBot’s Thingiverse website to print PLA with one extruder and the biomaterial with the other extruder.
We 3D printed the needed parts with our other MakerBot Replicator Desktop 3D Printer, and used them to modify the MakerBot Replicator 2X Experimental 3D Printer so that we could better iterate and test our ideas.
Todd Goldstein - PhD Candidate
The Feinstein Institute for Medical Research
The Feinstein Institute tried a few 3D printers, but the cost-effective choice was the MakerBot Replicator 2X Experimental 3D Printer, which could be placed on a desktop.
The team chose to use a standard MakerBot PLA Filament for their experiment. While testing, Mr. Goldstein discovered that the heat from the extruder head helped to sterilize the standard PLA as it printed. However, the bio-ink continues to remain at room temperature, and is extruded during the 3D printing procedure. It then fills all the ridges in the PLA scaffolding, and cures into a gel on the heated build plate of the MakerBot Replicator 2X. This technique enables printing a two-inch-long section of windpipe within two hours.
The ability to prototype, examine, touch, feel and then redesign within minutes, within hours, allows for the creation of this type of technology. If we had to send out these designs to a commercial printer far away and get the designs back several weeks later, we'd never be where we are today.
The advantage of PLA is that it’s used in all kinds of surgical implant devices.
Lee Smith - MD, Chief of Pediatric Otolaryngology
Cohen Children's Medical Center
After the bio-ink binds onto the scaffolding, it is sent to a bioreactor. The bioreactor, resembles a rotisserie oven, helps to keep the cells in warm and to grow in a uniform manner. To save costs, instead of a new bioreactor, which would cost about $50,000 to $150,000, Mr. Goldstein modified an incubator based on his specific requirement and built gears and other components on the MakerBot Replicator Desktop 3D Printer, thus accomplishing building a completely new bioreactor for the team to use.
The 3D printed windpipe or trachea segments could be maintained for four weeks in the customized incubator. According to Mr. Goldstein’s abstract, “The cells survived the 3D printing process, were able to continue dividing, and produced the extracellular matrix expected of tracheal chondrocytes.” In other words, the segments began growing just like windpipe cartilage.
The research being done at the Feinstein Institute is exciting and promising. We are continually amazed by what is being created with 3D Printers. To know that a MakerBot Replicator 3D Printer played a role in a potential medical breakthrough is inspiring.
Jenny Lawton - CEO
MakerBot®
On the success of their experiment, the Feinstein Institute described this work as a “proof of concept.” However, the team has more work to be do and only then can they set up a new protocol for repairing damaged windpipes. Medical research tends to take years to move from the lab to the practical applications. There can also be delays with the US Food and Drug Administration (FDA) approval. However, the FDA does have an exception termed compassionate therapy that allows a patient to consent to seeking an experimental procedure.
According to Dr. Smith, at least one patient comes through the North Shore-LIJ Health System each year who can’t be helped by the two traditional methods. He expects in the next five years to harvest a patient’s cells, grow them on a scaffold, and repair a windpipe. This customized approach may prove to be especially useful for treating children, says Dr. Smith.
When speaking about his work with 3D printing and this research, Mr. Goldstein notes, “It's completely changed the trajectory of my academic career.” Mr. Goldstein originally came to the Feinstein Institute as a molecular biologist, working with cells, chemicals and drugs.
Today, Mr. Goldstein is a 3D printing specialist at the Feinstein Institute, and is involved in printing replicas of organs for pre-operative planning and instruments to improve the lab. “Knowing that I can make a part that will save someone's child — that's life-changing,” said Mr. Goldstein.
MakerBot has supplied the Feinstein Institute with early samples of their MakerBot PLA Composite Filaments in Limestone (calcium carbonate) and Iron, which is yet to hit the market, so that the research Institute can continue their work to experiment with other kinds of tissue such as bone or 3D print personalized shields for cancer and radiation treatment.
Do you remember the Six Million Dollar Man? The Bionic Man is not the future, it’s the present. We have that ability to do that now. It’s really exciting!
Dr. Daniel A. Grande - Director of the Orthopedic Research Laboratory
The Feinstein Institute for Medical Research