Ferris wheels, cranes, excavators, tunnel boring machines, wind turbines and many other large machines have one thing in common: without large diameter bearings, they would not be able to turn. But the path to the large diameter bearing is a long one – both in the history of the technology and in manufacturing time. Manual work is still required at a decisive stage in the production process. A small assembly aid helps make this more ergonomic and simple.
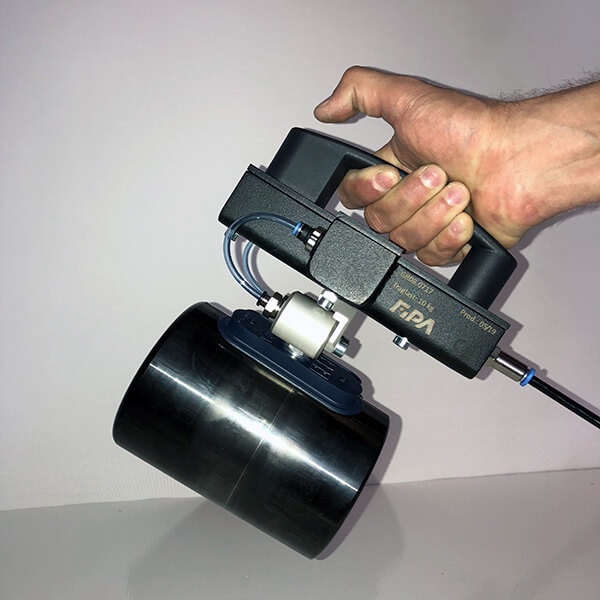
The plain bearing is one of the oldest types of slewing rings. Thanks to its simple structure, it was invented thousands of years ago. Ancient civilizations, such as the Egyptian, used it for irrigation systems and chariots.
A plain bearing fixes an axis or a shaft and allows the sliding surfaces to move against each other. A lubricating film generally separates the bearing and axle surfaces. Due to the frictional heat generated, Egyptian chariots would have quickly burst into flames at high speeds without lubricant.
Plain bearings nevertheless have some disadvantages. Wear is high at low speeds and a large friction torque must be overcome when starting up. The Celts already knew that 2,700 years ago. Remnants of a simple rolling bearing have been found in an excavated chariot. This knowledge was lost at some point. Modern rolling bearings were not designed and manufactured until the 19th century.
In everyday life, rolling bearings are found in bicycles and cars, in hand drills, electric screwdrivers, and sewing machines. They facilitate the low-friction movement of structural elements thanks to the rolling motion of the rolling elements, which can be designed as ball-, cylindrical-, needle-, tapered-, drum- and self-aligning rollers. The different types tend to be named for the shape of the rolling element. Of these, the ball bearing is the best-known.
A rolling bearing is more complicated than a plain bearing and consists of rolling elements, inner ring, an outer ring that contains the raceway of the rolling elements, a cage and seals.
The cage holds all the rolling elements in pockets and ensures that they are evenly spaced. For simple ball bearings, the cage is often dispensed with in order to save money. Seals prevent lubricants from escaping and protect the bearing against contamination.
Large diameter bearings – the Hercules among slewing rings
In ancient Greek mythology, Hercules carries the earth on his shoulders. Although large diameter bearings are naturally not designed for such crushing loads they can nevertheless withstand great forces in huge plants and large machines – day after day and often around the clock.
What is the difference between a rolling bearing and a large diameter bearing?
It is only their size – and they can be huge. Bearings manufactured in one piece can reach almost ten meters in diameter. Larger bearings are divided into several segments. Using this segmented design, diameters of over 20 meters are feasible.
A universal large diameter bearing does not exist. Every design has its strengths and weaknesses. There are particularly large differences in terms of radial and axial load capacity.
In building construction and civil engineering, large diameter bearings are mainly found in crawler cranes and road transport- and drilling equipment. Weight is a critical factor for mobile cranes. The competent authority will not issue road approval if the crane is too heavy. Special roller bearings enable very high load capacity in a small space and so offer a perfect weight/performance ratio.
Maritime applications of large diameter bearings require special corrosion protection against seawater. Specifications also include ozone and UV-resistant seals and, in particularly critical applications, even emergency seals.
Mining equipment such as excavators move high loads. Economical operation demands durable large diameter bearings with long maintenance intervals.
In wind turbines, large diameter bearings are used for rotor blade and azimuth adjustment. Special ships, known as floating production storage and offloading units (FPSO), are built for the production, storage, cleaning and loading of crude oil or natural gas. They are anchored to the seabed and kept in place using rotatable anchors. Segmented large diameter bearings in the anchors let the FPSOs rotate freely around the gas and oil production lines.
Source: http://www.fipa.com/us/