Shape-morphing materials that can form three-dimensional shapes from flat sheets provide exciting opportunities for the future of materials science. Digitally printing these materials offers a new way to construct them, leading to solutions to current issues with the technology, making possible the development of next-generation intelligent green shape-morphing products.
Image Credit: Golden Wind/Shutterstock.com
The Issues with Shape-Morphing Materials
The issues with shape-morphing materials are twofold: manufacturing processes largely rely on non-sustainable fossil fuels and finely extracted biomaterials that are difficult to process.
Manufacturing shape-morphic materials, particularly nanomaterials and micromaterials, with fossil fuels presents obvious problems. It contributes to carbon emissions and climate change, resource scarcity, and health risks. To pursue sustainability and make possible green chemistry, natural biomaterials derived from raw biomass are being explored.
Commonly used biomaterials require complex equipment, prefabricated templates, and strict reaction control. Techniques to manipulate their characteristics to improve their shape-changing abilities can be employed. Silk, cellulose, and agarose can be manipulated with controlled humidity changes. Photolithography and external electric fields can help realize complex dynamic deformation.
Currently, these issues are proving difficult to solve. Circumventing them will provide a pathway to sustainable, scalable technological development.
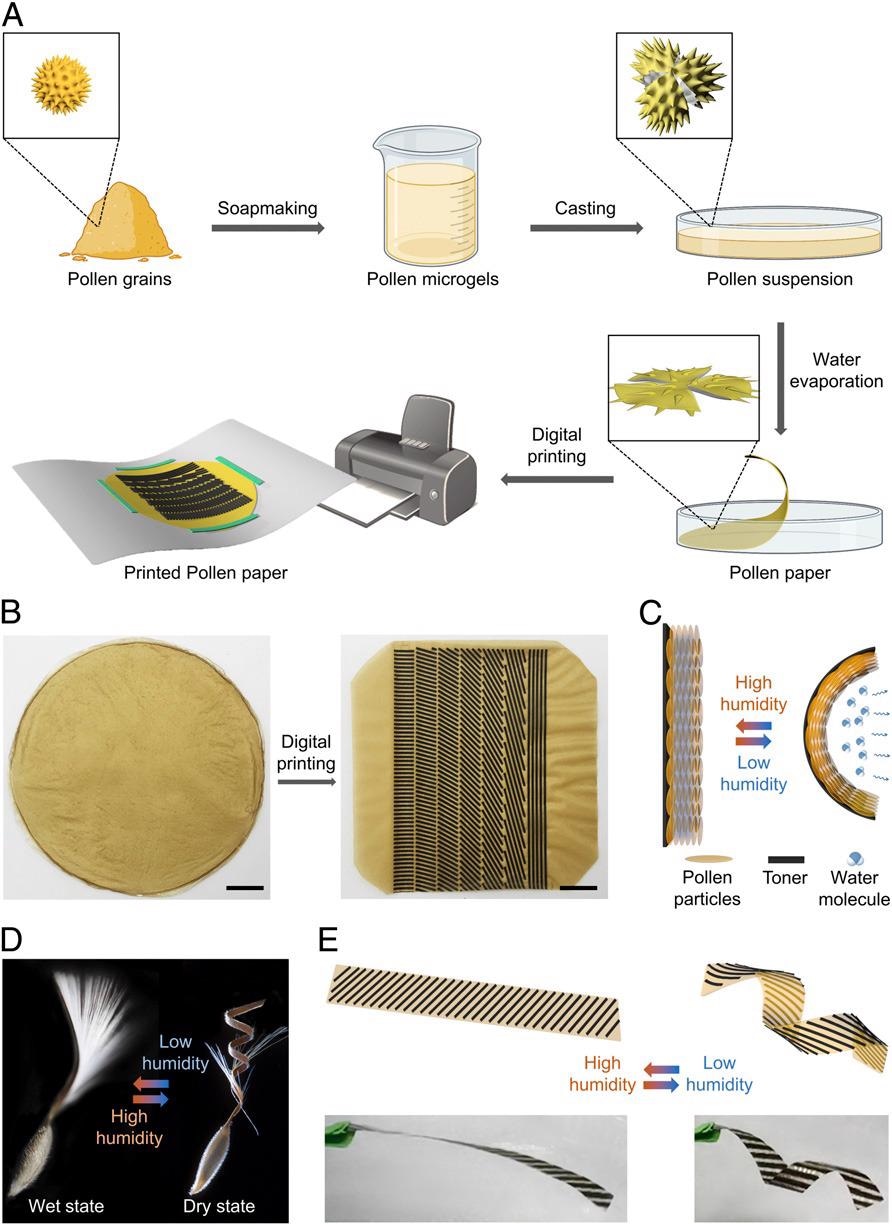
Biomimetic autonomous shape-morphing deformation of humidity-responsive pollen paper. (A) Schematic illustration of toner-patterned pollen paper fabrication through pollen microgels suspension casting and direct digital printing. (B) A customized pollen bilayer was fabricated by direct digital printing with patterns using toner. (Scale bar, 1 cm.) (C) Schematic illustration of the strain mismatch created by water adsorption and desorption in the bilayer comprising the hydrophilic pollen paper and the hydrophobic ink pattern of styrene acrylate copolymer (introduced through the laser toner). (D) The awn of an individual seed exhibiting straight and coiling morphology, depending on changes in humidity. Image credit: Shutterstock / Emily Eriksson and Coulanges. (E) A ribbon-shaped pollen paper (3 cm × 0.5 cm) printed with a specific toner stripe pattern self-coiled in response to humidity stimulation. Top represents schematic illustration, and Bottom shows corresponding photographs from experiments.
Creating Shape Changing Materials from Pollen Biomass
Shape-morphing materials have already been explored for applications in numerous fields. These include sensors, wearable devices, clean energy harvesting, soft robots, and biomedical devices. They can react to external stimuli such as heat, humidity, chemicals, light, and electricity. The technology has the potential to create truly smart materials.
A paper published on PNAS in October 2021 demonstrated a method to digitally print scalable, green shape-morphing materials from non-allergenic pollen biomass paper. Pollen biomass is easy to process, making it attractive for use as a substrate material. The technique for turning pollen biomass into a soft microgel is similar to soapmaking and creates a non-allergenic material that is capable of autonomous actuation to changes in humidity.
By using this new approach, complex materials with user-defined shape-morphing abilities were constructed from well-defined geometrical shapes and architectures. To complement the fabrication techniques, computational simulations were used to provide mechanistic and quantitative insights into the biomaterial’s characteristics. The method uses digital printing techniques which are widely available.
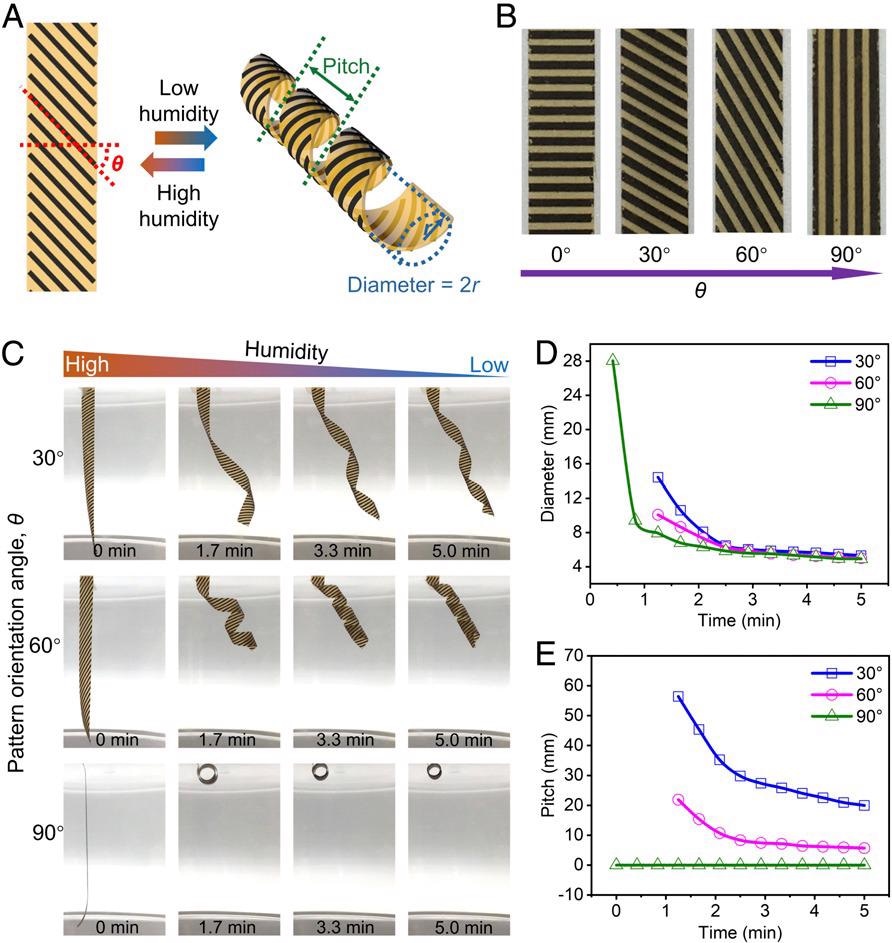
Bioinspired self-coiling morphology induced by the change in RH. (A) Schematic illustration of bioinspired coiling geometry and nomenclature of the patterned bilayer ribbon. (B) Images of bilayer ribbons with different toner pattern orientation angles, θ. (C) Programed self-coiling processes of the patterned bilayer ribbons with three different values of θ in response to RH changes from ∼70% to ∼20%. (D and E) Evolution of coiling diameter (D) and pitch (E) as a function of time for three different values of the pattern orientation angle (θ).
Methods and Materials
The innovative material created in the study involved printing an inactive layer onto the active pollen layer. Fabrication of the two-dimensional pollen layer was achieved with a two-step process: traditional soapmaking and subsequent pollen casting.
The inactive layer is comprised of styrene acrylate copolymer. Styrene acrylate copolymer is found in commercially available products such as edible ink and standard laser toner. The copolymer layer binds to the pollen layer, creating a tight and strong mechanical interface. The interlayer adhesion is facilitated and promoted by the pollen paper’s surface microroughness. The inactive copolymer layer is digitally printed into user-defined, custom-made patterns on the pollen layer.
To avoid any further changes in shape during service, postprocessing coatings are applied to effectively freeze the bilayer’s humidity-sensitive hygromorphic behavior. High-volume, commercial applications where humidity is an environmental factor can be designed thanks to this step. On-demand folding and tilting mechanisms can be produced that do not require extra elements like specially designed fasteners and hinges.
Additional flexibility in tuning the degree of shape change is provided by toner coverage rate and relative humidity levels. Biomimetic inspiration drawn from Pelargonium’s hygrophobic coiling behavior was used to design and print various stripe patterns constructed from the inactive copolymer layer and precisely control the coiling morphology of the bilayer. The orientation of stripe patterns can be adjusted to control the bilayer’s coiling morphology.
The finite elemental analysis was used to perform detailed simulations which modeled and predicted the bilayer’s geometric deformation when exposed to changes in humidity. Mechanistic insights and quantitative details that could not be obtained from experiments alone were thus made possible. Scanning electron microscopy was used to characterize the microstructure of the bilayer.
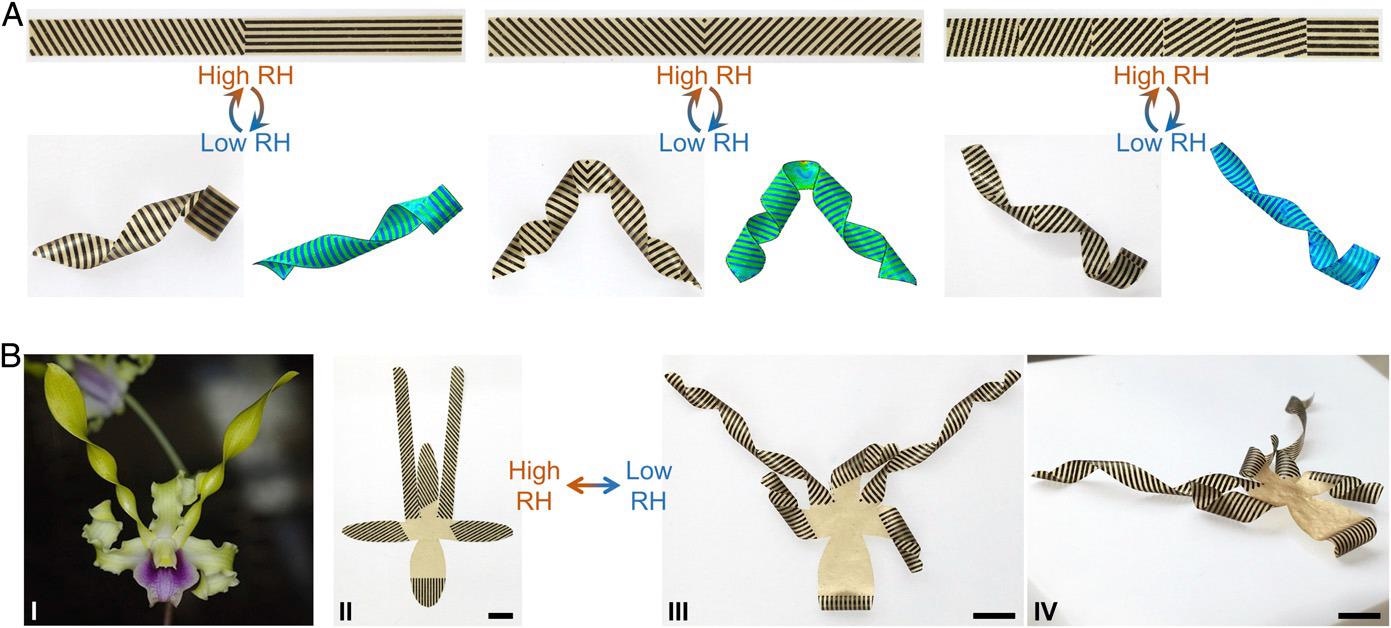
Complex hygromorphic deformation enabled through digital design of patterned bilayer units. (A) The 3D configurations of the bilayer ribbons with multiple coiling modes. For each of the three shapes of interest (Left, Middle, and Right), the experimental and simulation (in teal color) results are shown on the Bottom Left and Bottom Right, respectively. (B) A bilayer-based biomimetic orchid Dendrobium helix in response to low RH level. (I) An image of the Dendrobium helix found in nature (image from ref. 56). Image credit: Paul Zorn (photographer); (II) initial hydrated flat state; and (III and IV) top view and side view of the dehydrated “blooming” state, respectively. (Scale bars, 1 cm.)
The Future: Eco-Friendly, Scalable Digital Printing of Materials
Using this simple and efficient method, a moisture-sensitive biomaterial-based system is created that can reversibly morph into complex shapes and architectures which can be digitally customized and digitally printed. Thus, a dynamic, robust, and reliable system of creating not just programmable, but reversible shape-morphing materials can be developed.
This research has exciting implications for the future of materials science. It paves the way for intelligent green products that will provide innovative applications in biomedical sciences and electronics with functional characteristics. The implications for multiple scientific disciplines that will take advantage in the future of shape-changing materials are vast and exciting.
Further Reading:
Zhao, Z et al. (2021) Digital Printing of shape-morphing natural materials (online) PNAS 117(43) e2113715118 | PNAS.org. Available at: https://www.pnas.org/content/118/43/e2113715118
Disclaimer: The views expressed here are those of the author expressed in their private capacity and do not necessarily represent the views of AZoM.com Limited T/A AZoNetwork the owner and operator of this website. This disclaimer forms part of the Terms and conditions of use of this website.