New research in the journal Materials has investigated the impact of determining remelting processing parameters through mathematical simulations and experiments analyses in order to maximize a process industries chain for DMD part repair.
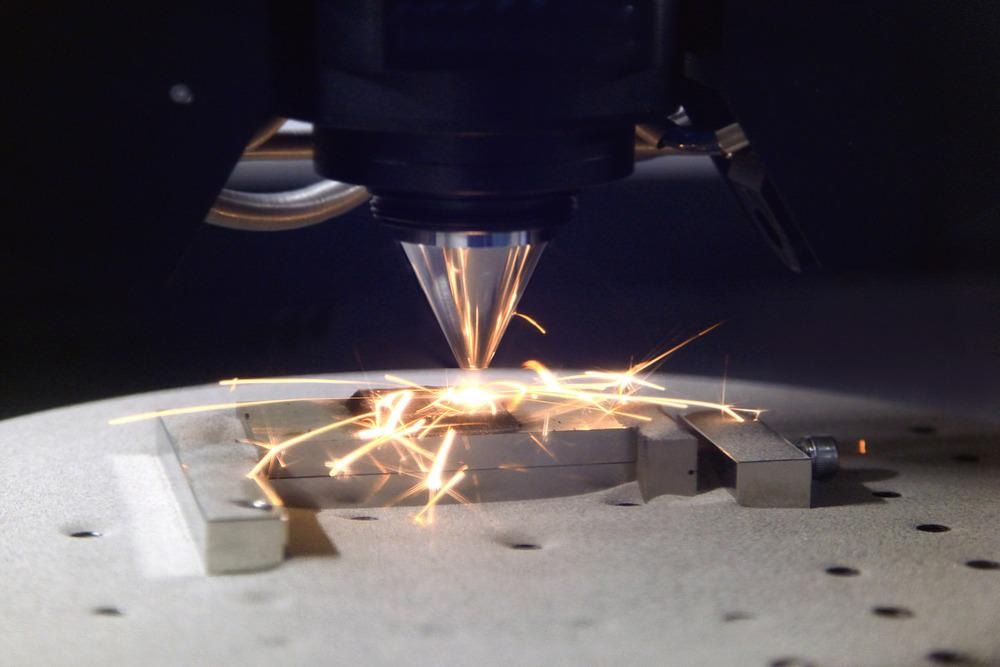
Study: Laser Remelting Process Simulation and Optimization for Additive Manufacturing of Nickel-Based Super Alloys. Image Credit: sspopov/Shutterstock.com
Because of their outstanding corrosion and high-temperature resistance, nickel-based super alloys are famous for their implementations in the energy and aviation industries. Direct metal deposition (DMD) of nickel alloys has achieved new tech readiness for a variety of applications, particularly turbomachinery element repair.
However, issues with part quality and defect creation during the DMD process continue to exist. Despite the fact that laser remelting can actually prevent and fix defects during metal additive manufacturing (AM), few researchers have concentrated on numerical modeling and innovative process parameterization in this context.
Mesh geometry and heat source location. Image Credit: Soffel, F., et al., Materials
Advantage of Metal Additive Manufacturing
Metal additive manufacturing (AM) as a new technology of nickel-based super alloys has received a lot of attention in the last few years, primarily because of useful applications in energy and aviation applications.
While powder bed fusion (PBF) processes have several advantages for relatively small and more complex-shaped part geometries, the manufacturing or repair of larger parts may necessitate the larger equipment size and ease of access of directed energy deposition methods. Direct metal deposition (DMD) is a welding track-creating process where a laser generates a melt pool within which metallic granules are continuously blown.
Challenge in Direct Metal Deposition (DMD)
A common application of DMD is the restoration of turbomachinery elements. Defect configuration is a challenge in DMD, particularly in the transition region between the substrate and the AM material. Laser remelting procedures were shown to reduce bond formation defects and cracks substantially. As a result, it is critical to incorporate laser remelting steps into part fabrication and repair.
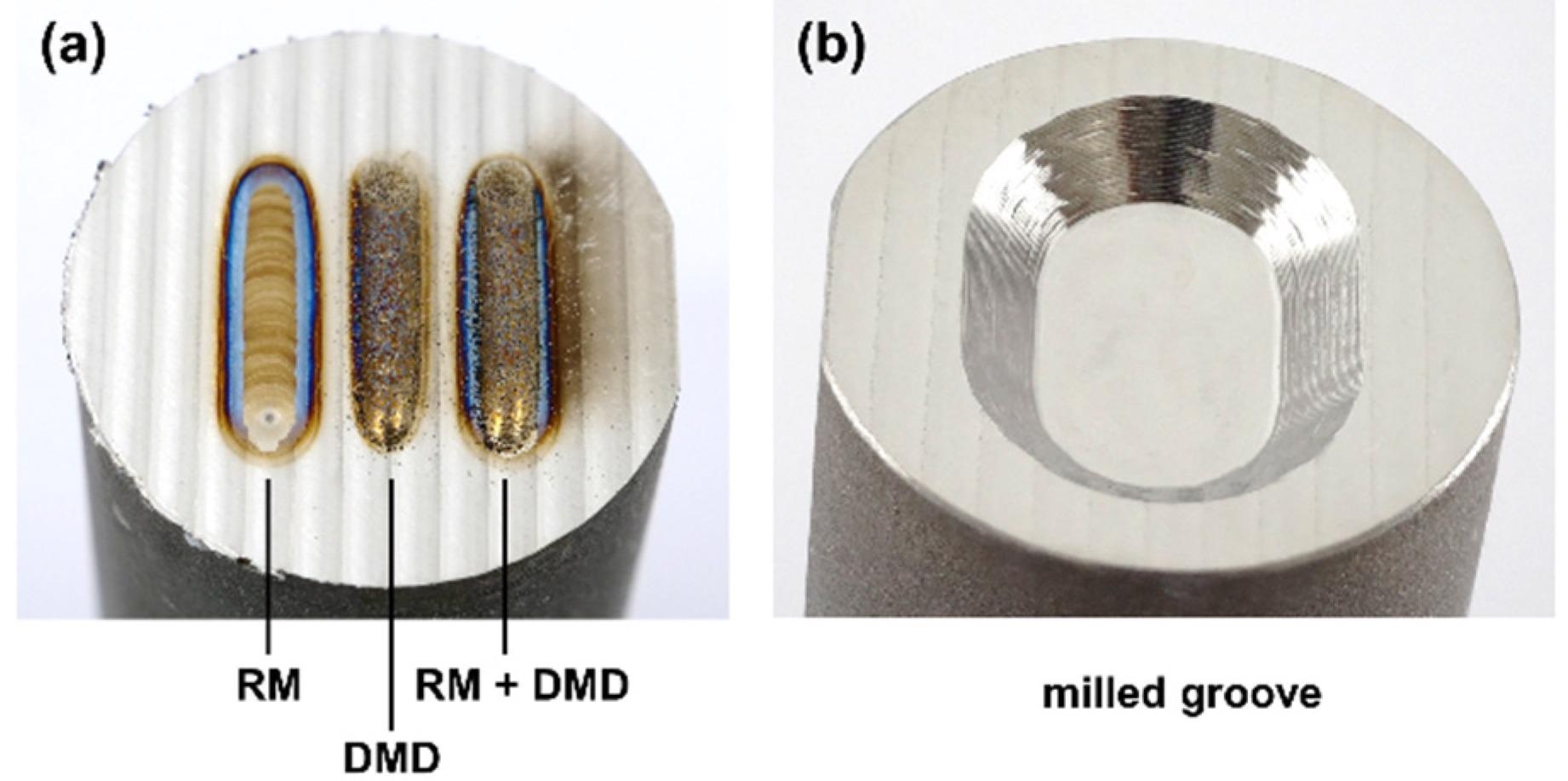
(a) Single tracks deposited in face-milled substrates and (b) groove geometry after machining. Image Credit: Soffel, F., et al., Materials
Laser Remelting as A Enhancement Process
Laser remelting is indeed a laser welding process used to melt and resolidify local materials. Laser remelting can be used to enhance part quality in surface roughness, saturation magnetization, and mechanical properties in metal AM. PBF structures were tested; laser remelting decreased surface roughness by fusing initially unmelted or partially melted granules with the deposit.
Laser remelting was implemented to an iron–cobalt-based alloy deposited by PBF, and it was discovered that grain refinement enhanced saturation magnetization and microhardness. suggested a process chain that included defect milling, sandblasting, laser remelting, and DMD.
The laser remelting process was used to decrease liquation cracking in the foundation material's heat-affected area. Laser spot size, laser power, and scan rate are the three most important parameters in laser remelting procedures. It is anticipated that computer modeling will aid in the selection of appropriate laser remelting process parameters.
Research Process
The study creates a mathematical laser remelting prototype and then uses the modeling results to optimize a laser remelting step in a chemical processing chain. At such a low computational complexity, a heat conduction methodology was built to analyze the influence of processing parameters on melt pool geometrical.
A second model that recognizes the flow pattern in the melt pool was adjusted, and both types of algorithms were compared with experimental record keeping. Whereas the fluid flow model had higher physical precision and required longer computing times, the heat conduction prototype could be quickly resolved and with minor deviations.
In comparison to the experimental findings, for cast Inconel 718 substances an optimum processing chain involving groove milling, laser remelting, and DMD was assessed. When compared to a combined method without transitional surface remelting, the laser remelting step resulted in a more unified bond formation of the DMD deposit to the cast base material.
Result of Advanced Remelting Mathematical Model
The two numerical concepts for laser remelting modeling, singletrack studies, as well as part scale experimental studies, were carried out to validate the model, demonstrating the potential application of the advanced remelting process for metal additive manufacturing. The findings verify that the proposed method improves the quality of metal AM components. The simplified heat conduction model can be used to calculate the impacts of the main laser remelting process parameter.
Experimental studies on a single remelting track with varying monitoring speeds verify the high physical precision from both the heat conduction and fluid flow models. The heat conduction model mildly overestimated the remelting depth and undervalued the width, while the fluid flow model had the highest geometrical precision.
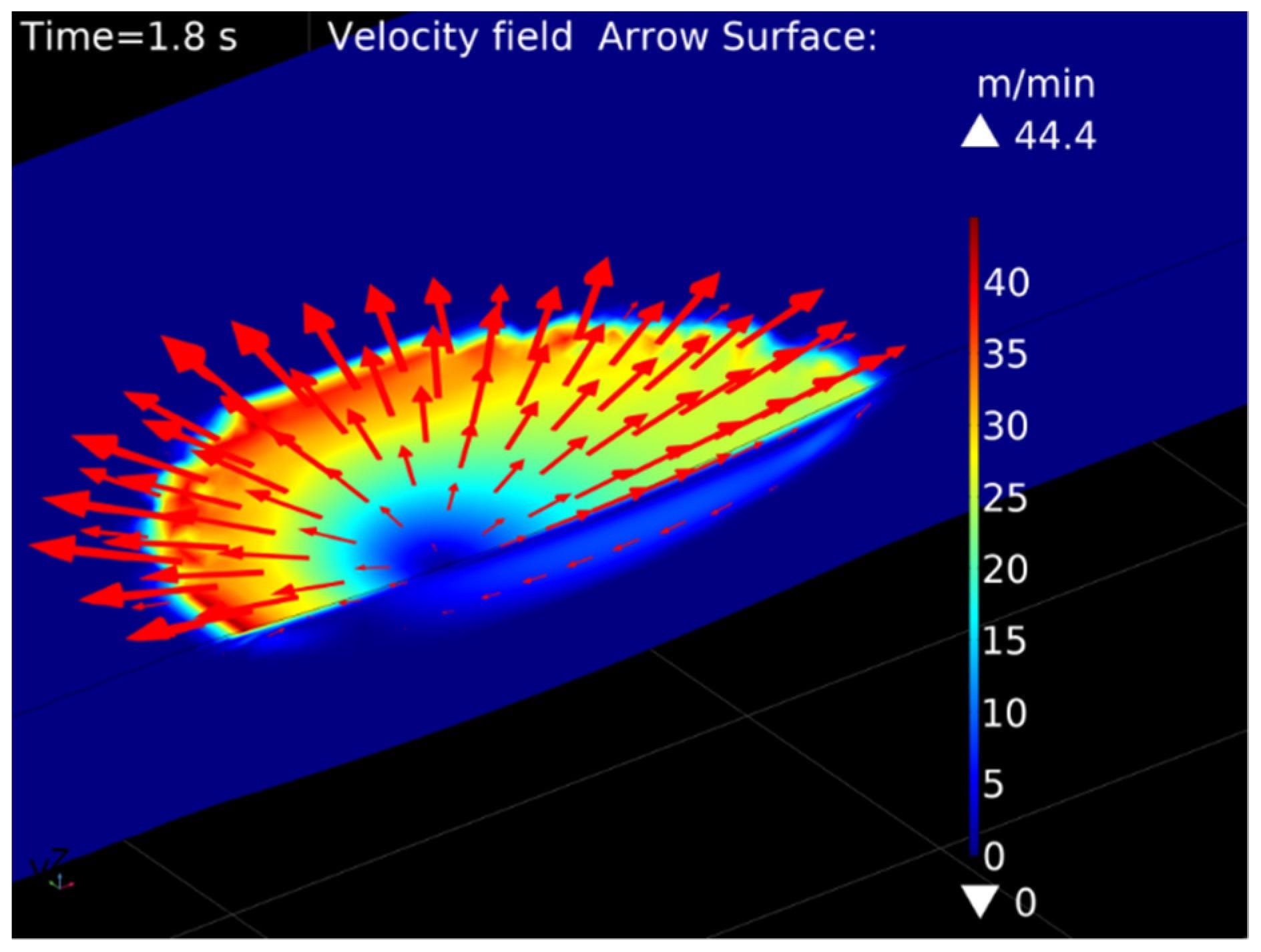
Velocity field of melt pool motion, computed by the fluid flow model for P = 1000 W, v = 400 mm/min, T = 20 °C. Image Credit: Soffel, F., et al., Materials
Research Limitation
The primary limitations of this research are connected to the numerical accuracy of the liquid flow model. Whereas the heat conduction model can be resolved immediately for a large number of processing conditions, it mildly overestimated the remelting depth and underestimated the width. The fluid flow model, on the other hand, could anticipate the melt pool shape of one reference condition very precisely; however, the powerful computational time and limited prototype robustness prevented it from being used for comprehensive parameter studies.
Reference
Soffel, F., et al. (2021). Laser Remelting Process Simulation and Optimization for Additive Manufacturing of Nickel-Based Super Alloys. Materials 2022, 15(1), 177; Published: 27 December 2021. https://www.mdpi.com/1996-1944/15/1/177
Disclaimer: The views expressed here are those of the author expressed in their private capacity and do not necessarily represent the views of AZoM.com Limited T/A AZoNetwork the owner and operator of this website. This disclaimer forms part of the Terms and conditions of use of this website.