Writing in the journal Polymers, a team of researchers from Oslo Metropolitan University and the University of Oslo in Norway has investigated the void content characterization and constituent components of composite polymer materials.
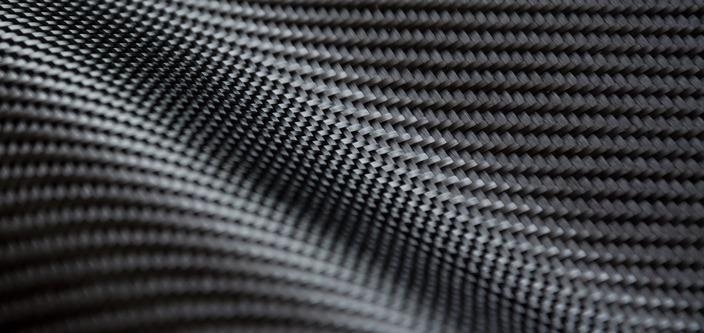
Study: Void Content Determination of Carbon Fiber Reinforced Polymers: A Comparison between Destructive and Non-Destructive Methods. Image Credit: Composite_Carbonman/Shutterstock.com
The team has compared destructive and non-destructive methods and has made recommendations on these methods have been made by the authors based on the application and the type of composite material under analysis.
Void Content and Carbon Fiber Reinforced Polymer Performance
Carbon fiber reinforced polymers have been widely explored for several applications such as marine structural components, piping, aerospace applications, automotive applications, and carbon-fiber microelectrodes. These materials exhibit favorable mechanical and physical properties that make them ideal next-generation materials, and in many cases significantly reduce the weight of components used in numerous technologies.
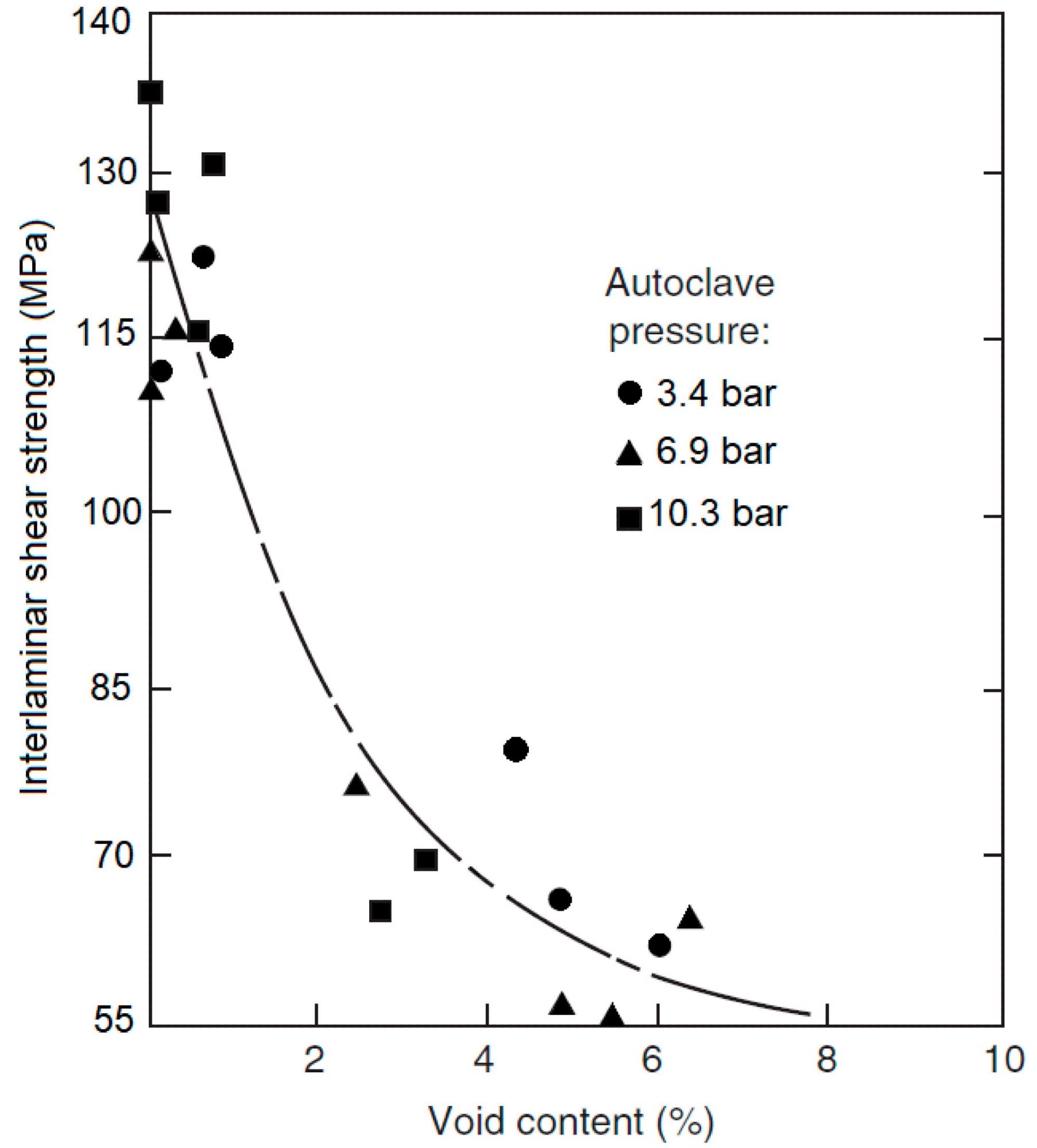
Effect of void content on the interlaminar shear strength. Image Credit: Elkolali, M et al., Polymers
Void content can impact the performance of carbon fiber reinforced polymers. When coating the fibers with resin, voids are formed due to inefficient replacement of air within the fiber structure with resin. Additionally, voids can form during lamination due to the trapping of air bubbles and volatiles. There are other factors that influence the void formation and the consequent quality of materials including the resin’s viscosity, processing parameters such as time and pressure, and the resin’s temperature during manufacturing.
Mainly spherical in shape, voids function can intensify stress and significantly impact the material’s mechanical properties. Laminates with high void contents can crack easily and the bonding between matrix and fiber can be weakened. Void content can also affect properties such as in-plane shear and flexural and tensile strength. Not only do voids affect the mechanical properties of materials, but they also cause fiber damage by facilitating abrasion and increasing the material’s vulnerability to weathering effects and water penetration.
Aside from void content, the fiber and matrix composition of materials influence their properties and performance, having the dominant effect on the composite material’s performance. Knowing the density of the material’s fiber and matrix components as well as the sample’s volume before matrix removal provides information on the void content’s volume.
In the automotive and aerospace industries, standardized gravimetric tests are used to eliminate the matrix content and measure the sample’s mass before and after matrix removal. Recently, the development of numerical techniques and improvements in computational power have facilitated the development of advanced numerical modeling for determining void content in composite materials. Several studies have used different numerical approaches for this purpose, providing useful information for researchers working in the field of carbon fiber reinforced polymer research.
Thus, to ensure the performance and quality of carbon fiber reinforced polymers, the level of void content must be significantly reduced during manufacturing. Several methods have been used to reduce their content during manufacturing such as vacuum bagging and autoclave curing, but these methods cannot entirely remove voids.
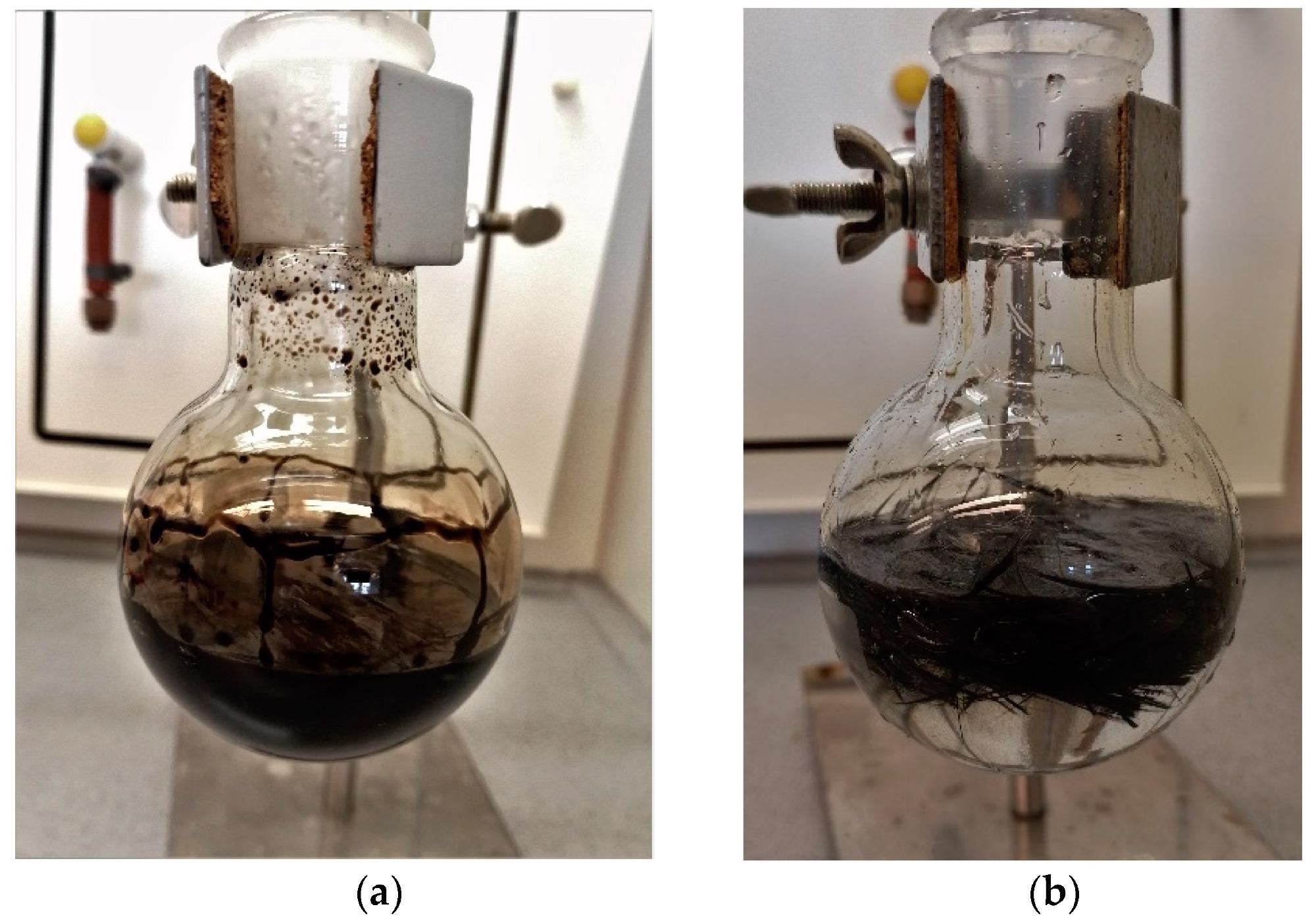
(a) Carbon/Epoxy sample during sulfuric acid digestion; (b) after the addition of Hydrogen Peroxide Description of what is contained in the second panel. Image Credit: Elkolali, M et al., Polymers
The Study
The aim of the new study published in Polymers is to perform destructive and non-destructive testing to determine the fiber, matrix, and void content of samples of filament wound tubes and compare test results. The authors investigated two destructive tests and one non-destructive test.
There were several additional aims of the study. The authors evaluated the destructive tests to investigate their accuracy and make a recommendation on the most suitable test. The non-destructive test was also evaluated. The resolution of this test’s results and the ability to perform and export the 3D analysis were evaluated by the authors. Numerical analysis on the scanned and reconstructed data of tested material samples was performed to enable further research on predicting laminate strengths and comparing results to mechanical tests.
A further aim of the study was to compare the accuracy, availability, and simplicity of the destructive and non-destructive tests. Two acid digestion tests were used for the destructive testing, one with sulfuric acid and one with nitric acid. The non-destructive test performed was Micro-CT scanning.
The authors demonstrated that using sulfuric acid was favorable, being much easier to use. The experiment time was under one hour, compared to forty hours for nitric acid, and using sulfuric acid was cheaper, and could more accurately determine the reinforcement and matrix’s mass content. However, more safety equipment was needed as it involved more hazards. However, destructive testing was not as accurate as Micro-CT scanning for identifying microvoids.
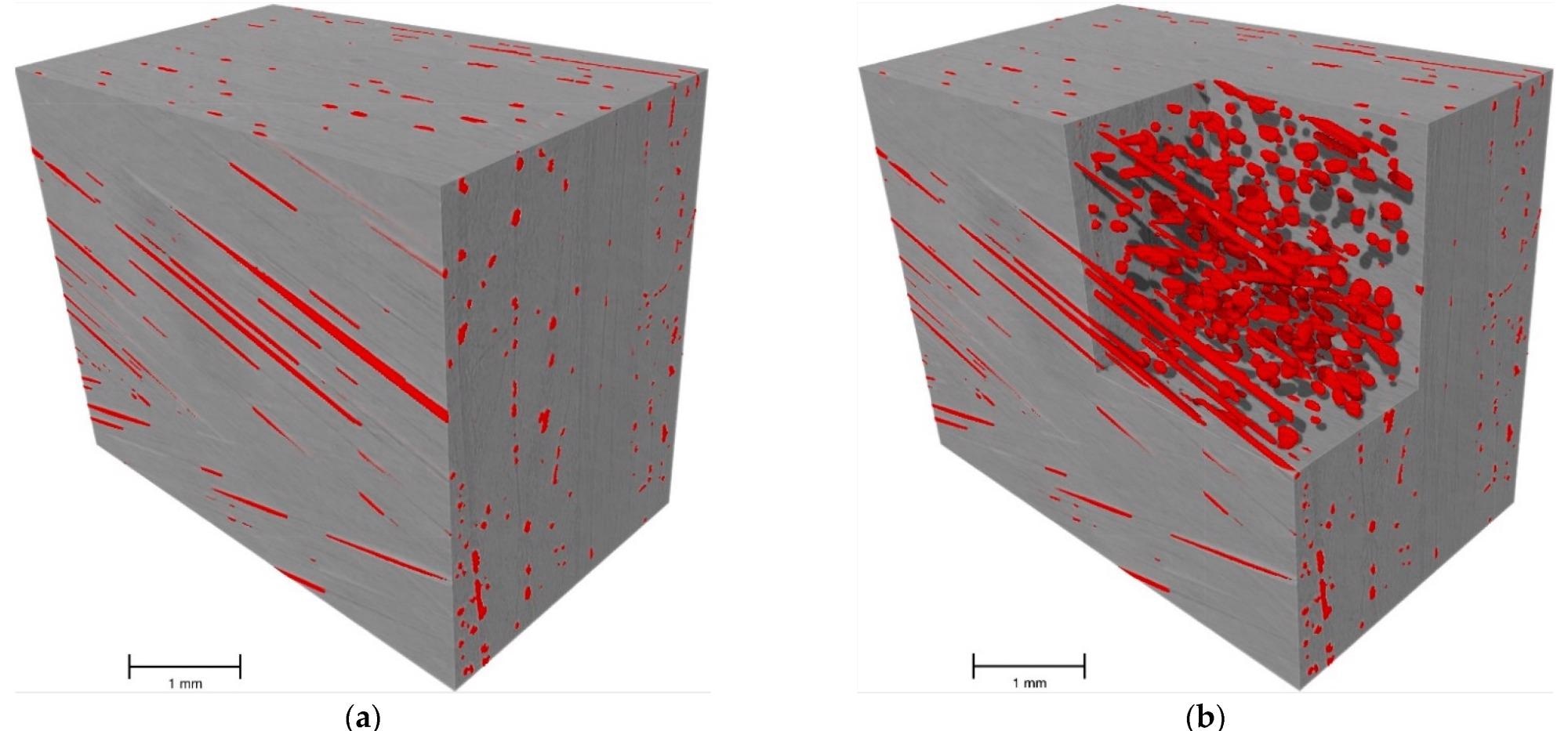
Scanned sample “µCT 2” showing the composite in grey and the voids in red; (a) the scanned sample, (b) a section cut showing the voids in the sample. Image Credit: Elkolali, M et al., Polymers
Whilst Micro-CT scanning can more precisely determine microvoids, results demonstrated that it could not distinguish between matrix and reinforcement due to the lack of considerable difference between them. However, like all non-destructive testing, the advantage of Micro-CT scanning is the possibility of performing further analyses on the same sample.
The authors have stated that future research will involve validation of FEM via mechanical testing and study the correlation of Micro-CT scan results to predict composite laminate in-plain and out-of-plan strengths. Additionally, future work will be used in the design of a deep autonomous underwater vehicle’s hull by adapting the mechanical properties of carbon fiber reinforced polymers.
Further Reading
Elkolali, M et al. (2022) Void Content Determination of Carbon Fiber Reinforced Polymers: A Comparison between Destructive and Non-Destructive Methods [online] Polymers 14(6) 1212 | mdpi.com. Available at: https://www.mdpi.com/2073-4360/14/6/1212
Disclaimer: The views expressed here are those of the author expressed in their private capacity and do not necessarily represent the views of AZoM.com Limited T/A AZoNetwork the owner and operator of this website. This disclaimer forms part of the Terms and conditions of use of this website.