In a study recently published in the open-access journal Additive Manufacturing, researchers explored an approach to control the material properties of three-dimensional (3D) printed thermoplastic elastomer (TPE) foam samples, with adjustments made to the material extrusion process parameters. It was determined that modifications in the printing environments may allow for adjusting a component’s stiffness to weight ratio.
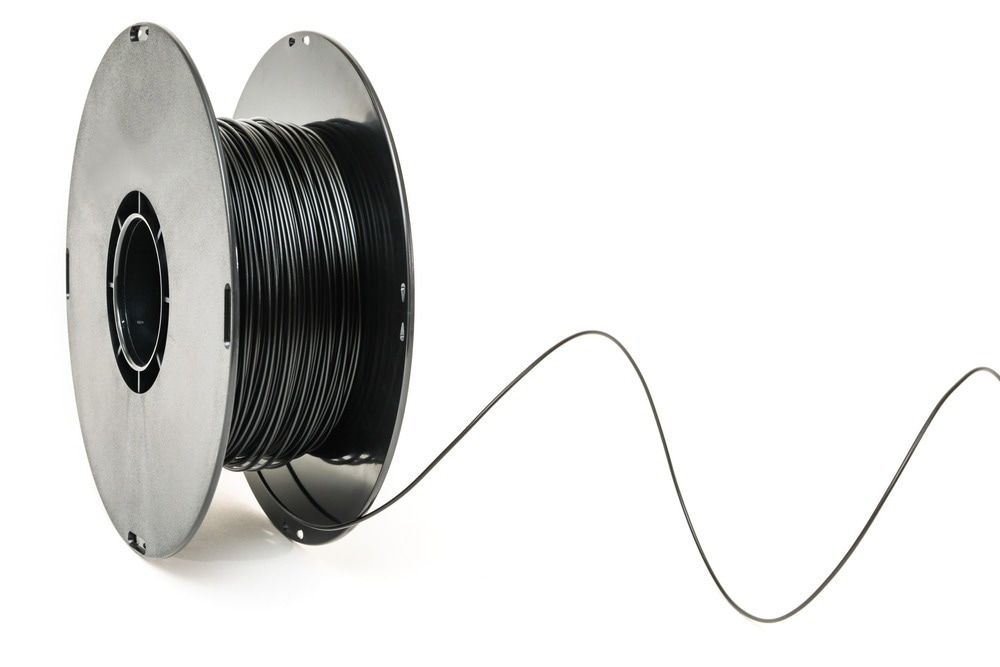
Study: Mastering the density of 3D printed thermoplastic elastomer foam structures with controlled temperature. Image Credit: HannaTor/Shutterstock.com
Background
Research on the variable microscopic structures of multi-scale materials has inspired progress in manufacturing materials and processes for their synthetic production. Polymers have been readily implemented in the manufacture of multi-scale structures owing to their strength-to-weight ratio, ease of processing, and market availability. Many polymer foams are generally manufactured by extrusion and batch foaming.
The manufacture of complex cellular structures is challenging using traditional manufacturing methods. However, advancements in additive manufacturing technologies have allowed their production while controlling the distribution of porosity. Due to the availability and simplicity of various thermoplastic filaments, fused filament fabrication (FFF) or fused deposition modeling (FDM) is a widely employed additive manufacturing method.
These filaments, commonly consisting of polymers like polycarbonate (PC) and acrylonitrile butadiene styrene (ABS), are often used for 3D-printed structures using a 3D volume slicing software to deposit layers via an extruder nozzle.
The present paper analyzed the impact of the temperature of the nozzle on the filament thickness and the reduction in density. Further, the density reduction was predicted in relation to the temperature using a Gompertz function. Finally, the nozzle temperature’s effect on the specific modulus was assessed.
About the Study
In this study, researchers used Nanovia Flex EXP (NFE) foamable filaments compounded with unexpanded thermally expanded microspheres (TEM). The elastomeric samples were 3D-printed with a RepRap DIY Prussa i3 3D printer. A nozzle diameter of 0.8 mm and 0.6 mm was used to print the samples. Furthermore, the compounded TEMs’ melting and glass transition temperatures and the phase change enthalpies were determined by differential scanning calorimetry (DSC), while the sample density was measured using a Mettler Toledo XS205DU balance.
A Mettler Toledo FP82HT hot stage system was used to determine the maximum expansion temperature, average diameter, and initial expansion temperature of the TEMs. Moreover, the TEM geometries and morphologies within the NFE filaments were observed using scanning electron microscopy (SEM) micrographs. On the other hand, the TEMs’ expansion curve was obtained experimentally.
Observations
It was observed that the expansion of the NFE-compounded TEM achieved micro-structural density reduction. It was noted that the sample density would be reduced with an increase in the number of microspheres. During 3D printing, the NFE filament was capable of reducing the sample density with an increase in the nozzle temperature.
Furthermore, in addition to increased layer height and nozzle diameter for thicker prints, the volumetric flow rate of the foamable filaments was further increased due to the expansion of the TEM inside the 3D printer’s heating chamber. However, with a reduced mass flow rate, the NFE filament would spend more time in the 3D printer’s heating chamber and thus melt along the printer’s extruder and clog the system. Increasing the layer height or the speed of printing could avoid this failure.
Additionally, the SEM cross-section micrographs of the samples exhibited an increase in cell density. It was also observed that the cell distribution remained homogeneous across the samples even though the increased temperature led to an increase in cell density. A reduction in the voids between the deposited sample layers was due to TEM expansion as a result of increased nozzle temperature. Moreover, the team found that the density was affected by the TEM volume fraction and decreased with the temperature increase due to TEM expansion.
Although a linear curve was obtained depicting density reduction in line with rising TEM volume fraction, the foamed samples and the unexpanded filaments printed at 240 °C showed a nonlinear behavior at a 200-250 °C nozzle temperature. To account for this, the Gompertz function was used to assess the density reduction with respect to temperature. In addition, it was also observed that the rise in nozzle temperature decreased the samples’ tensile strength, caused due to the increased microporosites inside the samples as a result of the TEM expansion.
Conclusions
To summarize, the team studied the physical characterization and the capability of foamable filaments to produce microscopic-level closed-cell morphologies using the FFF process. According to the authors, the manipulation of the 3D printing parameters gives a novel approach to the FFF 3D printing process, which allows in situ foaming along with specimen fabrication with foam gradients, providing a potential application of foamable filaments in the production of gradient structures.
More from AZoM: How Can Polymer Strips Be Used to Clean Up Oil Spills?
Source
Ajinkya Pawar, Gilles Ausias, Yves-Marie Corre, Yves Grohens, Julien Férec, Mastering the density of 3D printed thermoplastic elastomer foam structures with controlled temperature, Additive Manufacturing, 2022, 103066, ISSN 2214-8604, https://doi.org/10.1016/j.addma.2022.103066
Disclaimer: The views expressed here are those of the author expressed in their private capacity and do not necessarily represent the views of AZoM.com Limited T/A AZoNetwork the owner and operator of this website. This disclaimer forms part of the Terms and conditions of use of this website.