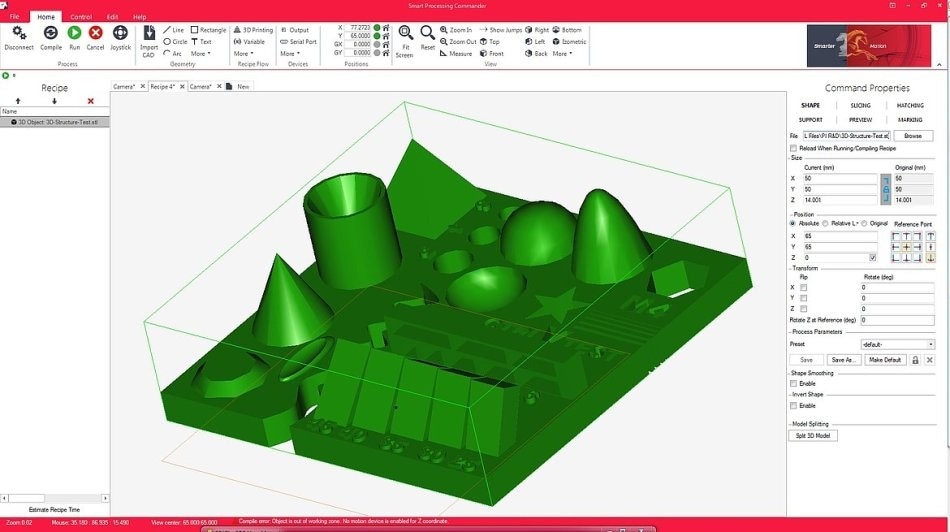
3D Printing Software allows direct import of industry standard STL files
The building blocks of 3D printing can be found in mid-nineteenth century Paris and the work of Sculptor and Photographer, François Willeme. Willeme patented a photographic technique to capture and create 3D data models which were able to be of use in recreating solid objects. Additional work in the latter part of the nineteenth century to create topological relief maps, in a layer-by-layer fabrication approach, was done by Joseph Blanther. These concepts would be apparent in the first practical demonstration of 3D Printing in the 1980s, when Charles Hull made the history books by inventing Stereolithography (SLA) with Selective Laser Sintering (SLS) to follow quickly afterwards.
Ever since, additive manufacturing technology has grown in both materials and methodology resulting in more accurate structures created in more workable materials with additional demanding dimensional tolerances and feature sizes to the micron scale and sub-micron scale. Current methods include both direct material dispense (DIW, for example) and laser techniques, such as Two-Photon Polymerization, and in a few instances, both put together onto one system.
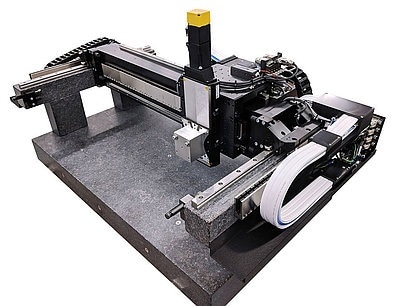
A-351 3D Print optimized gantry platform
Direct Ink Writing
In material dispense, Direct Ink Writing (DIW) fabrication methods are taking on a significant role in the advancement of 3D printing at key research institutions such as the Colorado School of Mines. At these preeminent institutions, materials research and methods come with system level necessities that must contemplate various material properties such as rheological behavior, composition, feature size, and placement precision (particularly vital for layer-by-layer fabrication with µm scale resolution) across the same coordinate system.
To explore applications in DIW, PI supplies an impactful and intuitive 3D Printing Software that enables import of industry standard STL files directly with adaptable parameter settings and batch processing for multiple print jobs (outstripping alternative systems that are limited to DXF file format and constraints for 3D Print).
This software also enables integration of laser-based processes with fixed or scanning optics, machine vision, and is able to integrate and communicate with other peripherals. The software conversion from model employs the most powerful trajectory algorithm and performance commercially available with the use of ACS XSEG and material dispense is arranged directly in accordance with user-settings straight from motion controller through hardware layer to dispenser.
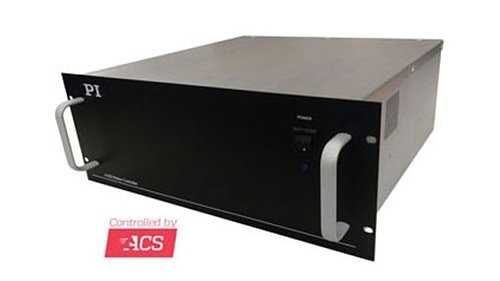
PI’s ACS-based motion controller provides EtherCat connectivity, drives the gantry and seamlessly communicates with the 3D Printing Software.
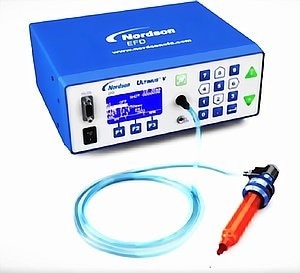
Ultimus™ V High Precision Dispenser (Image: Nordson)
PI’s ACS-based motion controller provides EtherCat connectivity, drives the gantry and seamlessly communicates with the 3D Printing Software.Ultimus™ V High Precision Dispenser (Image: Nordson)
3D Printing motion systems are constructed from standard 3D Print optimized gantry platforms and pre-configured to be used with Nordson Ultimus V (or customized to extruder). The direct hardware integration has been taken into consideration. The cabling for interface and triggering of the dispenser is supplied with the system, set to peak for controller cycle time and developed for the right trigger voltage. This enables easy integration, exceptionally strong performance, and the motion sub-system to ease R&D and commercial 3D Printer constructions.
With PI Motion, highly performing 3D Print Systems can be constructed in only a few days, are compatible with industrial standard STL files, and provide the greatest level of performance.
3D Bio-Printing
The potential of directly printing living organs, bone, tissue, and cartilages is so unprecedented in its size and implications that it would seem to exist more comfortably in the field of science fiction than real life. However, leaders spearheading the field of Bioprinting have already started adapting 3D printing technology to explore applications in the engineering of tissue and regenerative medicine.
Bioprinting exists at the cutting edge of complex materials and general process tolerances. The process can need both mapping (using techniques such as non-contact optical metrology and even at the cellular level requires process control). PI has been preparing for the future of Bioprinting with exceptionally performing flying gantry systems that are entirely non-wearing with software that can bring in third-party peripherals like scanners and profilers (both capable of capturing 3D profiles) and conducting layer-by-layer fabrication from these profiles.
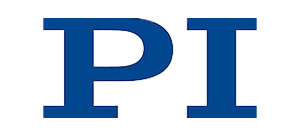
This information has been sourced, reviewed and adapted from materials provided by PI (Physik Instrumente) LP.
For more information on this source, please visit PI (Physik Instrumente) LP.