Could you start by providing a short overview of QATM and the company's work?
QATM was launched at the beginning of 2020 from two different Verder Scientific companies - ATM (experts in materialography) and Qness (innovators in hardness testing). The company employs around 200 staff between its two sites in Germany and the one in Austria.
The company's comprehensive portfolio includes everything required for metallography/materialography and hardness testing, including metallographic cutting, mounting, grinding and polishing machines, hardness testers, analysis software, lab furniture and consumables.
QATM works with international partners to distribute its portfolio of products in over 40 countries across the globe.
What is materialography, and how does this typically affect sample preparation?
Materialography or metallography is first and foremost the study of a material's microstructure. Materialography aims to investigate a material's technical properties – generally an essential factor in material development or quality control applications.
Samples must be prepared to enable this investigation, irrespective of whether a material is destined for use in steel production, the transportation industry, in the optical or electrical industry or for use in research in any of these sectors.
How important is metallographic grinding and polishing for the sample preparation process?
A material will typically undergo several procedures before the microstructure can be accessed. Metallographic grinding and polishing are vitally important as the final steps in mechanical sample preparation. Contrasting is often necessary to ensure that the microstructure is visible after polishing.
It is occasionally necessary to perform etching after metallographic polishing, but this depends on the specific details being investigated and is more common when working with metals.
High-quality analysis requires the preparation of a scratch-free surface with good flatness – a key factor when analyzing layers, coatings or electronic components. It is important to select appropriate sample preparation methods which are not too aggressive, as this may result in vital features of interest being worn away.

Placing a specimen into a manual grinding & polishing machine
Could you explain the basic steps of the materialographic grinding and polishing process?
Grinding and polishing involve a step-by-step reduction of the roughness of a surface to access the undeformed structure.
This process is based on using abrasive particles in progressively finer grain sizes. In materialographic grinding, these abrasives are bonded in resin or metal matrix, with the most frequently used grinding abrasives being silicon carbide particles. These particles are often used when working with softer, medium or hard materials, composites and electronics. It is also possible to utilize diamond particles for harder components like ceramics, carbides, glass or stone. Operators should always select abrasives that are harder than the material being prepared.
The use of bonded abrasives yields a high abrasion rate which is ideal for removing rust surface deformations from the cutting process, or material blocking the area of interest, but also for achieving a high degree of flatness.
Metallographic grinding can be categorized as planar grinding, fine grinding or ultra-fine grinding, with the classification depending on the size of the abrasive particles.
Polishing processes involve loose abrasives which roll over the surface. This is gentler and leads to a better surface finish but also yields lower removal rates. Metallographic polishing eliminates any remaining roughness from the grinding process, ensuring a good surface finish for further examination.
The most common abrasives in materialographic polishing and mechanical material removal are fine diamond particles (used in pre-polishing or intermediate polishing) or oxides, such as silica or alumina (used in final polishing).
What factors should be considered when selecting equipment and consumables for metallographic grinding and polishing processes?
There are a number of questions that should be considered prior to the selection of equipment and consumables. It is advisable to first consider the materials you want to prepare as the choice of consumables will be influenced by material properties such as hardness or ductility.
Defining the overall aim of the preparation process is another important factor. The goal of any metallographic grinding and polishing process is to achieve an acceptable result for the specific purpose. It is not always necessary for the true structure to be available at the highest resolution.
For example, an EBSD analysis requires a completely defect-free surface, but a macro-level analysis does not. Other factors influencing the suitability of a machine may include sample size, geometry and required throughput.
What are the most common types of metallographic grinding and polishing machines available from QATM?
Different types of manual and automated grinding and polishing machines are available. The simplest and least expensive type is a manual grinding and polishing machine with a rotating working wheel.
These manual grinders are available from QATM in a single version – the QPOL 250 M1 – as well as in a twin version - the QPOL 250 M2. Laboratories operating with a very low sample throughput may choose to opt for the simplicity of a manual machine.
Grinding and polishing machines Qpol 250 M1 / M2 | QATM
QATM's QPOL 250 M-Series
Semiautomatic machines feature a grinding and polishing head with an attached sample holder. These are also available in single or twin versions. These machines are labelled semiautomatic because sample cleaning and changing the consumables between steps are still manual processes.
Fully automatic systems, in contrast, are able to complete the entire metallographic grinding and polishing procedure without user intervention. All the user has to do is to set the parameters for all steps and press the start button.
QATM offers two fully automatic grinding and polishing machines. The QPOL 250 BOT for 250-millimeter working wheel diameters, and the QPOL 300 BOT for 300-millimeter working wheel diameters.
A portable grinder and polisher is also available from QATM – the QPOL 30 (SAPHIR 300). This machine features a grinding and polishing tip that is 30 millimeters in diameter.
The QPOL Vibro polisher from QATM has been specifically designed for vibration polishing - a method which ensures a particularly high-quality surface finish in a final polishing step.
For vibration polishing, samples are placed into a vibration bowl and the vibration causes the samples to move over the polishing cloth. This procedure provides very gentle abrasion and is highly suited to prepare samples prior to EBSD analysis.
Vibratory polisher Qpol Vibro | QATM
Qpol Vibro Polisher
What are the advantages and uses of the different types of consumables for metallographic grinding and polishing machines?
A wide range of consumables are available for grinding; for example, silicon carbide or grinding papers and foils are available in a range of grid sizes.
Papers or foils are typically more expensive than some of the abrasion options discussed so far, but these offer a higher abrasion rate and can be used multiple times before needing to be replaced. These are also necessary for applications like spectral analysis, where it is essential to avoid cross-contamination.
Grinding disks offer an alternative to grinding paper or foils. Grinding disks feature a rigid steel courier and either silicon carbide or diamond abrasive particles. These offer a higher rate of plainness and sharpness than grinding paper or foil.
A single disk can replace over a thousand grinding papers depending on the disk and the application, affording excellent reusability. Should a grinding disk become smeared, the surface can be easily cleaned using a cleaning stone.
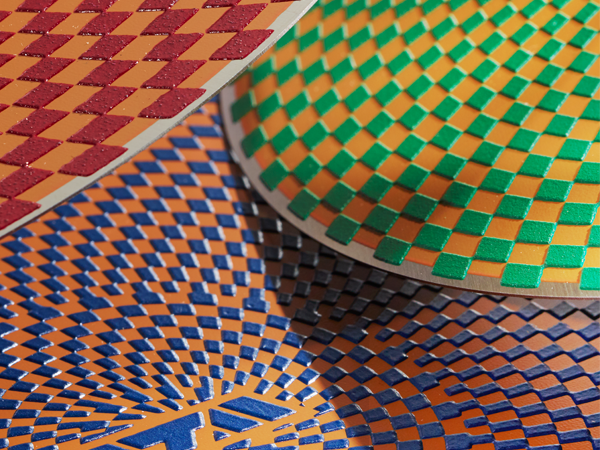
Metallographic grinding discs by QATM
Fine grinding (or lapping) is an additional, optional step that may be applied between grinding and polishing. This process uses a hard base and applies loose abrasive particles in the form of diamond suspension. QATM offers the Contero H disk for medium to hard materials and the Contero S for soft materials. These disks produce very planar samples with high edge retention due to their hard base.
Metallographic polishing consumables can generally be categorized as polishing abrasives and polishing cloths. Polishing abrasives are often supplied as diamond particles in the form of a suspension, a paste or a spray, in combination with a lubricant. These diamond suspensions and lubricants may be water-based, but water-free alternatives based on oil or alcohol are also available for specific applications.
Oxides are typically employed in final polishing. QATM offers several silicon dioxide and aluminum oxide products in the form of suspensions. Each product offers specific properties; for example, suspensions may be designed to maintain their liquid form for several days prior to crystallizing.
A wide range of polishing cloths are available, and these differ greatly in terms of the height of their fibers and their resiliency or stiffness. QATM offers a range of stiffer or harder fiber cloths (for example, Alpha or Beta) which are ideal for pre-polishing with diamond abrasives. These types of cloths offer the effective removal of surface roughness, while softer and higher napped polishing cloths (for example, Iota or Zeta) offer a gentler abrasive interaction for the final polish.
The abrasive polishing medium and the polishing cloth must be compatible. Once consumables are in place, it is also advisable to apply sufficient amounts of abrasives and lubricant to guarantee an appropriate result.
What are the typical steps and considerations involved in a manual grinding and polishing process?
It is important to apply sufficient water at the start of the materialographic grinding process to provide cooling and avoid any thermal influence on the microstructure. The water also has a cleaning effect, helping to prevent formation of grinding dust. It is important not to use too much water, however, as this may result in unwanted aquaplaning.
It is advisable to hold the sample with two hands to maintain a good grip and stability when preparing samples manually. Moderate, consistent force should be applied when moving the sample slowly over the whole radius of the working wheel. It is important to move the sample back and forth to make use of the entire grinding area.
The surface of the sample must be kept parallel to the grinding surface, and the rotation direction should be kept away from the body. If the operator accidentally lets go of the sample, the sample would be launched away from their body, minimizing the risk of injury.
A suitable grid size should be able to remove all previous scratches in a reasonable time. A single step should not last more than two minutes, and the sample needs to be rotated 90 degrees each time the grinding process moves down a size. This allows the operator to verify that every scratch from the previous grinding step has been eliminated.
Lubrication is also an important consideration for metallographic polishing steps, and it is advisable to keep polishing time as short as possible to minimize the chance of artifacts arising.
The sample should be cleaned thoroughly between all grinding and polishing steps to ensure removal of any remaining grinding or polishing particles which may affect the result or contaminate the polishing cloth.
Cleaning is typically performed using an ultrasonic bath or a combination of water and ethanol. A blow dryer may be used to efficiently dry the sample.
Does an automatic grinding and polishing process require a different approach?
One notable difference in automatic grinding and polishing is that it requires parameter setting for the designed program. Grinding programs will usually employ a rotation speed of approximately 300 RPM while polishing programs will use a speed of approximately 150 RPM.
Another difference is that the direction of rotation may vary. Moving the sample holder in the opposite direction to the working wheel will lead to a higher removal rate but also to higher deformation.
In contrast, synchronous rotation - with both sample holder and working wheel moving in the same direction - is less aggressive, resulting in lower removal rates, but also less deformation.
Positioning the sample holder too close to the center of the working wheel will result in samples extending beyond the edge of the wheel and lead to suboptimal grinding and polishing dynamics. The sample holder should ideally extend approximately 1 cm beyond the edge of the working wheel.
The majority of automatic grinding and polishing machines allow the application of force in central or single pressure mode. Central pressure mode applies force to the entire sample holder, and any samples clamped into this. This option is ideal for use with large samples or individual shapes.
Single pressure mode does not fix a sample, however. One or more samples are loose in the holder and are free to move around. Samples must have a round shape to benefit from this mode of operation. Force is applied directly via pins.
Automatic grinding and polishing machines require operators to set the duration of each individual step, including activating and setting dosing parameters, for any automated dosing system which may be in use.
Samples should also be cleaned between each step, even when working with automated grinding and polishing processes
How much do these processes vary depending on the sample material?
Metallographic grinding and polishing processes differ depending on the sample material. These differences usually affect the consumables required or the number of necessary grinding and polishing steps.
For example, steel with a hardness between 35 and 65 HRC (medium-hard to hard steels) is relatively easy to prepare. It only requires a three-step preparation method to ensure adequate results. Three grinding steps using grinding paper or grinding disks are sufficient, and the entire procedure is a matter of minutes.
It may be advisable to add an additional macro analysis step when working with more complex samples like welded joints, but polishing steps are not usually required for these samples.
In contrast, magnesium is very difficult to prepare. Magnesium is very soft and needs a number of materialographic grinding and polishing steps to ensure acceptable results. Preparation is complex and can take around 45 minutes. Ceramic materials typically exhibit a high degree of hardness, necessitating the use of diamond abrasives; for example, diamond grinding disks in two different grain sizes for grinding and diamond suspension on hard polishing cloths for polishing.
The preparation of sample materials that possess both hard and soft components, such as composites of ceramic and copper, is especially challenging. This type of sample forces users to choose between a preparation method for ceramics or a preparation method for copper, but the method chosen generally depends on the desired result.
For example, operators aiming to analyze the whole sample may need to prepare the sample twice, using two different preparation methods in order to analyze it fully. It would be quite difficult to develop a complex preparation method like this.
What are the most common issues arising in metallographic grinding and polishing processes?
A range of issues and artifacts may arise throughout grinding and polishing, with a single mistake potentially falsifying a final analysis result.
Pull-outs are one such commonly encountered type of artifact when working with brittle parts. If pull-outs are not cast in cutting or mounting, these are usually a result of aggressive grinding or polishing and can be avoided by using synchronous rotation in all grinding and polishing steps, except for the final polishing step, and ensuring the polishing cloth in use is relatively soft.
Pull-outs may be found in cast iron, components, coatings and composites, though these may be wrongly identified as cavities in the material.
Foreign inclusions can arise when the pressure is too high or during the preparation of very soft materials with a very hard abrasive such as diamond. This results in abrasive particles becoming embedded in the sample surface - a frequently encountered issue when working with composite materials which feature components of soft and hard phases, or when working with materials with varying hardness on one polishing cloth.
A number of steps can be taken to help avoid foreign inclusions, including using similar materials on one polishing cloth, selecting the most suitable abrasives for the sample material or storing polishing cloths in a dust-free environment.
Reliefs tend to occur when materials with different phases are polished for an extended period. The harder phases will, therefore, be more prominent than the softer phases. This artifact is generally the result of over-polishing and can be minimized by keeping the sample as flat as possible by using grinding disks that feature a hard carrier. Preparation time should be kept to a minimum, especially in the final steps. It is also advisable to use a polishing cloth with low elasticity.
Comet tails are found where non-metallic inclusions, pores and hard phases in a soft, basic matrix are held in one grinding and polishing direction during manual preparation. Comet tails are an issue when working with large sample materials but can be avoided by moving samples in such a way that there is no preferred direction.
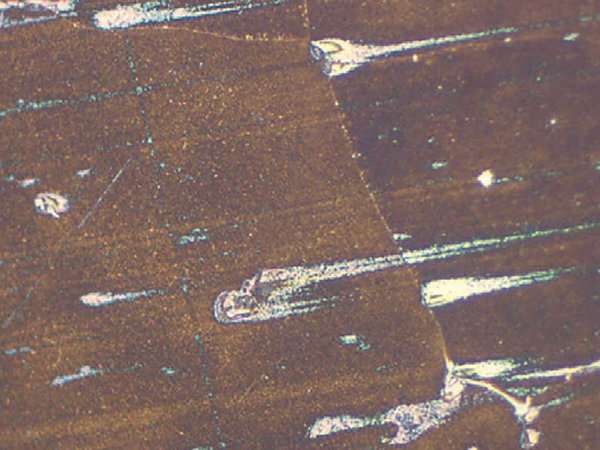
Specimen with comet tails
Discoloration or stains on the sample surface may be the result of drying marks of residual suspension, water or ethanol left over due to insufficient cleaning. This issue is not serious and can be easily addressed by correctly identifying the stains and applying additional cleaning steps.
Sample corrosion may occur when using a water-based preparation method for corrosion-prone samples, or when the sample is not dried fast enough. It is advisable to use an alcohol- or oil-based method to prepare extremely corrosion-prone samples.
Edge rounding is an issue when working with components featuring different degrees of hardness, for example, composites or a hard material embedded in a softer resin. This results in a soft material being removed faster than a hard material. Edge rounding effectively leads to two levels of sample, with a transition occurring at the interface where the material is rounded off. Investigation in these regions is very challenging.
Edge rounding is caused by the use of materialographic grinding and polishing media with a soft elastic base, so the use of grinding and polishing disks with a hard base for pre-polishing can help minimize or avoid this issue. The final polishing steps should be kept as short as possible.
Scratches may be found when a sample is not appropriately polished. Scratches occur in composites from one of the previous grinding steps, when one component is well polished but another shows scratches because of their varying hardness. Scratches may also occur when samples are not handled with proper care.
The initial preparation of a new material often involves a degree of trial and error. Operators will identify artifacts and determine their cause throughout the process. To streamline this process, it is important to check the sample by microscope after each individual preparation step. This allows the operator to identify which step caused the issue.
About Matthias Ziegenhagen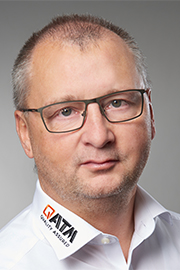
Matthias Ziegenhagen joined QATM in 2017 as an area sales manager for the northeastern part of Germany. He took over the role of sales manager for the German sales team before he changed to international sales management for the non-Verder distributors. At that time, he became the head of the QATM-Academy, doing all training courses for customers in Europe and abroad. During the pandemic, he wrote our ‘QATM-Expert Guide’.
He is a trained metallographer with more than 40 years of experience. He holds a degree in Material Science and in Quality Management. For nearly 20 years of his professional career, he was working in a Heat Treatment Shop.
This article is based on a webinar held by QATM. Click here to watch the free on-demand webinar on the Introduction to Metallographic Grinding & Polishing.
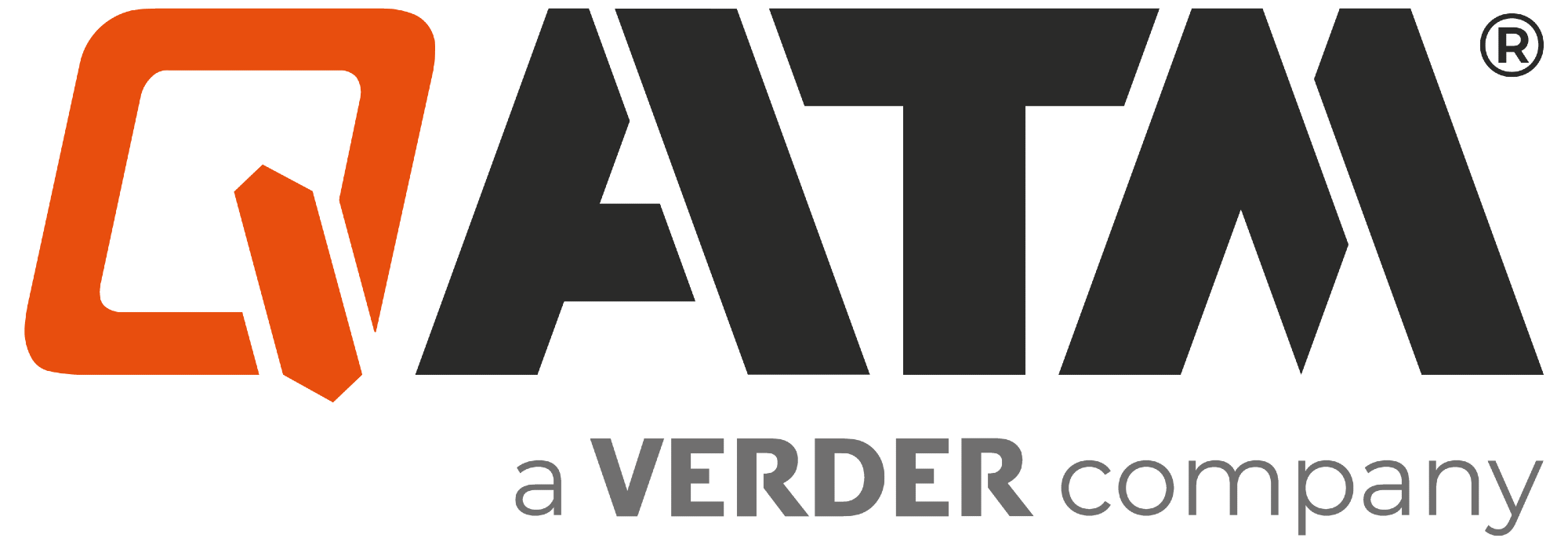
This information has been sourced, reviewed and adapted from materials provided by QATM.
For more information on this source, please visit QATM.
Disclaimer: The views expressed here are those of the interviewee and do not necessarily represent the views of AZoM.com Limited (T/A) AZoNetwork, the owner and operator of this website. This disclaimer forms part of the Terms and Conditions of use of this website.