Sponsored by PerkinElmerReviewed by Olivia FrostMay 14 2025
Advanced materials drive key improvements in automotive vehicles, benefiting manufacturers and consumers. As a result, ensuring reliable testing methods is essential.
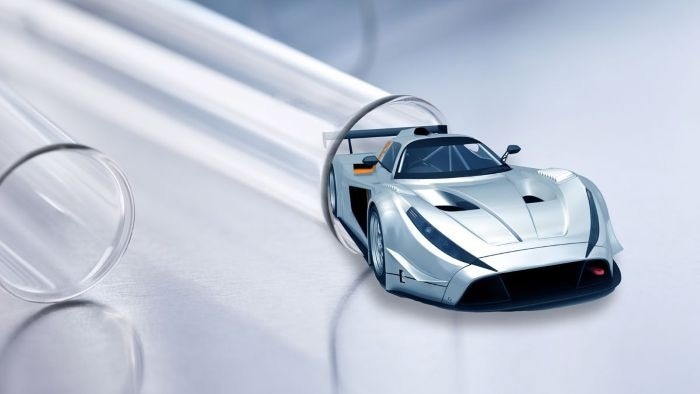
Image Credit: PerkinElmer
The development and application of advanced materials enhance vehicle design and production capabilities. These materials improve performance, safety, fuel efficiency, and sustainability.
Applications of advanced materials in the automotive sector include tire rubber, polymer cables, elastomers, and other silicone rubber components used in engines, interiors, and seating. However, all these materials must be tested to verify their durability and long-term performance under demanding conditions.
Lightweight Materials Improve Fuel Efficiency
Lightweight materials such as carbon fiber-reinforced composites and advanced polymers are increasingly replacing conventional metals such as steel and aluminum. These alternatives provide a superior strength-to-weight ratio, making vehicles lighter and more efficient. Reduced weight decreases energy consumption, enhancing fuel efficiency, lowering emissions, and extending battery life in electric vehicles.
Although steel remains a fundamental material in the industry, recent advancements have led to the development of high-strength steel (HSS) alloys. These alloys combine durability with reduced weight, making them ideal for reinforcing critical structural components.
Similarly, aluminum has been a key material for decades, and innovations in aluminum alloy technology have enhanced its strength, corrosion resistance, and durability, making it even more attractive to automotive manufacturers.
Depending on detection requirements, inorganic analysis methods using AA, ICP-OES, or ICP-MS are utilized to quantify metals and alloys.
Testing Techniques and Technologies
The application of advanced materials in automotive manufacturing determines the necessary testing requirements. Certain materials must be evaluated for their performance under extreme heat and pressure, while others require testing for durability against wear and friction. This also applies to safety assessments for off-gassing, which contributes to the characteristic "new car smell" for plastics in vehicle interiors.
PerkinElmer collaborates with manufacturers to study advanced materials by offering analytical instrumentation, expertise, and support services to drive innovation. Its solutions are designed to conduct a full range of analysis on advanced materials, tracking any changes in rheological properties under dynamic conditions while precisely controlling temperature, time, frequency, stress, atmosphere, or a combination of these factors.
For high-throughput sample processing, the Pyris™ 9 line of thermal instrumentation provides rapid cooling capabilities, significantly reducing the time between analysis cycles. Accelerated cooling rates enable increased batch processing, enhancing overall efficiency through continued use.
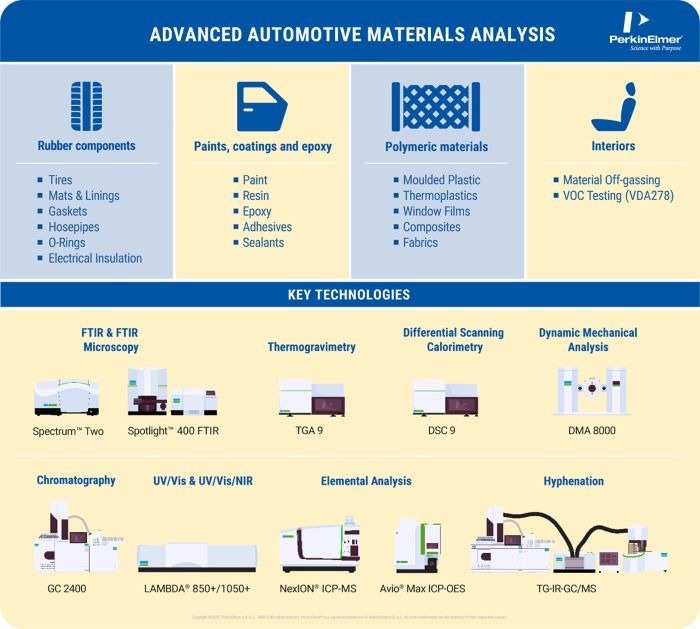
Image Credit: PerkinElmer
Mechanical Analysis in Rubbers
Polybutadiene rubbers are commonly utilized in applications where the ability to deform and return to the original shape is crucial, such as for car tires, wiper blades, and gaskets. Dynamic mechanical analysis (DMA) is highly effective in characterizing the material and assessing the final product's performance to ensure optimal compound properties and compliance with international abrasion standards.
Stimuli-Responsive Materials
A new class of materials used in the automotive industry includes stimuli-responsive materials, which can modify their properties in response to external environmental changes. This category includes thermoresponsive materials and electroactive polymers. Thermoresponsive materials are commonly derived from polyacrylamide, while electroactive polymers are often based on PVDF-derived materials.
TGA and DSC are key techniques for characterizing and assessing the quality of these materials. Evaluating factors such as thermal stability, degree of crystallinity, and phase-change behavior ensures that these materials respond appropriately to external stimuli.
Nanomaterials Driving Change
Thermogravimetric analyzers (TGA), Fourier-transform infrared spectroscopy (FTIR), and ultraviolet/visible/near-infrared spectroscopy (UV/VIS/NIR) instruments are essential for analyzing polymer components such as cables and molded plastics used in the automotive industry.
Coatings and paints have significantly advanced in recent years through the incorporation of inorganic or carbon materials, which can be characterized using FT-IR and UV-Vis techniques.
Implementing additives in the coating and paint mixtures imparts new properties that resolve challenges such as softening, delamination, and cracking that polymeric films tend to face. Carbon nanomaterials, including carbon nanotubes (CNTs) and nanoparticles (NPs), are commonly utilized for this purpose.
Various NPs, such as ZnO, FeO, CeO, TiO2, and silica, are integrated into conventional coatings to enhance sunlight resistance. With their wide surface area, these NPs effectively absorb the damaging ultraviolet component of sunlight, protecting coatings against weather-induced degradation.
Assessing the final composites and evaluating the impact of additives is crucial for understanding material improvements. In this context, FT-IR and UV-Vis provide valuable insights into polymer composition and additives' influence on the finished materials' spectroscopy properties.
Hyphenated Solutions & 3D Printing
Such solutions can also be hyphenated, or joined together, to conduct the most comprehensive analysis required for advanced materials. For instance, DSC/TGA and FT-IR instruments are commonly used to characterize advanced coatings and paints, including innovative smart coatings and epoxy resin. These can be coupled with a gas chromatography mass spectrometer (GC/MS) to identify potential degradation products from evolved gases.
As 3D printing with specialized additive materials gains traction in the automotive industry, parts are increasingly customized, and prototypes can be produced rapidly.
With these experimental manufacturing methods, additive materials must undergo rigorous testing, including monitoring the chemical composition of evolved gases during 3D printing. Hyphenation of TGA with FTIR, MS, and GC-MS instruments enables manufacturers to analyze evolved gases more effectively.
The Pyris™ 9 thermal range from PerkinElmer offers comprehensive control over the sample environment and, with its rapid cooldown rate, ensures high throughput and reliability, along with the flexibility to operate autonomously when needed.
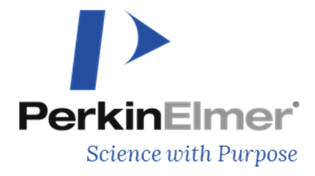
This information has been sourced, reviewed and adapted from materials provided by PerkinElmer.
For more information on this source, please visit PerkinElmer.