The injection blow moulding process is a key conventional process that enables the production of hollow plastic parts from a pre-moulded semi-finished piece, commonly referred to as a preform. It typically takes place in two main stages:
Stage 1: A semi-finished precursor, known as a preform, is created. This stage establishes important features like threading (especially for bottles), weight, and color.
Stage 2: The final shape and characteristics of the product are formed by applying heat and pressure, blowing air into the preform produced in the first stage.
Characteristics of the Injection Blow Moulding Process
This process helps achieve more accurate dimensional tolerances in final containers compared to other blow moulding techniques, resulting in products with enhanced barrier properties. Such attributes make the process particularly suitable for applications demanding high control over the container's specifications.
AIMPLAS Solutions
- Production of pre-series for validating products and ensuring regulatory compliance.
- Identification and selection of optimal material alternatives based on specific product needs.
- Development of CAE studies to confirm design suitability during project phases.
- Creation of prototypes for geometric and functional validation.
- Assessment of barrier properties influenced by process parameters and final product design.
- Adjustment of process parameters to align with product requirements and stabilize the process.
- Validation of new material developments for hollow part applications.
Conducting training sessions on the injection blow moulding process.
Equipment
To address the increasing demands in the plastics sector, AIMPLAS possesses blow moulding equipment designed for versatile analysis and validation of innovative developments in injection-blow-moulded containers. The blow moulding units support testing of various materials, including recyclable and recycled polymers and bioplastics, in line with the industry's sustainability initiatives.
These units facilitate swift changes in container design, allowing for demonstrative validation across any industry that can benefit from tailored solutions. Additionally, training sessions can be conducted at AIMPLAS facilities, offering dynamic, hands-on educational experiences to tackle potential challenges in the injection blow moulding process.
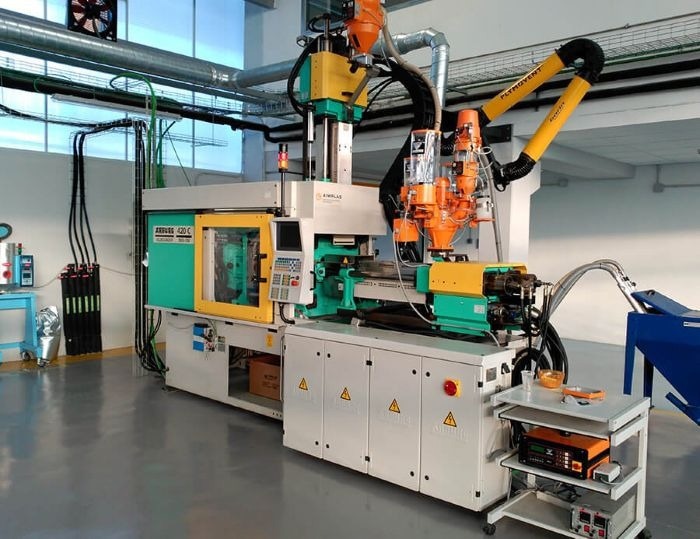
Image Credit: AIMPLAS
Materials Used in Injection Blow Moulding: PET and Sustainable Alternatives
PET is the primary material for producing injection-blow moulded containers, particularly bottles. However, AIMPLAS’ advancements enable the testing of diverse polymer types, including recyclable and recycled materials, as well as bioplastics, to align with the environmental and sustainability goals that society and the plastics industry are increasingly prioritizing.
Main Applications of the Injection Blow Moulding Process
The injection blow moulding process is primarily employed in manufacturing food, cosmetics, and pharmaceutical containers. It also finds applications in the automotive and agricultural industries. This process's versatility allows for the production of containers in various shapes and sizes while optimizing their durability and properties to meet the unique demands of each industry.

This information has been sourced, reviewed and adapted from materials provided by AIMPLAS.
For more information on this source, please visit AIMPLAS.