The FT4 Powder Rheometer - a universal powder tester for measuring powder flow properties and powder behaviour.
The FT4 was design for comprehensive powder characterisation, as a tool for solving powder processing issues. It differs from other powder testers in many ways but when assessing industrial value, three features are critical:
- The ability to simulate powder processing conditions, by testing samples in a consolidated, moderately stressed, aerated or fluidised state.
- The application of multi-faceted powder characterisation to assess dynamic flow, bulk and shear properties to construct the most comprehensive understanding of how a powder behaves.
- Unparalleled sensitivity, enabling the differentiation of powders that other testers classify as identical.
The FT4 Powder Rheometer® employs unique technology for measuring the resistance of the powder to flow, whilst the powder is in motion.
In addition to unique dynamic methodology, the FT4 also includes a shear cell for measuring the powder’s shear strength, a wall friction kit to quantify how the powder shears against the wall of the process equipment (in accordance with ASTM standard D7891), and includes accessories for measuring bulk properties, such as density, compressibility and permeability.
The range of measurement capabilities makes the FT4 a truly universal powder tester and by far the world’s most versatile instrument for measuring and understanding powder behaviour.
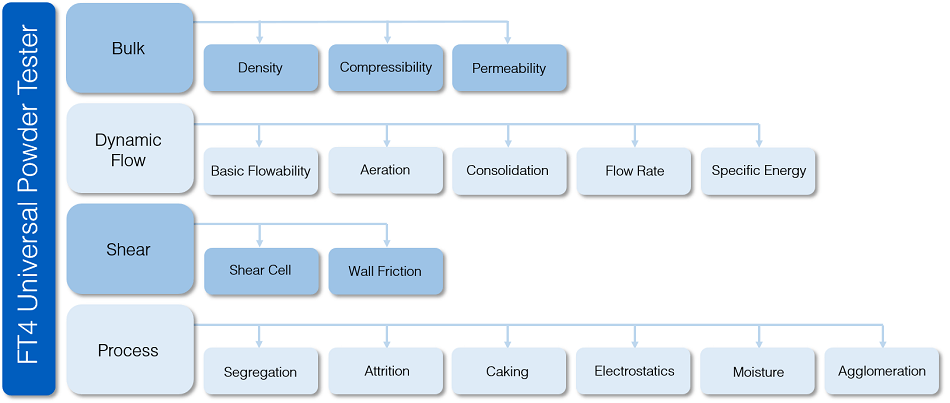
Features
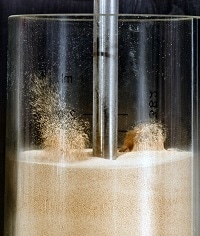
- Fully automated test programs and data analysis
- Conditioning mode provides unparalleled repeatability
- Range of sample size, 10ml to 160ml (in addition a 1ml Shear Cell can be selected for limited sample size)
Download the Brochure for More Information
FT4 Powder Rheometer - a Universal Powder Flow Tester
The equipment is the most professionally designed and user friendly equipment we’ve used.
Process Diversity
The nature of all processing environments is such that a range of conditions in unavoidable and the powder being processed will be handled under different stress regimes. To fully predict the powder’s in-process performance, it is essential to measure and quantify how it responds to each of these external variables.
External Variable |
When and where |
Effect |
Consolidation |
- Vibration / Tapping
- Direct Pressure (hopper, IBC, keg)
|
- Increase in particle pressure, contact area and number of contact points
- Reduction in air content between particles
|
Aeration |
- Gravity discharge
- Blending
- Pneumatic conveying
- Aerosolisation
|
- Reduction in particle pressure contact area and number of contact points
- Increase in air content between particles (increased porosity)
|
Flow (shear) rate |
- Within powder
- Powder against equipment wall
- Mixing
|
- Mostly non-Newtonian
- Greater resistance to flow at lower flow rates
|
Moisture |
- Storage
- Processing
- Intentionally introduced (granulation)
|
- Increase particle adhesion
- Reduced particle stiffness - more compliant but increased contact surface area
- Increase electrical conductivity
|
Electrostatic charge |
- Discharge from hopper
- Pneumatic conveying
- High shear mixing
|
- Increase bond strength between particles
- Adhesion of powder to equipment
|
Storage time |
- Raw materials / Intermediates
|
- Consolidation
- Caking
- Permanently affecting downstream performance?
|
Proven Applications
The FT4 has application in all powder processing industries, including Pharmaceuticals, Fine Chemicals, Food, Cosmetics, Toners, Metals, Ceramics, Plastics, Powder Coatings, Cements and Additive Manufacturing. Applications extend to:
- Filling
- Tablet Compression
- Hopper flow
- Wet granulation end point and scale up
- Flow additive selection and optimisation
- Humidity effects
- Electrostatic charge
- Mixing / Blending
- Feeding
- Segregation
- Attrition
- Dry powder inhalers
- Caking
- Milling
- Conveying
- Wall friction and adhesion
- Hopper design
- Compact hardness and payoff
Download the Brochure for More Information
Shear Cell Testing using the FT4 Powder Rheometer