Users frequently question whether their measuring devices are functioning properly and within specified measurement accuracy. ABB’s new CoriolisMaster flowmeter models include technology for integrated online diagnosis and accuracy verification. This technology regularly monitors the oscillating meter tube within the flowmeter for coating and erosion deposits.
Self-monitoring technology prevents costly downtime required for proof testing and provides other major cost savings. It allows compliance with increasingly firm quality standards and legal requirements for verification of flowmeter accuracy.
Coriolis and VeriMass Technology
Besides measuring highly accurate mass fluid flowrates, the Coriolis technique also offers numerous other advantages. The Coriolis metering principle is independent of the fluid's density, conductivity and temperature, making it extremely flexible to use. It is also independent of the flow velocity profiles. So, it does not require downstream and upstream straight runs of piping. A measurement of fluid density within the tubes is provided by the flowmeter as a bonus. It also includes a temperature sensor in order to compensate for elasticity and dimensional changes of the tubes with fluid temperature. These flowmeters are capable of measuring nearly zero flow, where other measurement methods do work or result in significant measurement errors.
Self-monitoring capabilities majorly augment the above capabilities. The special metering tubes present within the CoriolisMaster flowmeter are mechanically balanced. Balancing the meter tubes minimizes the energy for their oscillation. The amount of energy needed is reflected in the electric current required to drive the tube oscillations. Each measuring device leaves the factory with minimized driver current consumption and extremely well-balanced meter tubes.
Any mechanical change of the meter tubes caused by deposit formation or erosion affects the balancing of the meter tubes. This results in higher driver currents to maintain the same level of oscillation. VeriMass technology is a basic principle that can be used to detect tube changes and can serve as in-situ verification of accuracy. Measured value errors are often caused by imbalances of the meter tubes. The detection of these factors plays a major role in Coriolis mass flow measurement technology.
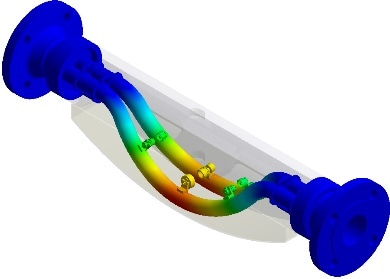
Fig. 1: Oscillating meter tubes inside a Coriolis flowmeter.
Learning the Baseline Driver Current
VeriMass uses this basic principle and monitors the driver current to identify possible changes of the meter tubes. The elimination of any short-term process effects is considered to be the major challenge for the use of this kind of verification. It is possible to accommodate these effects by a learning technique.
Users can document the initial baseline driver current after installation of a CoriolisMaster mass flowmeter. The user defines an initial calibration period, during which the measuring device “learns” the standard behavior of the flowmeter in the specific application. VeriMass technology monitors the driver current to establish its initial baseline, while eliminating any short-term effects. This self-calibration period adapts VeriMass to demanding processes such as liquid drops in gases, temporary gas phases in liquids or high viscosity liquids.
The initial calibration duration can be a few minutes up to several weeks. However, the self-calibration period rarely requires more than a few days following installation for the well-behaved processes. The tightness of the alarm threshold is set by the noisiness of the driver current signal during the self-calibration period. Smoother processes will be monitored with tighter alarm thresholds than noisier processes. This prevents possible false alarms.
The verification monitoring time is defined by the self-calibration period. VeriMass compares the newly detected current level to the initial baseline as the end of each monitoring period. Verification monitoring repeats automatically with no further interaction by the user. VeriMass sets off an alarm if a new current baseline exceeds user-defined tolerances. VeriMass technology works best for diagnosing errors caused by erosion and/or coating of the oscillating tubes. In the case of liquids, it suits processes with changing densities as well as those with only temporary gas bubbles and small viscosity changes.
VeriMass is capable of handling changes of different fluids with significantly different viscosities if the changes were present during the initial calibration period following installation. Liquids with erratic viscosities including changes of 50 mPas or more are not good application candidates. Additionally, VeriMass technology works well with gases having occasional liquid drops.
Operating VeriMass
VeriMass can be locally set up by navigating the menu on the LCD display of the CoriolisMaster flowmeter. Even more convenient, however, is setup using the CoriolisMaster Device Type Manager (DTM) or ABB’s new Field Information Manager using FDI packages. The DTM and FDI packages comprise of a rich and user-friendly graphical interface to make device configuration, diagnostics, maintenance and troubleshooting easy and fast. Users connect to the CoriolisMaster flowmeter via a host computer, HART commissioning device or directly to a PC.
VeriMass technology thus offers automatic testing/monitoring of the Coriolis meter tubes for possible deposit or erosion formation. ABB has produced and tested this innovative procedure to be a “user-friendly” method that will help detect the most frequent sources of errors in Coriolis flowmeters. A report generation function supplements the benefits. The procedure includes monitoring of all key measuring device parts that affect the accuracy of the measuring device.
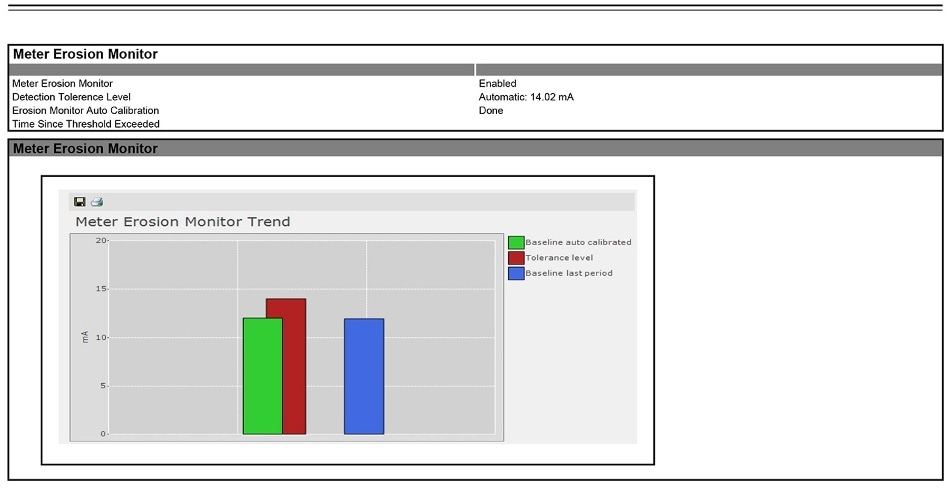
Fig. 2: Example CoriolisMaster Verification Report. Measurement device status summary would indicate GOOD.
All the interaction capabilities provided by the local display are offered by the CoriolisMaster flowmeter DTM. The DTM can also generate verification reports. The user will be able to enter date and identification details of the operator who checks the verification and generates two types of reports. A short report focuses on the erosion and coating monitor, including alarm history, event log and alarm status. The flowmeters parametrization is shown by the longer, more complete, report version. The VeriMass option is available for all FCB400 and FCB100, as well as FCH100 and FCH400 CoriolisMaster models.
Best practice suggests that it is essential to perform a retest of a Coriolis flowmeters calibration once a year. Factory calibration provides the greatest testing depth even though it is considered to be the most complex and expensive. In this case the user removes the flowmeter and sends it to the manufacturer for review and recalibration. Less costly on-site calibration with a reference device permits limited testing depth. Using the VeriMass diagnostic procedure together with onsite inspections, majorly simplifies and speeds calibration. It also makes possible testing depths of > 90 % at very little expense without the need for a so-called "proof test" recalibration either on site or at a test lab.
Other Considerations
The IEC 61508-2 and VDI / VDE2180 industry standards highlight that flexibility in determining calibration test intervals, including prolonging these intervals, is possible with the currently available diagnostic coverage and operating experience. NAMUR NE79 also mentions the desirability of extending intervals between test times through enhanced automatic diagnosis procedures with a wide degree of coverage. Conclusion: prolonging test intervals via internal self-monitoring and online diagnosis is allowed by the standards.
Self-monitoring flowmeters have a wide range of beneficial applications. Flowmeter usage for allocation or billing, such as for steam, water or gas lines, must ensure accurate measurements. This capability is also needed by applications subject to ISO 50001 Energy Management or ISO 9001 Quality Management. Additionally, self-monitoring can fulfill legal requirements, such as for Emissions Trading (TEHG) and for retesting protective devices in accordance with IEC 61508. All devices from the ABB CoriolisMaster family offer comprehensive internal self-monitoring functionality.
Self-monitoring offers numerous benefits besides these applications. The most obvious is effortless and quick testing on installed equipment – no process disruption, no device removal and no installation downtime. Yet users achieve a functional test from the sensed measured value through to the output signal with high testing depth. Users obtain regular verification of error-free operation with a clear pass/no-pass result. It is possible to prolong calibration intervals without additional accessories. This indeed results in increased productivity and installation efficiency.