A carbon fiber company in China was looking for an emission control system for a new pilot line at its specialty fiber products facility. This pilot line would comprise of furnaces and three ovens, which would produce Hydrogen Cyanide (HCN), Ammonia (NH3), and Carbon Monoxide (CO). The company finally opted for Anguil Asia because of its specific design for the application, as well as its local presence in the region.
Energy Analysis
When searching for an air pollution control partner, it was essential to find a vendor that not only had experience in this area but also a local presence. Fiber differs from one producer to another, and when selecting the emission control device, it's essential to consider the processing details that give each brand its signature characteristics. Anguil's Asia team demonstrated the expertise required to capture, control and to comply with hurdles that the processing plants face.
Prior to starting the project, the team at Anguil Asia performed a complete energy analysis at the facility which helped in ensuring that appropriate technology would be applied based on process parameters, efficiency needs, and destruction requirements. A Direct Fired Thermal Oxidizer (DFTO) and a Regenerative Thermal Oxidizer (RTO) were selected to process the furnace exhausts and the oven exhausts, respectively.
Multi-zone DFTO
.jpg)
Figure 1. Multi-zone DFTO
In order to treat the higher concentration exhaust stream emitting from the carbon fiber furnaces, a specialized multi-zone DFTO (Figure 1) was designed by Anguil, where the nitrogen compounds are removed at elevated temperatures in an oxygen depleted chamber. The remaining gases are quenched prior to moving into a secondary zone where overall emission destruction efficiencies are more than 99% with minimal production of NOX.
The furnace exhausts usually include tar that frequently cause plugging in a regular emission control device. In order to reduce these maintenance concerns and enhance reliability, special design considerations were undertaken. Anguil’s emission control system introduced furnace exhaust into the DFTO with a special inlet manifold, which prevents tar accumulation and plugging concerns. On most applications, airflow is forced through an RTO, however, this application was designed for an induced draft system for improved safety. This makes sure that all the Hydrogen Cyanide emissions will be drawn into the oxidizer for destruction, protecting the company's staff and the local area from a potentially dangerous situation.
Reducing Electrical Consumption
Since the three oxidation ovens at the customer's facility were electrically heated, it was important to reduce the electrical consumption in this project. As part of the energy analysis performed at this facility, it was proposed that the oxidation ovens would need a considerable amount of supplemental energy to sustain temperatures between 392°F and 572°F (200°C to 300°C). Since a significant amount of electrical power is used in the ovens, the customer wished to recover as much energy as possible from the oxidizer systems. Keeping this need in mind, Anguil recommended several secondary heat exchangers to provide the required preheated make-up air back to the ovens.
The DFTO would deplete at 1600°F (870°C), so Anguil integrated three shell and tube heat exchangers in series after the oxidizer. The two stainless steel heat exchangers would be supplying preheated makeup air back to Oven #2 and Oven #3. Subsequent to the first two heat exchangers, the process exhaust still included usable heat, and, hence, a third shell and tube heat exchanger was integrated to preheat the combustion air utilized in the DFTO. By preheating the DFTO combustion air, the destruction equipment becomes more energy efficient and reduces the quantity of supplemental natural gas required.
Regarding the energy recovery project, the shell and tube heat exchangers recover about 1.0 MMBTU/h (293kW/h) to be returned as preheated makeup air back to Oven #2 and Oven #3. The projected payback on the heat exchangers is within 3 months. On the other hand, the shell and tube heat exchanger to preheat combustion air to the DFTO will recover roughly 0.18 MMBTU/h (53kW/h), and the projected payback on the combustion-air heat exchanger is less than 7 months, assuming a natural gas cost of $10.00/MMBTU and a 24 hour/day operation.
Regenerative Thermal Oxidizer
Anguil used a Regenerative Thermal Oxidizer (RTO) to treat the higher flow, lower concentration exhaust from the ovens. This type of oxidizer has 98 to 99+% destruction efficiency with extremely low operating costs when compared to other emission abatement technologies available on the market. With thermal efficiencies of more than 96%, the RTO can operate with little to no supplemental fuel use.
During operation, the process gas first enters the RTO via an inlet manifold to poppet valves and then moves into energy recovery chambers where it is preheated. Both the process gas and contaminants are gradually heated in the ceramic media beds as they pass toward the combustion chamber. Following oxidization in the combustion chamber, the hot purified air generates thermal energy as it moves via the media bed in the outlet flow direction. Poppet valves change the airflow direction into the media beds to increase energy recovery in the oxidizer.
In order to provide the required preheated makeup air back to the ovens, a secondary plate-type heat exchanger was installed following the RTO. This heat exchanger recovers 70+% of the RTO exhaust energy. The preheated air is utilized instead of ambient air for the oven.
Conclusion
This project helped in reducing the overall emissions and operating costs for the carbon fiber company, along with a significant reduction in the total energy requirement. Thanks to the success of this project, an air pollution control system will also be installed on the customer's full scale production line.
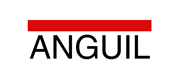
This information has been sourced, reviewed and adapted from materials provided by Anguil Environmental Systems.
For more information on this source, please visit Anguil Environmental Systems.