The bulk mechanical properties of virtually all materials used in engineering components and equipment are determined by how their texture and microstructure change during plastic deformation. SEM based in-situ compression or tensile testing helps in investigating the onset of plastic deformation and all intermediate deformation stages.
When this technique is combined with EBSD (electron backscatter diffraction), changes in microstructure and texture can be quantified. These quantitative results can be used to refine the plastic deformation theory, as well as to confirm the existing simulation models.
Due to technical challenges posed by drift, hardware design limitations, and acquisition time, the combination of these two techniques is not extensively used. High speed EBSD systems have solved the acquisition time issue - however, there are other issues remaining. These issues are discussed in this article.
Experimental Procedures and Results
These experiments were performed using a ZEISS SUPRA 55VP FE-SEM and a 10kN Kammrath & Weiss stage designed for in-situ tensile/compression tests, as shown in Figure 1. The stage was used at a 70° tilt for optimal EBSD signal.
.jpg)
Figure 1. Left – ARGUS™ FSE/BSE detectors and phosphor screen; Right top – tensile stage inside the SEM chamber as seen from the EBSD port; Right bottom – drawing of sample dimensions (values are given in mm).
The evolution of microstructure and texture was characterized by EBSD and orientation contrast imaging with the e–FlashHR+ high resolution EBSD detector and its integrated ARGUS™ FSE/BSE imaging system, featuring the unique capability of delivering color coded orientation contrast images.
Samples with dimensions specified in the drawing shown in Figure 1 were cut from annealed ARMCO steel with an average grain size of approximately 130µm, using spark erosion.
The minimum possible working distance for the sample was 27mm because of the relatively large size of the powerful in-situ tensile stage and the specific geometry required when performing EBSD analysis.
In order to compensate for the difference in height, the tilting capability of the e-Flash detector was used - the phosphor screen was moved downwards to follow the electron beam focus point as seen in Figure 2a and 2b. This helped in acquiring Kikuchi patterns in an optimum sample-detector geometry, resulting in a perfect signal distribution for both orientation mapping and orientation contrast imaging.
.jpg)
Figure 2. (a) Schematic view of the unique detector tilt feature and (b) the corresponding infrared (IR) chamber scope images showing the phosphor screen “following” the sample over a large domain of WDs. (c) IR chamber scope image showing the tensile stage / EBSD detector setup used during the experiments.
It is equally important to get the phosphor screen close enough to the sample for acquiring patterns with sufficient visible zone axes and good signal yield. This was done by safely inserting the phosphor screen in between the grip plates holding the sample as shown in Figure 2c.
Also the drift induced by the assembly weight or by the stage once deformation has started was manually corrected using the highly detailed orientation contrast images, also known as Fore Scattered Electron (FSE) images as shown in Figure 3.
.jpg)
Figure 3. Orientation contrast images showing microstructural evolution during in-situ tensile testing of ARMCO steel; initial microstructure (upper left) and after applying 120MPa (upper right), 180MPa (bottom left) and 210MPa (bottom right).
Four FSE images acquired in the same area at different stages of the tensile deformation process are shown in Figure 3. The images show the initial and final microstructure (210MPa), as well as two intermediate states, i.e. at 120MPa and 180MPa.
The FSE images are highly sensitive to small changes in the diffraction signal, thus allowing the user to observe the very beginning of the deformation process.
.jpg)
Figure 4. Grain Average Misorientation maps showing the “accumulation of deformation” inside the ARMCO steel grains at different stages of the in-situ tensile testing experiment; colors show orientation changes from 0 to 7 degrees.
Figure 4 presents the grain average misorientation maps of four datasets acquired at different stages of the tensile test experiment. The images show that the misorientation inside the grains increases with strain.
The high values of misorientations in the vicinity of grain boundaries (shown in black) confirm the migration of dislocations towards the grain boundaries, resulting in high dislocation density areas.
Conclusion
In-situ tensile and compression testing experiments combined with FSE imaging and EBSD analysis have been enabled by recent hardware and software advancements.
FSE imaging was used to identify the beginning of plastic deformation, while orientation maps were acquired to allow a proper quantification of the evolution of texture and microstructure during the different stages of the deformation process.
From the results it can be seen that the combination of in-situ tensile testing with EBSD and orientation contrast imaging can be successfully used to deepen one’s understanding of the complex phenomena that take place during all stages of plastic deformation in different types of materials.
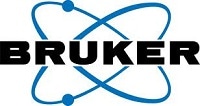
This information has been sourced, reviewed and adapted from materials provided by Bruker Nano Analytics.
For more information on this source, please visit Bruker Nano Analytics.