What typical problems do aluminum smelters face when producing seals for reduction cells?
The most persistent problem in sealing aluminum reduction cells is creating and maintaining a hermetic seal for the full service life of the reduction cell where the cathode bars penetrate the side wall of the reduction cells. If the hermetic seal fails right away due to spalling and cracking of hard refractory sealing materials, or over time with shrinkage and settling of ceramic fiber or mastic products due to chemical attack of the hydrofluoric acid atmosphere, an oxidation environment results which begins the gradual degradation of the reduction cells refractory and cathode lining. This situation results in reduced operational efficiency leading to the pre-mature removal of the reduction cell, and on occasion, will lead to a catastrophic failure of the reduction cell with full bleed out of the pot and the associated electrical damage and risks that are associated with such failures.
How do Mid-Mountain’s THERMOPAK® External Cathode Bar Seals help solve these issues for aluminum smelters?
Our THERMOPAK® External Cathode Bar Seal Boots are the first external seal designed to guard against the various and multiple points of attack which typically destroy all other sealing methods such as heat, abrasion, chemical attack, blind installation failures, expansion and contraction problems and leaking cells. Each THERMOPAK® External Cathode Bar Seal Boots require less than 5 minutes to install, and do not require steel back up plates or welding, making them quick and easy to install.
What materials are used in THERMOPAK® seals and what properties make them ideal for applications in aluminum smelting?
Mid-Mountain Materials, Inc. patented THERMOPAK® Cathode Bar Seal Boots are a four part composite design which work in harmony to guard against the multiple stresses on reduction cell seals. This allows the seals to perform well throughout the entire life of the reduction cell. Our proprietary ARMATEX® SBQF 100 component offers heat, chemical and abrasion resistance, and forms the semi-rigid frame of the seal. The ARMATEX® TAF 18 outer seal fabric component offers a hermetic seal, and resists chemical attack from the hydrofluoric acid atmosphere, while allowing the heat expansion movement of the cathode bar during initial startup of the reduction cell. The THERMOSEAL® 1000SF cement component allows complete lifetime bonding of the seal boot to the sidewall of the reduction cell, again tolerating the movement of the initial startup of the cell. The final component, the THERMOSEAL® M22 pumpable moldable fills the internal void of the seal boot, insuring the hermetic seal of each THERMOPAK® Cathode Bar Seal Boot while adding critical insulation at all cathode bar penetration points.
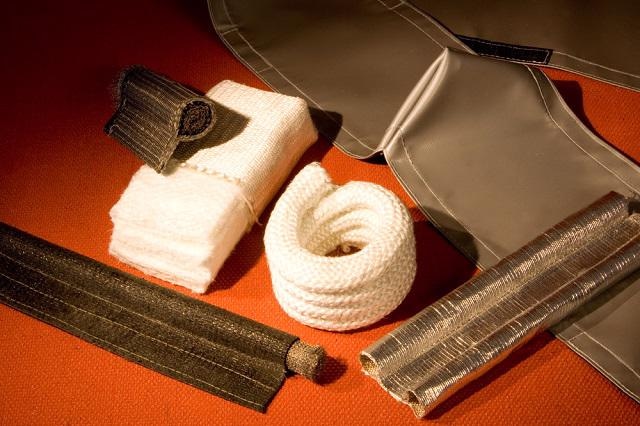
Image Credit: Mid-Mountain Materials, Inc.
As well as seals, the THERMOPAK® range includes Tray Pads which help reduce scrap in aluminum rolling mills. Can you explain how this is achieved?
Our THERMOPAK® Tray Pads are high temperature, high durability pads used to protect aluminum coils, slabs and plate from damage by direct contact with steel transport trays, V-racks, sling trays and rail cars during annealing, transport, cooling and storage of the aluminum. Movement of the aluminum on these steel surfaces, especially the hot aluminum, results in contact surface abrasions and denting commonly referred to as “bruising”, resulting in significantly increased scrap aluminum. Use of our tray pads eliminates most of these problems and reduces scrap generated by in-house handling methods of the aluminum.
How is the effectiveness of Tray Pads assessed?
The effectiveness of our tray pads is measured by direct comparison of scrap generated on bare trays versus padded trays. Our tray pads have been the focus of multiple Kaizen events focused on determining their effectiveness at reducing in house scrap generated from contact surface abrasions and denting or “bruising” of the aluminum. It has been determined through Kaizen analysis of padded versus non-padded trays that aluminum scrap is reduced by over 60% on padded trays versus non-padded trays resulting in significant cost savings as well as increased production for our tray pad customers.
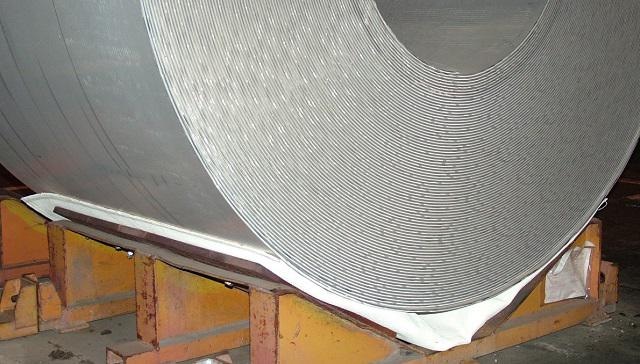
Image Credit: Mid-Mountain Materials, Inc.
What types of Tray Pads can Mid-Mountain supply?
Mid-Mountain currently supplies four standard styles of tray pads depending on the type of usage and temperature requirements of our customers. Our ARMATEX® QF40 Clear style tray pad is our most durable rated for 1000 F. Our FIRESTAR® 35 style is our most economical tray pad for use to 1000° F. Our HYTEX® 1400 style tray pad is rated for 1400° F and is frequently used in higher temperature environments such as the annealing furnaces. Our HYTEX® 700 style tray pad is the most durable of all these styles used for aluminum at lower temperatures of 450° F. or less.
Can these products be customized?
Yes, Mid-Mountain has multiple fabricating and manufacturing locations and we specialize in customizing solutions for our customers so we can build what is exactly right for your plant and your need.
How will the THERMOPAK® range develop in the future?
The THERMOPAK® range of products at Mid-Mountain Materials Inc. refers to our custom fabricated products to meet specific customer needs such as those we have discussed here. We see many additional areas to custom design products for the aluminum industry such as the wide range of Crucible Lid Seal Gaskets we already manufacture, die cut seals such as crucible spout seals and spout attachment seals, and our ever growing range of anode bar seals in reduction cells. Our philosophy is if you can find a need, we can build you a solution, so it is hard to say exactly what direction that might take us!
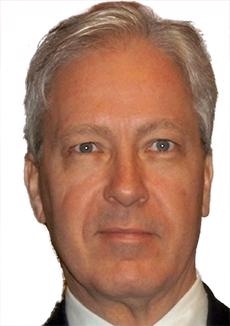
About Tony Carroll
Tony Carroll is in charge of Aluminum Industry Sales and Product Development at Mid-Mountain Materials Inc.
Tony began working in the field of supplying high temperature materials to the aluminum industry 36 years ago in a position of engineering sales and product design.
In 1986, Tony founded the former Evansville Refractory and Insulation Supply Company Inc. which was a worldwide supplier to the aluminum industry into the 1990’s before being purchased by a multi-National firm.
With multiple patents in multiple countries Tony has worked with plant engineers and operators in over 35 countries, developing unique solutions to a wide variety of challenges facing aluminum producers.
Disclaimer: The views expressed here are those of the interviewee and do not necessarily represent the views of AZoM.com Limited (T/A) AZoNetwork, the owner and operator of this website. This disclaimer forms part of the Terms and Conditions of use of this website.