In the recent years, the Helmholtz-Zentrum Berlin für Materialien und Energie GmbH (HZB, previously known as Hahn-Meitner Institute, HMI), Berlin, Germany, has developed a particular technique of cross-sectional specimen preparation for transmission electron microscopy (TEM), mainly suitable for thin film stacks of solar-cell devices.
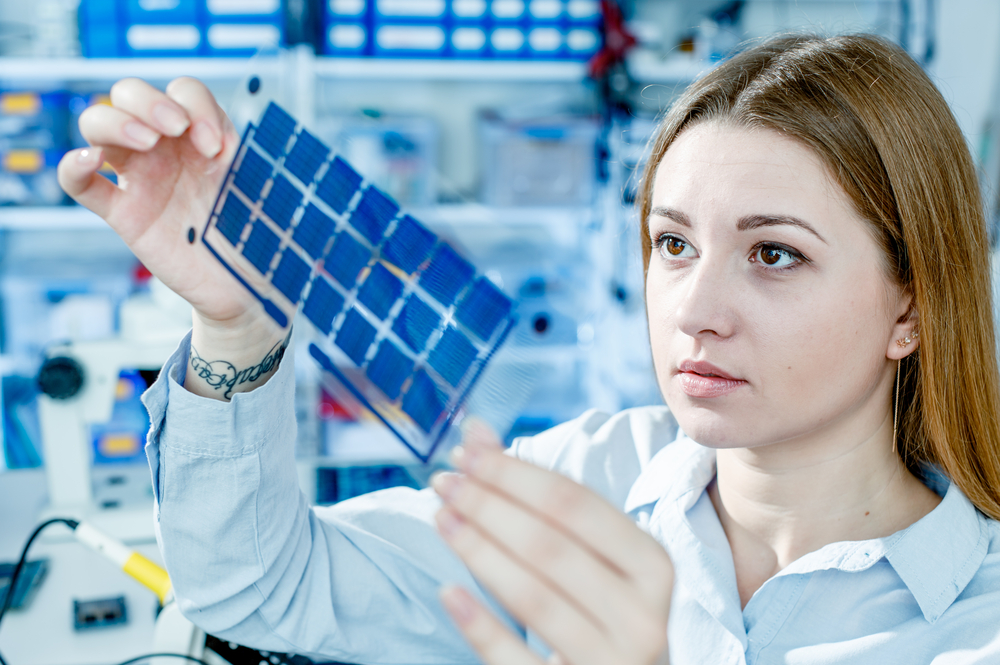
Image Credit: Shutterstock/luchschenF
This approach involved mechanical and argon (Ar) ion polishing of cross-section specimens, developed by face-to-face gluing of two thin film stacks using epoxy glue.
A significant utility for the mechanical polishing of cross-section specimens is the T-Tool introduced by H. Zang in 19981, which is similar to the more familiar Tripod2. The T-Tool has been further developed by Peter Schubert-Bischoff at HMI/HZB, currently adapted and applied by various laboratories across the globe. Figure 1a depicts a photograph of the T-Tool (HMI style) with a glass cylinder attached to it.
Mechanical Polishing Procedure
The mechanical polishing procedure involves lapping the cross-section specimen on diamond foils at various sizes of the diamond particles, gluing of a stabilizing metal ring on top of the polished specimen, as well as placing carbon fibers across the interface region of the cross-section, as shown in Figure 1b.
.jpg)
Figure 1. a) Photography of the T-Tool developed at HMI/HZB, with a glass cylinder attached to it, on top of which the specimen is clued by use of hot wax. b) Light micrograph of the inner part of a Mo support ring, showing the interface region (black vertical line in the middle of the image) with the glass substrates of the thin-film stacks on either side, as well as carbon fibers glued across the interface region of the cross-section.
These carbon fibers show a specific role during the Ar ion milling step of the preparation procedure, serving as screens for the ion beams. As a result, regions in between the carbon fibers are milled more preferentially, which leads to several positions at which the specimen becomes transparent to the electron beam (see positions highlighted by red ellipses in Figure 2a).
In addition, the specimen may be Ar ion polished several times, thus maximizing the number of positions for each specimen at which TEM analyzes may be performed.
However, it is often a prerequisite for a TEM study to examine a particular position in a material. The X,Y stage of the PIPS II system allows alignment of the Ar beams to region of interest on the sample. Therefore, it is possible to mill individual regions in between the carbon fibers (see Figure 2b).
.jpg)
Figure 2. a) Photography of a cross-section specimen after ion milling using a broad Ar ion beam, resulting in several holes in between the carbon fibers. b) The PIPS II system permits alignment of the Ar beams in such a way that holes form only within a small region of interest.
The enhanced specimen preparation approach described above was used to prepare cross-section specimens of a ZnO/CdS/Cu(In,Ga)Se2 /Mo glass thin film solar cell. This material system needs a high standard of specimen preparation, with regard to the mechanically instable interface between Mo and Cu(In,Ga)Se2, and also since ion milling of Cu(In,Ga)Se2 is incongruent, resulting in the formation of Cu agglomerates (highlighted by red circles in Figure 3a) on the surface of the specimen3.
These agglomerates can be significantly reduced by applying liquid N2 during the Ar ion milling in the PIPS II system (Figure 3b). A temperature of -40 °C was adjusted.
.jpg)
Figure 3. a) Bright-field TEM image of a ZnO/CdS/Cu(In,Ga)Se2/Mo solar-cell stack. Cu agglomerates on the Cu(In,Ga)Se2 surface are highlighted by red circles. b) No Cu agglomerates visible on a specimen prepared using optimized Ar ion beam parameters and liquid N2 cooling in the PIPS II system.
Within the ZnO/CdS/Cu(In,Ga)Se2 /Mo solar-cell stack prepared by use of optimized parameter settings, structural properties of the individual layers and their interfaces can be analyzed at high resolution (Figure 4).
.jpg)
Figure 4. Bright-field (a) and high-resolution TEM image (b) of the ZnO/CdS/Cu(In,Ga)Se2 stack prepared using liquid N2 cooling in the PIPS II system during Ar ion milling. Structural properties such as extended defects and orientation relationships between the CdS and Cu(In,Ga)Se2 layers can be analyzed at the sub-nanometer scale.
Acknowledgements:
We would like to thank Dr. T. Rissom, HZB, for providing the solar cell.
References
1. H. Zang, Thin Solid Films 320 (1998) 77-85.
2. J. B. Benedict, R. Anderson, S. J, Klepeis, M. Chaker, Specimen Preparation for TEM of Materials II, Mat. Res. Soc. Symp. Proc. 199 (1990) 189-204; J. B. Benedict, R. Anderson, S. J. Klepeis, Specimen Preparation for TEM of Materials III, Mat. Res. Soc. Symp. Proc. 254 (1991) 121-140.
3. D. Abou-Ras, B. Marsen, T. Rissom, F. Frost, H. Schulz, F. Bauer, V. Efimova, V. Hoffmann, A. Eicke, Micron 43 (2012) 470-474
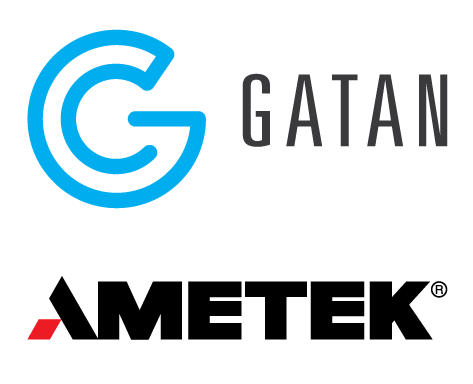
This information has been sourced, reviewed and adapted from materials provided by Gatan Inc.
For more information on this source, please visit Gatan Inc.