Aluminum (Al) is an abundant element, which constitutes up to 8% of the earth’s crust and appears ubiquitously in the supply chain of consumable goods. It is estimated that Europeans approximately consume 3–10 mg of aluminum from natural food sources every day.
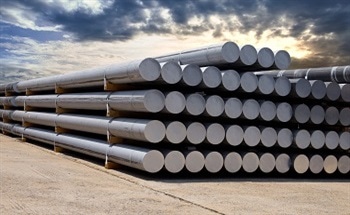
There are only less negative effects associated with aluminum exposure, whereas the positives of utilizing this naturally occurring metal are numerous. Owing to its excellent corrosion-resistant properties and incredible low density, it has been used in production at every level of human manufacturing, from food storage to aerospace development.
Every year, millions of tons of aluminum are processed, offering hundreds of thousands of jobs across the world. However, in spite of the relative benignity of the material, there are challenges related to aluminum handling and processing, which demand advanced material solutions.
Environmental Impact of Alumina Extraction
The main challenge faced by the aluminum industry is primary aluminum production, which involves the extraction of alumina (Al2O3) from bauxite ore in a chemical digestion process. The effluent material, or “red mud”, is an insoluble waste product with few well-known applications. This poses major storage difficulties, with various refineries turning to lagooning, marine dumping, or dry-stacking for the disposal of their bauxite waste.
However, the industry has made intensive efforts to enhance the sustainability of aluminum production and to minimize the carbon footprint of aluminum manufacturing. Advanced aluminum handling techniques and equipment have improved the potential of both primary and secondary, or recycled, aluminum processes which are almost 92% more energy efficient than traditional production methods.
Difficulties for Aluminum Handling Equipment
Both primary and secondary aluminum handling need extremely durable materials with high thermal- and corrosion-resistant properties. Molten aluminum is smelted at temperatures of up to 1796 °F (980 °C), and can chemically corrode materials through wetting or thermal spalling. This can decrease the service lives of refractory components like heater tubes and thermocouples, leading to major maintenance costs.
Molten aluminum handling is normally done using advanced sialon ceramics, which are specifically resistant to molten aluminum corrosion and wetting. These excellent mechanical properties are associated with high toughness and strength, and outstanding degrees of formability, enabling them to be molded into a variety of component shapes.
Sialon ceramics are usually formed into aluminum handling components, including level sensors, thermocouple sheaths, as well as riser and heater tubes. These are extraordinarily low maintenance parts, allowing improved industrial throughput and decreased mechanical downtime.
Aluminum Handling Equipment from International Syalons
International Syalons are principal suppliers of advanced sialon ceramic components for several applications, offering solutions for aluminum handling and processing applications. The Syalon 101 material from the company is optimized for non-ferrous metal forming procedures and is rapidly becoming the industry standard material for aluminum handling.
The Use of Sialon in the Aluminum Industry
The second-most industrially consumed metal globally is aluminum (Al). The global aluminum market produces more than 50 million tons of aluminum annually, mainly through the refinement of bauxite ore at sites at Russia, China, North America, and many other countries. At these sites, industrially viable alumina (Al2O3) is refined from bauxite through the Bayer process, which involves crushing and heating the metal with a sodium hydroxide solution in a pressure vessel at temperatures of up to 200 °C. The extracted alumina is then smelted at refractory temperatures of up to 980 °C in molten cryolite (Na3AlF6), to form pure aluminum for application in a wide range of industrial and commercial sectors.
The extreme requirements of aluminum production need high-thermal, durable materials with low aluminum penetration and excellent corrosion resistance. Refractory components like thermocouple protection sheaths, heater tubes and extrusion die casts must thus perform efficiently and consistently to maintain optimal production levels in an industry with such a huge global demand.
Advanced silicon nitrides (Si3N4), called sialons (Si-Al-O-N), are perfectly equipped to deal with such rigorous specifications. These refractory ceramics can be manufactured in a variety of shapes which show retention of strength up to 1450 °C, with a very low wettability to molten aluminum and outstanding thermal shock resistance ensuring a long service life of sialon in the aluminum industry.
SiAlON for Molten Aluminum Handling
International Syalons manufactures three primary sialon components for molten metal handling, which are pervasively used in the aluminum industry:
- Level sensors: Employed in the extrusion die casting of molten metals, including aluminum, into ingots or their final fit-for-purpose shapes. Temperature applications of sialon level sensors range up to 800 °C, thereby enabling accurate monitoring of molten aluminum in pressurized cavities.
- Riser and heater tubes: High-strength sialon ceramic cylindrical heaters for heating the melt in aluminum processing. These can be developed to a variety of dimensions.
- Thermocouple protection sheaths: Advanced ceramic tubes that can reliably and minutely monitor the temperature of aluminum foundries, with a selection of Syalon materials providing extraordinary physical properties at temperatures up to 1200 °C, and 1400 °C.
The repeated, durable use of sialon components for aluminum production is influential in recycling processes. Aluminum features excellent corrosion resistance, enabling technically infinite recycling properties. Recycled aluminum is usually smelted into ingots, according to the ordinary aluminum refractory process. These are then compounded into foundry alloys and shaped to a range of potential purposes using extrusion die equipment.
.jpg)
Cross-section of Syalon 101 thermocouple sheath after use in aluminum production, showing zero porosity or ingress of molten metal into ceramic
Sialon for Aluminum Forming Applications
The high durability and cost-efficiency of International Syalons’ materials provide amazing benefits beyond the smelting, refining, and handling of molten aluminum. With high thermal properties and excellent chemical stability, sialon ceramics are also helpful in the welding and shaping of aluminum alloys. The company manufactures a range of Syalon materials appropriate for such purposes, with products including:
- Welding jigs and fixtures: Used in orbital welding methods to fuse curved components to one another; generally employed in the aerospace industry for the production of aircraft fuselages.
- Weld location pins: Used in the welding of cage nuts for automotive assembly lines, with greatly enhanced efficiency over previously used steel nuts for vehicle operations.
International Syalons’ Materials for the Aluminum Industry
International Syalons has decades of experience in the development and manufacture of advanced sialon ceramics for application in refractory industries, including the aluminum industry. These materials have exhibited enhanced mechanical properties over conventional materials used in industrial environments, with a selection of advanced silicon nitride grades with differing chemical properties.
Syalon 101 is the inclusive option, with 0% porosity, and hence ultra-low aluminum penetration, together with high-strength properties and excellent levels of toughness. This outstanding refractory ceramic can be employed to produce hard-wearing heater and riser tubes, extrusion die equipment, and outstanding thermocouple protection sheaths.
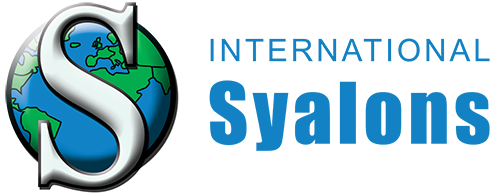
This information has been sourced, reviewed and adapted from materials provided by International Syalons.
For more information on this source, please visit International Syalons.