Jun 8 2009
Some motorbike riders found a custom fitted sat to be a desirable innovation. A survey done through the web site of a partner in the project, motorbike manufacturer, showed interest from the motorbike riders community.
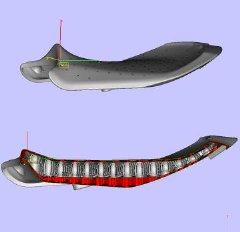
But, how does it work?
In general Custom-Fit technology follows this format: individual characteristics of the consumer, both geometrical and non geometrical, are captured using different scanning technologies, then this data is used to adapt product shape\characteristics using special CAD (Computer Aided Design) and finally products are made with Rapid Manufacturing technologies, the so called additive techniques which print in layers, moving seamlessly from plastics to metals, to give differing stiffness and flexibility, as required.
In the specific case of the motorbike seat the process starts by getting the 'pressure map' of the rider sitting on the motorbike. On this basis a 'comfort map' is defined, which identifies the zones in the seat which are mainly responsible for rider discomfort. This part of the process has been defined by the project partner, IBV institute of Valencia.
The idea is to customise the stiffness of the padding in relation to the different discomfort zones. These are identified on the seat design by superimposing the comfort map on to the seat design itself.
And now the big challenge: how to produce a one-piece part with different stiffness in different zones? This is not possible with traditional processes, but feasible with Rapid Manufacturing technologies. In fact, building layer by layer makes it possible to print parts with an inner graded structure. This feature allows us to design an inner structure made up of small 'barrel like' elements that act like small springs, with different stiffness in relation to their size. So, to customise the padding stiffness it was sufficient to design the inner 'barrel structure' with different sizes in relation to the stiffness required in the different zones (see figure).
This solution has been developed by the project partners DeMonfort University and Delcam plc. The concept is completely new and really opens the possibilities to offer a personalised option to motorbike riders.
The three customised paddings were Laser Sintered, assembled into the seat, and tested on motorbikes. Static and dynamic tests showed a good response from riders: the overall comfort felt by all the three riders had a better score with respect to standard seats and the customised ones gave better feelings in terms of control and stability for rider position.
Delivery time and cost figures still need improvements. That seems however to open some interesting opportunities for a customised version of the seat with a bearable impact on the normal process flow of a motorbike seat production.