Today, after decades of experience, the plastics industry has gained extensive knowledge of the mechanical and chemical characteristics of the material. Long-term cyclical loading, however, is an area that has barely been researched at all. The question of how long the engine mount, the intake manifold or the oil filter can withstand a pulsating compressive load in the presence of oil under changing temperatures can hardly be answered, because systematic investigations are lacking.
A universal test specimen whose behavior can be predicted virtually and verified experimentally is one prerequisite for gaining this knowledge about fatigue strength and durability.
Such a test specimen and the know-how obtained from it are essential especially when developing components for safety-related applications that are characterized by high loads. It is for this reason that BASF presented such a test specimen a little less than one year ago. Ultramid A3WG7 CR, a glass fiber-reinforced member of the PA 66 family that has been optimized specifically for high and long-term loads was found to be one suitable material for this purpose.
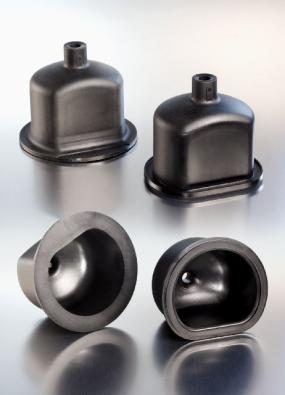
The open body with the designation ULTRASIM Fatigue Tester (UFT) was designed specifically for cyclical internal compressive loads and must satisfy many requirements: It has a minimum volume, withstands cyclical loads of maximum 30 bar, exhibits defined failure modes at defined locations and has a typical fiber distribution/ orientation at these predetermined weak spots.
To permit systematic investigation of weld joint behavior in particular, BASF is now introducing a second test specimen for fatigue tests, the ULTRASIM Weld Tester (UWT). It employs a special Ultramid (PA) that is preferred for use in welded components. As in the first specimen, one of the CR grades intended for high-load applications that can be described using BASF's ULTRASIM simulation tool may also be employed here.
Producing a new type of weld test specimen
The new ULTRASIM Weld Tester has a different geometry than its slightly older relative, the Fatigue Tester, since two test specimens are joined together for a weld test. For instance, there is a flange around the opening of the body, which is a typical weld geometry. The injection mold for the weld test specimen has a number of different inserts, so that not only two different flange thicknesses but also three test specimen sizes can be produced and combined.
With this toolbox, it is now possible to conduct systematic short- and long-term (fatigue) tests of the integrity and durability of welds under various conditions. One of the variables to be considered is the direction of motion during vibration welding, as are the joining pressure and amplitude employed during the welding operation. Glass fiber content and orientation at the weld joint may also be important, along with all of the variables that are already known from the ULTRASIM Fatigue Tester to have an effect on the ability to withstand loads: temperature, moisture level, stress concentration and type of load. One thing is known for sure: the bursting strength does not depend directly on the strength of the material. Geometry and processing of the component - namely, also the weld - have a significant effect as well.
Two-step testing process
An initial series of investigation is intended to establish the basic effect of welding parameters on the integrity of the specimen. This yields a set of optimal welding parameters. Using this knowledge, optimally welded test specimens can then be produced.
In a second step, the component experts investigate the fatigue strength, that is, the durability of the weld joints in the test specimen. Only then can reliable statements be made about the life expectancy of the weld, i.e. its fatigue behavior.
Both of these steps represent new territory for BASF and its concept: in the past, welding parameters were established only with the aid of plastic plaques produced specifically for this purpose. Using the ULTRASIM Weld Tester, it is now possible to use close to real-world welded test specimens instead. Initial results have already demonstrated that strength values differ from those found with simple plaques. While tensile and flexural properties can be measured only separately on welded test plaques, tensile and bending moments that occur simultaneously under internal pressure on the welded component can be investigated at the same time. Further, the ratio of tensile and flexural loads can be varied through use of different component sizes.
Most of the welded bodies on the market are symmetrical in shape, so that there is a priori no single particular weak spot. The UWT from BASF has been designed intentionally to be asymmetric and has one predefined weak spot. This characteristic is very important, as in this way it is possible to make use of the high predictability provided by the ULTRASIM computer program when laying out welds. Furthermore, the flexibility of the mold allows test specimens of different sizes to be welded together, so that close to real-world, namely, asymmetric, components can be produced. As a result, complex load profiles with a complicated interplay of tensile and flexural loads can be generated and investigated. With this capability, the conditions in real components can be approximated very closely.
More basic knowledge when working with customers
At present, the UWT is being used to develop systematic knowledge that is intended to bear fruit in projects with customers. The closer the weld tester can approach the planned component in terms of location of the weld joint, joining geometry, and welding parameters, the more reliably the BASF experts can predict the life expectancy of the customer's part. This requires a test specimen in which various (failure) modes can be created reproducibly - and with the aid of ULTRASIM - be understood. The knowledge gained benefits both sides, since a well-understood test specimen can be rapidly adapted to customer-specific parameter sets.
It is also possible in such a variable weld test specimen system to take into consideration the loads associated with different fluids specified by the customer. Exposure to fluid on one or both sides, thermal stresses and pressure loads can all be investigated simultaneously. The ability to conduct fluid investigations in conjunction with welds in this systematic manner is to date unique in the market. The material knowledge gained in this way is a long way from that provided by the classic test bar.
Plastic parts with longer service life
Images of fatigue phenomena are known from metallurgy: the so-called Wöhler curves plot the stress at break - a measure for strength - against the number of load cycles achieved. Wöhler curves for plastics are encountered only rarely in the literature. For engineering plastics subjected to high loads, there are hardly any systematic investigations of close to real-world components. The objective of the extensive studies being conducted with the ULTRASIM Weld Tester at BASF is to obtain Wöhler curves for welded plastic components that reproduce the effects of temperature, various fluids and pulsating pressures.
By combining investigations of weld joints and fatigue strength, BASF is pursuing a new dimension. Thanks to its very exactly defined form and flexibility, the patented, extremely variable test specimen for fatigue testing of weld joints represented by the ULTRASIM Weld Tester provides the opportunity to increase the knowledge concerning plastic parts enormously.
This knowledge will naturally be employed when parts like engine or transmission mounts are being developed, where continuous and high dynamic load is a main topic. Since this kind of safety-relevant components can only be manufactured from plastic specialties, the application of the new know-how will be concentrated on specific material groups. These skills will soon help customers to design components with a long service life.