The applications of advanced technical ceramics have multiplied manifold in the modern age. They are used for a wide array of tools and devices, ranging from sharp-edged tools to implants, and this suitability is largely due to their mechanical toughness. This varies, however, with the process through which the part is manufactured, and so each device should have its mechanical strength assessed by direct measurement of the part just as it comes from the factory. This is made possible by instrumented indentation which measures Young’s modulus as well as hardness without the need for any sort of residual impression imaging.
Instrumented indentation or nanoindentation is an advance on the standard tests of hardness, which include Brinell, Vickers, Rockwell and Knoop tests. Here a diamond (or less commonly another hard indenter) is pushed against the material to be evaluated, and the force and penetration due to this contact are continuously measured for the complete duration of application and removal of this force. This is thus superior to traditional methods in which only one parameter is evaluated, namely, the measure of deformation at a single force application. It has been recognized as standard under ISO and ASTM criteria. By this test, hardness (H) is the applied force divided by the projected area of contact, and is given in GPa units, but convertible to Vickers hardness also (HVc). The measurement of recovered displacement during the reduction of indentation force can also be used to find the local Young’s modulus (E) of the test material.
Two examples of this technique are described here, the first being on toughened zirconia called CoorsTek TTZ. Its grain size is about 40 µm and there is an intergranular phase (Figure 1). The grains are of cubic zirconia (ZrO2) stabilized in cubic lattice form by MgO substitutions, with intergranular silica mixed with some degree of impurity, due to the presence of this material in the substrate. The second test was carried out on single-crystal alumina (Al2O3).
The modus operandi is as follows: measurement of Young’s modulus, hardness and Vickers hardness using standard techniques, on both materials, and comparison of test results with the published results for these ceramic materials. This is followed by the use of NanoBlitz 3D, which is an indentation test method produced by Nanomechanics, to generate a surface map of CoorsTek TTZ within a second.
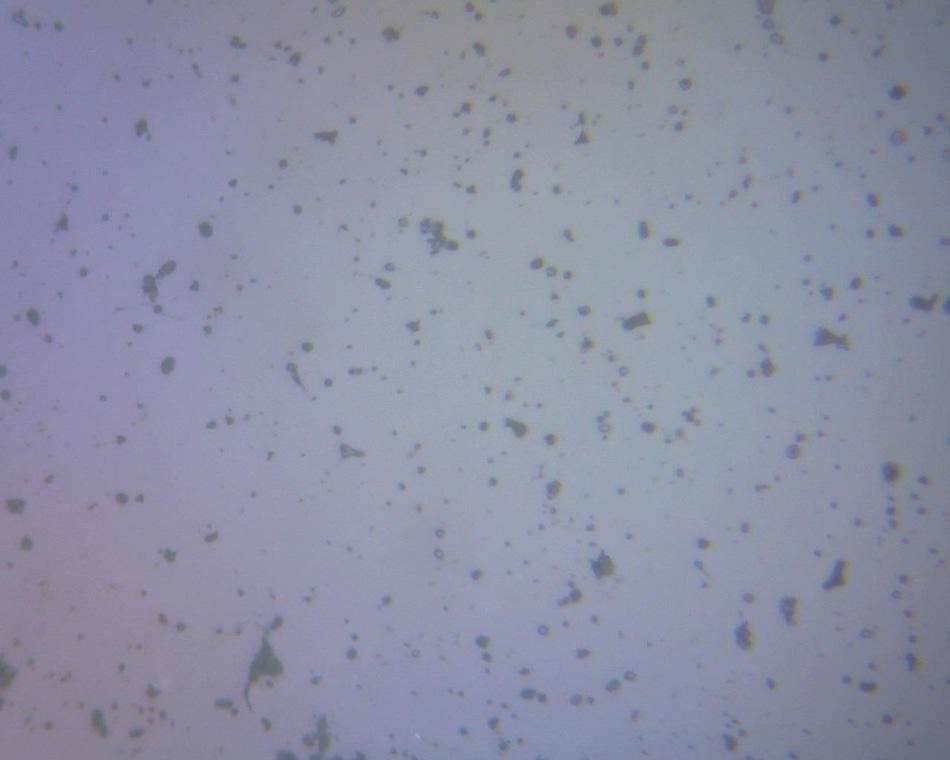
Figure 1. CoorsTek TTZ zirconia surface as prepared for instrumented indentation. Light phase is cubic zirconia; dark phase is inter-granular silica.
Materials and methods
A disk of alumina 2 cm in diameter was used as the test sample. The flat faces of the disc were polished to be optically normal to the c-axis of the crystal lattice, and the test was carried out on one face in the same direction as the c-axis. The TTZ sample was also a disc of about 2 cm diameter and 1 cm thickness, but it had to be polished after purchase to make it suitable for the instrumented indentation test. This was done using rough grinding with water and silicon carbide (beginning from 220 grit through 600 grit). The top surface which was to be used for the test was further polished with a medium nap cloth of 6 µm and 1 µm diamond using an extender with an alcohol base. The final polish was applied with two cloths, one with low nap and 0.05 µm colloidal silica, and a vibratory polisher which used 0.06 µm colloidal silica on medium nap cloth.
With the iNano from Nanomechanics, 20 indentations were made 40 µm apart on each sample of ceramic in accordance with ISO 14577 standards for instrumented indentation. The peak force on the CoorsTek TTZ and alumina samples was 25mN and 50 mN respectively. After a 20 second loading period, a dwell time of 2 seconds and an unloading rate identical to the loading rate, an 80 second period of constant force application was used towards the termination of unloading. This was to compensate for thermal drift (sample contraction and expansion with heat) and thus obtain more accurate measures of displacement. The total test time was about 2 minutes.
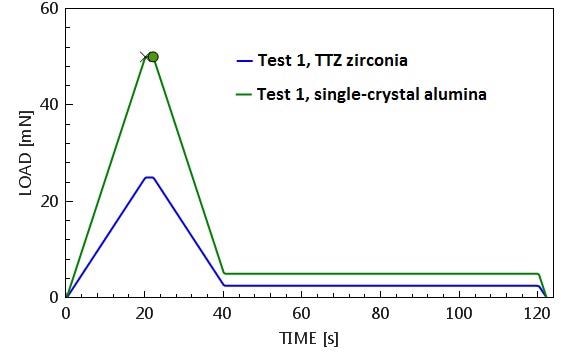
Figure 2. Load-time prescription for standardized indentations into TTZ zirconia (blue) and alumina (green).
The third step used NanoBlitz 3D from Nanomechanics to map the surface of a square area on the CoorsTek TTZ, measuring 100 µm by 100 µm. This included grains and intergranular space. A set of 50 by 50 indentations was set to obtain 2500 indentations in all, using 20mN peak force at each spot. The test was completed in about 30 minutes.
Results and discussion
As seen in Figure 3, the load-displacement curves for each sample measured in conformity with ISO 14577 norms were used to calculate the fundamental mechanical properties of Young’s modulus, hardness and Vickers hardness as seen in Table 1.
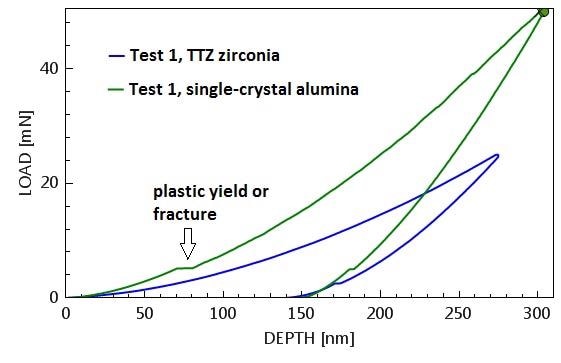
Figure 3. Load-displacement curves for two standardized indentations into TTZ zirconia (blue) and alumina (green).
Table 1. Summary of measured and reference properties.
Measured by instrumented indentation (ISO 14577) N = 20 |
Reference values |
Material |
Force (mN) |
E (GPa) |
H (GPa) |
HVc (kg/mm2) |
E (GPa) |
Microhardness (kg/mm2) |
Poisson’s Ratio |
Alumina (c-axis) |
50 |
435±14 |
29.9±1.15 |
2820±100 |
499§ [5] |
2200 (HV) [6] |
0.23 [5] |
CoorsTek TTZ |
25 |
249±9.7 |
17.0±0.69 |
1600±65 |
200 [1] |
1200 (HK 1kg) [1] |
0.3 [1] |
§499 GPa is for the c-axis direction; E = 403 GPa perpendicular to the c-axis [5].
Figure 4 displays the results of the NanoBlitz test on CoorsTek TTZ, with the derived Young’s modulus and hardness.
Young’s modulus for alumina was measured at 435 GPa along the c-axis in contrast to the reference value which is 499 GPa. This must not be taken as an inaccuracy because the E value in the a-b direction is only 403 GPa, since the material is very anisotropic and because indentation in any axis will depend also upon the elasticity in the other axis. The measured value will therefore fall between the values for each axis. The most influential paper on instrumented indentation by Oliver and Pharr give 441 GPa as the c-axis value for alumina.
When CoorsTek TTZ values are considered, the E value is higher than normally reported on bulk testing, and the researchers state that the reason is the small scale of the test. The indentations were made solely in the granular phase and the value obtained is that of this phase alone (cubic zirconia), in contrast to the bulk modulus value which reflects those of both the granular and intergranular phases and is therefore smaller.
Vickers hardness measurements were significantly higher than reference values for alumina and zirconia microhardness. It is necessary to remember the possibility of plastic deformation due to the initiation and spread of dislocation, which occurs in crystals. This is influenced by the scale on which the material is tested. The tinier the indentation, the smaller the included test volume, and the more variable is the chance of dislocation being present. The less the volume tested, the stronger the crystal appears to be, therefore – the “indentation size effect”. It is the opinion of the researchers that the discrepancy in measurement of HVc is due solely to the small scale, at which microhardness cannot be measured using conventional methods. This fineness of measurement is itself an advance of instrumented indentation.
The mapping of Young’s modulus and hardness (in Figure 4) also supply a wealth of information into the structure of CoorsTek TTZ at microscopic level, showing the intergranular phase to resemble low-grade silica in its mechanical strength with a Young’s modulus of about 70 GPa and hardness of about 5 GPa. This method of testing thus helps to look into the properties of this ceramic and to predict its mechanical behavior with better accuracy than bulk testing of its tension, microhardness and compression.
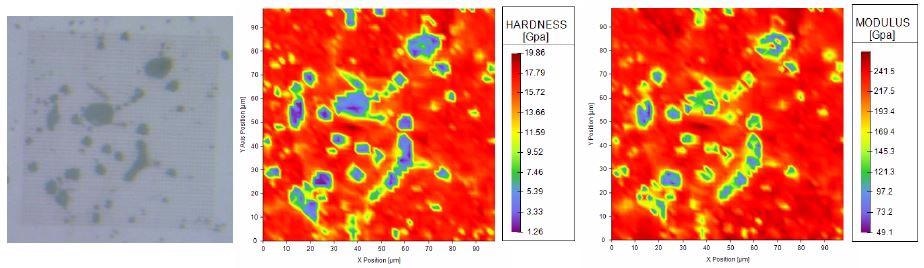
Figure 4. For CoorsTek TTZ, surface maps of hardness (top) and Young’s modulus (bottom. The center image shows the indentation array (50 x 50) used to generate the mechanical-properties maps.
Conclusion
To sum up, the technique of nanoindentation is valuable in micro-level testing of mechanical properties such as Young’s modulus and hardness because of the close relationship between the microstructure and the volume of the material. This is important because the microstructure is fundamental to the mechanical behavior of the material, as proved by this work. At lower scales, deformation strength increases. When the CoorsTek TTZ alone is considered, the bulk Young’s modulus is clearly seen to arise from the properties of not only the crystalline cubic zirconia phase but also the amorphous intergranular phase.
Acknowledgment
Nanomechanics, Inc. gratefully acknowledges insight into TTZ microstructure provided by David Johanns.
References and Further Reading
- “TTZ Zirconia Material Properties,” URL: https://www.coorstek.com/en/materials/zirconia/ last accessed 2016-03-21.
- ‘‘Metallic Materials–Instrumented Indentation Test for Hardness and Materials Parameters,’’ ISO 14577, International Organization for Standardization, Geneva, Switzerland (2002).
- ‘‘Standard Practice for Instrumented Indentation Testing,’’ E2546–07, ASTM International, West Conshohocken, PA (2007).
- Simmons G. and Wang H., Single Crystal Elastic Constants and Calculated Aggregate Properties: A Handbook, 2nd ed., M.I.T. Press, Cambridge, MA (1971).
- “Sapphire (Al2O3) Specifications,”.
- Oliver, W.C. and Pharr, G.M., “An Improved Technique for Determining Hardness and Elastic Modulus Using Load and Displacement Sensing Indentation Experiments, Journal of Materials Research 7(6):1564-1583 (1992).
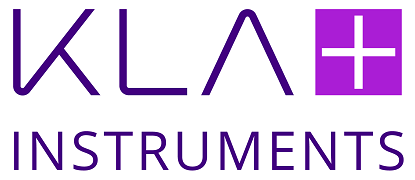
This information has been sourced, reviewed and adapted from materials provided by Nanomechanics, Inc.
For more information on this source, please visit Nanomechanics, Inc.