The aim of this project is to develop a “cure capable AFP mandrel”— a structural, high-accuracy, composite tool which is CTE-matched to the component.
This was an advancement of the composite Automated Fiber Placement (AFP) mandrels currently employed by GKN Aerospace in the production of rear wing spars of the Airbus A350 XWB, which aimed at considerable reductions in tooling as well as manufacturing costs.
.jpg)
Image Credit: Toray Advanced Composites
Development of AFP Mandrel
- Made using Toray AmberTool® HX42
- Nominal 36-ply laminate, by combining both unidirectional and woven tooling prepregs
- Foam core construction eliminates the need for a pattern and enables vibration dampening during final tool machining to guarantee higher accuracy
Toray AmberTool HX42 Composite Tooling Prepregs
- Established system for aerospace tooling
- Low coefficient of thermal expansion for an epoxy tooling resin (CTE 3 x 10-6/°C)
- A tack life of five days, permitting time for lamination of larger tools
- Machinable to realize a highly accurate tool surface
Project Outcome
- A 3.5 m long section of a cure-capable AFP mandrel tool was successfully produced
- Composite components produced from the development AFP mandrel showed exceptional dimensional accuracy when compared to parts produced from an Invar mold of similar geometry
The AFP mandrel test tool developed during the project shows a unique combination of three elements.
A structural item
- Low deflection and high stiffness to satisfy the AFP process criteria
A high-accuracy mold tool
- Long-life capable, vacuum-integral, machined surface to satisfy mold tool performance criteria
CTE matched to the component
- To realize the needed part accuracy
.jpg)
Image Credit: Toray Advanced Composites
GKN Aerospace AFP Mandrels
- Composite AFP mandrels are used to manufacture the rear wing spars of the Airbus A350 XWB
- Maximum weight of 2750 kg
- Maximum length of 13.5 m
- Accurate within ±0.25 mm over the entire surface
- Maximum deflection of <0.1 mm with a 100 kg load placed at the center
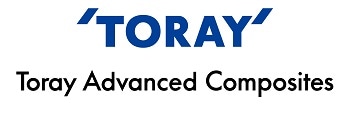
This information has been sourced, reviewed and adapted from materials provided by Toray Advanced Composites.
For more information on this source, please visit Toray Advanced Composites.