In this experiment, the sample used consisted of pelletized PE-LD and PE-LLD and PE-HD in the form of a film.
Conditions of Measurement
Measuring cell: DSC821E with air cooling
Pan: Hermetically sealed lidded aluminum standard pan of 40 µl
Sample preparation: PE-LD disc weighing 9.796 mg cut from a pellet
PE-LLD disc weighing 8.128 mg cut from a pellet
PE-HD disc of 10.314 mg weight punched from a film
DSC measurement: Heating from 30 oC to 180 oC at 10 K/min
Atmosphere of static air was employed.
.jpg)
Evaluation
The results are depicted in the following table:
.jpg)
It is to be stressed that the peak temperature can be evaluated using either of two values, the first being the extrapolated intersection point between the two inflection tangents, and the peak of the DSC curve.
The value arrived at using the first value is relatively independent of the arbitrary peak shape caused by random noise, and this is important because this noise would otherwise cause the actual maximum to vary between runs, causing irreducible peak temperatures. The extrapolated value is therefore more reliable.
Interpretation
The three different qualities of PE have distinct typical melting peaks and different peak temperatures.
Conclusion
The DSC melting curve shows a peak temperature which is the most commonly determined characteristic of polymers in the semicrystalline state. It is therefore the most important parameter used for processing and is generally used to identify the compound.
Characterization of PE in Terms of Crystallinity
The samples used in this experiment were PE-LD and PE-LLD in pellet form while PE-HD is used as a film.
Conditions of Measurement
Measuring cell: DSC821e with air cooling
Pan: Hermetically sealed lidded aluminum standard pan of 40 µl
Sample preparation: PE-LD disc weighing 9.796 mg cut from a pellet
PE-LLD disc weighing 8.128 mg cut from a pellet
PE-HD disc of 10.314 mg weight punched from a film
DSC measurement: Heating from 30 oC to 180 oC at 10 K/min
Atmosphere of static air was employed.
.jpg)
Evaluation
The results are described in the table below:
.jpg)
It should be noted that a straight baseline is utilized to integrate the curve, and accurate weighing of the sample is important because of the use of a normalized sample.
Interpretation
The area falling under the peak is representative of the heat of fusion of the sample. It depends directly upon the amount of crystallites in the sample. By comparing the heat of fusion measured by this method to the theoretical heat of fusion of 100% crystalline polyethylene of 293 J/g.
Conclusions
The crystallinity of the sample by DSC shows how much of the sample is amorphous and how much crystalline. The sample becomes more crystalline as its structure becomes more regular, that is, when it not branched or has only short branches spaced regularly, as well as the heat exposure it has suffered. Increasing crystallinity leads to increase in hardness and in strength, which means that the result of DSC measurement corresponds well with mechanical behavior.
PE-HD Characterization by Conversion Curves
In this experiment, the sample was Lupolen 4261 in the form of pellets and another sample of the same material in molded form.
Conditions of Measurement
Measuring cell: DSC821e with air cooling
Pan: A lidded aluminum standard pan of 40 µl with a predrilled hole in the lid
Sample preparation: Discs weighing about 5 mg each cut from the molded part or the pellet
DSC measurement: The thermal history was eliminated by heating from 25 oC to 200 oC at 10 K/min followed by cooling it at 5 K/min. During the actual experimental measurement, the second heating was performed from 25 oC to 200 oC at 10 K/min.
An atmosphere of nitrogen at 50 cm3/min was employed.
.jpg)
Evaluation
The results are described in the table below:
.jpg)
Interpretation
The manner of sample melting is characterized using the heat of fusion, the peak temperature and the maximum width at half height. The three values are taken together or a conversion curve is used. The conversion curve is also called the fraction melted, and represents the percentage of crystallites that has undergone melting at the temperature in question.
It may be shown as a table or a graph. Unlike the degree of crystallinity of a sample, conversion is dependent on other variables and so does not vary with inaccuracies in sample weight. The samples were weighed in a balance accurate to 0.1 mg. If there is an uncertainty in sample weight to 0.3 mg, for instance, it could result to 6% inaccuracy in the resulting heat of fusion calculated from this experiment, and so to the degree of crystallinity measured.
Conclusion
Both samples showed more or less the same melting behavior, with the chief difference being with respect to the heat of melting. The following shows the crystallization behavior compared between the two samples.
PE-HD Characterization by Crystallization Behavior
The samples for this experiment were Lupolen 4261 as pellets and as a molded part.
Conditions of Measurement
Measuring cell: DSC20
Pan: A lidded aluminum standard pan of 40 µl with a predrilled hole in the lid
Sample preparation: Discs weighing about 5 mg each cut from the molded part or the pellet
DSC measurement: The sample was melted by heating to 200 oC at 10 K/min. During the actual experimental measurement, cooling was performed from 200 oC to 25 oC to at 10 K/min.
An atmosphere of nitrogen at 50 cm3/min was employed.
.jpg)
Evaluation
The results are shown in the following table:
.jpg)
Interpretation
The behavior during the crystallization of the sample is described in terms of the onset of crystallization, the peak width of the curve and the heat of crystallization. The conversion curve and the corresponding curve are used to compare the samples in this respect.
Conclusion
Both samples show similar crystallization and show a difference in heat of crystallization which is almost identical to the difference in melting behavior of the samples as measured in the last experiment.
Comparing PE-HD from Different Manufacturers
The samples used in this experiment were Vestolen a 6017, Stamylan HD 7771, Finathene 58070 and Lupolen 4261.
Conditions of Measurement
Measuring cell: DSC20
Pan: A lidded aluminum standard pan of 40 µl with a predrilled hole in the lid
Sample preparation: Discs cut from the pellets
DSC measurement: Heating from 30 oC to 200 oC at 10 K/min.
An atmosphere of nitrogen at 50 cm3/min was employed.
.jpg)
Evaluation
The results of the experiment are shown below:
.jpg)
It should be noted that the diagram shows only the Vestolen curve for the sake of clarity.
Interpretation
In all the samples, the DSC curves show the onset of deviation from baseline values between temperatures of 50 oC and 60 oC, and return to original values at higher temperatures between 145 oC and 160 oC.
Conclusions
There are marked and characteristic differences between the melting peaks of different qualities of PE-HD by DSC. To eliminate the thermal history and resulting effects, it is necessary to premelt and then recrystallize the samples at 10 K/min. The masses of the samples should be more or less identical, such as 5 ± 2 mg. The width of the peak is especially variable with the mass of the sample, as the more the mass, the greater the time taken for melting and the broader the peak becomes.
PE Melting Curve and Thermal History
In this experiment the sample consisted of PE-HD film.
Conditions of Measurement
Measuring cell: DSC821e with air cooling
Pan: A lidded aluminum standard pan of 40 µl which is hermetically sealed
Sample preparation: Disc weighing 2.33 mg which is punched out from the film
DSC measurement: The sample was pretreated by annealing it at 129 oC for 60 minutes, and then cooling it to 40 oC at 5 K/minute. The second phase consisted of heating it from 40 oC to 180 oC at 5 K/min, as shown in the curve representing PE-HD which has undergone annealing at 129 oC, and then cooling it from 160 oC to 40 oC at 5 K/minute. The second round of heating was from 40 oC to 180 oC at 5 K/minute, as shown in the PE-HD curve where the thermal history has been eliminated.
An atmosphere of static air was employed.
.jpg)
Evaluation
It is possible to measure the melting gap either as the onset of melting or by using the conversion curve. The greatest importance is attached, however, to the temperature of annealing.
Interpretation
When the sample is annealed at 129 oC crystallites are segregated, in that the smaller ones undergo melting and recrystallization, forming crystallites again which melt above 129 oC. However, this excludes crystallites which melt at or below this temperature. With cooling of the sample, small crystallites which have melting points at or below 129 oC reform, but a melting gap, at 129 oC, is seen during the second run of sample heating. By melting the sample completely, it is possible to eliminate all thermal history.
Conclusion
The DSC curve varies in shape with the sample’s thermal history. The importance of detecting the melting gap is verifying that the temperature at which the sample was processed was correct, such as when high-voltage cables of PE are annealed. By melting the sample completely, the thermal history is eliminated, and thus this step is essential to compare different raw materials.
PE-HD Identification of Cable Tubing and Recycled Material
The sample used in this experiment consisted of two automotive tubings as well as recycled material claimed to be PE-HD.
Conditions of Measurement
Measuring cell: DSC20
Pan: A lidded aluminum standard pan of 40 µl with a predrilled hole in the lid
Sample preparation: Discs cut from the materials
DSC measurement: Heating from 30 oC to 200 oC at 10 K/min. 5
An atmosphere of nitrogen at 50cm3/ min was employed.
.jpg)
Evaluation
The results are represented in the table below:
.jpg)
Interpretation
All three samples show melting curves on DSC which are typical of PE-HD.
Conclusions
The use of the DSC melting curve allows the identification of PE-HD material, and shows that one of the tubings which was sub-standard was also made of this material. Samples should be premelted and cooled at the same rate such as 10 K/minute to eliminate the thermal history.
Recycled material lacked the appropriate label to mark it as original manufacturer’s packaging material. This underlines the need to make sure the material is the right one. In addition, it is necessary to confirm that its quality is kept intact through the early processing and recycling of the material.
DSC of Recycled Sheets, said to be PE-HD
The sample in this case consisted of distorted and brittle sheets which were claimed to be manufactured from PE-HD.
Conditions of Measurement
Measuring cell: DSC20
Pan: A lidded aluminum standard pan of 40 µl with a predrilled hole in the lid
Sample preparation: Disc of 6.8 mg weight cut from the materials
DSC measurement: Heating from 30 oC to 200 oC at 10 K/min. 5
An atmosphere of nitrogen at 50 cm3/min was employed.
.jpg)
Evaluation
When the heat of fusion is found for the polypropylene (PP) maximum at 14.3 J/g, it provides a basis for the calculation of the approximate PP content. For instance, if the heat of fusion of pure PP is 60 J/g, as is generally seen, the content is calculated as follows:
Content = ΔH/ΔHPP·100%, i.e. 23.9%
Interpretation
The melting curve depicts the nature of the material to be a blend of PP with a peak temperature of 163 oC with PE-HD with a temperature maximum of 135 oC, and not pure PE.
Conclusion
DSC testing in this case provided evidence of the lack of pre-agreed quality in the material supplied, which was then replaced by the supplier without additional cost.
PE-LD Comparison of Two Products
For this experiment, pellets of Lupolen 1800 S and Lupolen conz. SL 020 were used as samples.
Conditions of Measurement
Measuring cell: DSC20
Pan: A lidded aluminum standard pan of 40 µl with a predrilled hole in the lid
Sample preparation: Discs cut from the center of the pellets
DSC measurement: Heating from 30 oC to 250 oC at 10 K/min.
An atmosphere of air at 50 cm3/min was employed.
.jpg)
Evaluation
The results are shown in the following table:
.jpg)
Interpretation
The DSC curves have a shape typical of PE-LD but show an exothermic component at a temperature over 200 oC because of the beginning of the oxidative change.
Conclusions
The percentage crystallinity as well as the peak temperature both show the two samples to be of nearly identical quality and their chemical nature to be PE-LD. The fact that both start to show oxidative changes at about 220 oC may be due to the stabilized nature of the samples, since basic PE shows onset of oxidation at a somewhat higher temperature. The stability of Lupolen 1800 S is higher than of the other sample material, and can be further improved by the addition of antioxidants, to yield a temperature of onset of oxidation of about 260 oC.
PE Oxidation Stability
The sample in this experiment is Lupolen GM5040 T12, as a stabilized film of PE-HD.
Conditions of Measurement
Measuring cell: DSC821e cell with air cooling and a gas controller
Pan: A lidless aluminum standard pan of 40 µl and a copper pan of 40 µl for the sake of comparison
Sample preparation: Discs punched out of the film
DSC measurement: According EN 728 (European standard):
Under nitrogen, 50 cm3 /min 3 min isothermal at 30 °C, then heating to 200 °C at 20 K/min, 2 min isothermal at 200 °C.
Under oxygen, 50 cm3 /min (automatically switched by the gas controller): Isothermally at 200 °C starts the actual measurement. Since only the onset of oxidation is required, the actual measurement time can be reduced using the Conditional Experiment Termination software option.
An atmosphere of nitrogen followed by oxygen in alternation was used, the two being switched automatically by a gas controller.
.jpg)
Evaluation
In the aluminum pan the sample showed the onset of oxidation in 15.9 minutes, called the Oxidation Induction Time (OIT), while the onset took 9.5 minutes in the copper pan. The evaluation of the melting curve was also achieved.
Interpretation
The time after switching to oxygen to the onset of oxidation (intersection of baseline with the tangent) is called the induction period or Oxidation Induction Time, OIT. If the OIT is greater the compound is more stable. The oxidation reaction is catalyzed if copper or its alloys are in contact with the sample and therefore if the polyolefins are likely to be exposed to copper this possibility must be compensated for by using special additives.
The additives themselves undergo efficiency testing in a copper pan with the sample. If the sample is stable the OIT will be half or more of the value got from testing in an aluminum pan. In the absence of these additives, the OIT becomes ten times less when determined in a copper pan.
It should be noted that unlike other polymers, polyolefins have characteristic induction periods. For other polymers, testing should be done by heating with oxygen at a slow rate such as 5 K/minute for choice, until exothermic oxidation begins to be seen.
Conclusion
It is easy and quick to determine oxidation stability using DSC, especially when the sample is a water pipe or electrical cable that requires a long life and its quality is to be assured. Each batch of raw materials must undergo measurement. The fusion peak found in this method allows the polymer to be identified.
Cross-Linked PE by Dynamic Load TMA
The sample used in this experiment was crosslinked PE as a sheet.
Conditions of Measurement
Measuring cell: TMA40 using a ballpoint probe of 3 mm
Pan: The sample is placed between discs of fused silica which have a diameter of 6 mm and are 0.5 mm thick.
Sample preparation: Rectangular samples about 4 x4 cm cut off from the sheet with a knife, with a height of 5.1 mm which is that of the original sheet.
TMA measurement: In the first run of heating the temperature is 150 oC at 10 K/minute, by which the thermal history is eliminated. After cooling the sample without regulation to 25 oC the measurement was taken while heating occurred at 10 K/minute. The sample was also pretreated under a dynamic load.
Load: The load changed with a period of 6 seconds between 0.01 N and 0.19 N
An atmosphere of static air was used.
.jpg)
Evaluation
The amorphous state showed an elastic deformation of 1.9% from which the complex Young’s modulus, E was calculated as shown below:
E = ΔF/(A·ΔLr), where ΔF is the change in force, A the cross-sectional area of the sample, and ΔLr the relative change in length (1.9%).
E = 0.18 N/(4⋅4 mm2⋅0.019) = 0.59 N/mm2.
The envelopes showed a difference in onset at 99.6 oC in proportion to the melting of the crystallite.
As shown below, the slope of the upper envelope is used to calculate the coefficients of expansion, at a load of 0.01 N:
275 ppm/K when the temperature is between 40 oC and 50 oC in semicrystalline state
353 ppm/K when it is between 120 oC and 130 oC in amorphous state
Interpretation
Both standard PE and crosslinked PE show rigidity below the melting range in crystallite form. With crystallite melting there is an increase in volume with a rubbery-like change in properties. The elastic deformation of about 1.9% is seen with force variation. The upper and lower envelopes vary in intervening distance in proportion to the compliance, I/E. The expansion undergone by the sample is shown in the overall slope of the curve envelope.
It should be noted that non-crosslinked PE is forced out from between the silica discs once melting occurs, which is called plastic deformation.
Conclusions
Crosslinked PE above the melting range for crystallites shows thermomechanical properties which are quite distinct from ordinary PE, such as a rubber-like elastic property instead of viscous flow, because the crosslinking of the polymer makes plastic deformation impossible.
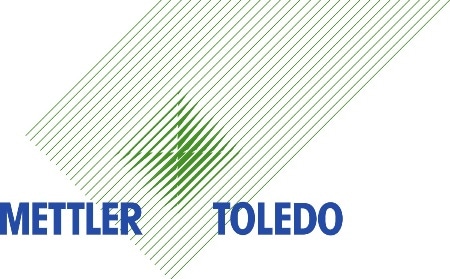
This information has been sourced, reviewed and adapted from materials provided by Mettler Toledo - Thermal Analysis.
For more information on this source, please visit Mettler Toledo - Thermal Analysis.