Interview conducted by Alex SmithNov 15 2021
In this interview, AZoM talks to Jurgen Schawe from Mettler Toledo about fast scanning chip calorimetry and the various applications this can be utilized in.
Could you please begin by giving our readers an overview of the Differential scanning calorimetry (DSC) method and why this technique is useful?
The DSC technique measures the heat involved in a thermal event. This can be an endothermal or exothermal transformation of a material. Besides isothermal measurements, this technique can be used in heating and cooling modes. For conventional DSC, the typical scanning rate range is between 0.1 and 100 °C per minute, and samples in the milligram range that are enclosed in a small crucible are used.
A conventional DSC device contains a sensor with two separate measurement positions - one for the sample in the crucible, and the other for the reference, which is usually an empty crucible. The sensor is located in a furnace that operates at a precisely controlled temperature. The measurement system is several centimeters in diameter.
Information that can be derived from DSC curves are the enthalpy and temperature of phase transformations like crystallization, melting, solid-solid transformations and for liquid crystalline materials also liquid-liquid transformations. For amorphous and semi-crystalline materials, the glass transition can be analyzed. Furthermore, the enthalpy and temperature of chemical reactions like crosslinking, decomposition, or dehydration can be measured. The kinetics of these thermal events can be analyzed by measurements with various heating or cooling rates.
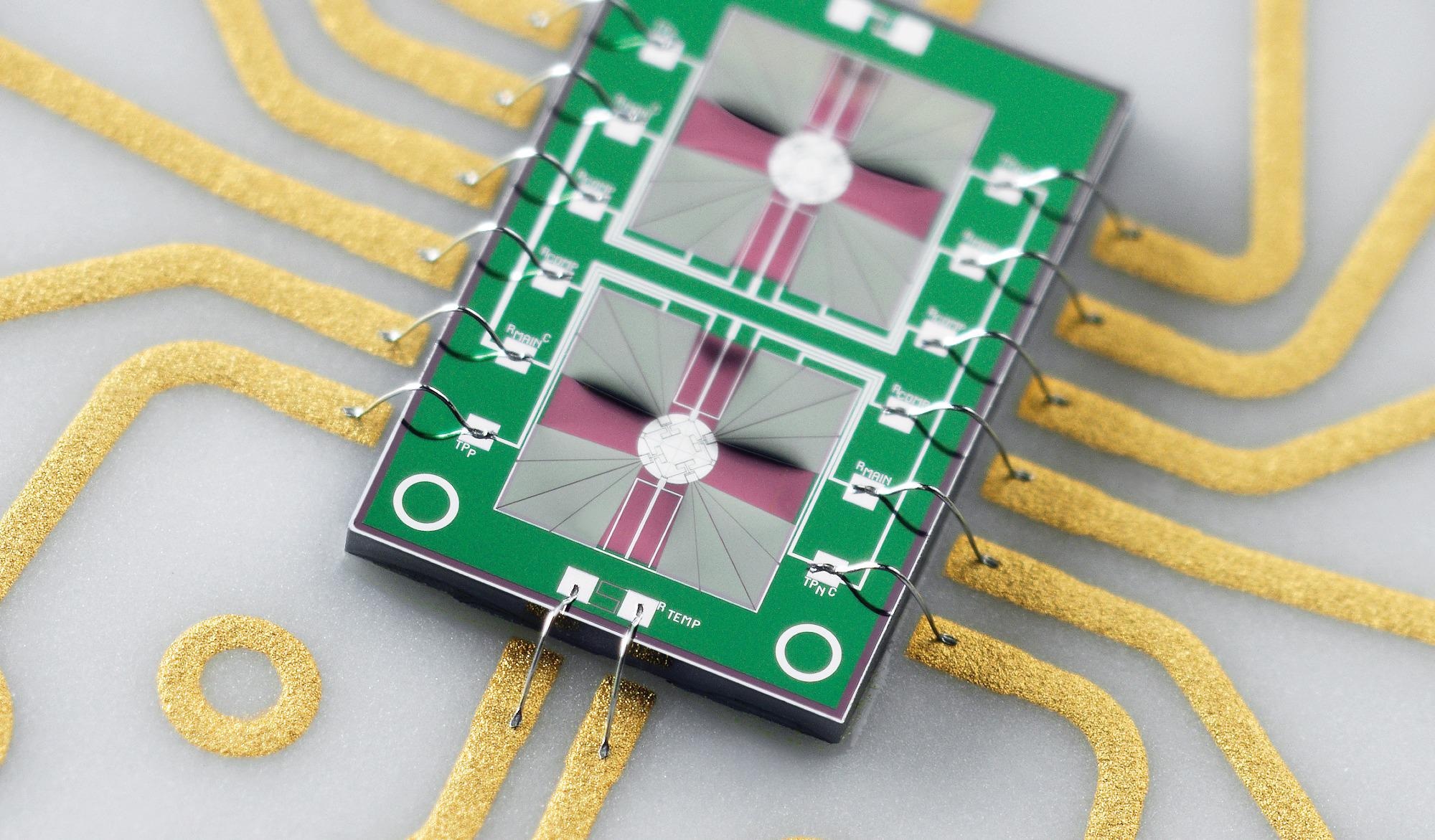
Image credit: Mettler Toledo
What are some of the limitations of the traditional DSC approach, and how can these be overcome?
There are limitations regarding the interpretations of measurement curves and understanding of material behavior during processing.
Let’s start with the interpretation.
Modern materials like polymers, metal alloys, or pharmaceuticals usually form metastable structures, which may transform into more stable modifications during heating. Such reorganization processes are not always visible in conventional DSC because exothermic and endothermic events can occur simultaneously and the total heat measured becomes very small.
Many thermal events are so fast that they cannot be completely studied using conventional DSC. Examples are the crystallization of many polymers or glass-forming metal alloys. Due to the limitations of the scanning rate, it is not possible to study isothermal crystallization in a wide temperature range because the crystallization may occur already during cooling from the melting to the crystallization temperature.
Another problem is related to the thermal stability of many organic materials. Such materials often tend to decompose during melting processes. This has the consequence that neither the melting enthalpy nor the melting temperature can be correctly determined using conventional calorimetric techniques.
Material processing is often related to fast cooling or heating. Typical rates are between 10 to several thousand °C per second. The behavior of materials during such rates cannot be directly studied using conventional DSC. Besides many conventional processing techniques, also the modern technique of additive manufacturing, also known as 3D printing, are examples in which high heating and cooling rates are used.
To overcome the limitations due to the insufficient scanning rates, Mettler Toledo developed Flash DSC. This is a new type of rapid scanning DSC instrument using the latest technology.
What advantages does the Flash DSC offer over conventional DSC instruments?
The Flash DSC is a non-adiabatic chip calorimeter, which combines an innovative measurement and control concept with user-friendly ergonomics and functionality.
The Flash DSC sensors are based on MEMS technology and contain a complete DSC with a sample and reference furnace embedded on a thin silicon nitrate membrane. This sensor design makes the heat capacity of the furnaces small, which leads to fast scanning rates.
To cool the sample with a fast cooling rate, the sample is surrounded with a relatively cooled gas. This enables a quick cooldown of the sample. To improve the thermal contact between sample and sensor, the sample is directly placed on the sensor without any crucible.
Currently, two sensors are available - the standard sensor UFS for a maximum temperature of about 500 °C and the high-temperature sensor UFH that can be used up to 1000 °C. The minimum temperature is about -95 °C. These sensors offer wide scanning rate ranges typically between 1 and 10,000 °C per second for UFS sensors, and up to 50,000 °C per second for the UFH sensor, respectively. This high dynamic range opens new horizons for the kinetic analysis of thermal events.
It is important to realize that there is an overlap of scanning rates between Flash DSC and a conventional DSC.
To achieve the ultra-high scanning rates, the Flash DSC can work with a small sample - typically a few micrograms down to nanograms in mass.
The preparation and insertion of these tiny samples can be performed by a user who is able to sit comfortably in front of the instrument. To ensure optimal thermal contact, the sample is positioned directly onto the sensor with the aid of a microscope. This also ensures simple and reliable sample handling. In addition, other preparation techniques are possible. For instance, thin films can be prepared using spin coating or spattering.
Thanks to the innovative sensor support, the sensor can be quickly and easily changed in less than a minute. A lid can also be mounted on top of the sensor support and is sealed with screws to protect oxygen-sensitive materials.
Could you expand on the sensors available in the Flash DSC?
At the heart of the Flash DSC is the MEMS technology-based chip sensor. Mounted in a ceramic frame with electrical contacts, the standard UFS sensor consists of two identical two micrometer thick Silicon Nitride membranes. The sensor features sample and reference areas with incorporated heaters and thermocouples, each with a diameter of 0.5 millimeters.
The sensor is effectively a complete, miniaturized DSC furnace for sample and reference analysis.
The high degree of symmetry between the two sides of the sensor, the high sensitivity, and the short time constant produces an extremely reproducible measurement and a high dynamic range of the Flash DSC, which is about two orders in magnitude bigger than in conventional DSC. The nominal maximum temperature of the UFS sensor is 450 °C. However, it can also be used at higher temperatures up to 520 °C. Flash DSC can be operated with a standard UFS sensor or a high-temperature UFH sensor.
The UFH sensor enables measurements up to 1000 °C, making it ideal for the study of ceramics and metals, such as bulk metallic glasses. The sample and reference areas are smaller. The diameter is 80 micrometers. Two heaters surround these areas. The smaller geometry reduces the time constant of the sensor and increases the maximum scanning rate to over ten thousand °C per second. This makes this sensor also useful for many polymer applications.
What steps should users take to ensure they get the best results when investigating kinetic processes using DSC?
It is often advisable to use a wide variety of heating and cooling rates when kinetic processes significantly affect the structure formation in the material under investigation.
In these cases, the structures depend on the cooling conditions and are often metastable. This means that the structures can change as a result of temperature change or during isothermal storage.
Polymers are an example of a material that forms metastable structures. Due to their molecular structure, they produce only small crystallites on cooling from the melting point. The size of the crystallites depends on the crystallization temperature. A higher cooling rate decreases the crystallization temperature, and by further decreasing this, glass can be formed for many polymers.
Reorganization can occur when heating, which leads to crystal perfection. A possible process could be melting less perfect crystallites and recrystallizing them to form more stable structures. In such a case, exothermic and endothermic processes occur at the same time and the DSC curve shows no significant indication of such processes.
It is important to note that in these circumstances, the DSC melting curve shows the result of the reorganization and not the melting of the original crystallites.
The degree of reorganization depends on the heating rate, and at high heating rates, the reorganization can be suppressed. Metastable structures are formed in many other materials besides polymers, for example, polymorphic substances.
In metal alloys, diffusion processes, phase separation, precipitation, and other time-dependent processes lead to the formation of metastable structures.
The different phases and their distribution depend on the crystallization conditions.
For example, physical stability, entropy retardation, and crystallization kinetics at low temperatures are of particular interest for glass-forming materials.
Due to differences in the activation energies of physical processes and chemical reactions, it is possible to separate chemical reactions, such as decomposition, from phase transformations like glass transition and melting by using high heating rates. This is a big advantage for the measurement of chemically unstable materials.
The kinetics of structure formation can be studied by performing cooling measurements at different cooling rates.
An important advantage of the Flash DSC is that the cooling rates correspond to those of technical processes, such as those which occur in injection molding or laser sintering. This allows us to closely follow the formation of a structure that occurs in the process and obtain information about the function and action of additives.
What are some other applications areas where the Flash DSC can be useful?
Other application areas of the Flash DSC include the analysis of processes involving the complex and rapid formation of structures, the determination of the reaction kinetics of fast reactions, or the investigation and comparison of the action of additives at cooling rates directly relevant to the process.
As the scanning rates are high, a comprehensive thermal analysis of materials can be performed in millisecond ranges. For example, the isothermal crystallization process can be directly measured across a wide temperature range.
These measurements are very sensitive to the influence of additives or small compositional modifications. The Flash DSC allows the investigation of very small amounts of sample, down to just a few nanograms.
As the data can be measured under actual process conditions, this can be used in simulation calculations, for example, to optimize the performance of tools, the composition of materials, or processing parameters.
The need for heating and cooling rates higher than those available with a conventional DSC is driven by potential applications.
What key points would you like our readers to take away about the value of the Flash DSC, and where can they find out more information?
The Flash DSC is the ideal complement to conventional DSC. This is primarily because the instrument provides an extremely wide range of heating and cooling rates - a very important factor for the characterization of modern materials.
The data obtainable via the Flash DSC optimizes the production processes, specifically because materials can be measured at the cooling rates at which they were produced. Materials or production conditions can be improved through the measurement of structure formation at cooling rates relevant to those that occur in production.
The instrument’s capacity for fast and variable measurements also allows materials to be characterized in a very short period of time.
The ultra-high cooling rates of the Flash DSC enable processes involving structure formation on cooling to be measured. In contrast, ultra-high heating rates reduce measurement times and can be used to investigate reorganization processes or to prevent reorganization from occurring.
Thanks to the high sensitivity, the Flash DSC’s heating, and cooling rates overlap, to a certain extent, with those of a conventional DSC. This enables experimental results to be directly compared.
The temperature range of the Flash DSC is -95 °C to 1000 °C, and the instrument’s application-oriented ergonomics and functionality have been specifically designed to enable easy and rapid sample preparation.
As shown by the large number of scientific publications, Flash DSC has become an important method in the characterization of materials, with which many previously unknown effects have already been detected and its range of application is continuously expanding.
A wide range of Flash DSC applications can be downloaded via the internet. METTLER TOLEDO publishes articles on thermal analysis and applications from different fields in the well-known METTLER TOLEDO bi-annual technical customer magazine. Back issues can also be downloaded as PDFs.
To learn more about the Flash DSC or other METTLER TOLEDO thermal analysis products, please visit our website or call your local METTLER TOLEDO sales specialist. Our website also includes information on our full range of handbooks, brochures, webinars, videos, application notes, training courses, apps, and other products.
About Dr. Jürgen Schawe
Jürgen E. K. Schawe was awarded a Ph.D. in solid state physics in 1984. After that, Dr. Schawe worked at the University of Rostock in the Polymer Physics Group, and from 1992 to 1998 at the Section of Calorimetry at the University of Ulm. Since 1999 he has worked for Mettler-Toledo GmbH in Nänikon, Switzerland. Dr. Schawe is a senior application scientist for Material Characterization. Since 2020, he has been a visiting scientist at the Department of Materials at the ETH Zurich. Dr. Schawe was awarded the 2010 STK Award of Applied Chemical Thermodynamics by the Swiss Society for Thermal Analysis and Calorimetry. To date, Dr. Schawe has published 80 articles in pre-reviewed scientific journals, including high rating journals like Nature Communications. He edited a special issue of Thermochimica Acta, wrote a book chapter and has been awarded 5 patents.

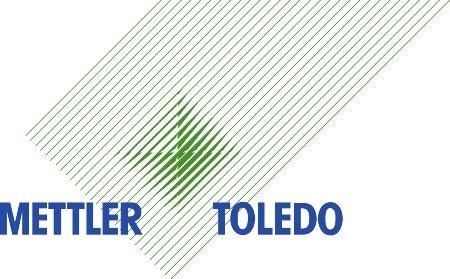
This information has been sourced, reviewed and adapted from materials provided by Mettler Toledo - Thermal Analysis.
For more information on this source, please visit Mettler Toledo - Thermal Analysis.
Disclaimer: The views expressed here are those of the interviewee and do not necessarily represent the views of AZoM.com Limited (T/A) AZoNetwork, the owner and operator of this website. This disclaimer forms part of the Terms and Conditions of use of this website.