Carbon fiber reinforced polymer composites, or CFRPs, have excellent mechanical properties, such as high strength-to-weight ratios, high stiffness, and the potential to bear dynamic loading in service without catastrophic failure.
In-Situ Fiber Push-Out Tests with the Hysitron PI 88 SEM PicoIndenter
Therefore, in many applications, CFRPs excel as structural components, specifically in the aerospace industry where they are rapidly replacing heavier metallic components. A composite gets its mechanical strength from not just a combination of mechanical properties of the constituent matrix and fiber materials but also the strength of the interface between them.
A fiber push-out test can be carried out to measure the sliding characteristics and interfacial strength of individual fibers in reinforced composite materials. This study employs Bruker's Hysitron® PI 89 SEM PicoIndenter® equipped with the 800 °C heating option for characterizing the interfacial strength between individual carbon fibers and the surrounding polyamide matrix, as a function of temperature.
.jpg)
Figure 1. Hysitron PI 89 SEM PicoIndenter with 800 °C module
In-Situ Fiber Push-Out at Elevated Temperatures
A Hysitron PI 89 SEM PicoIndenter equipped with a 5 μm diameter diamond flat punch on a carbon fiber-reinforced polymer suspended on a grooved steel substrate was used to perform the fiber push-out experiments. The fibers were loaded using displacement-controlled feedback to the point where complete interfacial failure was observed and the fibers started sliding through the matrix.
The tests were performed at different elevated temperatures up to 300 °C as well as at room temperature. Closed-loop resistive heating of both the sample and the probe was carried out to achieve the heating. The in-situ nature of the testing enabled real-time, direct observation of the failure progression and push-out mechanism, as well as the exact alignment of the tip on the fiber.
Sample Preparation
From a bulk fiber-reinforced composite sample, a thin sample with a cross-section of 5 mm x 5 mm and a thickness of 300 μm was prepared. As illustrated in Figure 2a, a polished substrate and the sample were clamped together and fitted on a heater attached to the SEM PicoIndenter. Space for the fiber push-out was provided by grooving the substrate. As illustrated in Figure 2b, the tip was aligned and positioned above the fibers by using the Hysitron PI 89 stage.
.jpg)
.jpg)
.jpg)
Figure 2. (a) Low-magnification SEM image of a sample clamped to a substrate; (b) pre- and (c) post-images of a fiber push-out test.
Interfacial Failure
Figure 3 illustrates two load-displacement (P-h) curves showing different stiffness regimes at the time of loading. The progression of interfacial failure can be understood with the help of the videos recorded during the tests. The low initial stiffness of the P-h curves is due to bending down of the thin sample to make contact with the grooved support.
.jpg)
Figure 3. Load vs displacement curves of fiber push-out at room temperature (blue) and 316 °C (red).
The applied load is transferred completely to the fiber as soon as the sample makes solid contact with the substrate, thereby increasing the stiffness of the curve. At this phase, the shear stress is introduced by the applied compressive load at the interface with a maximum value at the sample surface. Interfacial debonding starts and load drops at a critical value of interfacial shear stress.
The term failure load refers to the maximum sustained load before debonding can be observed. Based on the debonding mechanism and temperature, the P-h curves demonstrated gradual, sudden, or stepped load drops. Gradual and multi-step load drops are caused by slow propagation of crack through the interface, whereas sharper load drops are related to the complete failure of the interface. Even surrounding fiber-matrix interfaces failed in some instances. Figure 2c shows an image of complete fiber push-out.
Role of Temperature
The tests were performed at a temperature ranging from room temperature to 316 °C. As illustrated in Figure 4, a failure load reduction was noted at elevated temperatures as the interfacial shear strength reduces and the interface turns weaker. Furthermore, with the softening of the matrix at elevated temperatures, it was pulled away more easily from the surrounding fibers when the loaded fiber was pushed-out. Following the tests, the backside of the sample, the push-out fibers, and the surrounding matrix was observed by removing the sample from the Hysitron PI 89. An image of the push-out fibers is shown in Figure 5.
.jpg)
Figure 4. Push-out force vs temperature. A sharp reduction in push-out force was observed as the temperature approached 300 °C.
.jpg)
Figure 5. The backside of the sample showing complete push-out of the tested fibers.
Conclusions
A method for measuring the debonding strength of single fibers within fiber-reinforced composites is demonstrated by the fiber push-out study. The in-situ nature of the tests also offers useful information not just about the progression of failure but also about the effect of temperature on the deformation process — observations that would go unobserved if the tests are not performed inside an SEM.
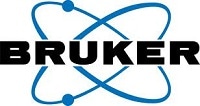
This information has been sourced, reviewed and adapted from materials provided by Bruker Nano Surfaces.
For more information on this source, please visit Bruker Nano Surfaces.