Currently, composites are widely in use in various parts of the modern world such as constructions, nonwovens, textiles, and automobile industry. The interface in composites plays a fundamental role in the final mechanical properties. Two key methods have been added to strengthen the interface between matrix and reinforcement: (i) adding a third component as compatibilizer and (ii) morphological development. Concerning the latter, morphological development of polymer blends is another method that boosts the interfacial adhesion of two mismatched polymers.
In the last 10 years, numerous morphologies have been added — such as droplet,1 platelet,2 coral,3 and fibrillar4 — to boost the mechanical properties of polymer blend systems. The formed morphology is under control of different factors such as molecular weight, chemical structure, viscosity ratio, and processing parameters.3 Therefore, it can be anticipated that difference in the above-mentioned factors has an impact on the final formed morphology.
Similarly, microfibrillar architecture has emerged in the last 10 years as a new type of microstructure wherein two incompatible polymers develop an in situ-reinforced blend by formation of fibrillar morphology.4 To realize the fibrillar morphology, three consequential steps should be carried out:
- Blending of two incompatible blends with varied melting temperatures
- Cold drawing at temperatures below the Tm of dispersed phase
- Isotropization at temperatures below the Tm of dispersed phase
The dispersed phase is fibrillated by using different methods such as injection molding,5 compression molding,6 and fiber spinning7. In contrast to the other methods, the spinning process inserts higher elongational stress, which may enable the fibrillation mechanism and droplet may experience the maximum value of elongational stress field. Laboratory Mixing Extruder (LME) manufactured by Dynisco has established itself as a device with the potential to spin the polymer melt at various temperatures.7,8
The temperature profile of the LME is controlled via rotor and die zones. The rotor can rotate at different speeds and a take-up device can be attached to draw the polymer melt as monofilament. As was stated in earlier works, the LME has the capability to not only work as a spinning device, but also to fibrillate the dispersed phase in polymer blends of [Polypropylene (PP)/Poly amide 6 (PA6)] and [Polypropylene (PP)/Polytrimethylene Terephthalate (PTT)] (schematic 1).7,8
.jpg)
Schematic 1. The LME setup and its components to produce fibrillary reinforced monofilaments.
Figure 1 denotes cryogenically fractured surfaces of as-extruded samples and fibers of PP/PTT. As can be seen in Figure 1 (a)-(b), as-extruded samples exhibit a droplet-matrix morphology whose microstructures turn coarser upon raising the PTT content. The mean diameters of droplets in as-extruded samples of 6 wt% and 10 wt% were 1.26 ± 0.7 μm and 1.9 ± 0.9 μm, respectively. Interestingly, microstructures of fibers in Figure 1 (c)-(d) showed fibrillar entities that are oriented along the fiber axis. The mean diameters of fibrils across the fibers were 0.53 ± 0.1 μm and 0.9 ± 0.4 μm, respectively. Evidently, the LME has the potential to spin monofilaments having fibrillar entities of PTT.
.jpg)
Figure 1. SEM images. (a) and (b): Fractured surfaces of as-extruded samples with 6 wt% and 10 wt% of PTT, respectively. (c) and (d): Etched surfaces of one spun blend filament containing 6 wt% and 10 wt% of PTT, respectively. The scale bar is 10 μm.
To have a proper understanding of the droplet deformation mechanism, rheological approach was carried out to examine the different steps of fibrillation. As a rule of thumb, to preserve elongated inclusions intact, the measurement temperature was maintained at 195 °C, which is below the Tm of PTT.
Dynamic viscoelastic responses of as-extruded blends and fibers at 195 °C are shown in Figure 2. In Figure 2(a), it can be seen that by boosting the PTT content, storage moduli of as-extruded samples increased. This improvement can be credited to interfacial tension, volume fraction, and size of the dispersed phase. Remarkably, fibers characterized higher magnitudes together with non-terminal trend compared with as-extruded samples at low frequency. The presence of secondary plateau was also seen for PP/PA6 blend system wherein PA6 droplets formed fibrillated texture all over the PP matrix.7 This non-terminal behavior was credited to the presence of fibrillated droplets and the development of the physical fibrillar network (PFN) is reflected by improvement in storage modulus and spreading of the secondary plateau at low-frequency region.8
.jpg)
Figure 2. Linear viscoelastic responses of as-extruded samples and fibers containing 6 wt% and 10 wt% of PTT at 195 °C. (a) Dynamic storage modulus and (b) complex viscosity.
Flow behaviors of the fibril-fortified fibers are illustrated in η*-ω graphs (Figure 2(b)). Evidently, the complex viscosity of as-extruded samples at low frequencies improved when the PTT content was increased. Interestingly, the flow behaviors of the fibers revealed a marked increase in complex viscosity in the form of viscosity upturn, along with faster shift to power-law region with regards to raising the PTT content and consequently fibril maturation. The detected upturn of complex viscosity at low frequencies can be credited to yield behavior of fibril-concentrated PP matrix.
Conclusion and Outlook
As one of the most successful morphologies, fibrillar morphology allows the blend systems to eliminate the aggregation problem of nano-fillers in nanocomposites. Consequently, enhancing the processing conditions, to realize ideal properties, would be of interest.
In this article, the LME was established as a spinning tool to fibrillate the droplet phase in the blend system of PP/PTT. It was discovered that upon the development of fibrillar entities, terminal behavior is substituted with non-terminal trend. Furthermore, the fibril growth can be reflected by an improvement in the secondary plateau together with the enlargement of this region, which can be measured as the change of the droplet phase into fibril. As fibrillar morphology has the capability to considerably improve the mechanical strength, it would be of interest to detect the behavior of secondary plateau by altering the type of dispersed phase.
According to the individual molecular characteristic of each polymer, the distinctive behavior of the secondary plateau may differ. Additionally, the potential of the LME to spin nanocomposite fibers is still under examination, which would be made public in the near future.
References
- J. Shen, M. Wang, J. Li, and S. Guo: “In situ fibrillation of polyamide 6 in isotactic polypropylene occurring in the laminating-multiplying die,” Polym. Adv. Technol., 2011, 22(2), 237–245, doi: 10.1002/pat.1525.
- J. S. Hong, J. L. Kim, K. H. Ahn, and S. J. Lee: “Morphology development of PBT/PE blends during extrusion and its reflection on the rheological properties,” J. Appl. Polym. Sci., 2005, 97(4), 1702–1709, doi: 10.1002/app.21695.
- P. Cassagnau and A. Michel: “New morphologies in immiscible polymer blends generated by a dynamic quenching process,” Polymer, 2001, 42(7), 3139–3152, doi: 10.1016/S0032- 3861(00)00602-9.
- S. Fakirov: “Nano- and Microfibrillar Single-Polymer Composites: A Review,” Macromol. Mater. Eng., 2013, 298(1), 9–32, doi: 10.1002/mame.201200226.
- B. Na, Q. Zhang, Q. Fu, G. Zhang, and K. Shen: “Super polyolefin blends achieved via dynamic packing injection molding: The morphology and mechanical properties of HDPE/EVA blends,” Polymer, 2002, 43(26), 7367–7376, doi: 10.1016/S0032-3861(02)00637-7.
- R. J. Shields, D. Bhattacharyya, and S. Fakirov: “Oxygen permeability analysis of microfibril reinforced composites from PE/PET blends,” Composites Part A: Applied Science and Manufacturing, 2008, 39(6), 940–949, doi: 10.1016/j.compositesa.2008.03.008.
- R. Hajiraissi, Y. Jahani, and T. Hallmann: “Investigation of rheology and morphology to follow physical fibrillar network evolution through fiber spinning of PP/PA6 blend fiber,” Polym Eng Sci, 2017, 65, 107, doi: 10.1002/pen.24686.
- R. Hajiraissi and Y. Jahani: “Non-terminal behavior as a finger print to follow droplet deformation,” Adv Polym Technol, 2017, 298, 9, doi: 10.1002/adv.21810.
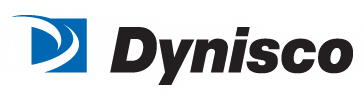
This information has been sourced, reviewed and adapted from materials provided by Dynisco.
For more information on this source, please visit Dynisco.