When working with powders, in-process performance and final product quality will be influenced by the properties of the raw materials delivered to the process. The ability to control these raw materials, and therefore reliably predict process performance, is essential to ensuring the properties and quality of the final product.
Powder flowability is not an inherent material property but is more about the ability of powder to flow in the desired manner in a specific piece of equipment. Successful processing demands that the powder and the process are well-matched and it is not uncommon for the same powder to perform well in one process but poorly in another. This means that several characterization methodologies are required, the results from which can be correlated with process ranking to produce a design space of parameters that correspond to acceptable process behavior.
A method of accurately measuring process-relevant properties of incoming raw materials is therefore highly beneficial to a wide range of applications in various industries. The case study below considers the evaluation of bulk excipients for tableting and the impact of storage and handling conditions.
Variations in Process Performance and Product Quality
Sorbitol is often used as the bulk excipient in the production of a tablet. In this example, a tablet manufacturer was experiencing variation in final product quality when using two batches of sorbitol that had previously been categorized as identical by their supplier. Tablets produced from one batch were consistently softer and less stable than those from the other batch. Following further investigation, the excipient supplier was unable to differentiate between the batches using techniques they had available.
The only difference identified was that the batches had been stored at different locations before being supplied to the customer: the well-performing batch was stored in a silo close to the loading area (Silo 1), and the poorly-performing batch in a Silo further away (Silo 2), necessitating additional conveyance prior to processing.
Samples from both these batches were analyzed using an FT4 Powder Rheometer® (Freeman Technology, UK).
Test Results
Dynamic Testing: Basic Flowability Energy
The sample from Silo 2 generated a higher Basic Flowability Energy (BFE) than the sample from Silo 1. This indicates that it was more resistant to dynamic flow in a confined space (such as in a screw conveying or mixing process) requiring more energy to achieve the same outcome.
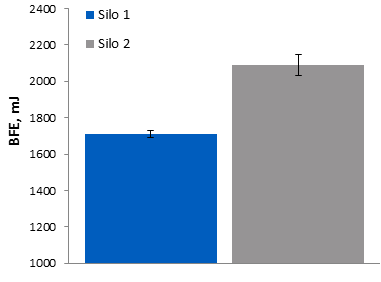
Image Credit: Freeman Technology
Bulk Testing: Compressibility
The sample from Silo 2 was more compressible than the sample from Silo 1, indicating that it entrained a greater proportion of air within its bulk, which is typically a property of more cohesive powders. Higher Compressibility can contribute to poorer behavior in processes where a powder is subjected to an applied force, such as in mechanical feeders or tablet presses, or simply as a consequence of storage in large quantities.
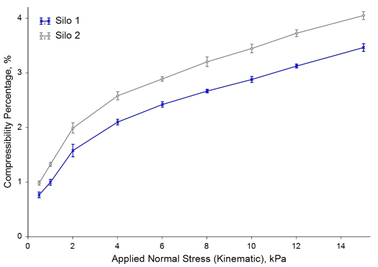
Image Credit: Freeman Technology
Bulk Testing: Permeability
Similarly, the sample from the Silo 2 generated a higher Pressure Drop across the Powder Bed under a constant throughput of air, indicating that this sample was less permeable than the sample from the Silo 1. Low permeability can contribute to poor performance in operations where a powder is required to release entrained air, such as die filling and tableting, and can adversely impact gravitational flow in general.
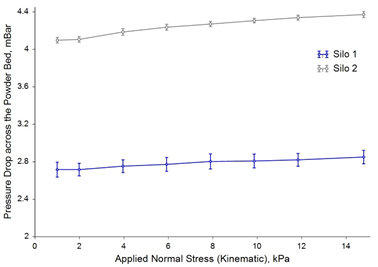
Image Credit: Freeman Technology
Shear Cell Testing
Counter-intuitively, the sample from Silo 2 generated slightly lower Shear Stress values following consolidation at 9 kPa than the sample from Silo 1. This suggests it would more readily transition from a static, consolidated state into a state of flow, such as when required to flow from a hopper. This illustrates how Shear Cell test results may not always be most relevant as the test conditions do not represent what the powder is subjected to in the process. Even when evaluating hopper flow, shear properties alone may not fully describe performance, as Permeability is also known to be influential.
The yield loci for the two samples are non-linear and suggest that the powder from Silo 2 may generate higher Shear Stress values at lower levels of consolidation. Furthermore, due to the location and shape of the yield loci, Mohr circle’s analysis of the data could not be completed as a linear best fit line intercepts the y-axis below zero.
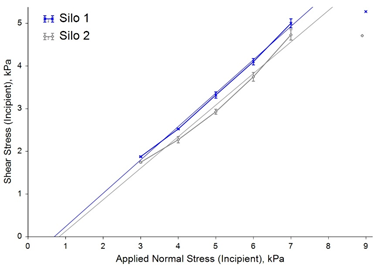
Image Credit: Freeman Technology
Conclusions
The FT4 Powder Rheometer identified clear and repeatable differences between two very similar materials that performed differently in a process. The sample from Silo 2 demonstrates a greater resistance to forced flow (higher BFE), higher Compressibility, and lower Permeability, which are all indicators of greater cohesivity. This information could be used to screen raw materials in order to identify those that are suitable for processing and those that are likely to be problematic. Furthermore, the results demonstrate that Shear Cell testing alone may not provide a reliable representation of powder behavior in this process, due to the differing stress and flow regimes present.
Rather than relying on single number characterization to describe behavior across all processes, the FT4’s multivariate approach simulates a range of unit operations, allowing for the direct investigation of a powder’s response to various processes and environmental conditions.
Please click here for more information about the FT4 Powder Rheometer.

This information has been sourced, reviewed and adapted from materials provided by Freeman Technology.
For more information on this source, please visit Freeman Technology.