An interview with Steve Bowen from Yokogawa Fluid Imaging Technologies on the use of Flow Imaging Microscopy to improve particle analysis of printer toners.
What is particle analysis?
Particle analysis involves taking a sample of a substance and analyzing the individual particles of the sample. The basic goal is to determine the constituents of a mixture and to differentiate between particles in the sample. Typical measurements of particles that are of interest include particle size distribution, particle count, various measurements of particle shape, and particle concentration.
For simplicity, results of a particle analysis are typically reported graphically, with particle size plotted against some other variable. Particle size is often stated as equivalent spherical diameter (ESD), which is an estimated value based on measurements of the particle while assuming the particle is a sphere.
Can you give an overview of volumetric particle analysis?
Rapid particle processing requirements led to the development of several high-volume, indirect measurement techniques such as the Coulter counter, laser diffraction, light obscuration and dynamic light scattering. Indirect calculation of particle size is based on signal profile, where signal is proportional to volume.
There are advantages and disadvantages to volumetric particle analysis. The advantages include the ability to: rapidly determine size and count, obtain statistically significant data, create particle distribution graphs, and procure detailed particle statistics.
The primary disadvantage is that these methods assume that particles are spherical. The analysis is limited to count and size, and shapes cannot be distinguished.
What is Flow Imaging Microscopy?
While volumetric methods are sufficient to calculate particle size, when shape and/or morphological data is needed, a more in-depth analysis is required to truly characterize a particle.
Flow Imaging Microscopy (FIM) combines the benefits of manual microscopy with those of volumetric techniques. Microscopic particle measurements are taken from images quickly enough to produce statistically significant results. Additionally, multiple measurements are taken for each particle, thereby providing the detailed information often needed for a thorough particle analysis. The addition of specialized software also provides sophisticated post-processing of data, and the ability to see real images of your particles, in order to give you an in-depth understanding of your sample.
How does Flow Imaging Microscopy work?
Flow imaging microscopy uses digital images to measure the size and shape of each particle. Essentially, the operator in traditional microscopy is replaced by a computer to extract the information from the images.
The sample containing the particles streams through the flow cell past the microscope optics. Thousands of particle images are captured per second.
To capture sharp images of moving particles, they are “frozen” in space using a strobed illumination source combined synchronously with a very short shutter speed.
As each frame of the camera’s field of view is captured, the software, in real-time, extracts the particle images from the background and stores them.
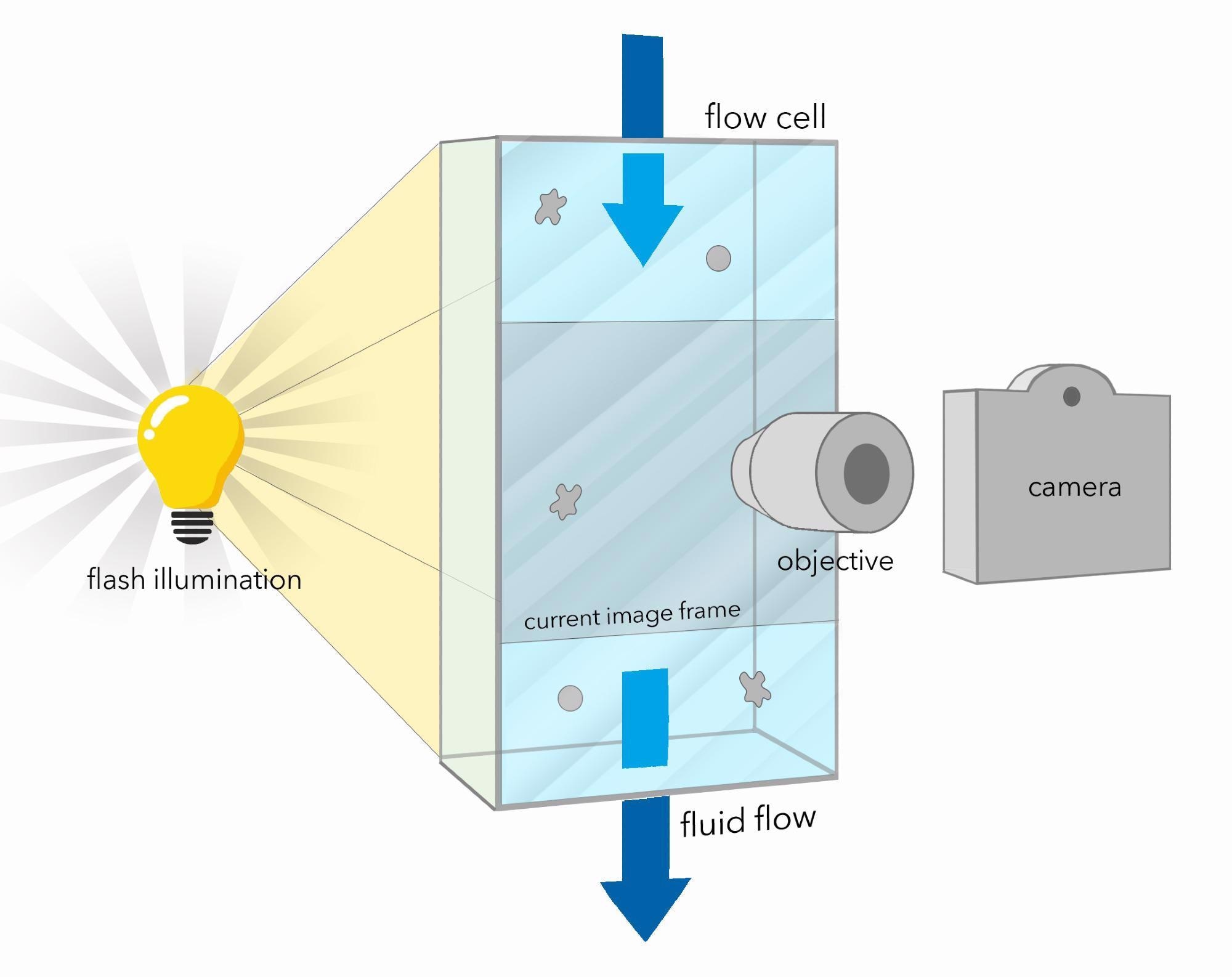
In an imaging-based system, particle measurements are made directly from the image of the particle. Since the system’s optics are fixed and the magnification is known, distance measurements on the image can be directly converted to real distance measurements on the object. No generalizations are made about a particle’s shape. Plus, you can view the image to ensure that the data is being properly interpreted.
Common measurements include equivalent spherical diameter; area-based diameter, length, width, and aspect ratio; area and volume; circularity and elongation; edge gradient; intensity, average intensity, and sigma intensity; transparency, and many more. The FlowCam® flow imaging microscope calculates more than 40 properties for each particle.
Watch a video: How does the FlowCam work?
What might a company be missing if they only rely on volumetric techniques?
In addition to the inability to detect particle shape, volumetric techniques are often limited in their ability to accurately calculate particle size since volumetric techniques assume all particles are perfectly spherical. Elongated particles or irregularly shaped particles adversely impact the math used by volumetric methods when calculating particle size.
These images below are from a customer who was using laser diffraction to characterize the particles in their fluids. They had a sense that the data they were getting was not accurate. Laser diffraction results indicated that there were no particles larger than 65 µm in their samples.
They then asked us to use the FlowCam to run the same samples. In addition to seeing particles that were highly irregularly shaped, the FlowCam found many contaminant particles greater than 90 µm and even greater than 300 µm that were missed entirely by laser diffraction.
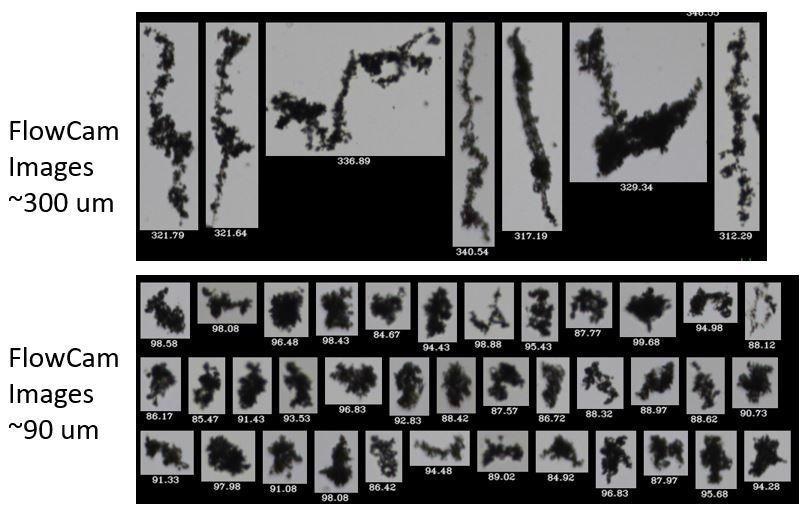
Please give us some examples of how Flow Imaging Microscopy works for the analysis of printer toner.
The size and shape of printer toner particles can considerably impact the image resolution and efficiency of a printer. The consistency of these particles also influences the distribution of charge the particles hold and, as a consequence, can affect overall image quality. Image characterization can help to determine the size, shape, circularity and material uniformity of printer toner particles during and after production.
Software filters can be created to look for toner aggregates, by filtering for low circular fit and circularity properties.
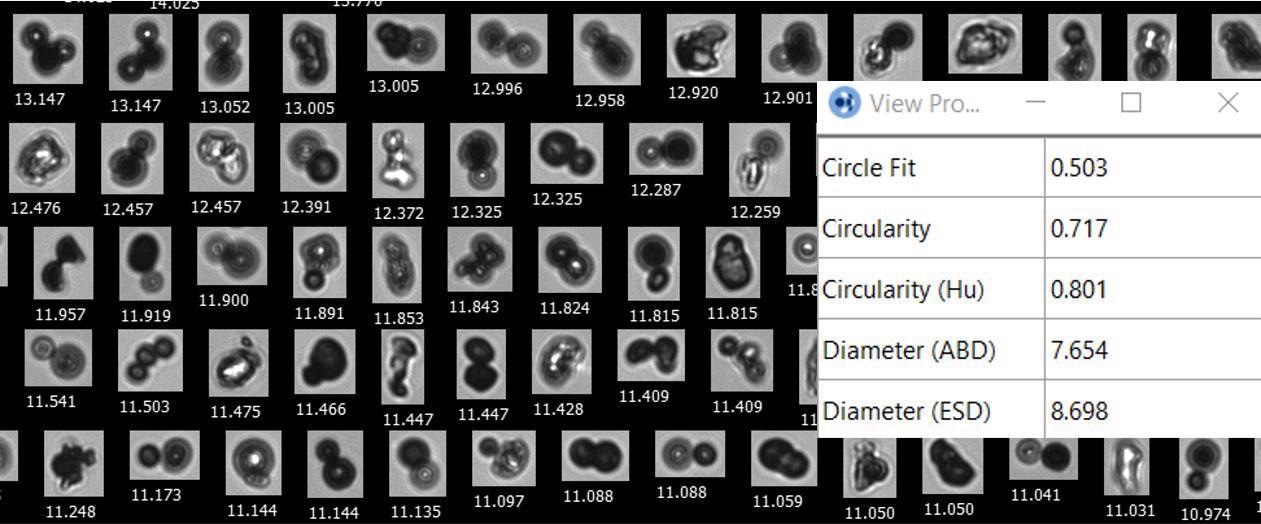
Another reason that FIM is a valuable tool for ink and toner manufacturers is that it gives you the ability to see not only the whole particle size distribution (PSD) but also the ability to analyze specific ranges and outliers separately, which can be done with software filters based upon morphology characteristics.
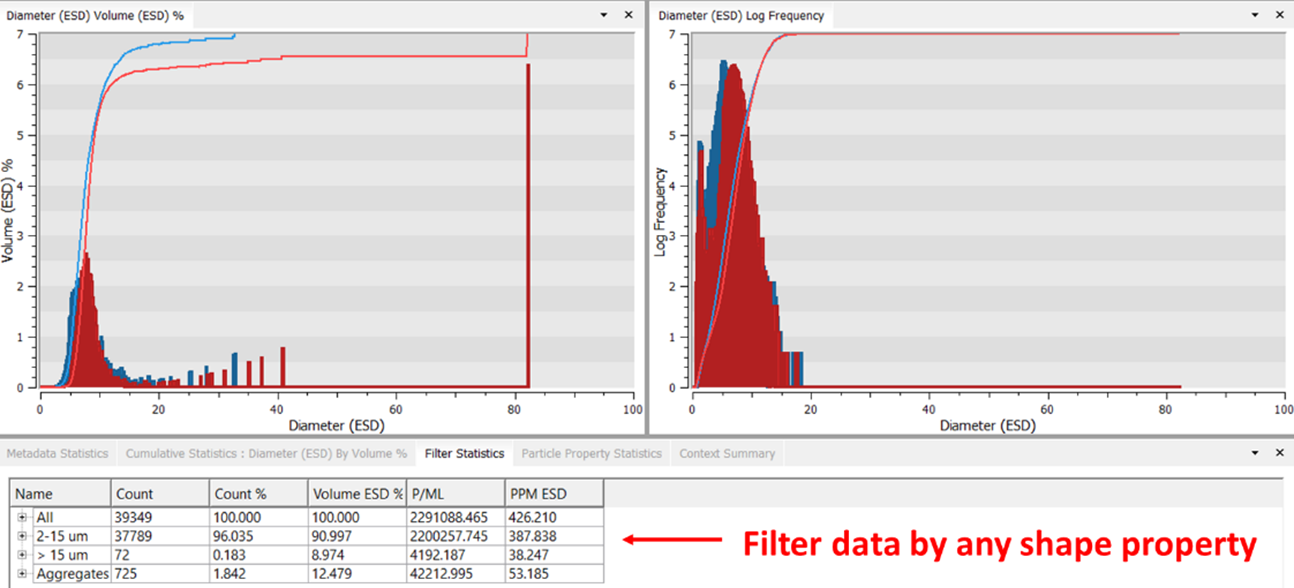
For example, the customer who ran the sample below wanted to evaluate the circularity of toner particles in the 2-15 µm range. A filter was set up for that.
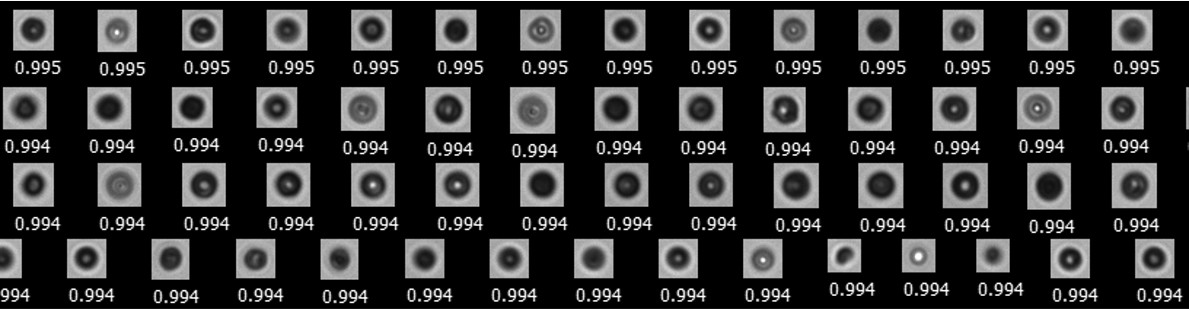
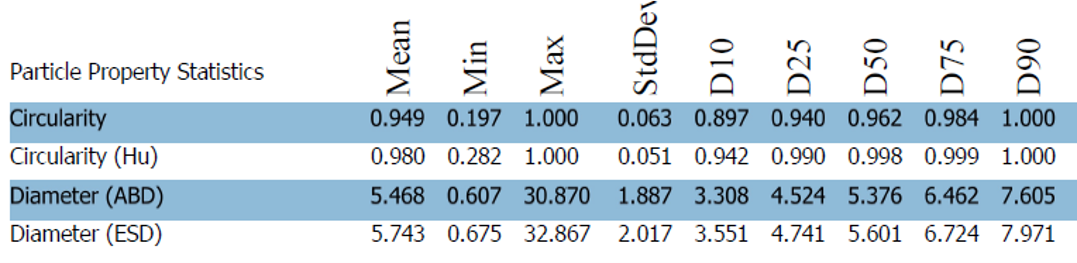
Toner outliers and contaminants can also be easily evaluated. For example, through imaging, one can differentiate between air bubbles and solid particles.
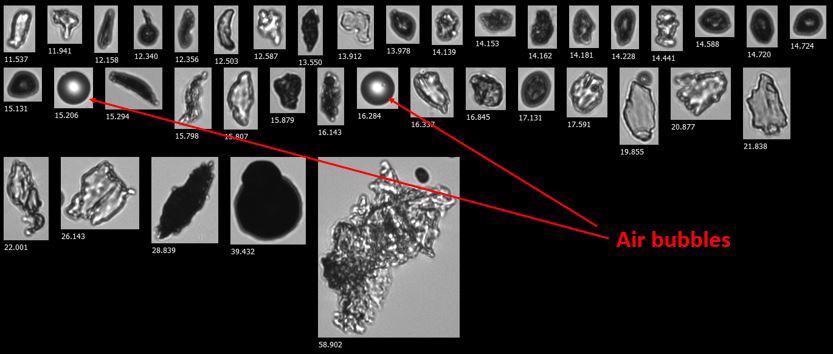
Can you summarize why the FlowCam is better suited for printer toner analysis than volumetric techniques like laser diffraction?
Image analysis enabled by Flow Imaging Microscopy is crucial to the ability to measure particle circularity, one of the principal properties relevant to quality control analysis in the manufacturing of printer toner. Other high-volume particle analysis techniques are able to determine particle size, but since they assume that all particles are spheres, they do not allow for particle shape analysis.
The combination of particle size and shape monitoring, as made possible using the FlowCam, enhances the quality control process essential to printer toner manufacturers. Implementing a QA/QC filter can help assess the general quality of each analyzed sample. The FlowCam is well adapted for a broad range of applications that necessitate rapid, quantitative results. The instrument has an intuitive design that enables an operator to conduct on-site testing of a product with conformational data, statistics and reporting.
About Steve Bowen
Steve Bowen has 30 years of experience in database consulting, product development, marketing, business development, and entrepreneurial startup ventures. He began his
career working in database consulting and application development at Oracle’s professional services practice for various clients in engineering and manufacturing industries. He then moved over to Novell and worked in product management in Novell’s Extended Networks Division developing network-enabled intelligent devices. Steve jumped into the rapidly emerging Internet software industry via a Web startup venture with PartNET, which was ultimately acquired by Medibuy, a healthcare supply chain e-commerce portable. Steve currently serves as the Director of North American Sales for Yokogawa Fluid Imaging Technologies. Steve has a B.S. in Mechanical Engineering from the University of Utah and an M.S. in Manufacturing Systems Engineering from Stanford University.
Disclaimer: The views expressed here are those of the interviewee and do not necessarily represent the views of AZoM.com Limited (T/A) AZoNetwork, the owner and operator of this website. This disclaimer forms part of the Terms and Conditions of use of this website.