In this interview, Lisa Williams, Technical Solutions Specialist from AMETEK Spectro Scientific talks to AZoM about their range of products and technology that can use oil analysis data to reduce ongoing maintenance costs.
Could you start by giving our readers a brief overview of Spectro Scientific’s work?
Ametek Spectro Scientific provides oil and fluid-based predictive analytics solutions. Our instrument and software solutions support the maintenance of critical assets in a range of global end markets including industrial facilities, military and fleet applications.
Our corporate office is located in Chelmsford, Massachusetts. We also have offices in Vienna and Beijing. All three of these offices support operations, sales, customer support, and depot repair. Additionally, our US headquarters supports our research & development and instrument assembly operations.
How important is oil analysis in developing a robust reliability program?
Oil analysis tests like viscosity, elemental analysis, and particle counts are helpful to monitor and trend, even when equipment condition is considered to be satisfactory. Issues detected at this point would be discovered early enough in the failure process to perform any necessary maintenance well before failure, keeping costs of repairs relatively low.
As a machine failure progresses, abnormal wear can be detected and still addressed fairly early in the process to keep costs under control. As we get closer to the machine failing, repair costs tend to increase while also running the risk of lost production time.
It is common to see other predictive technologies paired with oil analysis as part of a complete condition monitoring program. Technologies like vibration analysis and infrared thermography are often paired with oil analysis to provide increased confidence in making critical decisions about a machine. These technologies fit together like a puzzle, each providing information that allow the reliability engineer to make an educated decision about the component.
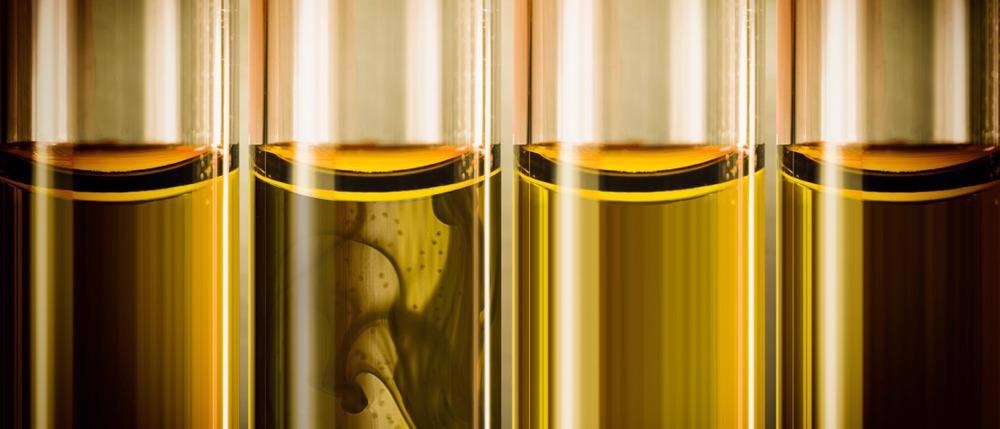
Image Credit: IU Liquid and water photo/Shutterstock.com
What are the common causes of equipment failure?
Equipment can fail due to obsolescence, accidents, and surface degradation. Oil analysis techniques, particularly wear particle analysis, can be extremely helpful in understanding surface degradation. Once we understand what kind of particulate is being generated, we can take action to minimize or avoid it. Ensuring the oil is clean and dry from the beginning of an installation is important in helping to control the wear and prolong the life of the equipment.
How does oil analysis help to avoid these issues and what is the business case for investing in this technology?
Lubricant analysis could be compared to a blood test for humans. If we trend the correct parameters like blood pressure and cholesterol, we gain an overall understanding of our health. If we see deviations in those trends over time, we know to take action and change something in our lifestyles. The same concept can be applied to machinery health when we look at the three key areas of wear, contamination, and chemistry of the lubricant itself. We can use data in these three areas to help us lower costs, reduce unplanned downtime, and increase asset life.
However, it is important that we trend the correct parameters. Determining these parameters involves understanding the organization's maintenance goals.
Around 80% of machine failures are related to dirty oil, so cleaning up oil, using appropriate filtration and monitoring particle counts are a good place to start. It is important to structure a positive business case when trying to get support from an organization to purchase the required instrumentation. Initial buy-in from management is essential. Keep in mind, run to failure is usually the most expensive way to operate, so the numbers typically support the business case for investment.
Between 60% and 70% of industrial facilities use some type of oil analysis as part of their reliability program. While the use of on-site testing is growing, there are still some concerns about bringing lab testing on-site. Because of this, on-site oil analysis solutions need to be simple, efficient, and holistic. Lab equipment operation needs to be turnkey; data should be easy to interpret and understand and reports need to be easy to interpret and implement at the plant level.
Addressing these issues and implementing on-site solutions can remove the waiting period associated with outsourcing samples, allowing organizations to take control of their programs, customize reports, and trend Key Performance Indicators (KPIs) in real-time.
KPIs are measurable values that demonstrate how effectively a company is achieving key business objectives. Strong reliability programs typically have key performance indicators tied to company financial goals.
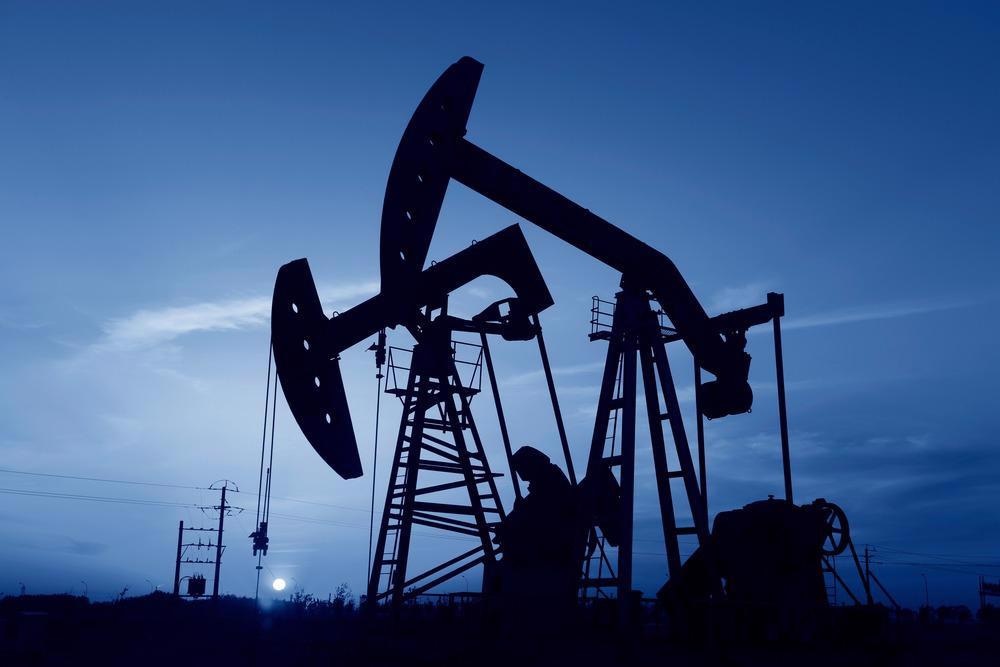
Image Credit: Haizhen Du/Shutterstock.com
Could you give our readers an example scenario of how data can be used to drive decisions around KPIs?
A manager may say that they want to cut maintenance costs by 25%. This is very broad guidance, so we must break that down into a tangible goal(s) we can achieve within our maintenance space.
In practice, this goal could involve increasing the production of machines by 25% and/or reducing oil consumption by 25%, but even then, this is too broad. Questions need to be asked, such as: how are we going to reduce oil consumption by 25%? Are we going to try to extend the time between oil changes? Are we going to sweeten oil when it is necessary instead of just draining the entire reservoir? In terms of production, we could ask; Are we going to monitor contamination and varnish to control uptime of the equipment? We can use data to help us make all of these decisions.
Data is powerful, but we need to use the correct data, and this must be in alignment with KPIs. For example, if we are trying to increase production on a particular machine by 25%, we need to reduce the chances that we will experience unexpected downtime due to improper equipment installation or lubricant contamination issues. Remember, around 80% of machine failures can be traced back to particle contamination, so ensuring minimal contamination of the lubricant will increase uptime.
Once we know what data to trend to achieve our KPIs, we have to choose the right equipment to trend that data.
Spectro Scientific - Using Data to Drive Down Costs
What sort of instruments and equipment are commonly used to help achieve these KPIs?
We can explore this by continuing with our previous example of increasing production by 25%. Increasing production means taking steps to decrease the chances we will experience downtime, so we need to specifically trend parameters like moisture and particle counts that can impact bearing life and cause abnormal wear conditions.
The LaserNet Fines(R) and the FluidScan(R) would be useful tools to have on-site for these specific parameters and it is advisable to also have appropriate filters and desiccant breathers in place to properly clean and maintain the lubricant on a daily basis.
Another common KPI involves zero failures on equipment deemed as "critical". There are many machines that must not experience any failures, for example, a conveyor in a paper mill or an emergency generator in a hospital or power plant. This is a challenging task, but not impossible. Samples may need to be taken monthly and information received must be thorough enough to provide a good overview of the machine’s current condition. In this instance, the MiniLab 153 would be appropriate to trend chemistry, viscosity, particle count, and wear conditions of that particular piece of equipment.
To provide a real-world example, we recently worked with grocery supply chain and logistics firm ES3, located in the United States. This year they have been running their machines nearly 24/7 to meet product demand, using their in-house lab to manage all of their oil samples from the gearboxes that support the cranes and robotics in the facility.
ES3 laid the foundation for their laboratory work with lubrication training through ICML and STLE, earning their certifications and learning about the process of lubricant analysis. They did not purchase a whole system from Spectro Scientific initially, instead they opted to initially purchase a FluidScan and a LaserNet Fines. They later expanded to a full MiniLab 53 system and then added on additional software to manage all of that data.
The MicroLab application can also be used to support fleet maintenance, often resulting in considerable cost savings.
How does the TruVu360 software fit into this process?
The TruVu 360 fluid intelligence software is designed to be used on-site by the maintenance team. It has two components: the TruVu360 software, which is a web-based package where all the data is housed and processed and the TruVu360 Device Console that runs the MiniLab system itself.
The TruVu360 software allows for trending of historical data. It also has diagnostic recommendations and maintenance actions pre-programmed into the software for 31 different component types ranging from hydraulic systems to gas engines. Each of these components have a specific set of rules and alarm limits programmed in the software, all designed to support the maintenance program. The adaptive rules engine feature makes this software unique and the end-user has the ability to change alarm limits and diagnostics statements as needed to reflect the organization's goals.
What role do alarm limits play in ensuring that KPIs are met and programs are justified?
An integral part of meeting KPIs has to do with setting alarm limits that are reasonable while allowing enough time to address the issues at hand. Alarm limits can be one of the most intimidating parts of setting up a program, so we have tried to take the guesswork out of this process using the 31 different component types programmed into TruVu 360.
Selecting the right component type and using the recommended alarm limits is appropriate for many users who may be new to oil analysis. We work with users on both ends of the spectrum, so users who are more advanced and know exactly what alarm limits should be, can program that information into TruVu360.
Additionally, a range of diagnostic statements come preloaded with the software and can be edited as users start to feel more comfortable with understanding the component behavior.
Tracking cost savings is the easiest way to justify reliability programs, so the TruVu360 software allows users to track currency and labor hours in terms of savings per sample. It then keeps a running total on that performance dashboard, so those numbers are available immediately and in real-time.
The software also allows the end-user to add maintenance notes with additional detailed information on the actions that were taken with the equipment once the alarm has been triggered. For example, this alarm may have resulted in an oil change or changing the oil type completely. These maintenance notes allow us to close the loop while providing useful data that can be used to make more informed decisions in the future.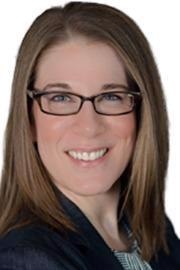
About Lisa Williams
Lisa Williams is a results-focused solution provider working in reliability engineering and tribology for the past 13 years. Specializing in lubricant analysis, she currently serves as a technical solutions specialist on the product management team at AMETEK Spectro Scientific.
She holds STLE’s Certified Lubrication Specialist™ (CLS) certification and also holds the Level I Machine Lubricant Analyst (MLA I) and Level II Laboratory Lubricant Analyst (LLA II) certifications with the International Council of Machinery Lubrication (ICML).
She currently serves as vice chair of the ASTM D02.CS96 Committee for In-service Lubricant Testing and Practices and served as the technical lead on two ASTM standards for in-service grease sampling and analysis, ASTM D7718 and ASTM D7918. Williams holds a bachelor’s of science degree in chemistry from York College of Pennsylvania and a master’s of business administration from Elizabethtown College.
Disclaimer: The views expressed here are those of the interviewee and do not necessarily represent the views of AZoM.com Limited (T/A) AZoNetwork, the owner and operator of this website. This disclaimer forms part of the Terms and Conditions of use of this website.