Milling is a popular and effective top-down process utilized in the production of glass powders, with particle sizes ranging in size from the nanoscale to microns. This article explores a range of milling process types employed in the production of Mo-Sci’s range of specialty glass powders.
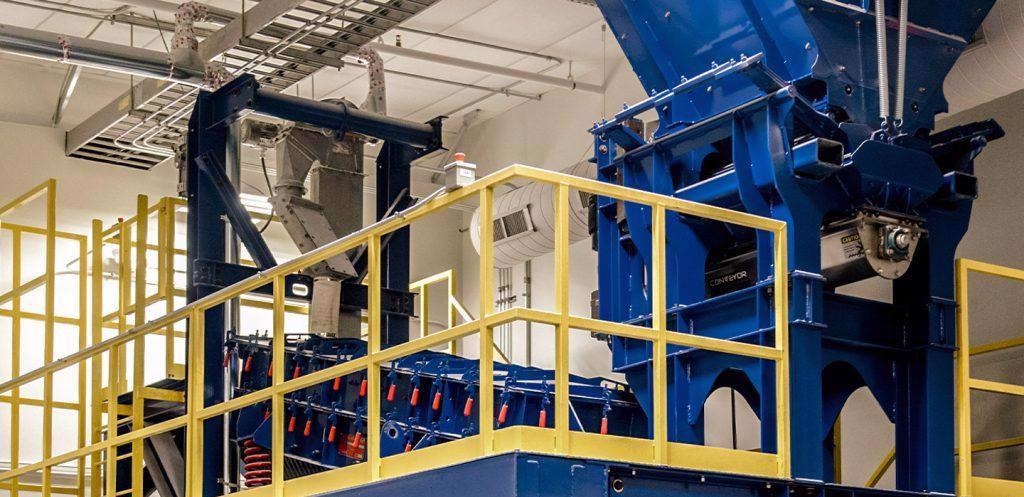
Image Credit: Mo-Sci Corp.
The most common forms of glass provided by Mo-Sci are microspheres, ingots, and glass powder.
Powdered glass, in particular, is central to a range of applications throughout industry and research; for example, glass nanofillers offer distinct benefits to the development of composite materials used in dental and medical prosthetics.1,2
These composites offer excellent strength and superior biocompatibility due to their hydrophobicity, surface roughness, and chemical inertness.
Nanofillers and glass powders can be produced via ‘bottom-up’ methods like the sol-gel process. These techniques are often impractical, however, particularly when producing glass particles that feature complex compositions.3
A ‘top-down’ solution is considered a better option under these circumstances, whereby larger glass particles are broken down into smaller particles in a process referred to as ‘milling.’
It should be noted that in a machining context, the term ‘milling’ has two meanings. This may refer either to grinding (for example, using a ball mill) or cutting (for example, using a CNC mill). This article employs the term in the former sense – referring to grinding processes.
Common Glass Milling Processes
Jaw Crusher
Use of a ‘jaw crusher’ results in the coarsest grind of any process outlined here.
A jaw crusher functions in a similar manner to a standard nutcracker, employing the direct application of compressive force between a pair of mechanical ‘jaws’ to fracture solid materials.
These jaws will generally be arranged vertically, meaning that the gap between them will narrow as material falls through the system.
Particle size will, therefore, decrease as the material moves through the crusher, with crushed material exiting through the narrow gap at the bottom between the jaws once this has been processed.
Jaw crushers are heavy-duty machines typically found in mining and quarry applications. As such, these are well suited to continuous use with materials exhibiting varying degrees of hardness.
Jaw crushers are often used when processing larger fragments of material, but these are unsuitable for fine grinding. Instead, these tools may be employed as a preliminary step prior to controlled grinding using a jet mill or ball mill.
Hammer Mill
A hammer mill (or hammer crusher) offers improved precision over a jaw crusher.
This tool uses hammers to crush aggregate material into smaller particles. It is frequently used for processing organic waste, papers, and foodstuffs, including grain and fruit. Hammer mills are also commonly used to produce glass powder.
Hammer mills are highly durable tools suitable for coarse grinding, and these are available with single or multiple rows of hammers.
Ball Mill
Its adaptability and cost-effectiveness have led ball milling to become one of the most popular and widely used glass milling techniques.
A ball mill for glass processing is comprised of a rotating or vibrating ceramic-lined drum, with several – typically alumina, zirconia, or other durable material – balls inside the drum, forming the grinding medium.
Once the glass is added to the drum, the drum rotates, causing continuous impact and attrition between the balls and the glass, ultimately breaking the glass down into smaller particles.
Ball mills offer excellent versatility and are available in a wide range of sizes. These tools can perform dry or wet milling and are compatible with a diverse array of grinding media.
Ball mills are also able to accommodate batch or continuous processing, while grind size can be adjusted by altering the balls’ diameter.
Industrial ball mills can coarsely crush relatively large material, while lab-grade ball mills are suitable for finely milling glass to the micron level and further. ‘High energy’ ball milling offers users the capacity to reliably grind the material into nanoscale particles.4
Centrifugal Mill
The majority of centrifugal mills are found in labware. A centrifugal mill employs a shearing action between a rotor and a fixed sleeve to break down the material in a relatively well-defined fashion.
These instruments offer extremely high rotational speeds (up to several tens of thousands of RPM), facilitating the rapid, intricately controlled grinding of small batches of material. Sieves allow the extraction of particle sizes as small as tens of microns in diameter.
Jet Mill
The jet mill is a precision piece of equipment that employs a high-velocity flow of gas or compressed air to prompt the collision of glass particles inside a chamber.
Once the particles have reached a small enough size, a process known as cyclonic separation allows particles to exit the gas stream.
Jet mills can be used to continuously mill glass particles until these reach the required size, allowing glass powder to be milled with minimal variation in particle size.5
Similar to ball mills, jet mills can also grind glass powder down to sub-micron particle sizes.
Milled Glass Powders from Mo-Sci
Mo-Sci possesses extensive experience in all these milling methods, allowing the company to offer a comprehensive range of specialty glass powders - including powders exhibiting complex formulations often unavailable elsewhere.
As well as using different types of mills, Mo-Sci employs an array of milling media, including alumina, zirconia, and yttria-stabilized zirconia (YSZ), and perform wet milling in alcohol or water to deliver exceptional results.
References
- Velez, M. et al. Processing of yttrium aluminosilicate (YAS) glasses for dental composites. Cerâmica 57, 1–9 (2011).
- Erol-Taygun, M., Zheng, K. & Boccaccini, A. R. Nanoscale Bioactive Glasses in Medical Applications. Int J Appl Glass Sci 4, 136–148 (2013).
- Vital, A. et al. Ultrafine comminution of dental glass in a stirred media mill. Chemical Engineering Science 63, 484–494 (2008).
- Yang, L. 2 – Nanotechnology-enhanced metals and alloys for orthopedic implants. in Nanotechnology-Enhanced Orthopedic Materials (ed. Yang, L.) 27–47 (Woodhead Publishing, 2015). doi:10.1016/B978-0-85709-844-3.00002-1.
- Wachtman, J. B. Materials and Equipment – Whitewares Manufacturing. (John Wiley & Sons, 2009).
Acknowledgments
Produced from materials originally authored by Krista Grayson from Mo-Sci Corporation.
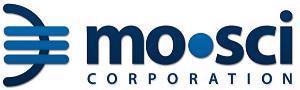
This information has been sourced, reviewed and adapted from materials provided by Mo-Sci Corp.
For more information on this source, please visit Mo-Sci Corp.