Hot rolling processes (Figure 1) tend to produce an oxide layer on the surface of the steel strip. It is necessary to remove this layer – also known as ‘scale’ – prior to performing further processing.
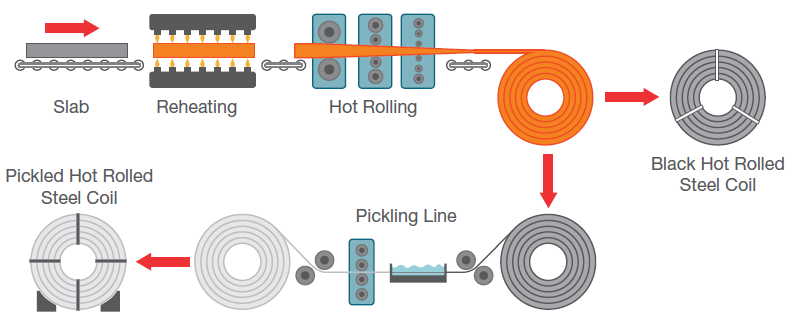
Figure 1. Hot-rolled steel sheet production process. Image Credit: Thermo Fisher Scientific – Electron Microscopy Solutions
Shotblasting may be employed in the removal of scale from hard-to-reach parts or when working with sheet processing like stainless steel. The most common method for oxide scale removal on carbon steels is an acid bath dissolution process known as ‘pickling.’
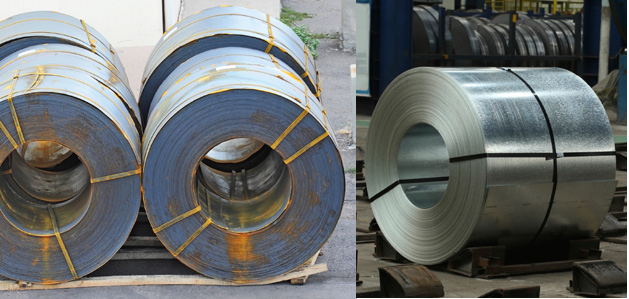
Figure 2. Hot-rolled coils or “black bands” in the left image show black oxide scale formed during reheating and red rust which formed at ambient temperature. The right image shows a hot-rolled steel coil after pickling. Image Credit: Thermo Fisher Scientific – Electron Microscopy Solutions
The pickling process removes surface oxides by immersing a hot-rolled steel sheet in a highly concentrated, temperature-controlled acid solution (Figure 2).
A number of acids are used in pickling processes, such as hydrochloric, sulfuric, nitric and hydrofluoric acids. When working with steel alloys, it may be necessary to utilize a specific combination of acids to optimize material cleaning while preserving the base metal.
Following pickling, the etched steel strip is rinsed in water several times to ensure that no pickling residues remain on the surface. The strip is then dried in warm air.
This article outlines the characterization of a structural steel sample that underwent a pickling process and had been left in the etched condition – meaning there was no oil, phosphate or primer coating present.
Stains were detected after the drying step, however, prompting a further investigation to determine the cause.
Methods
Assessment of the underlying cause was completed using the Thermo Scientific™ Axia™ ChemiSEM – a novel scanning electron microscope (SEM) that offers live quantitative elemental mapping via its always-on energy dispersive X-ray spectroscopy (EDS) capabilities.
This innovative feature allows an operator to view all the necessary elemental information at any time without the need to switch techniques.
Discussion
Figure 3 displays an image of the defective surface. It was necessary to employ both scanning electron microscopy and the chemical information available via EDS to investigate the defect.
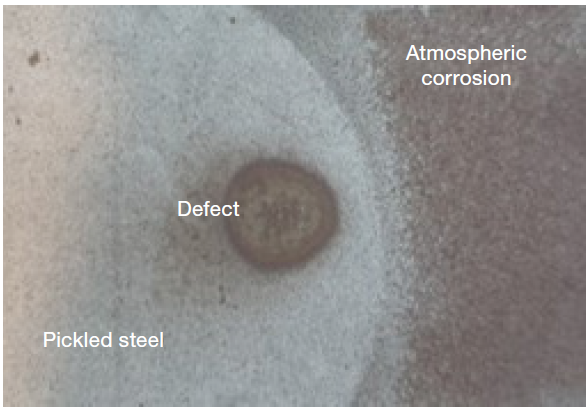
Figure 3. Defective sample. Image Credit: Thermo Fisher Scientific – Electron Microscopy Solutions
This facilitated an assessment of the presence of morphological abnormalities and a comparison of compositional differences with the clean surface.
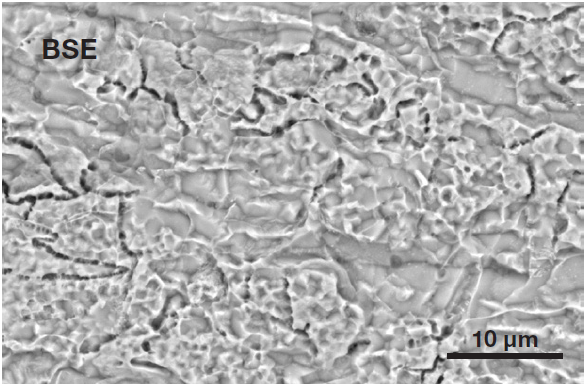
Figure 4. Typical surface of an etched steel (Acc voltage 15 keV, beam current 0.44 nA). Image Credit: Thermo Fisher Scientific – Electron Microscopy Solutions
Figure 4 displays a typical surface of etched steel. To verify the presence of different morphological features, an image was acquired inside the stain spot with the same magnification and acquisition parameters (Figure 5).
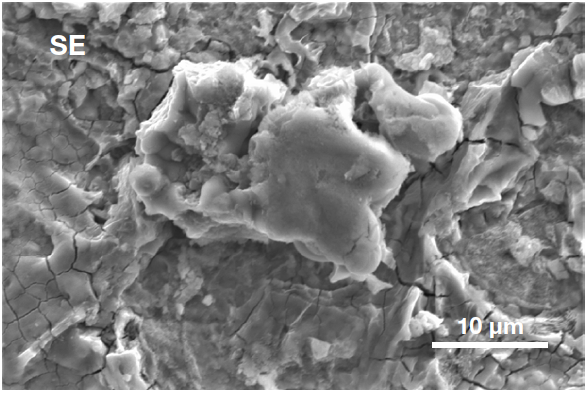
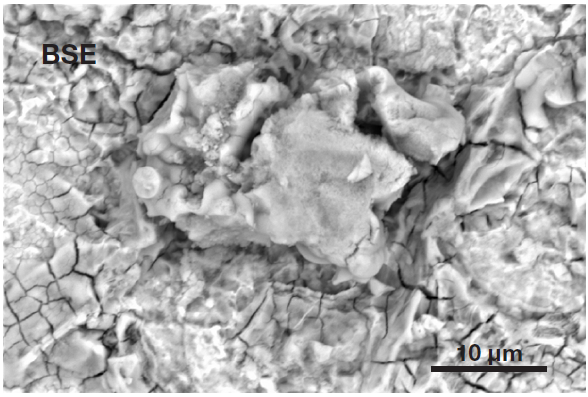
Figure 5. Secondary electron image (top) acquired inside the defective area. It shows the presence of a particle, higher than the surrounding surface, confirming it can be identified as a foreign object. Backscattered electron image (bottom) shows the compositional contrast (Acc voltage 15 keV, beam current 0.44 nA). Image Credit: Thermo Fisher Scientific – Electron Microscopy Solutions
A foreign particle can be seen on the analyzed surface. This is also observable in the secondary electron image, whereby the particle seems to be at a different height to the rest of the surface.
The backscattered electron image illustrates that the compositional contrast offered by traditional SEM imaging is not sufficient to confirm its status as an unknown object or – crucially – to reveal its composition.
The novel approach available via the Axia ChemiSEM means that quantitative elemental information for the area of interest is obtained during the collection of SEM images. This can then be displayed on either the secondary electron or the backscattered electron image (as preferred) with a single click.
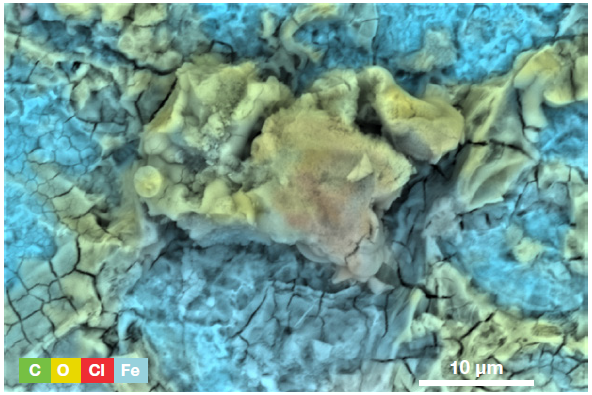
Figure 6. ChemiSEM image of the area displayed in Figure 5 (Acc voltage 15 keV, beam current 0.44 nA, acquisition time 60 s). Image Credit: Thermo Fisher Scientific – Electron Microscopy Solutions
A ChemiSEM image was used to illustrate the distribution of all the elements present (Figure 6). The presence of iron was anticipated, but the presence of oxygen confirms that the sample is oxidized, highlighting where this is occurring.
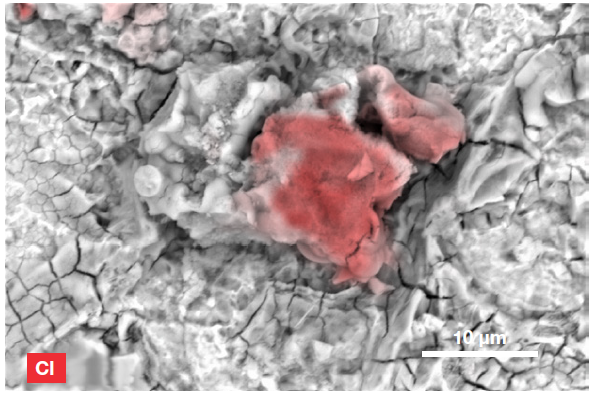
Figure 7. ChemiSEM image of the Cl distribution (Acc voltage 15 keV, beam current 0.44 nA, acquisition time 60 s). Image Credit: Thermo Fisher Scientific – Electron Microscopy Solutions
The presence of chlorine was not expected, however, prompting further investigation. The Axia ChemiSEM allows users to hide certain elements to allow only the element of interest to be shown– this provided an instant confirmation of chlorine distribution.
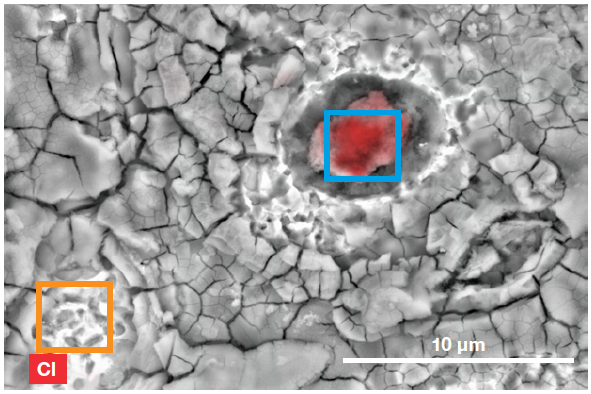
Figure 8. ChemiSEM image showing the two areas used for the region analyses. Image Credit: Thermo Fisher Scientific – Electron Microscopy Solutions
Rapid area analyses were performed on a different foreign particle, as well as on a clean area of the etched steel (Figure 8). This enabled the quantification of contaminants in the stain spot.
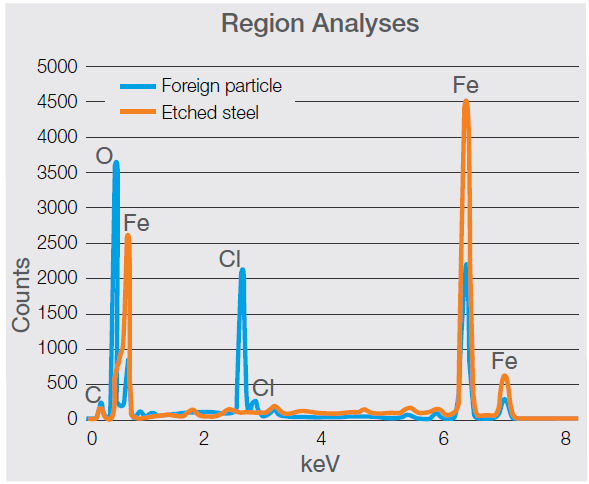
Figure 9. Spectra acquired on the foreign particle and on a clean etched steel surface. The comparison shows the presence of the chlorine peaks (the main peak (Kα) is visible at 2.621 keV) and a higher content of oxygen (Kα at 0.525 keV) in the foreign particle (Acc voltage 15 keV, beam current 0.44 nA, acquisition time 30 s). Image Credit: Thermo Fisher Scientific – Electron Microscopy Solutions
Both the spectrum (Figure 9) and quantifications (Table 1) confirm a distinct difference between the two areas, while the levels of oxygen and chlorine measured in the particle support the likelihood of a foreign object being present.
Table 1. Quantification of the two areas of interest. Source: Thermo Fisher Scientific – Electron Microscopy Solutions
|
Foreign Particle |
Etched Steel |
Element |
Atomic % |
Atomic % |
O |
57.9 |
9.5 |
Cl |
9.8 |
— |
Fe |
32.3 |
90.5 |
Stain spots present on the surface of the sample contained chlorides in a number of areas, indicating that the sample may have been treated with hydrochloric acid and not adequately washed. This may have resulted in droplets of the pickling acid reaching the surface, causing the stain.
Conclusion
Pickling is an essential steel surface treatment, particularly in cases where the steel is required to be uniform and free of surface oxides or stains. The process employs acid solution, which must be followed by a thorough washing step to eliminate any acid contamination on the surface of the steel.
This article demonstrated the characterization of a contaminated surface of etched steel to study the underlying cause of the contamination.
The Axia ChemiSEM enabled a thorough investigation of the defect’s surface morphology and chemical constituents.
A chemical map was created within approximately 1 minute of analysis time, whereby a range of microscopic surface features were colored according to their composition.
The surface stain was quickly found to contain an abundance of chlorides, indicating that a droplet of acid had reached the surface following the competition of the cleaning step.
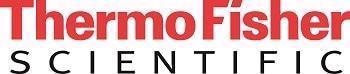
This information has been sourced, reviewed and adapted from materials provided by Thermo Fisher Scientific – Electron Microscopy Solutions.
For more information on this source, please visit Thermo Fisher Scientific – Electron Microscopy Solutions.