The paper or screen upon which this article is read, the way drinking water is pre-treated, the chairs that people sit on, the pain reliever used to alleviate headaches – all of these varied processes and products, along with tens of thousands more, depend on the chemicals industry.
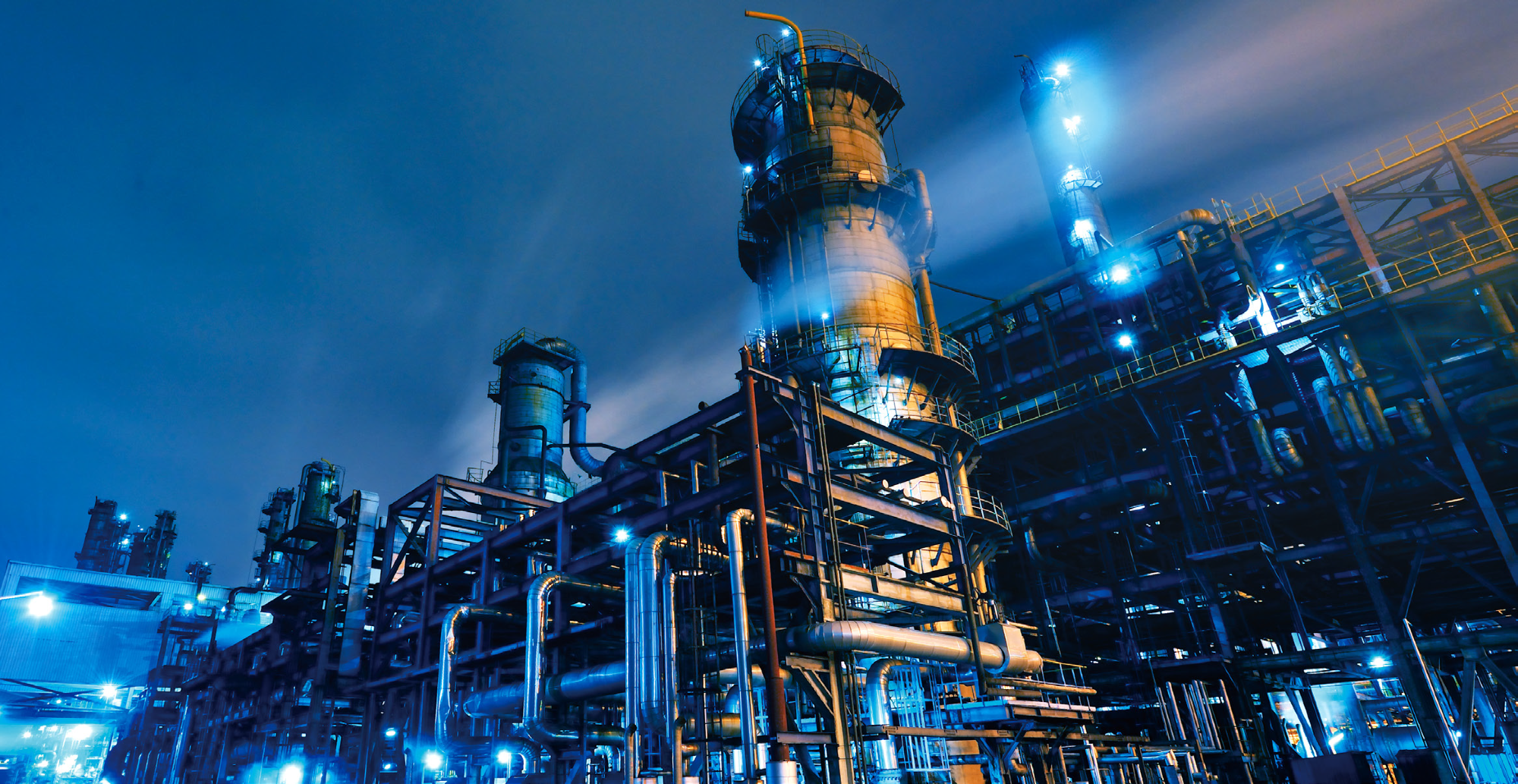
Image Credit: PerkinElmer
The global chemicals industry assists in the manufacture of a huge range of products that are used globally. Certain chemicals become elements of physical products. Others are critical for industrial processes.
Commodity, Fine and Specialty Chemicals
The chemicals industry is categorized into three main fields: specialty chemicals, commodity chemicals and fine chemicals. Commodity chemicals are employed to create fine chemicals. Fine chemicals are combined to produce specialty chemicals with characteristics that are specific to the end use.
The category of commodity chemicals can range from industry to industry. Petroleum and other energy/fuel chemicals are mainly classed as organic commodity chemicals. The chemicals industry generally deems organic commodity chemicals to be those that are mass-created from petroleum.
Commodity chemicals are the foundation materials for the chemicals field. They are mass-created in chemical plants that constantly operate to meet international demand.
- Organic commodity chemicals are based on petroleum (also known as petrochemicals) and are mainly derivatives of benzene. Some examples of commodity chemicals are phenols, chlorobenzenes, aniline, cyclohexane, cumene, xylenes and ethylbenzene.
- Inorganic commodity chemicals are created from metals and different minerals. These elements are utilized to create bases, acids, salts, oxides and additional inorganic chemicals. Examples of inorganic commodity chemicals are potash and caustic soda, sulfuric acid, hydrochloric acid, copper oxide and iron chloride.
Fine chemicals are single, pure chemicals created in tailored batches. The manufacture of fine chemicals is an advanced, multi-stage procedure that must create batches with ultra-high levels of purity and meet strict specifications.
Examples of fine chemicals are active pharmaceutical ingredients (API), proteins and peptides, biocides, steroids and alkaloids.
Fine chemicals are utilized to create specialty chemicals that have distinct features required for their desired end use. A few examples of fields that depend upon fine chemicals are agrochemicals, pharmaceuticals, automotive, electronics, construction and cosmetics.
Specialty chemicals are combinations of two or more fine chemicals that create a blend with a distinct function. Specialty chemicals may be called effect chemicals or performance chemicals as they are designed for action in the end-users application.
A varied range of processes and products depend on specialty chemicals, for example, corrosion inhibitors, catalysts, photography, livestock feed additives, inks, paints, water, waste treatment chemicals and coatings, among numerous others.
History
The modern chemicals industry originated in the early 1800s when the focus was mainly on dyes and explosives. British teenager William Perkin is considered to have founded the organic chemicals industry in 1856.
The young chemist was working on designing a system to synthesize quinine, a natural anti-malarial treatment that was very expensive and in high demand. Perkin experimented with reacting potassium dichromate with various coal-tar derived salts.
After using aniline salt with no success, Perkin noticed that a purple solution formed in an experimental flask when he was using alcohol to clean it. The solution was discovered to permanently and easily dye fabrics – the first coal-tar aniline dye. This marked the expansion of the production and discovery of organic chemicals derived from petroleum.1,2
For many decades, England was the center of the increasing chemicals market, with Germany taking the forefront in the 1880s. During that era, the United States and France also had significant chemicals markets.1
The arrival of World War I gave rise to a further period of substantial growth and innovation in the chemicals market. Hindered supply lines for important medicines and other chemicals prompted this increase in countries across the globe, and a number of new chemicals were founded and produced.3
Innovation continued in this field in the 20 years after World War I ended, such as developments in medicines, polymers and agrochemicals.
The complete commercialization of the new materials, however, was stalled until the Second World War. Examples of ground-breaking chemical production and use in the 1940s were polymers, synthetic rubber, chemical weapons, lightweight aircraft materials and more.4
The agrochemical and pharmaceutical fields were well-established and continued to expand in the 1950s, directly paving the way for organic chemicals.
By the late 1970s, segments for specific fine chemicals and specialty chemicals were established.
The chemicals field has been a part of life-changing developments over the last 40 years, persevering in spite of turbulent international economies and raw materials prices.1,3
The Chemicals Market
For many decades, the pharmaceutical field has been the biggest consumer of fine chemicals. Agrochemicals is another high-volume, long-term customer. The electronics market is a growing driver of expansion in the fine chemicals field.
The global chemicals market reached a profit of 3.94 trillion USD in 2019. Asia has the largest global market share, which has continued since 2012. The largest chemicals producer is China, accounting for around 36% of global sales in 2018, followed by the European Union (EU) at 17% and the United States (US) at 14%.5,6
Table 1. Source: PerkinElmer
Commodity Chemicals |
Fine Chemicals |
Specialty Chemicals |
Single basic chemicals |
Single complex chemicals of ultrahigh purity |
Mixtures of fine chemicals |
High volume production Low cost |
Low volume production (<1,000 tons/year) High cost (>$10/kg) |
Quantities and costs based on end-use industry |
Mass produced in continuous-process plants, using standardized reactions, to meet global demand |
Produced in customized batches |
Blended in customized batches |
Use is based on their versatility as raw materials |
Use is based on specific molecular characteristics |
Use is based on specific functionality |
Fine chemicals constitute the largest segment of the international chemicals market. International fine chemical profits were 155.55 billion USD in 2018 and are predicted to reach 219.49 billion USD by 2024.
North America and Europe lead the way in the production of fine chemicals. Fine chemicals revenues were 36.17 billion USD in North America and 46.31 billion USD in Europe in 2018. The Asia-Pacific region is increasing fine chemical production, particularly in India and China.7
For several years, the pharmaceutical field has been the largest consumer of fine chemicals. In 2016, fine chemical purchases by the pharmaceutical field were 78.2 billion USD and are predicted to grow to 153.7 billion USD by 2025.
The continual growth is thought to be mainly driven by the aging international population along with a rise in demand for preventive healthcare solutions.8
The international specialty chemicals field produced 630 billion USD in 2019. It is predicted to increase at a rate of 3.7% between 2020 and 2027. This market growth is being fueled by rising demand for function-specific and high-performance chemicals across the end-use industries, for example, pulp and paper, oil and gas and cosmetics and personal care.
These chemicals are known as specialties as they are created in smaller quantities and are tailored to a handful of applications, different from the majority of fine and commodity chemicals.9
In July 2020, the top five global specialty chemical segments were electronics/electrical, polymers, surfactants, flavors and fragrances and industrial and institutional cleaners.
These segments combined accounted for an estimated 38% of the specialty chemical market. The biggest consumer of specialty chemicals was China, with North America following closely. In total, they utilize almost 50% of international specialty chemicals.10
The 2020 COVID-19 pandemic has influenced the chemicals field in a variety of ways. As an example, during the second quarter of 2020, BASF experienced a significant decrease in demand from the auto industry for surface technologies, materials and performance and basic chemicals.
Simultaneously, the company’s nutrition and care business profits increased, and agrochemical profits were stable.
The outcome of these disparate activity levels was a total revenue decline of 12% compared to the second quarter of 2019. Other chemical businesses reported equivalent declines in the automotive market with coinciding stability in others.11
Process QA/QC
Table 2. Source: PerkinElmer
Production QA/QC Considerations |
Raw Materials QA/QC |
In-Process Monitoring |
Final Product QA/QC |
- Composition
- Concentration
- Purity
|
- Molecular structure (fine)
- Presence of contaminants
- Phys/chem properties
- Efficiency
- Yield
- Throughput
|
- Composition
- Molecular structure (fine)
- Concentration
- Purity
- Stability
- Phys/chem properties
- Functionality (specialty)
|
The COVID-19 pandemic has also impacted activity within the chemicals industry. Compared to 2019 levels, the number of mergers, acquisitions and sales of chemicals businesses significantly declined during the first half of 2020.
The only major deal reported was the acquisition of BP’s Global Aromatics and Acetyls business by INEOS.12
Challenges
Dependable use and production of chemicals are only attainable when the market’s technical challenges and requirements are effectively met. Certain challenges and needs are relevant to all chemical fields; others are specific to the end use or the segment.
Chemical manufacturing employs a succession of integrated stages that include QA/QC checks during the process, from raw materials to the final product.
The initial stage in all chemical manufacturing workflows is analyzing raw materials for purity and composition before they enter the process of production. As the production process develops, checks are performed at strategic checkpoints to ensure the process upholds high yield, throughput and efficiency.
Fine Chemicals
Fine chemicals have strict customer guidelines, the majority of which are established on end-use regulatory or industry standards. For example:
- The pharmaceutical field is legally required to comply with good manufacturing practices (GMP) during the process of production, including the stability, purity, concentration and composition of active pharmaceutical ingredients (API), packaging materials and inactive components.
- The agrochemicals industry is legally required to comply with strict requirements for active pesticide ingredients, such as stability, purity, composition and concentration.
- The electronics field is ruled by SEMI Standards that specify the ultra-high levels of purity required for chemicals employed in the semiconductor and electronics industry.
In the manufacture of fine chemicals, intermediate chemicals need to be regularly observed for adherence to regulatory and customer standards. The main parameters that are normally monitored for all fine chemicals are:
- Chemical properties
- Molecular structure
- Potential contaminants
Intermediates are also evaluated for batch-specific guidelines. The last batch of every fine chemical production run is subjected to the same analyses performed on process intermediates, along with the calculation of its final concentration and composition, batch-specific requirements, purity, synthesis residues content.
Specialty Chemicals
The increasing range of specialty chemical blends demands even more advanced quality control specifications. Sophisticated analytical instrumentation is required to:
- Validate the purity level of each blend
- Confirm that it meets the functionality specifications needed for its desired end use
- Identify the complex composition of specialty chemical blend
A comprehensive compositional certification should be created and supplied to the customer with the shipment after the final product has been analyzed for each fine or specialty chemical batch.
An integrated analytical platform can record and generate the necessary documentation automatically after each final batch analysis has been completed.
Regulatory Compliance
Manufacturers of chemicals must uphold compliance with all relevant regulatory protocols in their countries of operation and their regions. A number of almost global compliance requirements are detailed below.
Permitting
A business that utilizes materials that are classed as hazardous will need to be permitted to procure, use and store those materials.
The permit outlines the amounts and types of materials that the company can store, obtain and otherwise use in their processes. It also stipulates the reporting, monitoring and record-keeping regulations to keep the permit.
Air permitting is necessary for chemicals manufacturing processes. The permit’s requirements will be reliant on the location of the facility and the content of the air emissions. Air permits outline the reporting, monitoring and record-keeping rules to uphold the permit.
On-Site Materials Management
A materials management plan must be in place for all chemicals found at the chemicals manufacturing facility - both non-hazardous and hazardous.
The plan should outline how the materials will be stored, loaded, unloaded and moved inside the facility, along with containment measures and spill prevention. The plan should include monitoring and maintenance schedules, reporting procedures, spill response plans and record-keeping guidelines.
Table 3. Source: PerkinElmer
Production QA/QC Considerations |
Permitting |
Material Handling and Storage |
Waste Management |
- Hazardous materials
- Air
- Location-dependent permits
|
- Materials management and transport
- Spill prevention and response
- Storm water pollution prevention
|
- Hazardous waste
- Process wastewater
- Other process-related wastes
|
Depending on the extent of outside operations or storage at the facility, a stormwater pollution prevention plan may be necessary. The plan includes analysis and sampling protocols for stormwater discharges, record-keeping and reporting guidelines and remedial action plans.
Off-Site Materials Transport
The transport of manufactured chemicals to the customer and other facilities downstream must be compliant with local, federal and state transportation rules.
Considerations for transport compliance and planning include satisfactory routing for particular classes and/or volumes of chemicals, vehicle and container requirements, and sufficient placarding and other labeling. The transport operator should additionally have sufficient certification and training in emergency response strategies.
Waste Management
Manufacturing facilities of all kinds generate process wastewater and additional process wastes. The processes and materials employed at the facility will dictate the contents of these and other waste streams created by a chemical production facility.
Periodic sampling and analysis, along with a permit from the facility, will be required to discharge process wastewater to an off-site treatment facility.
The treatment facility will outline the guidelines for waste volume and content restrictions, reporting and testing.
Certain chemicals manufacturing facilities utilize on-site operations for the treatment of wastewater. The treated water can then be released to a nearby system or as a point-source discharge to a local body of water.
For both choices, permits are required and will involve analysis and sampling, content and volume restrictions, reporting and other regulations specific to the region.
Contaminated or off-specification materials are another example of process wastes. Transport, characterization and storage of the wastes must adhere to local, national and state regulations.
If any wastes are categorized as hazardous or otherwise specifically regulated, a special permit may be needed.
The treatment or waste disposal facility will need analytical information on the content of each unique waste stream to validate that their acceptance of the waste adheres to the rules of their operating permit.
Employee Health and Safety
The materials utilized and created at chemicals manufacturing facilities must be directly managed to prevent exposure to employees. Possible methods of exposure are the dermal absorption of chemicals, incidental ingestion of particulates and chemicals and inhalation of volatile and semi-volatile organic compounds and airborne particles.
A detailed exposure prevention and monitoring plan is crucial to adhere to regulatory standards and to safeguard the health of employees. Some of the elements of a successful health and safety program are:
- Target parameters to be observed
- Personal protective equipment (PPE) requirements
- Analytical sensitivity requirements
- Analysis and sampling schedule and SOPs
- Regulatory reporting requirements, schedule and methods
- Remedial action alternatives
- Record-keeping processes
- Additional regulatory-specific guidelines
A consistently executed and well-designed employee health and safety program safeguards employees and helps the business avoid expensive liability lawsuits and regulatory penalties.
Minimizing Environmental Impacts
The environmental impacts of operations should also be considered by chemicals manufacturers.
Along with complying with permitting and other regulatory standards, considering the environmental impact of a facility can increase the sustainability of the operation and manage expenses.
A number of practical steps that can help a business to achieve these goals are:
- The improvement of process controls to decrease air emissions and waste production. This can also control expenditure and maximize production efficiency.
- The use of R&D processes to reduce the usage of possibly toxic materials in the production system. This can decrease waste disposal costs and the requirement for restrictive permit conditions or special permits.
- R&D processes to maximize the recyclability of final and intermediate products. This can contribute to the development of the circular economy and enhance operational sustainability.
Trends
There are many trends that are growing in the chemicals industry. The following are some of the more widely observed trends.
Biobased Materials
Biobased materials are products that are created from biomass (living matter) or by systems that utilize biomass. Research and development in biotechnology have been growing for some time and continue to expand in success and scope.
Even at a time when petroleum prices are low, innovation in biobased chemicals is being fueled by product manufacturer demands for higher-performing chemicals and consumer demand for more sustainable materials.
Biobased commodity chemicals are being created from carbohydrate biomass, providing a new foundation for a sustainable chemicals market.
Utilizing biomass feedstocks in the chemicals industry can assist in decreasing emissions of greenhouse gas while additionally avoiding the variations in the availability and cost of fossil fuel-based feedstocks.
Inventive biotechnology companies are engineering biobased chemicals that can be employed to create materials that are more sustainable. Examples of the varied range of biobased products being created at present include:
- Biopharmaceuticals
- Agricultural biochemicals
- Microbe produced enzymes employed in industrial procedures
- Biobased films for touch screen displays
- Biobased adhesives and coatings
- Biodegradable diapers
- Bioplastic packaging
As the development continues, the chemicals field will likely see enhanced sustainability in their processes which can result in cost savings and higher efficiency.
Pharmaceuticals
The COVID-19 pandemic has had enormous effects on the performance, plans and priorities of almost all industries, including pharmaceuticals. The majority of pharma businesses have shifted the priority of some of their R&D tasks to produce drugs that are effective in treating and preventing COVID-19.
As the pandemic continues, trends that previously existed continue to require the efforts of the pharmaceuticals field.
The rates of chronic disease and the increasing global geriatric population continue to be the main influencers of innovation in the development of pharmaceuticals.
In response to both longer-term medical conditions and COVID-19, the chemicals industry is constantly being challenged to face the growing needs and applications with specialty chemical blends and new fine chemical APIs.
Company leaders in the pharmaceutical industry note that investing in their R&D strategy and successes is a main priority for their businesses now and in the foreseeable future.
They predict their efforts will focus on early detection, non-pharmacological interventions and prevention, along with novel drug therapeutics. The fine chemicals industry will need to continue to offer innovative, highly specific solutions for APIs, diagnostics and preventative treatments.13
The biosimilar drugs market continues to grow as health care payers and consumers demand therapeutics at a lower price. Since 2013, the total amount of biosimilars in the market or under development has increased by 208%.
Biosimilars are very similar but are not specific duplicates of brand-name drugs as they do not have matching ingredients.
Biosimilars have to be tested and proven to offer the same clinical and therapeutic outcomes as the brand-name drug to be approved for market.
The chemicals industry will continue to be depended on to supply innovative fine chemicals to allow continual expansion in biosimilar availability, development and efficacy.14
Chemicals Recycling
The terms advanced recycling, transformational technologies and chemical recycling are utilized interchangeably.
The chemical recycling of plastics is where used plastics are broken down into one or more of their initial building blocks that are then employed as feedstocks to synthesize different chemicals. The term chemical recycling distinguishes the technique from conventional mechanical recycling of plastics.
Mechanical recycling is successful for purer and more modern plastics, for example, water bottles.
More advanced plastics — such as unsorted plastic waste, multi-layer plastics, or heavily contaminated plastics — are not suitable for mechanical recycling, which is where chemical recycling is most effective.
Advanced recycling employs heat or solvents to disintegrate the plastics for further use. This significantly decreases the volume of plastic waste that needs to be disposed of through burning or landfilling. Combined with the successes of mechanical recycling, this reduces the use of non-renewable resources like petroleum.
The chemicals manufacturing field is slowly increasing its use of recycled raw materials. Certain businesses are even building plastic recycling processes into their facilities of production. These practices will progress the development of the circular economy and strengthen the industry.
The three main techniques for advanced recycling are:
- Depolymerization breaks the molecular bonds of the plastic to release its monomer building blocks so that they can be utilized for other chemical syntheses.
- Conversion breaks the molecular bonds of the plastic and recombines the molecules to produce chemical feedstocks and hydrocarbons similar to organic commodity chemicals.
- Purification utilizes a solvent to dissolve the plastic to allow additives to be removed, creating a purified polymer resin.
Nanotechnologies
Some exciting developments to the chemicals industry are being introduced by the production of an ever-increasing amount of nanotechnologies, including the use of nanoparticles in drug delivery and as catalysts.
Catalysts
Catalysts are relied upon in the chemicals industry to improve reaction times during the production workflow. Developers of nanotechnology aim to create catalysts that are highly active and selective while having long lifespans and low energy requirements.
These performance characteristics are attained by carefully evaluating the primary physical and chemical characteristics in the development of particles, for example:
- Shape, size and spatial distribution
- Electrical structure and surface composition
- Chemical and thermal stability
In the fine chemicals industry, nanocarbon particles are being utilized as catalysts.
Compared to conventional carbon materials, nano-sized carbon particles have advantages due to new research into nanocarbon curvature, heteroatom doping, optimized electron transfer and confinement.
Additional kinds of nanocatalysts are being designed for industrial use, including those based on oxides and metals.15,16
Table 4. Source: PerkinElmer
Carbon-based Nanocatalysts |
Metal-based Nanocatalysts |
- Graphite
- Graphene
- Carbon nanotubes (CNT)
- 3D porous nanocarbons
|
- Platinum group metals
- Titanium, Cobalt, Silver, Iron, Aluminum, Nickel, others
- Metal oxides
|
Drug Delivery
For a number of pharmaceutical therapies, nanoparticles are being utilized as drug delivery systems. Metals, lipids, carbon and polymers are some of today’s frequently employed materials for drug delivery nanoparticles.
Nanoparticle systems offer many benefits compared to conventional delivery techniques like capsules and tablets. The advantages include:
- Reduced cytotoxicity
- More specific targeting
- Sustained and controlled release
- Delivery of drugs that are poorly soluble
- Improved bio-distribution and metabolism
Nanoparticle delivery systems continue to solve challenges in drug therapies, for example, accurately characterizing molecular targets, overcoming drug resistance in target cells and moving drugs across the blood-brain barrier.16,17,18
Industry 4.0
Industry 4.0 is being referred to as the fourth industrial revolution, and for good reason. Industry 4.0 is the combination of an advanced digital technology platform with the physical manufacturing operations of a facility, producing a flawless integrated system across processes.
Real-time continual data acquisition is offered by the physical-digital interconnection that strengthens communication across the system.
The advanced analytics of the platform evaluates the data and creates automated control actions and insights that are critical for business and operational parameters such as:
- Energy efficiency
- Workflow optimization and QA/QC
- Safety management
- Supply chain management
- Preventative maintenance
Industry 4.0 is gradually being adopted by the chemicals industry. The research and development of new or enhanced products is one field that has begun to use the integrated system.
The advanced analytics platform can utilize materials parameters and historical data to limit R&D failures, perform product simulations and improve the efficacy of laboratory testing.
Summary
The chemicals industry has undergone significant innovation and growth across the last 150 years. It will undoubtedly continue to develop as novel materials, technologies and end-uses are designed within the various fields that depend upon chemicals.
Advanced analytical platforms and capabilities will be a fundamental part of the success of the chemicals industry and the companies that it supports.
References
- Michigan State University. 2020. Chemicals: Background. https://globaledge.msu.edu/industries/chemicals/background
- Science Museum. 2018. Mauve Mania. https://blog.sciencemuseum.org.uk/mauve-mania/
- Syntor. 2019. The History of Fine Chemicals UK. https://actylis.com/
- Smith J.K. 1988. World War II and the Transformation of the American Chemical Industry. https://doi.org/10.1007/978-94-017-2958-1_2
- Statista. 2020. Revenue of the chemical industry worldwide 2002-2019. https://www.statista.com/statistics/302081/revenueof-global-chemical-industry/
- European Chemical Industry Council. 2020 Facts & Figures of the European Chemical Industry. https://cefic.org/app/uploads/2019/01/The-European-Chemical-Industry-Facts-And-Figures-2020.pdf?utm_campaign=POLITICO-Promotion-2020---Competitive-Europe&utm_source=POLITICO-OpEd&utm_medium=post-organic&utm_content=Facts-and-Figures-2020&utm_term=Europe_cefic_Anyone_Campaign_Reach_POLITICO_Promotion_2020_-_Competitive_Europe__1-2019042_post-organic_Facts-and-Figures-2020
- Absolute Reports. 2019. Global Fine Chemicals Market 2019 by Company, Regions, Type and Application, Forecast to 2024. https://www.absolutereports.com/global-fine-chemicals-market-14427113
- Grandview Research. 2017. Pharmaceutical Fine Chemicals Market Worth $153.7 Billion by 2025. https://www.grandviewresearch.com/
- Grandview Research. 2020. Specialty Chemicals Market Size, Share and Trends Analysis Report By Product (Institutional & Industrial Cleaners, Flavor and Fragrances, Food and Feed Additives), By Region, And Segment Forecasts, 2020 – 2027. https://www.grandviewresearch.com/industry-analysis/specialty-chemicals-market
- HIS Markit. 2020. Overview of the Specialty Chemicals Industry. https://www.spglobal.com/commodityinsights/en/ci/products/specialty-chemicals-industry-scup.html
- Chemical and Engineering News. 2020. Chemical Companies Preview Second-Quarter COVID-19 Impact. https://cen.acs.org/business/economy/Chemical-companies-preview-second-quarter/98/i28
- PWC. 2020. Chemicals Deals Insights Midyear 2020. https://www.pwc.com/us/en/industries/industrial-products/library/chemicals-deals-insights.html
- Deloitte. 2020. Biopharma Leaders Prioritize R&D, Technological Transformation, and Global Market Presence. https://www.deloitte.com/uk/en/Industries/tmt/about.html?id=gb:2ps:3gl:4always-on-global-search:5:6abt:20240320::&gad_source=1&gad_campaignid=22302611259&gbraid=0AAAAABR9RflhgqdAeao1s29MofRXNSEx8&gclid=CjwKCAjw6s7CBhACEiwAuHQckgxeOygeya8xQbVuLoaTOi0Imh_1sYJe2MTYSx0dsZQLNSEOkgoz4hoCLx8QAvD_BwE&gclsrc=aw.ds
- Cancer Treatment Centers of America. 2018. What’s the Difference? Biosimilar and Generic Drugs. https://www.cancercenter.com/
- Figueiredo, José. 2017. Application of Nanocarbon Materials to Catalysis: Applications in the Chemical Industry, Energy Development, and Environment Protection. https://doi.org/10.1002/9783527699827.ch3
- National Nanotechnology Initiative. 2020. Benefits and Applications. https://www.nano.gov/you/nanotechnology-benefits
- Ghaffari, Maryam et al. 2019. Industrial Applications of Nanomaterials, Chapter 17: Nanotechnology for pharmaceuticals. https://doi.org/10.1016/B978-0-12-815749-7.00017-7
- Moghis, U. Ahmad et al. 2012. Lipids in Nanotechnology, Chapter 7: Applications of Nanotechnology in Pharmaceutical Development. https://doi.org/10.1016/B978-0-9818936-7-9.50010-X
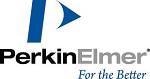
This information has been sourced, reviewed and adapted from materials provided by PerkinElmer.
For more information on this source, please visit PerkinElmer.