The rising use of carbon fiber composites in high-volume manufacturing drives the demand for real-time cure state knowledge. Dielectric cure monitoring is the only technique that can examine material properties during manufacturing, also known as dielectric analysis or DEA.
A previous study has shown that this technique can shorten average SMC press cycle times by identifying the end of the cure. The 10-second decrease in SMC molding time, attributed to DEA, was estimated to save $70,000/year/press in labor costs compared to a timer set at 60 seconds.1
Filters are typically needed for dielectric sensors to block conductive fibers and prevent electrode short circuits. However, filters must be avoided in quick, repetitive operations because they require manual replacement after each test and add time, effort, and expense.
Carbon+Unitrode sensors from Lambient Technologies have a tough, insulating coating that permits direct contact with carbon fiber composites for cure monitoring without filters. To monitor the entire cure and determine when it is safe to open a press or mold, manufacturers can use Carbon+Unitrode sensors.
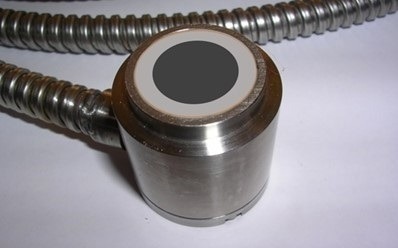
Figure 1. Carbon+Unitrode-1” coated, reusable sensor. Image Credit: Lambient Technologies
What is Dielectric Cure Monitoring?
The AC electrical resistivity and permittivity of a material, which change as the material cures, are measured by dielectric cure monitoring. Both the frequency-independent (ρFI) and frequency-dependent (ρAC) components of resistivity are important for monitoring the progress of a cure. The degree of polymerization before gelation affects ρFI by affecting ion mobility and mechanical viscosity.
The change in mechanical viscosity and the change in ρFI are proportional for many materials. To highlight this connection, the term “ion viscosity” (IV), also known as “AC ion viscosity” (IVAC), was created as a shorthand for “frequency independent resistivity” and is defined as follows:
(Eq. 1) |
IV = ρFI |
(ohm-cm) |
Data for log (ion viscosity) and slope of log (ion viscosity), which denote the degree of cure, are presented and discussed in this article. The plots display distinguishing characteristics such as minimum ion viscosity, the maximum slope of log (ion viscosity), and the time left until a chosen end of cure.
For the sake of simplicity, log (ion viscosity) will be referred to as log (IV), and log (ion viscosity) slope will be referred to as slope.
Cure Monitoring with the Carbon+Unitrode-1” Coated Sensor
Both carbon fiber sheet molding compound (CF-SMC) and carbon fiber reinforced prepreg (CFRP) use carbon fibers’ high strength and low weight. However, direct contact between conductive fillers and dielectric sensors runs the risk of short-circuiting electrodes and interfering with the measurement.
Since McIlagger2 first described depositing an insulating layer on electrodes to prevent fiber contact, others have used it to research how carbon fiber composites cure. CFRP and CF-SMC cure monitoring is made possible by the reusable Unitrode-1” dielectric sensor of Figure 2 and its Carbon+ coating.
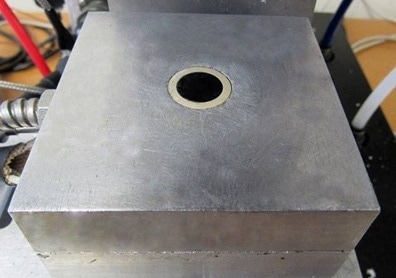
Figure 2. Carbon+Unitrode-1” coated dielectric sensor in press platen. Image Credit: Lambient Technologies
A lay-up using the Carbon+Unitrode sensor is shown in Figure 3. The electrode is permanently bonded to a non-porous insulating layer, preventing it from touching conductive fibers.
Consequently, a composite can be applied to the sensor without a filter. The electric field from the electrode passes through the insulating layer into the composite in Figure 4’s cross-sectional view of this lay-up.
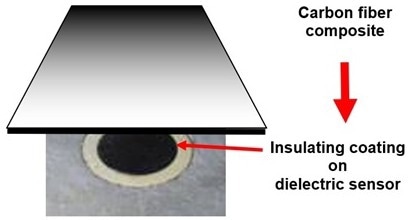
Figure 3. Typical lay-up with a Carbon+Unitrode sensor. Image Credit: Lambient Technologies
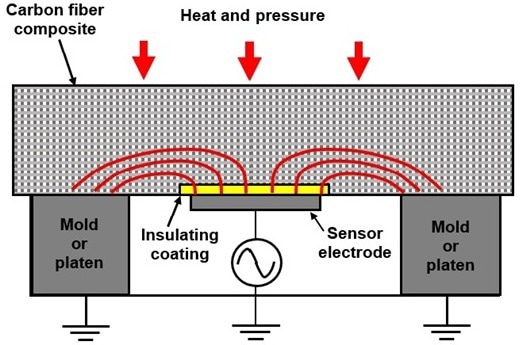
Figure 4. Cross section of lay-up with coated sensor, showing electric field (red). Image Credit: Lambient Technologies
A blocking layer, or capacitor, is introduced between the electrode and the material tested by the insulating coating. Cure monitoring with coated sensors is not conceivable with DC methods because capacitors only pass AC signals.
Dielectric measurements with a carbon fiber composite placed directly on the electrode combine the contributions of:
- The time-varying conductance of the resin as it cures
- The blocking layer capacitance
- The unknown and time-varying conductance between the carbon fibers and the resin
- The fixed conductance of the carbon fibers
On a Carbon+Unitrode sensor, Figure 5 shows the log (IV) and slope during the two-stage curing of a carbon fiber reinforced prepreg. A heated press operating at 120 °C applies pressure to the CFRP, which is in direct contact with the sensor for the initial stage. The second stage’s dielectric response occurs at 190 °C and is consistent with the typical behavior of the thermosets.
The mechanical and ion viscosities of the resin rapidly decrease with the abrupt temperature rise. The material has the lowest mechanical and ion viscosity for a brief period before the curing reaction takes control of the response - in this case, after about 70 minutes - and mechanical and ion viscosity begin to rise.
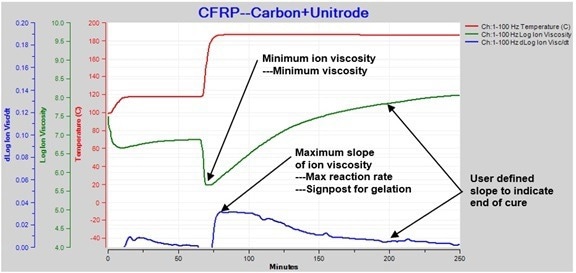
Figure 5. Cure of CFRP in direct contact with Carbon+Unitrode-1” sensor. Image Credit: Lambient Technologies
Mechanical viscosity increases quickly during gelation and eventually becomes unmeasurable. Although the time of maximum slope can be used as a signpost that can correlate with gelation, gelation is a mechanical event rather than an electrical one, so no dielectric features indicate the gel point.
The ion viscosity curve flattens, and its slope approaches zero as the reaction ends. The end of cure in manufacturing is a user-defined slope based on the application's demands. Dielectric cure monitoring equipment can send a signal to automatically open a press or mold once the end of the cure has been determined.
Cure Monitoring with a Filtered Unitrode-1” Sensor
A carbon composite sample is placed on a filter in Figure 6, which then covers an uncoated Unitrode-1 sensor. Filters to block fibers and pass resin to dielectric sensors are the preferred handling method for carbon fiber composites as they enable precise observation of the cure state. Porous paper, fiberglass felt, or other appropriate materials can be used as filters.
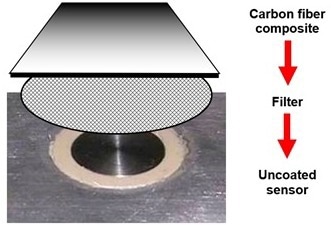
Figure 6. Typical lay-up with filter on an uncoated sensor. Image Credit: Lambient Technologies
The resin flows from the sample into the filter after heating and compression. Figure 7 depicts a cross-section of the lay-up and demonstrates how the filter, which is non-conductive and has little impact on the electrical response, is penetrated by the electric field from the electrodes.
As a result, dielectric measurements using a filter primarily identify the resin and correctly describe the material’s condition.
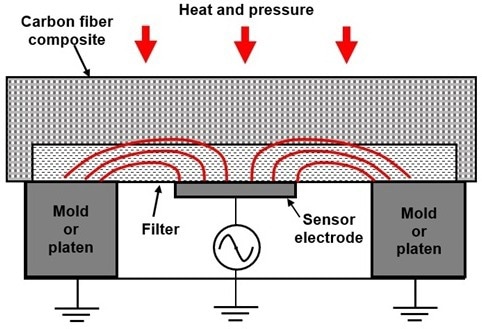
Figure 7. Cross section of lay-up with filtered Unitrode sensor, showing electric field (red). Image Credit: Lambient Technologies
The slope and ion viscosity of CFRP, as measured by the filtered and coated Unitrode, are compared in Figure 8.
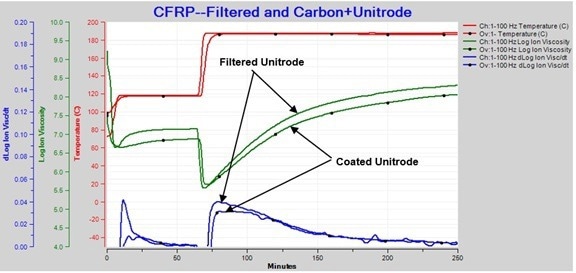
Figure 8. Comparison of CFRP data from filtered and coated Unitrode sensors. Image Credit: Lambient Technologies
The ion viscosity curves for the two sensors are nearly identical, except for a slight level difference. The additional conductivity of the carbon fibers, which would reduce the ion viscosity measured with an unfiltered, coated sensor, may be the source of this variation.
However, the slope curves mostly overlap, indicating that the coated Carbon+Unitrode can measure the cure state of carbon fiber reinforced prepreg and other carbon fiber composites just as well as a filtered sensor.
References
- Day, D.R. and Lee, H.L., “Analysis and Control of SMC Part to Part Variations,” Session 13-C of Proceedings of the 17th Annual Conference, Composites Institute, the Society of the Plastics Industry, Inc., Feb 3-6, 1992
- A. McIlhagger, D. Brown, B. Hill, “Development of a dielectric system for the on-line monitoring of the resin transfer moulding process,” Composites Part A Applied Science and Manufacturing, 31(12): 1373-1381, December 2000
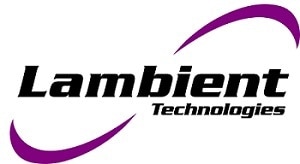
This information has been sourced, reviewed and adapted from materials provided by Lambient Technologies.
For more information on this source, please visit Lambient Technologies.