Historically, FTIR gas analyzers were only capable of measuring down to the mid parts per billion (ppb) range.
However, new advances in FTIR gas analysis technology now allow for routine impurity measurements at low parts per billion (ppb) to mid parts per trillion (ppt) level. This means that optically enhanced FTIR (OE-FTIR) can rival the sensitivity of gas chromatography based techniques with faster analysis times and a lower cost of ownership. In this interview, AZoM spoke with Martin Spartz of Thermo Fisher Scientific to find out more.
Please could you introduce yourself and your role at Thermo Fisher Scientific?
My name is Martin Spartz, and I have a Ph.D. in analytical chemistry from Kansas State University. I co-founded the company Max Analytical Technologies, which was recently acquired by Thermo Fisher Scientific.
I am now the Senior Director of Gas Analysis R&D at Thermo Fisher Scientific. My research focuses on developing next-generation FTIR gas analysis systems that can measure ultra-trace levels of components in complex samples.
How does your research help support the development of next-generation FTIR analysis?
In our Gas Analysis Solutions group at Thermo Fisher Scientific, we have developed a new ultra-sensitive technology that allows us to measure into the ppt range for impurities in things like bulk and specialty gases.
Our Thermo Scientific™ MAX-iR™ FTIR Gas Analyzer is a compact industrial gas analyzer. It is a 5U rack-mounted design and was developed with minimal maintenance in mind. The spectrometer comes equipped with a series of unique characteristics.
First, there is a single crystal zinc selenide beamsplitter that gives the system very high thermal stability and greater baseline stability to allow for very low-level measurements.
Instead of using a helium-neon laser, the system uses a vertical cavity surface emitting laser (VCSEL) diode laser. This allows the instrument to run for 10 to 20 years with very little maintenance, which is ideal for process and environmental applications.
The MAX-iR analyzer is configured with one of three detectors. A DTGS (deuterated triglycine sulfate) detector, comes standard in the system, which allows for the measurement of the entire mid-infrared spectrum. In a sense, that means it is possible to measure all organic and inorganic gases that might be in a sample.
Detection limits for a DTGS detector coupled with the MAX-iR gas analyzer are in the tens of ppb range. If lower levels are required, an MCT (mercury-cadmium-telluride) or an InAs (indium arsenide) detector is utilized. The MCT and InAs detectors are thermoelectrically cooled and do not require liquid nitrogen for operation.
These detectors are then coupled with optical band pass filters or long pass filters to get the highest signal-to-noise ratio in the lowest detection limits possible. These configurations demonstrate sensitivities three orders of magnitude lower into the tens of parts per trillion.
What unique characteristics does the system have over other existing systems?
The MAX-iR gas analyzer has a number of unique and interesting characteristics. First, it uses aspherical optics in the gas cell to ensure the highest light throughput possible.
Secondly, the gas cell and associated mirrors are designed to run from vacuum to 10 atmospheres, and they do it dynamically so the pressure can be changed in the gas cell while carrying out the measurements.
There is also the Thermo Scientific™ StarBoost™ Optical Enhancement Technology, that produces the highest sensitivity possible for an FTIR gas analyzer. This technology, in particular, was the genesis for the term optically enhanced FTIR which we abbreviate as OE-FTIR.
Can you tell us a bit more about what StarBoost Technology really is?
StarBoost technology is what gives the MAX-iR gas analyzer a very high signal-to-noise ratio that allows users to achieve such ultra-low measurements. It works by taking a very high D* detector and coupling it with an optical filter. The optical filter removes all the frequencies that are of no interest for a specific measurement.
For example, if we were to measure one compound, say HCl, we could configure the instrument to only look at regions of the infrared spectrum where HCl absorbs. By doing that, the detector becomes significantly more sensitive because we limit the amount of light hitting the detector. With this reduced amount of light reaching the detector, we can increase the detector gain and actually get even more signal-to-noise.
Can you provide a brief overview of how the system operates?
The MAX-iR is an FTIR-based gas analyzer. The main components in an FTIR gas analyzer are an infrared emitting source, an FTIR spectrometer, a multiple pass gas cell ("White Cell") and an infrared sensitive detector. The gas cell in the MAX-iR analyzer has 48 passes and a pathlength of 9.86 m, with a volume of < 500 mL.
Samples are sent to the gas cell at flows between 0.5 and 10 liters per minute, while infrared spectra are continuously collected by passing the IR beam through the gas cell with the sample present and onto the detector.
Any organic or inorganic gas present in the gas cell will absorb a portion of the IR light. The frequency of the light absorbed tells users which compounds are present. The amount of light absorbed at each frequency tells users the concentration of each compound present.
Amazingly, since the sample gas only interacts with the optical beam, the analyzer calibration can be fixed and unchanging over the life of the instrument. If configured well (like all MAX-iR analyzers), the calibration curve can be transfered from one instrument to another.
When you have collected the data, how do you use this to achieve optimal efficiency and determine the instrument’s accuracy?
Once the data are collected, the spectra are analyzed by the Thermo Scientific™ MAX-Acquisition™ or MAX-Analytics™ Software. These software platforms utilize a custom classical least squares regression analysis to identify and quantify each compound in the sample spectrum.
To confirm the accuracy of the automated analysis, an R2 mathematical analysis and a residual "visual" analysis are performed for each analyte. A high R2 analysis, close to 1.0, suggests that the analyte was most likely properly quantified. The visual residual analysis provides the user with graphical information on how to improve the analysis if necessary.
Since the IR spectra are stored for every measurement, the data analysis can be redone and improved as many times as is necessary. Additional compounds can be added to the method electronically at any time by the user to quantify new analytes and to reduce their interference to other analytes.
Lastly, the software platforms have a rapid search feature to identify potential unknowns within the spectra.
What benefits would you say using FTIR offers, and how does the MAX-iR analyzer with StarBoost technology, or OE-FTIR as you call it, optimize this system?
There are a number of significant benefits of FTIR over other analytical technologies. First, the infrared analysis is performed in real to near-real-time because there is little to no sample preparation and no separation required. Second, all organic and inorganic compounds present in a sample can be analyzed simultaneously from ppb to % levels. Third, the MAX-iR analyzer's calibration library is transferable from instrument-to-instrument and is fixed for the life of the instrument.
The StarBoost optical technology allows users to measure compounds at levels never achieved before by FTIR gas analysis. We are now routinely measuring gas impurities in bulk gases at 10s of parts per trillion (ppt). We are also measuring for air toxics like ethylene oxide and formaldehyde at 100 ppt to 1 ppb levels in near-real-time. These types of measurement are now possible with OE-FTIR technology.
When Autoreference technology is incorporated into the analysis methodology, no background spectrum is required. This is ideal for continuous measurements where the background may be changing by 1,000 times more than the peak that is being measured.
And when analyzing compressed gases and using the Pressure Modulation technology, users can zero the analyzer on the sample gas. So, expensive purifiers are not required to zero the analyzer for each analyte of interest. In fact, this technology can even demonstrate when purifiers are not working or bleeding impurities.
What do the majority of your customers look for when seeking an analyzer?
Our customers are looking for analyzers that can be set up quickly and be fully operational within a day of installation. Our customers want completely automated systems that don't require specialized technicians or chemists to operate. They want systems that come fully calibrated and are ready to produce high quality analytical data on start-up.
The MAX-Acquistion Software operates on all MAX-iR analyzers and OE-FTIR based systems. This software collects all the data, analyzes it and reports it to the client DCS automatically.
As an example, the Thermo Scientific™ MAX-Bev™ System for beverage CO2 impurity monitoring is so easy to operate, the truck driver delivering the CO2 to a beverage plant will run the analyzer and print a report without assistance. The system contains a very sophisticated analyzer capable of measuring ppb level impurities in beverage grade CO2 and determining the CO2% to +/-0.03%, yet it is very easy to operate.
Are there any other key features of the system that you have not yet mentioned?
All of the MAX-iR based systems have alarm monitoring for the hardware and the gases. If users want to alarm on a specific impurity level, they can set that, which would then alert the control panel in their facility.
Each alarm can be sent to the factory DCS using Modbus. Alternatively, if the users have the Thermo Scientific™ MAX-INT Factory Interface Module, they can also transmit analog signals, if required. This offers the flexibility to use the software the way users want or the way their system is configured.
Thermo Fisher Scientific offers the most sensitive FTIR gas analyzer on the market - an OE-FTIR system. It is fully optimized, compact, and designed to run for 10-plus years with little to no maintenance.
About Martin Spartz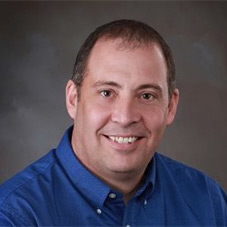
Marty has a Ph.D. in Analytical Chemistry from Kansas State University. He is now the Sr. Director of Gas Analysis R&D at Thermo Fisher Scientific. Marty focus is on research to develop next generation FTIR gas analysis systems that can measure ultra-trace components in complex samples.
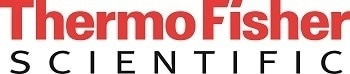
This information has been sourced, reviewed and adapted from materials provided by Thermo Fisher Scientific – Materials & Structural Analysis.
For more information on this source, please visit Thermo Fisher Scientific – Materials & Structural Analysis.
Disclaimer: The views expressed here are those of the interviewee and do not necessarily represent the views of AZoM.com Limited (T/A) AZoNetwork, the owner and operator of this website. This disclaimer forms part of the Terms and Conditions of use of this website.