When it comes to selecting core materials for aerospace applications, today’s design engineers are faced with an ever-expanding list of choices and increasing challenges. Since the introduction of passenger jet transportation, aircraft OEMs, Tier 1 and Tier 2 firms have tried to improve efficiency and safety while lowering costs.
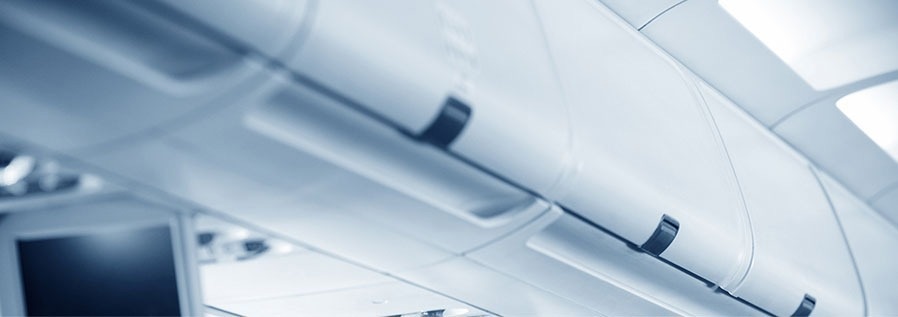
Image Credit: General Plastics Manufacturing
Fuel efficiency becomes a crucial motivator in the rapid development of innovative lightweight materials, as it accounts for up to 50% of direct operating expenses.
In less than a generation, composite materials have gone from accounting for 10–15% of passenger jets to accounting for more than 50%. Increasing cost-cutting efforts in the aerospace transport industry have resulted in an increase in suitable materials that fit a defined form and function.
There are so many positive things to be gained by designing next-generation aircraft with these composite materials. Along with their light-weight characteristic, they provide greater design freedom. You’re able to manufacture planes in a more efficient way with lighter-weight parts. And, you can make larger assemblies to send to the final manufacturers, where they can be assembled in an easier, more effective manner.
Joel Meyer Ph.D., Manager, Chemistry Laboratory, General Plastics Manufacturing
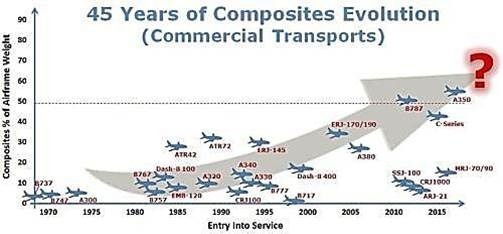
Image Credit: General Plastics Manufacturing
Fire, Smoke, Toxicity, and Heat Release Specifications
Until 1986, materials had to pass a 60-second vertical flame test. Since then, FAA standards have included horizontal burns and oil burn tests, as well as smoke and heat release specifications, including the 65/65/200 peak heat release, average heat release over time, and optical smoke density measurements.
All materials must comply with the FST/OSU designation in addition to these criteria because many OEMs also have toxicity requirements.
These standards are important since interior components account for roughly 20% of an aircraft’s total fire load at landing, which is when the majority of mishaps occur. These specifications are typically applied to the big ceiling and wall panels, as well as structures that cover huge areas within the aircraft.
Acoustic insulation panels, floor panels, partitions, side walls, stow bins, and other interior components fall under this category.
Composite materials make up over 90% of the interior furnishings of today’s passenger planes. As composites are made up of a variety of chemical components, they can burn in a variety of ways, releasing variable quantities of stored chemical energy.
The longer and hotter a material burns, and the more smoke produced, the higher the risk to passengers and crew inside an aircraft.
Cutting Through Competing Imperatives
While there are numerous composite core aerospace materials on the market, meeting all of the requirements for physical properties, safety specifications, environmental impact, design flexibility, and cost efficiency is the most difficult problem.
Finding the combination of lightweight, to-spec material that meets the FST/OSU criteria at an affordable cost has absolutely been the holy grail for engineers designing aircraft interiors. A weighted analysis of materials for strength, durability, weight, and cost is paramount, and leads manufacturers to ask the question: ‘What properties does the application really require?’ before material designs are finished.
Joel Meyer Ph.D., Manager, Chemistry Laboratory, General Plastics Manufacturing
Designing aircraft interiors also means that the potential next-generation requirements need to be anticipated. The recent decision in Europe to phase out all halogen-containing flame retardant materials and chemicals, which could endanger passengers, heralds a global transition toward halogen-free, fire-safe materials.
Some materials, like polymethacrylimide (PMI) and styrene acrylonitrile (SAN), have excellent physical properties yet fail FST/OSU testing, making them unsuitable for next-generation aircraft.
On the other hand, a material like polyvinylchloride (PVC) is strong, and 65/65/200 heat release and smoke density compliant but has a low glass transition temperature (Tg). Thus, it is typically deemed unsuitable for aerospace prepregs and adhesives that must stand up to temperatures of over 200 ºF for composite layup panel processing
Others, such as polyethersulfone, have desirable properties but are much more expensive than polyurethane foams.
For certain applications, the ability to support heavy loads dictates extremely strong core material. Due to its inherent unidirectional strength and lightweight nature, honeycomb material has been the default core material for composite panels.
However, in non-load-bearing applications, it is plainly over-engineered and comes with a significant cost premium due to the time- and labor-intensive manufacturing process. That cost is then subsequently passed down to the passengers that make use of the aircraft.
To provide a more cost-effective solution for aircraft design, it has recently become vital to use new materials. This has given design engineers the ability to experiment with materials that match a specific function rather than utilizing over-engineered honeycomb for every application, regardless of the loads and strains that the material is subjected to.
Supporting Aircraft OEMs with On-Spec Materials
- Thermoformable using drape or mold-forming processes, meaning it is suited to the design of shallow slopes and angles
- Easily vacuum-bagged to form laminates
- Supports high processing temperatures of up to 275 °F and offers good chemical compatibility
- Formulated to offer outstanding FST/OSU properties coupled with great variability in density, strength, modulus, and other properties
- Optimized for the location, whether non-load-bearing, light- to moderate-load-bearing
- It will essentially last forever if protected from light and heat
General Plastics has worked directly with OEMs for over 80 years to create novel materials and implement new designs into aircraft, assisting them in achieving cost-effective, lightweight, safe, and to-spec materials that contribute to their current and future success.
LAST-A-FOAM® FR-3800 FST from General Plastics is the first polyurethane material to meet the FST/OSU specification, and it was created to meet the industry’s requirement for a low-cost core alternative that meets FST/OSU properties.
Despite the fact that flame-retardant polyurethanes have been around for decades, some do not fulfill severe FST/OSU and smoke toxicity criteria.
The FR-3800 FST polyurethane material is halogen-free and meets the FST/OSU 65/65/200 specification.
Unlike other flame-retardant materials, which sacrifice essential physical attributes in order to achieve fire resistance, these foams have the same strength and stiffness as other aerospace-grade foams. They were developed specifically to meet current industry requirements, including the BMS-8133 specification for aircraft interiors.
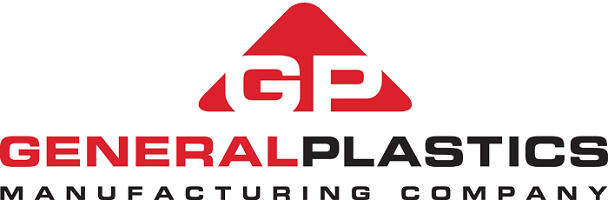
This information has been sourced, reviewed and adapted from materials provided by General Plastics Manufacturing.
For more information on this source, please visit General Plastics Manufacturing.