Researchers from the Buchmann Institute for Molecular Life Sciences at Goethe University in Frankfurt am Main, Germany, have employed the microArch® S140, a microscale 3D printer developed by Boston Micro Fabrication (BMF), to fabricate hydrowells. These miniaturized vessels are utilized for culturing 3D cellular spheroids in microgravity conditions.
The effort was part of the Spheroid Aggregation and Viability in Space (SHAPE) experiment, which has received support from the German Aerospace Center (DLR). The experiment will be conducted aboard the International Space Station (ISS), a low-earth orbit platform for scientific research.
Hydrowells and Spheroids for Cell Cultures
Hydrowells, custom hydrogel well-plates, are manufactured using agarose, a polysaccharide material. Instead of plastic or glass vessels, they are utilized as containers for cellular spheroids in microgravity environments.
Cellular spheroids are three-dimensional tissue models with various applications, including regenerative medicine and cancer research. The non-adhesive compartments of hydrowells allow for easy media exchange through diffusion and provide a biocompatible environment.
Spheroids, three-dimensional cell cultures grown in suspension within individual hydro wells, form sphere-like formations. The use of hydrowells ensures that individual spheroids do not aggregate into uncontrolled sizes.
The Buchmann Institute for Molecular Life Sciences' participation in the SHAPE experiment required using specially designed hydrowells with unique features. These hydrowells had a funnel-shaped entrance, a cylindrical cross-section, and a bottom section that was either U-shaped, conical, or truncated.
The design of the bottom section of the hydrowells was crucial to the experiment’s success, as it facilitated spheroid formation and long-term cell culturing. The hydrowells were fabricated using positive molds, which have a convex shape.
The decision to use microscale 3D printing for mold fabrication was driven by its ability to deliver high resolution, produce smooth surfaces, use high-performance materials, and support rapid development.
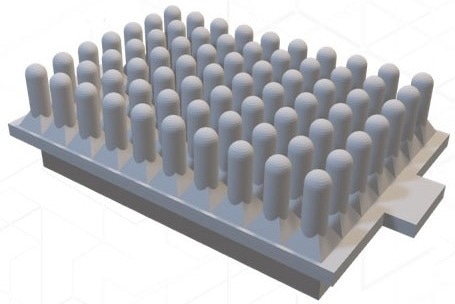
Model of Funnel Shaped Hydrowells. Image Credit: Boston Micro Fabrication (BMF)
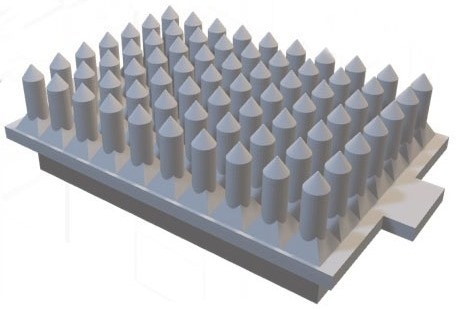
Model of Cylindrical Cross Section Hydrowells. Image Credit: Boston Micro Fabrication (BMF)
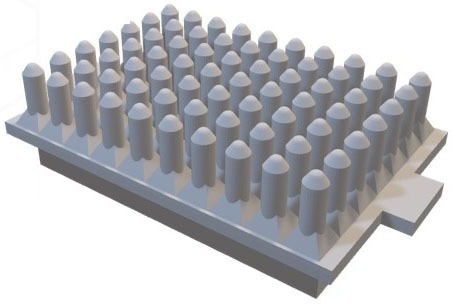
U-bottom Hydrowells. Image Credit: Boston Micro Fabrication (BMF)
Microscale 3D Printing Equipment and Materials
The microArch® S140, the microscale printer utilized by the Buchmann Institute for Molecular Life Sciences, has an optical resolution of 10 µm and the capability to produce parts with a surface finish of 0.4-0.9 µm Ra (top) and 1.5-2.5 µm Ra (side).
The technology behind the S140, projection micro-stereolithography (PµSL), is responsible for its exceptional smoothness and precision. This technology outperforms the standard stereolithographic (SLA) printers, which have ~25-50 µm resolution, by a large margin.
BMF offers ultra-high-resolution equipment that utilizes engineering-grade photosensitive resins and can print layer thicknesses ranging from 10 µm to 40 µm. The company also supports an open material system.
The BMF HT200 resin, which was used to produce the positive hydrowell molds, is highly durable and combines high strength with the ability to withstand high temperatures up to 200 °C.
This resin's resistance to high temperatures and pressures made it suitable for sterilization using autoclaving, which helps prevent bacterial contamination of the hydrowells. After autoclaving, the layer definition of the hydrowell molds is well-preserved, with no warping or delamination observed.
The thermal and mechanical properties of the 3D-printed material ensured the outstanding and consistent quality of the final product.
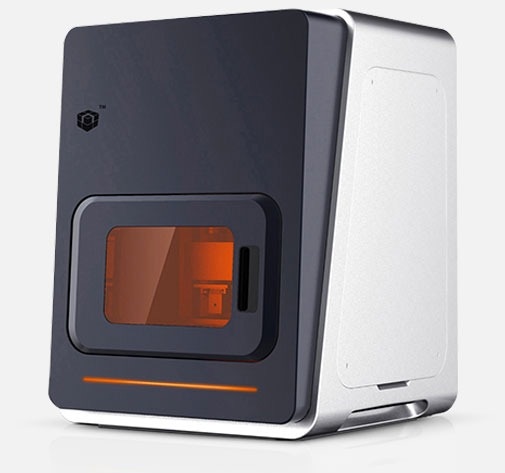
The microArch©S140. Image Credit: Boston Micro Fabrication (BMF)
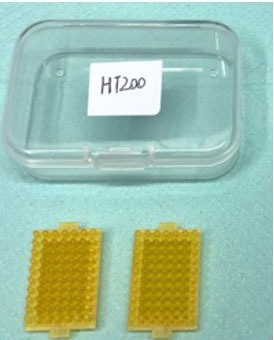
BMF's HT200 resin. Image Credit: Boston Micro Fabrication (BMF)
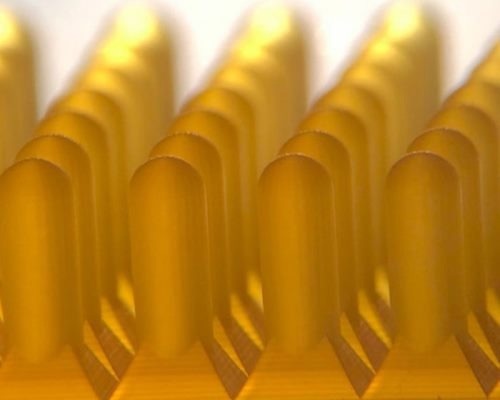
HT200 Hydrowells. Image Credit: Boston Micro Fabrication (BMF)
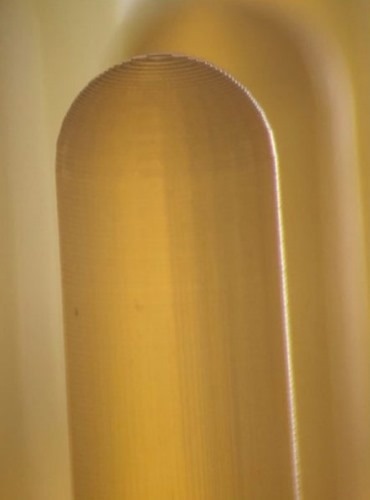
Close up of Hydrowell using BMF's HT200 resin. Image Credit: Boston Micro Fabrication (BMF)
Resolution, Surface Finish, and Autoclaving
The team at Goethe University, led by Dr. Francesco Pampaloni, Ph.D., a tenured staff scientist and principal investigator, utilized the microArch® S140 from Boston Micro Fabrication to fabricate the positive molds required for the production of hydrowells.
The BMF micromolds have a superior resolution and surface finish, which allows the fabrication of high-quality hydrowells to reliably produce spheroids with a consistent size.
Dr. Francesco Pampaloni, Ph.D., Tenured Staff Scientist and Principal Investigator, Goethe University
He added that the 3D printing material used for the molds can “fully withstand wet autoclaving at 121°C and 2.1 bar, ensuring the sterility of the hydrowells”.
For further information regarding the microArch® S140 and the PµSL technology, individuals may contact Boston Micro Fabrication.
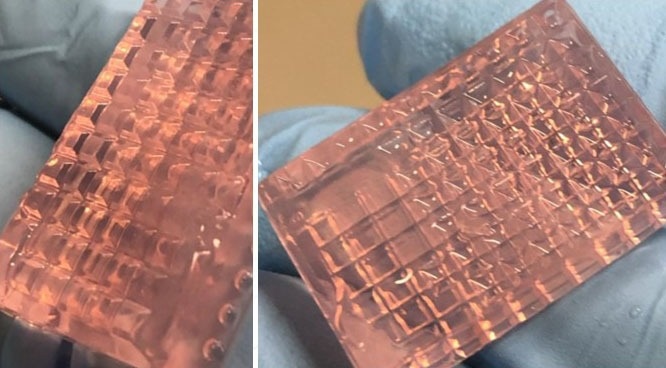
Overview of Hydrowells. Image Credit: Boston Micro Fabrication (BMF)
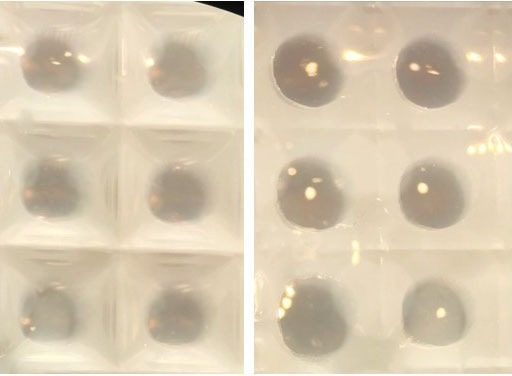
Hydrowells with and without cellular spheroids. Image Credit: Boston Micro Fabrication (BMF)
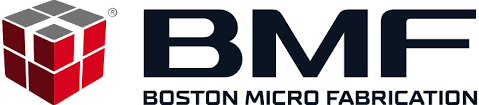
This information has been sourced, reviewed and adapted from materials provided by Boston Micro Fabrication (BMF).
For more information on this source, please visit Boston Micro Fabrication (BMF).