In industry, certain materials are expected to maintain their performance and properties under even the most extreme conditions. For space exploration, cryogenic storage containers, and ice-breaking equipment, it is essential that materials maintain their impact toughness and tensile strength and are resilient to the effects of low temperatures.1
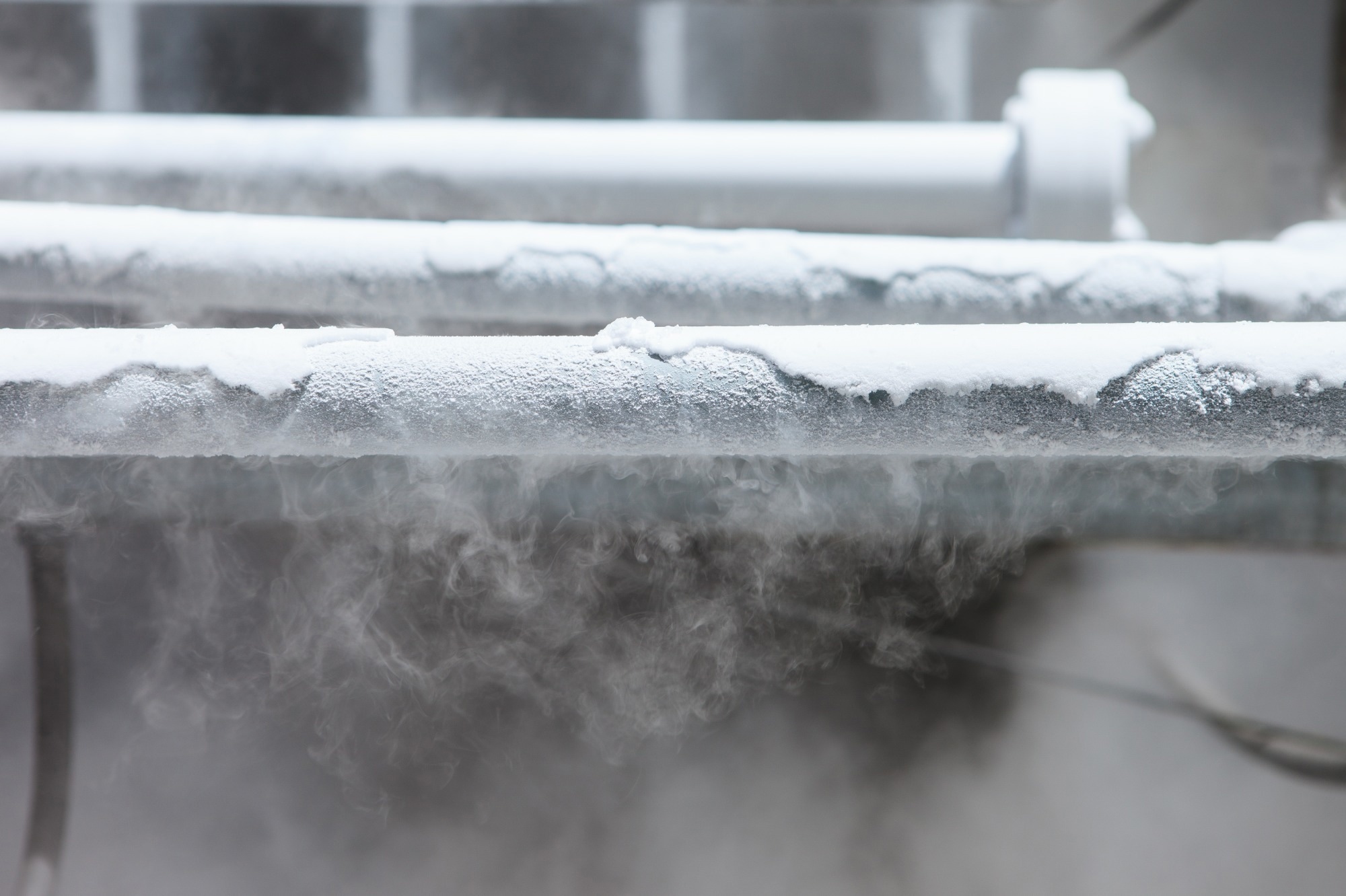
Image Credit: Shutterstock.com/PhotoLove
However, most metals and materials become increasingly brittle with decreasing temperature. The reason for this embrittlement at cryogenic temperature is that the restriction of the movement of the atoms in the crystal lattice means that there are no ‘slip systems’ to allow for distortions. This reduced mobility thus means that it is easier for cracks to form, ultimately causing the observed brittle behavior of the material.2
Nonetheless, not all materials exhibit the same temperature sensitivity and dependence on macroscopic behavior; cryogenic materials, such as aluminum, titanium, and some steel alloys, for instance, are a viable option.
A growing interest in the possibility of a ‘hydrogen economy,’ where hydrogen replaces many fossil fuels as the energy source of choice, is also driving the development of more cryogenic materials for liquid helium storage.3 The challenge, however, is finding experimental methods that can be used to characterize brittle behavior at the atomic level and allow us to understand what materials are likely to possess good cryogenic toughness.
Characterizing cracks and defects requires techniques with excellent spatial resolution and 3D reconstruction capabilities. Using X-Rays that have good penetration depth to characterize the bulk of material as well as the surface is also important for improving our understanding of what makes materials cryogenically tough.
This article explores the experimental methods used to characterize brittle behavior and highlights recent findings that shed light on the exceptional cryogenic toughness of specific austenitic steel alloys. These insights have the potential to revolutionize the development of affordable and abundant materials for cryogenic storage, opening up new possibilities for various industries.
Methods
Understanding cryogenic toughness means combining two types of experiments – a variation of stress/strain and impact testing to test the properties of the material and a high-resolution imaging technique to understand how the forces exerted on the material have affected its structure at the atomistic level.
Common tests on potential cryogenic materials include looking at mechanical strength and elongation, as well as the measurement of the Charpy impact toughness – a parameter that measures the energy absorbed by a test specimen while breaking under impact load.4 Such tests can be performed either at room temperature or under cryogenic conditions.
Imaging methods for defect evaluation include scanning electron microscopy, electron backscatter diffraction (EBSD), and X-Ray computed tomography (CT) – all of which can be used to investigate the structure of the material at the micrometer scale. With the right image processing and segmentation software, X-Ray tomography can be used to visualize a full 3D image and decompose it into individual layers. Finally, every defect can be numerically characterized, and educated choices can be made to improve the materials’ performance.
One of the most common cryogenic materials that is ideal for a variety of applications is austenitic steel. There are a number of types of austenitic steel, but they are characterized by the presence of alloying elements like nickel and chromium. Some varieties also contain a percentage of molybdenum and titanium.
Recently, researchers have found that fine-grained Fe-30Mn-0.11C – a specific variety of austenitic steel – has an unusual degree of cryogenic toughness.5 To determine why this low-cost austenitic steel variety showed such unusual behavior, the research team used a series of experimental techniques in combination with mechanical property tests.
Results
After impact testing, the research team performed 3D fracture surface morphology analysis on the micro-computed tomography samples to see where the main and subordinate cracks were forming.4 The results of the analysis revealed that the very fine-grained sample with a much smaller average particle size showed several cracks, including a large main feature and several subordinate cracks, whereas the coarse grain sample showed a single deep crack but ultimately a flat surface structure.
In order to help the researchers understand the position, shape, and dimensions of the crack formation, the team needed to use image reconstruction. Segmentation of the images could then be used to label and assign the different structures and identify how and where they were performing.
Automation of the segmentation procedures meant the research team could systematically segment images and sort fracture types in a reliable, reproducible way that was not dependent on operator opinion or skill level. Automating the image construction process for the 3D fracture surface morphology analysis also meant that the samples could be examined much more efficiently.
The impact experiments were repeated at both liquid nitrogen temperatures (77 K) and at room temperature for alloys of both particle sizes. The stacking fault energy and analysis of the images made it clear that only the very fine-grained sample showed the inverse temperature dependence required for an ideal cryogenic storage material.
In the case of the Fe-30Mn-0.11C, microscopic 3D analysis was required to identify the inverse temperature dependence of the toughness. The study demonstrated how simply changing the grain size of a relatively cheap material that relies on a high manganese content can provide material properties suitable for cryogenic behavior, especially considering that many of the current materials designed to resist cryogenic impacts are based on high entropy alloys which are often very costly to manufacture.
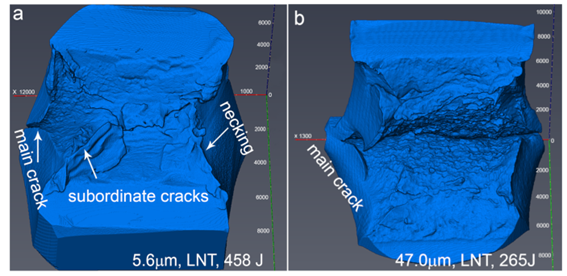
This figure displays 3D fracture surface morphology using micro-computed tomography of fine- and coarse-grained samples. Image Credit: Wang, Y., et al. https://doi.org/10.1038/s43246-021-00149-8
Conclusions
The findings from this work could be applied to other, more conventional steel alloys to explain their temperature-dependent behavior. Moreover, by changing the processing conditions to have smaller mean particle sizes, other more conventional steels could find a new application, meaning that Fe-30Mn-0.11C may not be the only abundant, affordable alloy used for cryogenic storage.
Avizo Software from Thermo Fisher Scientific was crucial for the visualization of results and for performing segmentation of the imaging data and measurement of the features of interest. Avizo Software is designed to automate and simplify many of the complex steps involved in image processing and analysis. The majority of materials science evaluation techniques involve some form of sequential 2D imaging – often alongside a 3D reconstruction. Avizo Software can help simplify these steps to help you get the most information out of your data.
Learn more: Introduction to Avizo Software for metals and alloys characterization
References and Further Reading
- Hong, S. Y., & Zhao, Z. (1999). Thermal aspects, material considerations and cooling strategies in cryogenic machining. Clean Products and Processes, 1, 107–116. https://doi.org/10.1007/s100980050016
- Weinberger, C. R., Boyce, B. L., & Battaile, C. C. (2013). Slip planes in bcc transition metals. International Materials Reviews, 58(5), 296–314. https://doi.org/10.1179/1743280412Y.0000000015
- Qiu, Y., Yang, H., Tong, L., & Wang, L. (2021). Research progress of cryogenic materials for storage and transportation of liquid hydrogen. Metals, 11(7). https://doi.org/10.3390/met11071101
- Wang, Y., Zhang, Y., Godfrey, A., Kang, J., Peng, Y., Wang, T., Hansen, N., & Huang, X. (2021). Cryogenic toughness in a low-cost austenitic steel. Communications Materials, 2(1), 1–10. https://doi.org/10.1038/s43246-021-00149-8
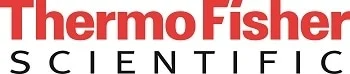
This information has been sourced, reviewed and adapted from materials provided by Thermo Fisher Scientific - Software.
For more information on this source, please visit Thermo Fisher Scientific - Software.