High-performance metals and alloys must withstand challenging temperatures and demanding environments, such as those found in the aerospace and nuclear industries. Such materials, like aluminum, zirconium, nickel, and titanium alloys, must also be stable, strong, and resistant to impact and corrosion. As such, scientists and engineers constantly strive to refine and expand the range of materials with enhanced properties.
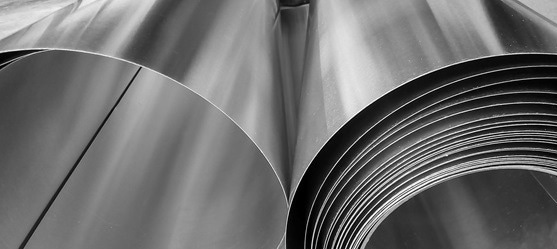
Image Credit: Aulia1/Shutterstock.com
Manufacturers rely on advanced production techniques that monitor and control various material features to meet these stringent demands. Among these critical features are inclusions, precipitates, and grains, which significantly influence the mechanical properties and behavior of the metals and alloys. However, the key to achieving superior performance is understanding the influence of these characteristics on the mechanical properties and behavior of the materials.
This article will discuss the importance of monitoring inclusions, precipitates, and grains in the production of high-performance metals and alloys while also exploring the significance of these material features, such as their size, shape and distribution, the challenges involved in their characterization, and the advanced techniques used to monitor and control them.
Inclusions
Inclusions are impurities that occur naturally or as a result of the manufacturing process of metals, significantly altering the structural integrity and performance of the material.
Inclusions of non-metallics, such as oxides and sulfides, are typically formed through several possible pathways, including chemical reactions, physical effects, or contamination during processing.
Inclusions disturb the uniformity of the material’s structure, which can significantly affect mechanical properties, such as strength and hardness, and lead to defects, cracks, and fatigue failure in the final product.1 They can also impact casting and process flow operations.2 However, there are ways to control and tailor inclusions, ultimately improving the material’s properties and performance. For example, in some cases, oxides and sulfides in steel can increase hardness and wear resistance, while other inclusions can boost crystallization, improving the material’s overall structure.3 Research into inclusions is critical to refining and optimizing materials.
One aspect of the investigation into inclusions is determining what reactions occur between inclusions and the metal or alloy, then controlling them. For example, in steel making, reactions between slag and liquid steel during casting affect the shape and properties of inclusions which, in turn, has significant implications for the final product.
Investigating inclusions can involve various advanced analytical techniques, such as scanning electron microscopy (SEM) and energy dispersive spectroscopy (EDS). One research group combined X-Ray computed tomography (XCT), high-temperature confocal scanning laser microscopy (HT-CSLM), and advanced electron microscopy techniques to study their samples.4
The researchers used these advanced techniques in conjunction with image processing software, which helped them extract, measure, and report on the features of interest in a dataset.
Segmenting the data this way allowed the team to investigate the inclusions’ size, shape, and composition and probe the interface between the materials. The resulting segmentation can also be reused in computational fluid dynamics software and other simulators.
Precipitates
Precipitates have strengthened various alloys since early last century. For example, small amounts of vanadium, niobium, and titanium added to steel can increase strength and toughness. These micro alloys (containing less than 0.10% alloying elements) react with carbon and nitrogen to form nanoscale carbonitride precipitates which appear as a very fine dispersion throughout the material.5 Researchers are still investigating the science behind how precipitates form and grow, how they interact with solid solutes and grain boundaries, and how mechanical properties are affected.6,7
Designing the optimal microstructures requires control of solid-state phase transformations involving complex chemistry and interaction with structural defects. Progress in experimental characterization and modeling has helped improve knowledge and description of these processes.
Techniques, such as transmission electron microscopy (TEM) can provide high-resolution nanoscale information on the types of precipitates and their effects on the material. Combining EDS with TEM can establish the composition of individual precipitates. However, this process is time-consuming, requiring extensive data sets to generate reliable, statistically significant results.
The operator has to manually collect data on chemical composition, which is limited to a few dozen particles a day, or use separate particle imaging without chemical information.
The solution is using automated software to automatically analyze hundreds of particles without wasting the operator’s time. By automating the process, statistically relevant data sets (up to thousands of data points) can be characterized in one day or faster in some instances.
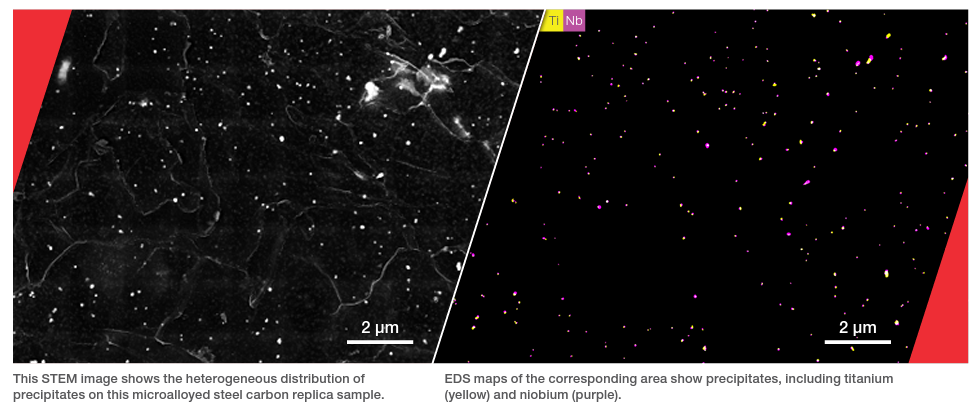
Image Credit: Thermo Fisher Scientific
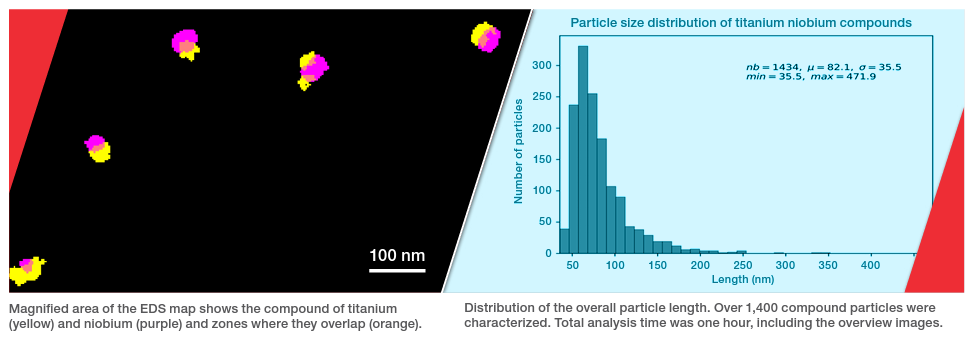
Image Credit: Thermo Fisher Scientific
Grains
As a molten metal or alloy solidifies, separate crystal structures combine to form grains. Their structure, size, and distribution depend on the composition of the material and how it was made. Thus, it is critical to control grain structures in metals and alloys as they can profoundly impact mechanical properties such as strength, hardness, and ductility.
Failures in many metals and alloys have been associated with issues around the grain boundary, such as creep, corrosion, and brittleness. Fine grains, for example, can reduce hot tearing, which is when fractures form as a metal solidifies; or they can cause defects in hot spots.8 Investigating how fine grain and coarse grain materials react differently provides insight into how fractures might occur at grain boundaries or interior regions and how microstructure changes on deformation.9 Researchers developing new alloys for enhanced mechanical properties analyze grains from various complex reactions.
It is essential to tune the material's microstructure to achieve the optimum product. SEM is a useful tool to visualize grains and grain boundaries. SEM can provide surface and cross-sectional images of samples, while EDX analysis can provide information on how elements are distributed within samples.10
Software that can segment and analyze datasets quickly and accurately can also significantly speed up investigations. Meanwhile, focused ion beam SEM can produce 3D datasets which can be reconstructed using automated software.9 Analysis of these datasets allows researchers to visualize 3D distributions of intermetallic phases in specific areas of interest. EDS mapscan also be analyzed to identify the chemical composition of particular phases.
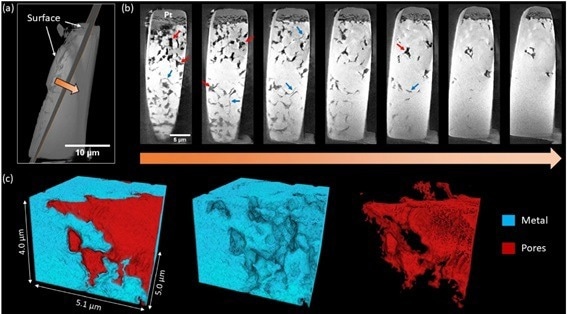
The figure shows Ni–20Cr foil corroded in KCl–NaCl in air for 16 h at 700 °C: (a) Diagonal slice used for depth profiling. (b) Pseudo-2D cross sections along depth direction, spaced approximately 0.4 μm apart. Larger pores and intergranular cracks are indicated using red and blue arrows. (c) 3D volume rendering of near-surface region displaying pore formation. Visualization of 2D pseudo cross-section images and 3D volumes was conducted in Thermo Fisher Scientific’s Avizo software. Image Credit: Yu L-C. et al. https://doi.org/10.1038/s41598-022-20286-5
Conclusion
Three major factors (inclusions, precipitates, and grain structure) influence high-performance metals and alloys' mechanical properties and behavior. Thus, characterizing these factors' size, shape, distribution, and chemical composition helps researchers overcome shortcomings and develop the highest-performing materials.
Advanced imaging and spectroscopy techniques, such as SEM, TEM, and EDS, provide the data necessary to measure the material's performance. However, high expertise is required to interpret such data, and software plays a crucial role in automating the analysis of the feature of interest and generating an easy-to-read report.
Thermo Fisher Scientific designs systems capable of collecting images and specroscopy data, as well as software to efficiently extract and measure datasets with high accuracy and time. Thermo Scientific™ Avizo™ Software can aid researchers in studying inclusions, precipitates, and grains by providing accurate image processing in a manual or automated way and includes advanced segmentation, quantification, and reporting tools, boosting productivity and output of the engineering teams.11
For materials scientists looking for an automated system to analyze precipitates in metals and alloys, Thermo Fisher offers the Thermo Scientific™ Automated Particle Workflow (APW),12, which combines unique hardware and software into one nanoparticle characterization workflow on TEM. The microscope runs unattended and can collect and characterize thousands of particles daily.
These automated solutions provide a comprehensive environment for studying and quantifying fundamental properties of high-performance steel and metals, empowering materials scientists to develop high-end materials confidently.
Learn more: Introduction to Avizo Software for metals and alloys characterization
References and Further Reading
- Wang, J. et al. Effects of aluminum and titanium additions on the formation of non-metallic inclusions in nickel-based superalloys. Journal of Alloys and Compounds, Volume 906, 2022, 164281.
- Yang, S. et al. Inclusions in wrought superalloys: a review. Journal of Iron and Steel Research International volume 28, pages921–937 (2021).
- Costa da Silva, ALV. Non-metallic inclusions in steels – origin and control. Journal of Materials Research and Technology, Volume 7, Issue 3, 2018, Pages 283-299.
- Raviraj, A. et al. The Spontaneous Emulsification of Entrained Inclusions During Casting of High Aluminum Steels. Metallurgical and Materials Transactions B volume 52, pages1154–1163 (2021).
- Precipitate analysis in metals with the Automated Particle Workflow (thermofisher.com).
- Ma, K. Precipitation in nanostructured alloys: A brief review. MRS Bulletin volume 46, pages 250–257 (2021).
- Wu, H. Thermal Stability of the Precipitates in Dilute Al-Er-Zr/Hf Alloys at Elevated Temperature. Metals 2022, 12(8), 1242.
- Stanic, D. et al. Influence of Copper Addition in AlSi7MgCu Alloy on Microstructure Development and Tensile Strength Improvement. Metals 2020, 10(12), 1623.
- Wang, Y. et al. Cryogenic toughness in a low-cost austenitic steelCommun Mater 2, 44 (2021).
- Yu L-C. et al. Evolution of micro-pores in Ni–Cr alloys via molten salt dealloying. Scientific Reports volume 12, Article number: 20785 (2022).
- Avizo Software for alloy and metal analysis (thermofisher.com).
- Nanoparticle analysis (thermofisher.com).
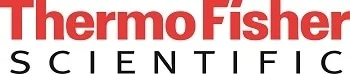
This information has been sourced, reviewed and adapted from materials provided by Thermo Fisher Scientific - Software.
For more information on this source, please visit Thermo Fisher Scientific - Software.