The screw conveyor has an extensive history. Archimedes (ca. 212 BC) invented the first screw conveyor, and his design is still used today for irrigation and grain transfer. Screw conveyors became widely used in industry during the middle of the nineteenth century.
With the introduction of industrial polymers in the first half of the twentieth century, screw conveyors, also known as extruders, developed as an important instrument for polymer processing.
Single extruders can be used to melt and shape polymers; however, they have limited performance. As they function with a filled barrel under pressure, there is no venting or split feeding, and mixing options are limited.
To meet the increased demand for continuous mixing in the polymer sector, R. Erdmenger created and patented a twin-screw compounder with intermeshing, self-wiping screws.
This article discusses a variety of compounding activities, as well as process-dependent and independent parameters. The article provides an overview of how to improve the compounding process and screw setup, as well as information on automated retention time measurement.
In addition, recommendations for scaling up from a small laboratory compounder to a larger pilot plant or small-scale production extruder are provided.
The Compounder
The primary compounding operations of a parallel twin-screw compounder are feeding, melting, conveying, mixing, venting, and extrusion of the homogenized product (Figure 1). The volumetric or gravimetric feeder delivers solid material into the feed zone. Air is removed, and the low-density material is compacted.
In the subsequent stage, the material is transported forward and heated in a partially filled, non-pressurized conveying section. In the initial mixing zone, the material is melted and plastified. The mixing zones are filled with material. A conveying zone follows, which can be utilized for venting, filler splitting, or liquid feeding.
The mixing and conveying stages are then alternated to produce a homogenous product. The conveying screw parts in the venting zone are used to vent volatiles and air, either at atmospheric pressure or under vacuum.
The extrusion section builds up pressure and shapes the material. In most applications, a strand is extruded, cooled in a water bath, and then chopped into pellets.
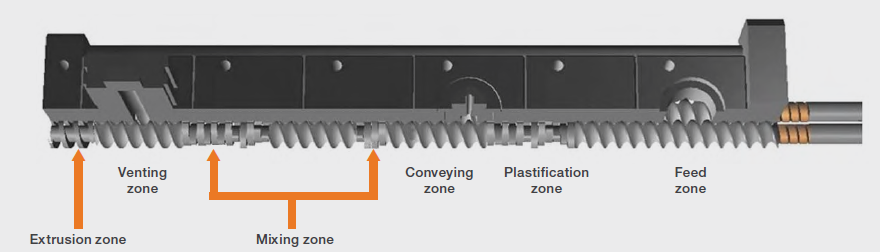
Figure 1. Barrel and screw layout. Image Credit: Thermo Fisher Scientific – Materials Characterization
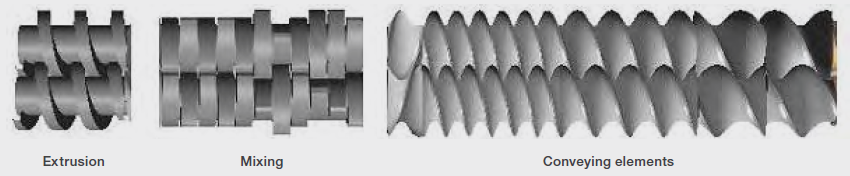
Figure 2. Screw elements. Image Credit: Thermo Fisher Scientific – Materials Characterization
Screw Elements
Due to the segmented screw architecture, the screw assembly is variable. The most prevalent screw elements are self-cleaning and intermeshing conveyance elements with Erdmenger-designed forms. The remaining screw elements are intended for mixing, extrusion, or specialized distributive mixing elements (Figure 2).
Processing Parameters and Dependencies
Material throughput, residence time or material distribution in the system, and melt temperature are all dependent on or can be changed by a variety of parameters.
The throughput has a considerable impact on the residence time. A larger throughput reduces both the average residence time and the width of the residence time distribution (Figure 3).
The screw speed has a relatively small influence on the residence time. Backward-mixing elements have a significant effect on residence duration and dispersion increases. Screw speed and feed rate have the greatest impact on melt temperature.
Greater screw speeds provide mechanical energy input in the mixing zones, resulting in a greater melt temperature (Figure 4).
Scale-up
After successful trials with a small-scale laboratory compounder (Figure 5), scaling the process to a larger pilot plant or production compounder is always difficult. The primary requirements are that both compounders have the same, or similar, barrel geometry and screw configuration.
The residence times and melt temperatures should be similar to those used in the laboratory test, and the compounder should operate adiabatically. In the first approach, the screw speed and temperature profile should be identical to those used in the laboratory. The starting feed rate is calculated using the Schuler rule.1
The specific energy is then changed by varying the throughput. The main source of energy is the screw's shear energy. The scale-up is limited by the barrel's available surface and its relationship to volume; the rate of heat transmission (heating or cooling) reduces with increasing barrel diameter.
The volume grows by a factor of three, although the surface area only increases by a factor of two.
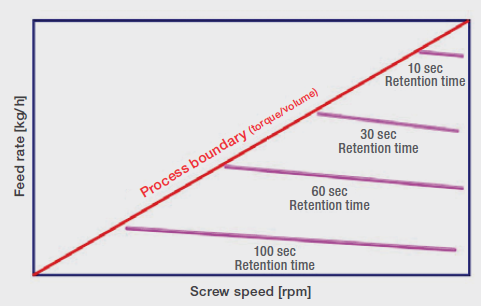
Figure 3. Residence time and feed rate. Image Credit: Thermo Fisher Scientific – Materials Characterization
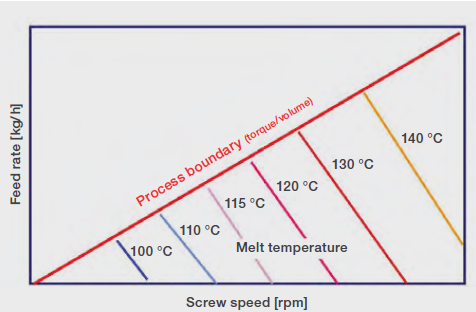
Figure 4. Residence time and screw speed. Image Credit: Thermo Fisher Scientific – Materials Characterization
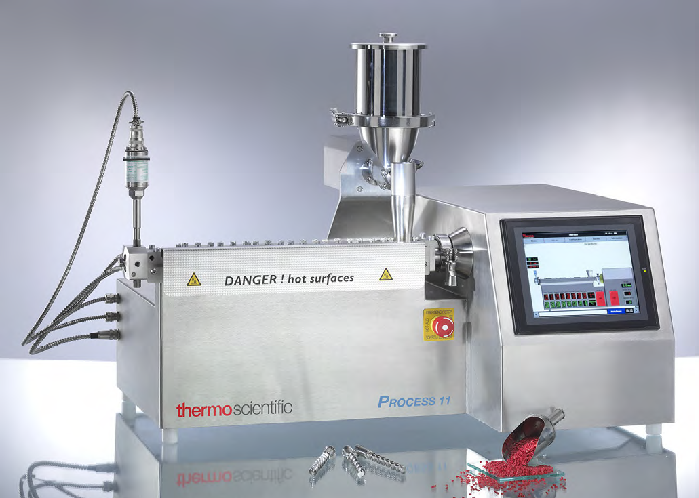
Figure 5. Thermo Scientific Process 11—11 mm lab scale screw compounder. Image Credit: Thermo Fisher Scientific – Materials Characterization
A test was done on the laboratory-scale Thermo Scientific™ Process 11 Twin-Screw Extruder with a throughput of 1 kg/h and screw speed of 200 rpm. These settings yielded a specific energy of 559 kJ/kg and a residence time of approximately 55 s.
To scale up to Process 16, a 16 mm compounder, the Schuler rule states that the throughput should be 3 kg/hour. Under these conditions, the measured residence time and specific energy in Process 16 were much lower than those in the Process 11 Extruder.
An adjustment of the feed rate to 2.5 kg/h produced results similar to the smaller-scale residence duration and specific energy (566 kJ/kg) (Figure 6).
Conclusion
When transitioning from a laboratory-scale compounder to a bigger unit, the theoretical factor for throughput must be changed. The residence time is a critical process parameter for scale-up.
Instead of monitoring residence time using a tracer and a timer, it is preferable to use a camera system and examine the change in color intensity of the tracer. This results in a residence time distribution where the average residence time is at its maximum, representing the optimal outcome.
By understanding the smaller-scale processing parameters and making appropriate adjustments to factors like those mentioned, scaling up to a larger, yet otherwise identical, compounder is quite feasible.
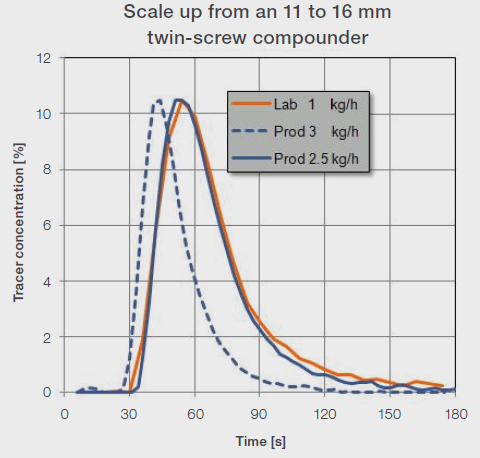
Figure 6. Residence time for scale up tests. Image Credit: Thermo Fisher Scientific – Materials Characterization
Reference
- W. Schuler (1996). Process Engineering Design of Co-Rotating Twin Screw Extruder, Dissertation, University of Wales Swansea, 1996.
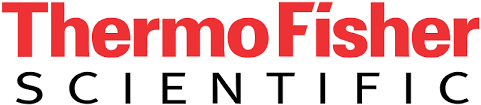
This information has been sourced, reviewed and adapted from materials provided by Thermo Fisher Scientific – Materials Characterization.
For more information on this source, please visit Thermo Fisher Scientific – Materials Characterization