Battery production faces challenges in manufacturing expertise, workforce training, and cost competitiveness, impacting the industry's growth and innovation. In this interview, learn how Thermo Fisher Scientific are tackling the battery production challenge.
What are the most critical challenges currently facing battery manufacturing?
Prof. Stanley Whittingham: While the US and Europe have led in battery chemistry innovation, we’ve fallen behind in manufacturing expertise. Much of that know-how shifted to Asia years ago, and we haven’t kept pace. We also lack workforce development and long-term industrial commitment. To compete globally, we need sustained investment in building technical manufacturing capabilities and infrastructure from the ground up.
Prof. Louis Piper: The workforce gap is especially urgent. In the UK alone, we’ll need around 100,000 skilled workers in battery manufacturing by 2040. And it’s not just about Ph.D.'s—we need technicians, process engineers, and operators just as much. Meeting that demand requires coordinated efforts, with strong government backing and close collaboration between industry, academia, and training institutions.
Ines Miller: From an industry standpoint, the biggest hurdle is scaling local production while maintaining high and consistent quality. Right now, only a handful of global players can manufacture at the highest levels of output and yield. Western companies are under real pressure to catch up, particularly given the cost advantages Asian manufacturers currently hold.
What emerging technologies could have the biggest impact on battery manufacturing in the next decade?
Ines Miller: Battery chemistry is likely to evolve incrementally rather than through disruption. We’re already seeing a split: high-nickel and silicon-based chemistry for performance-focused applications, and LFP (lithium iron phosphate) or LMFP (lithium manganese iron phosphate) for cost-sensitive, stable systems. But the real leap may come from manufacturing innovations—dry coating, for example, could significantly cut costs and environmental impact while enabling the use of thicker electrodes.
Prof. Louis Piper: Much of our focus is on driving down cost across the manufacturing process. That includes eliminating toxic solvents like NMP, optimizing formation cycling, and adapting existing lines to support solid-state and lithium-metal technologies. There’s also a big opportunity to improve process integration—streamlining coating, calendaring, and formation steps could boost performance and simplify production.
Prof. Stanley Whittingham: I see a gradual shift away from carbon-based anodes and cobalt-heavy cathodes. Lithium-metal anodes and cobalt-free cathode chemistries will become more prominent. At the same time, dry processing will help phase out hazardous, costly solvents like NMP. And as conductivity improves, thicker electrodes will become more practical, offering higher energy density without adding complexity.
How can AI and machine learning support battery manufacturing?
Prof. Louis Piper: AI has a major role to play in real-time quality control. At WMG, we’re applying machine learning to steps like electrode coating and formation to predict performance and catch defects early. Battery production generates terabytes of data every day—AI is essential for processing that volume quickly and translating it into actionable insights.
Prof. Stanley Whittingham: We’re already seeing the impact. Companies like CATL have thousands of engineers focused on AI integration, and it has paid off—their cell quality has improved significantly. The biggest value isn’t in discovering new materials, but in using AI to fine-tune manufacturing processes and boost yield.
Ines Miller: Battery production involves more than 30,000 process parameters, so identifying where issues arise isn’t trivial. AI helps uncover defect patterns, optimize formation protocols, and enable automated control systems. We’re seeing growing industry demand for AI-driven metrology and closed-loop feedback to stabilize production and support scaling.
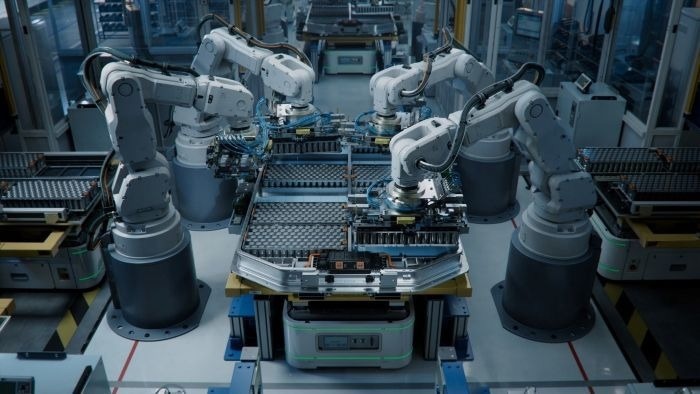
Image Credit: IM Imagery/Shutterstock.com
What are best practices for managing IP in collaborative research between academia and industry?
Prof. Stanley Whittingham: In the US, IP ownership in collaborative research is guided by federal laws like the Bayh–Dole Act. At Binghamton, when we provide services such as battery testing, the IP generally remains with the company. But when we’re co-developing new technology, we take a flexible, case-by-case approach to avoid bottlenecks and ensure that innovations can move toward commercialization.
Prof. Louis Piper: We work within a variety of partnership frameworks—direct contracts, government-funded initiatives like the Faraday Institution, and Catapult programs—all of which include IP management strategies. The key is balancing clarity with pragmatism. Patents are important, but so are licensing pathways and support for spinouts. Our focus is on enabling industrial deployment, not creating roadblocks.
Ines Miller: From the industry side, we’re seeing more companies, especially in Asia, adopt IP licensing models. They retain control over battery designs and process IP while supporting OEMs in scaling production. That model allows for innovation protection alongside local implementation. When working with academic partners, clear ownership terms and well-defined agreements are essential to align goals and avoid conflict down the line.
What regional initiatives are supporting local battery manufacturing capabilities?
Prof. Stanley Whittingham: In New York, we’re developing two major federally funded facilities aimed at strengthening domestic manufacturing. One is a $113 million center for prototyping and scaling up cylindrical and pouch cells, with a strong emphasis on workforce training. The other is a $160 million NSF Engines program focused on applied R&D, covering innovations like dry coating, recycling, and thick electrodes, designed to leapfrog conventional gigafactory technologies.
Prof. Louis Piper: At WMG, we’ve continuously upgraded our pilot manufacturing line to stay aligned with industry trends. That includes adding advanced environmental controls, capabilities for thick electrode processing, and dry coating. We’re also collaborating globally—from Chile to Croatia—on strategies around critical minerals and workforce development to strengthen supply chains and skills pipelines.
Ines Miller: On the industry side, a major challenge is moving from lab-scale concepts to production-ready designs. Many companies underestimate how critical it is to choose the right equipment and vendors early on. A lack of operational experience is a common bottleneck, and that’s one area where Asian manufacturers continue to lead—especially in terms of efficiency and throughput.
What role does recycling play in the future of battery manufacturing?
Prof. Louis Piper: Recycling is becoming increasingly important, especially in Europe, where regulations now require the recovery of key materials like lithium, cobalt, and nickel. However, most of today’s recycling volume comes from production scrap, not end-of-life batteries from vehicles. To scale effectively, we need more efficient black mass processing and systems designed to handle consistent, high-quality feedstocks.
Prof. Stanley Whittingham: That’s a key point—the bulk of battery waste today still comes from manufacturing scrap, not used batteries. These materials are often of high purity and shouldn’t be reduced to black mass without consideration. We need smarter recycling approaches that retain as much material value as possible rather than treating everything as raw input for smelting.
Ines Miller: Recycling is essential not just for sustainability, but also for supply chain security. It helps reduce the industry’s carbon footprint and lowers dependence on mining. There’s a real opening for Western companies to lead here—startups like Redwood Materials and Li-Cycle are making headway, but there’s still plenty of room for innovation in how we recover and reuse critical materials.
What strategies are helping improve battery safety in manufacturing and applications?
Prof. Stanley Whittingham: Safety issues don’t always originate from the battery cells themselves; many problems are due to poor enclosure design or the use of low-quality, uncertified components. In places like New York, UL certification is now mandatory, which is a positive move. Still, low-cost, unverified imports continue to pose serious risks.
Prof. Louis Piper: Chemistry also plays a major role in safety. Materials like LFP and LMFP offer significantly better thermal stability compared to high-nickel cathodes. As we scale up larger-format cells and more complex pack architectures, updated safety protocols and design standards are essential. There’s also ongoing research aimed at better understanding and mitigating thermal runaway.
Ines Miller: Safety needs to be engineered at every level—from the choice of cell chemistry to the architecture of the full battery pack. We’re seeing development of advanced materials like thermal gap fillers and multifunctional coatings that enhance resistance to thermal propagation. Passive safety features are improving in parallel with performance advances.
This is interview one in the eight-piece Building Better Batteries series.
Watch the Accompanying Webinar: Current Challenges in Building Better Batteries
About the Speakers
Prof. Stanley Whittingham, Nobel Laureate in Chemistry (2019), Professor at Binghamton University
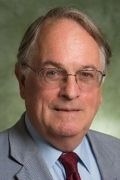
A pioneer of lithium-ion batteries, Prof. Whittingham has over 50 years of experience in solid-state chemistry, battery materials, and ion transport. He led the development of the first lithium battery in the 1970s while working at Exxon.
Prof. Louis Piper, Professor of Physics at WMG, University of Warwick
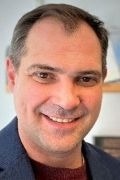
Prof. Piper’s work bridges surface physics, materials science, and manufacturing innovation. At WMG, he leads initiatives on battery degradation, pilot line development, and advanced electrode design in collaboration with academia and industry.
Ines Miller, Associate Partner at P3 Group, Germany

With a background in business chemistry, Ines leads P3’s global battery technology consulting practice. She advises automotive and energy companies on industrialization, supply chain strategy, and operational ramp-up for cell manufacturing.
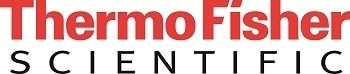
This information has been sourced, reviewed and adapted from materials provided by Thermo Fisher Scientific.
For more information on this source, please visit thermofisher.com/battery-solutions.
Disclaimer: The views expressed here are those of the interviewee and do not necessarily represent the views of AZoM.com Limited (T/A) AZoNetwork, the owner and operator of this website. This disclaimer forms part of the Terms and Conditions of use of this website.