Chopped prepreg molding compound (CPMC), a relatively new material form resembling molding compounds made from chopped resin impregnated tow, provides design and processing engineers various benefits including resin selection flexibility, variable chip widths abnd lengths. Moreover, it is possible to pre-form the chopped prepreg into shapes before molding to aid fabrication and optimize structural performance.
Chopped prepreg can be offered in a Sheet Molding Compound (HexMC) as a rolled up mat and a Bulk Molding Compounds (Toray Molding Compound) form as loose chips.
Chopped prepreg in the sheet molding compound form lessens in-process labor effort involved in the conversion of a molding compound into a mat as in a quasi-isotropic prepreg ply stack, while chopped prepreg in the bulk form not only gives more options in designing pre-forms for structural performance but also eliminates material waste.
.jpg)
Figure 1. CPMC shown in bulk and sheet form.
Application Technology
Part Fabrication Requirements
Molding of chopped prepregs is typically performed at isothermal temperatures in matched metal dies. Contrary to prepreg autoclave molding, the matched metal dies deliver dimensionally controlled surfaces on either sides of the component. Applying pressure to the molding compound when the fiber and resin move as one unit is the key for molding prepreg based chopped molding compounds. If the resin is to too thin to shift the fiber or too thick to flow, there will be a problem in filling the molding compound in the mold, leading to a poor quality part.
Chemical thickening and thermal thickening of the resin before molding are used to obtain the preferred resin viscosity for molding compounds. Prepreg manufacturers can perform chemical thickening, while it is possible to perform thermal thickening either by the part’s molder or the prepreg fabricator. The molding temperature may get affected by characteristics such as preform installation time, part thickness and the part strength during demolding (Tg sensitivity). Lower cure temperatures facilitate the process repeatability but require additional press time in all cases. Process engineers must also take into account shelf life considerations, exothermic reactions and degree of cure.
Structure and Design
Traditionally molding compounds have been used for non-structural parts. However, the technology advancements with prepreg based mold compounds due to the employment of more advanced fibers, advanced resin systems, straight fibers, improved fiber wet-out, precision resin control and customized chip sizes. Table 1 lists out different combinations of fiber/resin available from chopped prepreg.
Table 1. Example of the variety of fiber/resin combinations available from chopped prepreg
Product |
Description |
MS-1A |
MS-1A is a high-performance carbon fiber/epoxy resin compression molding system based on high modulus carbon fiber. MS-1A compression molding compound yields unparalleled stiffness and high strength. MS-1A is qualified for space applications |
MS-1H |
MS-1H is a carbon fiber/epoxy resin compression molding system using a high modulus PAN carbon fiber. This is an excellent high stiffness molding compound that has been qualified to military and commercial applications. It has excellent out time stability and processes very well in small and thin cross section parts. It is the performance alternative to the MS-4H molding compound. |
MS-4A |
MS-4A is a carbon fiber/epoxy resin compression molding system based on standard modulus carbon fiber. MS-4A compression molding compound affords economical processing while providing good strength, stiffness, and moldability. MS-4A is available in fiber lengths ranging from ¼ inch to 2 inch for custom applications. |
MS-4H |
MS-4H is a carbon fiber/epoxy resin compression molding system. This is an excellent low cost high performance carbon fiber molding compound that has been qualified to military and commercial applications. It has excellent out time stability and processes very well in medium to large heavy parts. |
Cetex MC1200 |
Toray Cetex MC1200 PEEK is a thermoplastic based molding compound based on either standard or intermediate modulus carbon fiber. It is tough, fire retardant and capable of using very fast cycle times (less than 10-15 minutes) for forming. |
Moreover, these materials deliver higher structural performance as they are capable of being easily molded into ribs and gussets. The following factors need to be considered in designing parts with structural molding compounds:
- The preform charge design (3D charge patterns are akin to prepreg layups)
- Part form, fit, and function requirements
- The mold design (identifies charge loading, how flow will occur, and the approach to remove the part)
- The effect of the candidate designs on production costs (complexity has an impact on labor and yields)
It is essential to take in to account each of these factors to achieve the optimal overall design for performance, weight and cost. Key focus should be on
- The design of the charge patterns (plies)
- Patterns that ensure load transitions essential for the loads to flow from thick to thin areas and around corners
- drive local part thickness to eliminate stress concentrations
- The molding approach
- single axis or multi-axis
- driven by part feature requirements or performance (minimal flow)
- Mold design to install preform and demold part
- the mold design should be in such a way that facilitates placing a near net 3D preform in the mold
- Provide opportunity for the bulk factor of the patterns
- Protect random fiber orientations preferred for quasi-isotropic properties by reducing flow induced fiber alignment
- Provide drafts and avoid undercuts, which obstruct part demolding
Application Opportunities
Applications of CPMC
CPMC is a cost and weight effective alternative to aluminum and continuous fiber prepreg. It can be utilized to create 3D forms resembling existing aluminum parts. It is not easy to fabricate these forms with continuous prepreg material. Moreover, CPMC rivals well with continuous fiber prepregs, when the part features flaws such as attachment holes. The impact of holes and other flaws on CPMC is much smaller when compared to continuous fiber composites.
CPMC is flaw tolerant due to the transition of loads through the matrix from one chip to the other. Hence, the creation of an additional flow or hole will not produce the same knock down factor encountered by continuous fiber prepreg parts. Flaw tolerance is verified by conducting no-hole compression and open-hole compression tests on the chopped fiber molding compound and a quasi-isotropic laminate.
The same carbon/epoxy prepreg material is utilized as the chopped prepreg in the molding compound and as unidirectional tape in the laminate. Table 2 compares the impact of holes on the Quasi-Isotropic CFP Products and CPMC.
Table 2. Comparison Data Showing the Impact of Holes (flaws) on the Strength of CPMC and Quasi-Isotropic CFP Products
CPMC
Chopped Prepreg Molding compound
CFP
Continuous Fiber Prepreg (Quasi - Isotropic) |
Open Hole Compression ASTM D 6484 |
No-Hole Compression ASTM D 6484 Modified |
Strength (MPa) |
Strength (Ksi) |
Strength (MPa) |
Strength (Ksi) |
CPMC |
CFP |
CPMC |
CFP |
CPMC |
CFP* |
CPMC |
CFP* |
248.2 |
280.6 |
36.0 |
40.7 |
337.2 |
530.9 |
48.9 |
77.0 |
262.0 |
277.9 |
38.0 |
40.3 |
333.0 |
489.5 |
48.3 |
71.0 |
239.9 |
275.1 |
34.8 |
39.9 |
323.4 |
423.3 |
46.9 |
61.4 |
275.8 |
284.1 |
40.0 |
41.2 |
328.2 |
600.5 |
47.6 |
87.1 |
242.7 |
276.5 |
35.2 |
40.1 |
342.7 |
504.7 |
49.7 |
73.2 |
277.9 |
|
40.3 |
|
354.4 |
*Values recorded when test was stopped |
51.4 |
*Values recorded when test was stopped |
298.5 |
43.3 |
288.2 |
41.8 |
288.2 |
41.8 |
327.5 |
47.5 |
271.7 |
39.4 |
355.1 |
51.5 |
258.6 |
37.5 |
311.0 |
45.1 |
293.7 |
42.6 |
337.8 |
49.0 |
299.2 |
43.4 |
289.6 |
42.0 |
241.3 |
35.0 |
329.6 |
47.8 |
232.4 |
33.7 |
343.4 |
49.8 |
255.8 |
37.1 |
354.4 |
51.4 |
Mean |
265.7 |
278.8 |
38.5 |
40.4 |
330.4 |
509.8 |
47.9 |
73.9 |
S Deviation |
22.6 |
3.6 |
3.3 |
0.5 |
20.8 |
64.4 |
3.0 |
9.3 |
COVariance |
8.5% |
1.3% |
8.5% |
1.3% |
6.3% |
12.6% |
6.3% |
12.6% |
Chopped Prepreg MC - Strength |
Continuous Fiber Prepreg |
without hole |
w/Hole |
% drop |
without hole |
w/Hole |
% drop |
330.4 |
265.7 |
19.6% |
509.8* |
278.8 |
> 45.3% |
47.9 |
38.5 |
19.6% |
73.9* |
40.4 |
> 45.3% |
Chopped prepreg’s inherent flaws lower the impact of additional flaws like holes, heat and moisture. From Table 2, the performance hit is roughly 20% for the molding compound and is more than 45% in the case of prepreg. According to current design rules, the same knock down factor is applied to prepregs and molding compounds. Based on this new insight, CPMC with lower knock down factors provides more options for this material form.
Table 3 provides the results of another flaw driven test that compares the bearing strength of CPMC and quasi-isotropic continuous fiber prepreg composites.
Table 3. Bearing Strength Comparison
Bearing Response ASTM D 5961 (Method B, Supported, Tension) |
|
Strength (MPa) |
Strength (Ksi) |
CPMC |
CFP |
CPMC |
CFP |
CPMC
Chopped Prepreg Molding compound |
787.6 |
946.7 |
114.2 |
137.3 |
1021.6 |
943.1 |
148.2 |
136.8 |
914.9 |
970.2 |
132.7 |
140.7 |
892.8 |
887.6 |
129.5 |
128.7 |
901.1 |
920.2 |
130.7 |
133.5 |
CFP
Continuous Fiber Prepreg (Quasi - Isotropic) |
898.1 |
|
130.3 |
|
816.6 |
118.4 |
783.2 |
113.6 |
916.0 |
132.9 |
784.2 |
113.7 |
839.6 |
121.8 |
902.2 |
130.9 |
744.9 |
108.0 |
835.8 |
121.2 |
839.8 |
121.8 |
Mean |
858.6 |
933.6 |
124.5 |
135.4 |
S Deviation |
71.5 |
31.2 |
10.4 |
4.5 |
COVariance |
8.3% |
3.3% |
8.3% |
3.3% |
Bearing Strength Comparision |
|
Minimum |
% reduction |
Mean |
% reduction |
(Mpa) |
|
(Mpa) |
|
CFP |
887.6 |
16% |
933.6 |
8% |
CPMC |
744.9 |
858.6 |
|
(Ksi) |
|
(Ksi) |
|
CFP |
128.7 |
16% |
135.4 |
8% |
CPMC |
108.0 |
124.5 |
|
|
|
|
|
CPMC - An Alternative to Aluminum
A 45% weight reduction can be achieved with carbon fiber composites when a 1:1 replacement is made for aluminum. Moreover, it is easier to form CPMC into attachments that encounter other carbon parts. This eliminates the galvanic reaction problem occurring with aluminum parts. Table 4 compares the material properties of CPMC with 6061 T6 aluminum properties.
Table 4. Mechanical Test Data Comparison of CPMC and Aluminum
Figure 2 shows CPMC substitution for aluminum.
Material |
Tensile |
Compression |
Shear |
Strength |
Modulus |
Strength |
Modulus |
Strength |
|
MPa |
Ksi |
GPa |
MSi |
MPa |
Ksi |
GPa |
MSi |
MPa |
Ksi |
CPMC (MS4H-1") |
302.0 |
43.8 |
42.7 |
6.2 |
330.3 |
47.9 |
50.3 |
7.3 |
177.9 |
25.8 |
6061-T6 |
290.0 |
42.0 |
68.9 |
10.0 |
290.0 |
42.0 |
68.9 |
10.0 |
186.0 |
27.0 |
7075-T6 |
524.0 |
76.0 |
71.7 |
10.4 |
524.0 |
76.0 |
71.7 |
10.4 |
317.0 |
46.0 |
.jpg)
Figure 2. CPMC Substitution for Aluminum (Courtesy Toray – CCS Composites)
Material substitution with CPMC can be easily done with a few changes. However, the following areas need to be considered:
- Part load paths requirements - design alterations such as thickness blends and corner wraps to address materials that are quasi-isotropic in nature instead of isotropic.
- Thickness requirements as very thin parts <0.045" need additional process development
- Stiffness requirements – apply geometry for local stiffening such as gussets
- Thread requirements -Ensure the use of molded or bonded in inserts in those areas (boss maybe needed)
- Undercuts requirements for the molding direction, a typical machined feature in aluminum
- Drafts requirements for part removal as aluminum machined parts do not have drafted surfaces in majority of the cases
Besides weight reduction and galvanic reaction benefits, replacing a carbon CPMC with aluminum also provides improved fatigue performance and radio translucency.
CPMC - Application Examples
Figure 3 shows representative CPMC parts.
.jpg)
Figure 3. Representative CPMC Parts (Courtesy Toray – CCS Composites).
Conclusion
CPMC, as a new material form, provides compelling benefits over aluminum and continuous fiber prepreg in certain applications. This article discussed engineering considerations for designing and fabricating chopped prepreg based parts. CPMC is useful in designing parts during the inclusion of flaw conditions such as attachment holes and environmental conditions. For aluminum, CPMC provides a more direct conversion thanks to its 3D molding capabilities. There is a need to substitute aluminum interfacing components with materials that avoid galvanic reaction with carbon when adoption of composites increases in primary structural applications. High structural requirements and 3D geometry make CPMCs a suitable material to fulfill these demands.
About Toray Advanced Composites
Toray is a multinational company that combines textile technology with related chemical processes. Toray develop and produce specialist materials with specific properties. Protective materials for fire-fighting clothing, and strong, lightweight materials in aircraft are good examples of these, as are materials that block UV radiation for applications like tentcloth and awnings.
Toray’s activities can be divided into four areas of application:
- Safety and protection
- Aerospace
- Sport and recreation
- Infrastructure and the environment
Toray has divided these segments into the eight divisions:
- Protective Fabrics
- Outdoor Fabrics
- Space Composites
- Aerospace Composites
- Industrial Composites
- Advanced Armour
- Geosynthetics
- Industrial Fabrics
- Grass
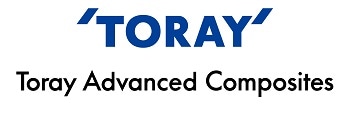
This information has been sourced, reviewed and adapted from materials provided by Toray Advanced Composites.
For more information on this source, please visit Toray Advanced Composites.
Authored by: Jack D. Fudge PE, Toray Advanced Composites
Presented at: SAMPE Conference 41st ITSC Wichita KS Oct 19-22nd, 2009