The operating temperature at which jet engine blades are able to safely rub against abradable shroud linings has been dramatically increased from 350 to 1200°C. This has been made possible by executing wear mechanism studies and by close collaboration with major engine manufacturers.
Methods of Increasing Gas Turbine Engine Efficiency
In the last two decades, air traffic volume has increased considerably, whereas the total quantity of fuel consumed has remained almost unchanged. The jet engine manufacturers strongly contributed towards this by increasing engine efficiency and power generation. This was achieved by raising the operating temperatures, by the use of efficient aerodynamic design and by the use of lightweight materials. Because all of these are mature technologies, one of the last means to further increase the efficiency is the reduction of the clearance distance between the blade tip and casing. This increase in efficiency can save airlines significant operating costs. The implementation of abradable coatings also increases the surge margin, thus increasing the stability and active safety of engine flow conditions.
Uses of Abradables
Abradables are not restricted to aeroengines. They can be used in most rotating machinery such as stationary gas turbines, turbo compressors, radial compressors, turbo chargers, and pumps. Sulzer Innotec and Sulzer Metco, in close co-operation with most major jet engine manufacturers, are world leaders in the development of abradable coatings to cope with the operating conditions throughout the jet engine (figure 1).
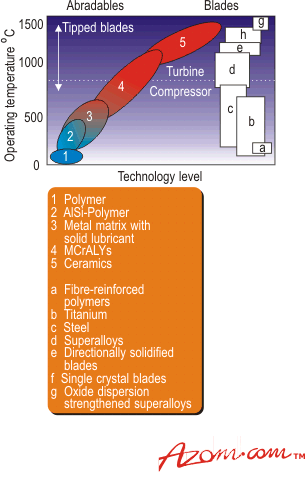
|
Figure1. Abradable family versus technology level.
|
Development of Abradables
The development of abradables necessitates numerous tests, ranging from powder fabrication to the selection of the optimum thermal spray process, in order to simulative laboratory testing and, finally, field trials. This would lead to the certification of the abradables by engine manufacturers. The goal is to produce a seal that does not cause blade wear, which maintains smooth shroud surface and which remains intact for thousands of operating hours.
Function of Abradables
The reduction of the blade tip to casing clearance can result in the blades rubbing against the shroud. By coating the shroud with abradables, however, this interaction can be tolerated. The thermally sprayed coatings are designed to release fine wear debris when machined by the high velocity blades, while causing no blade wear (figure 2).
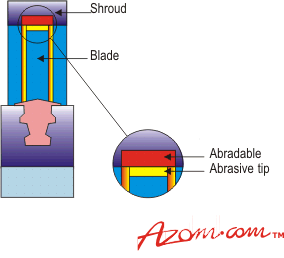
|
Figure 2. Schematic of an abradable seal.
|
Abradable coatings must remain smooth with the least amount of grooving, rupture or cause wear to the blade under all possible cutting conditions. A good abradable accommodates different wear mechanisms created by changing rub conditions, namely blade material, temperature, blade tip velocity and incursion rate.
How do Abradable Coatings Work?
When sliding over the surface of an abradable, the blade tip strikes the coating particles which are protruding from the surface of the coating. The force of impact drives the individual particle into the coating. The stored elastic energy causes the particle to rebound and de-bond. Because of the newly created free surface, the wear debris assumes a larger volume. The released particle (wear debris) must now have the opportunity to escape. This requires thin blade tip cross sections or rough, sandpaper-like surfaces on the blade tips. Entrapment of the particle between the blade tip and the coating results in increasing shear forces and local plastic deformation or rupture of the coating. The energy necessary for the abrading process is supplied by the blade tip. It must suffice to break out the individual protruding particles, thereby generating a new surface. The greater the particle bond, the more energy the blade tip must supply in order to free the particles. If the forces are too high the blade tip heats up and begins to wear, sometimes by abrasion but predominantly by melting.
Laboratory tests conducted on a special tribometer have made it possible to study the wear mechanisms found when blade tips cut into abradables. This information is converted into a model which takes into account not only the operating conditions but also the structure of the coating, the blade material and the blade tip design. By applying this model, coatings have been developed that are capable of operating at surface temperatures up to 1200°C. The matrix materials range from Al-Si for low temperature, MCrAlY for mid range temperature to yttrium-stabilised zirconia for high temperature turbine section, table 1.
Table 1. Relative properties for various coatings.
|
Al/Si + release agent
|
450
|
75
|
Up to 2mm
|
35-40
|
McrAlY + release agent + polymer
|
700
|
75-80
|
Up to 2mm
|
35-40
|
YSZ + polymer + release agent
|
1200
|
90-92
|
Up to 2mm
|
20-25
|
Enhancing Abradability
For enhanced abradability the energy for particle detachment must be reduced. The model, therefore, calls for small matrix particles, a polymer to generate porosity and solid lubricants or release agents to act as dislocators within the coating. During thermal spray deposition, the polymer phase lowers the coating stresses, thereby allowing the deposition of thick coatings. When burnt-out in a subsequent heat treatment, the abradability of the coatings is further improved, (figure 3).
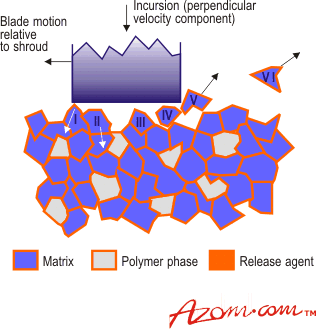
|
Figure 3. Schematic of an abradable model.
|
Figure 3 shows a side view, with a blade passing over the abradable surface. Particles on the surface are affected as follows:
• Particle I was struck by the blade and through momentum transfer, accelerates downwards into the coating.
• Particle II was impacted earlier and is still travelling downwards elastically deforming the neighbouring particles an itself.
• Particle III has transferred all the energy it absorbed during the impact into elastic energy.
• Particle IV was accelerated out of the coating because of the release of the stored elastic energy and tore itself free from surrounding particles.
• Because of the thin blade tip, particle V is able to leave the surface of the abradable coating.
• Particle VI has broken free and passed though the engine. The small size of the wear debris causes no collateral damage to the following blades and vanes.
Ceramic Abradables
For operating temperatures above 900°C, only ceramic-based abradables are suitable. In order to cut a ceramic-based abradable, the blade tips must be reinforced by a well adhered abrasive grit. Very good results are obtained by laser remelting of blade tips with simultaneous injection of hard particles. In ceramic matrix abradables, the use of a releasing agent is not necessary because ceramics wear in a brittle manner. The model for ceramic abradables, figure 3, is based on the idea that the interaction between the blade tip and the shroud surface must result in the brittle release of coating wear debris. The debris should carry away as much energy of the interaction as possible. The continued sliding of the blade over the seal must be avoided. Contact must result in debris formation and be such that the shroud is no longer in contact with the tip. If this rule is not followed, and plastic deformation of any member of the couple is allowed to take place, or very smooth surfaces are produced that result in prolonged sliding contact of the tip over the shroud. The result of which is that melting wear will become the predominant mechanism. The rub experienced by the tip is continuous, as opposed to the intermittent rub for the shroud. The tip has less time and mass available for cooling. Thus, if melting wear is the dominant mechanism, substantial blade wear caused by melting will take place.
Wear at High Speed
A further observation is that above approximately 100m/s debris is released to the rear of the blade. Chip formation as seen in traditional machining does not occur. The blade moves largely parallel to the shroud surface but due to the incursion a perpendicular velocity component is also present. This results in the collision between the shroud surface asperities and the blade tip. A transfer of momentum from the blade to the surface protrusion takes place. The particle is forced away from the tip into the coating. The elastic energy stored then pushes the particle upwards towards the free surface. After the blade tip has passed, and if the particle bonding is weaker than the outward force, the particle will break free of the surface taking most of the impact energy with it. This is an efficient means of wearing.
Effect of Tip Width
When the coating fractures into individual components in the surface zone, the wear debris produced will have a larger volume than in its original form. This volume increase has to be accommodated by the seal system. It thus follows that the blade tip must be very thin to allow the debris to escape to the rear. If this is not the case, the fragments will be trapped between the shroud and tip. The high contact pressure can cause shroud rupture whereas the sliding contact can cause the overheating of the blade tip. This can induce tip wear caused by melting. Experience has shown that when a tip width of 0.7mm is exceeded the likelihood of blade wear and shroud rupture increase strongly
All of these aspects contribute to the construction of models which help materials engineers develop abradable coatings which function in an efficient manner. The efficiency by which the blade-coating interaction takes place, helps to draw the valuable extra percentages of power efficiency from the machinery.
Coating Application Techniques
The abradables are applied by flame, high velocity oxy fuel (HVOF) and atmospheric plasma spraying (APS). Flame spraying is capable of producing very porous coatings, but the reproducibility of this porosity is strongly dependent on the process parameters. Too high porosity can be susceptible to compaction during cutting. HVOF and APS coatings are sprayed relatively densely, and, therefore, require a sacrificial phase that can be burnt out to generate porosity. APS and HVOF are generally preferred because their controllable spraying parameters assure reproducible quality.
|