A pusher furnace is a continuous thermal system which applies heat to the incoming material via multiple thermal control zones.
Process material is loaded onto boats or trays and/or set onto a pusher plate. Boats are pushed into the pusher furnace, typically one at a time, via a pneumatic or ball screw pusher at the desired push rate.
Because material is processed in boats and trays, the flowability and shape of the material is not an issue. Material of all shapes and sizes can be heat treated in a pusher furnace.
Pusher furnaces also save time and reduce energy costs compared to batch furnaces, as they do not need to undergo constant thermal cycling, which increases the time required and takes a toll on the life of the insulation.
Harper aims at systems that offer the greatest operating life, lowest operating cost, and highest efficiency for the manufacturing of advanced materials. Harper's pusher plate and tunnel kilns are ideal for processes needing accurate control of atmosphere and temperature. They can handle processes requiring longer residence times with precise control of the heating rate
Controlling Atmosphere in Pusher Furnaces
Controlled atmospheres can be achieved using a muffle to separate the process material from the environment. If an inert atmosphere is required, the loading boat will enter a purge chamber before entering the heated zone of the furnace.
If a reducing atmosphere is required, 100% hydrogen for example, the boats can pass through Harper’s inclined door with flame curtain before entering the thermal system.
The delicate pressure control in the system is specially considered in order to provide the right direction of the atmosphere flow path in the kiln. This enables evacuation of volatiles and optimizes atmosphere uniformity.
Additionally, Harper’s unique gas curtain technology provides zone-to-zone atmosphere definition under specific conditions. The conveyor furnace is designed as a complete system with the ability to incorporate advanced control systems, skid mounting, gas treatment and handling, turnkey installation and complete field commissioning.
The furnace features Kiln temperatures up to 2800°C and controlled atmospheres including flammable gases and multiple atmospheres.
All of Harper’s Pusher furnaces vary due to our customers unique process needs. Our systems include graphite pushers for high termperatures up to 2800°C; a range of atmospheres including hydrogen and inert environments; multiple-zone furnaces with pre-heat, high heat and cooling zones; and boat stacking facilities up to multi-storey configurations.
Colleen Marren
Applications Engineer, Harper International
Download the brochure for more information
Product Features
The key features of the pusher tunnel furnaces are:
-
Advanced graphite pushers for high temperature applications incorporate strategic heating element placement to achieve optimal temperature uniformity and advanced insulation designs to reduce energy consumption
-
Accurate control of atmosphere dew point along the length of the furnace achieved through sophisticated gas distribution technology
-
Optimized design for maintenance and replacement parts and minimization of field installation effort through modular construction
-
Multiple independently controlled temperature zones (length and width)
Typical Pusher Furnace Applications
Typical applications for processes include:
- sintering
- reduction of metal oxides
- calcination
- carbonization
- purification
- debinding
- parts processing
Products commonly made with pusher furnaces include, but are not limited to:
- uranium dioxide fuel pellets
- purification of tungsten carbide powders
- processing aerospace alloys
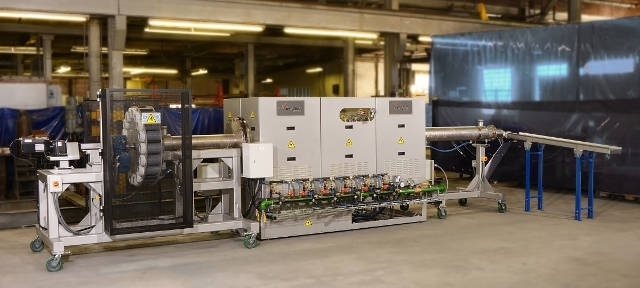
Case Study: Sintering UO2 Fuel Pellets
One specific example where pusher furnaces are used is in the sintering of uranium dioxide fuel pellets. Harper has produced a number of nuclear sintering furnaces.
These furnaces process un-sintered “green” fuel pellets in a furnace at about 1750°C. A precisely controlled reducing atmosphere with a high concentration of hydrogen is required.
Sintering consolidates the pellets and decreases their volume. A single pellet yields about the same amount of energy as one ton of steaming coal.
More information on this application
Ignite™ R&D Program
With Harper's Ignite™ program, testing in their research and development lab is made easy. Harper’s pilot scale rotary furnace can be converted into a pusher by removing the rotary tube and inserting a rectangular muffle that has the inner width of 6 inches and hot zone length of 5 feet.
Systems can have up to three hot zones capable of 1550°C, as well as a cooling zone to cool the boats before discharge. This will help with scale up to a pilot scale or production scale pusher furnace.
“With our Ignite™ program, our experts and PhD’s on staff at Harper, we are really able to make a custom designed pusher furnace that can give their customers their desired products. We have a lot of people working on each design and each person adds great value to the final furnace system design”
Colleen Marren
Applications Engineer, Harper International
More information on the Ignite™ program